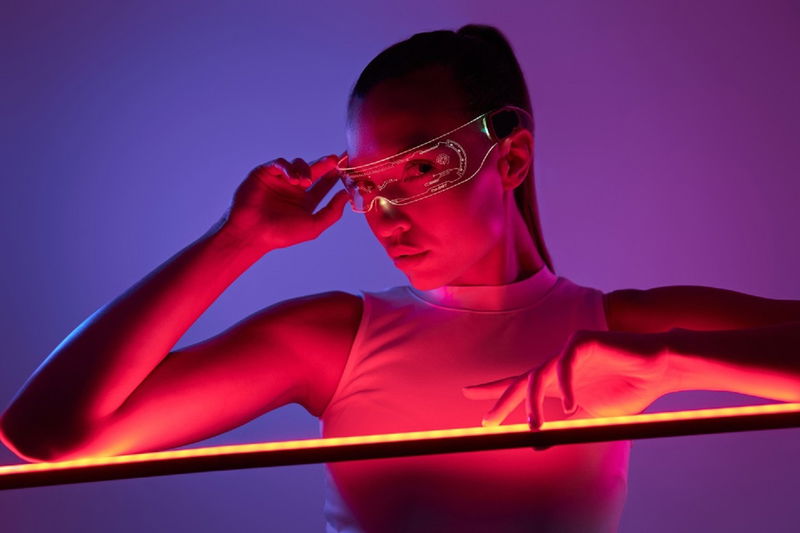
What is Maintenance Management?
Maintenance management provides structure and order in planning, scheduling, completing, and monitoring equipment maintenance work. Maintenance management requires more than simply working directly with equipment - it involves an intricate system of processes and controls. Tracking work orders for maintenance and other activities properly requires using physical and software tools.
Asset bar codes and scanners can help increase efficiency in any facility or office, with many companies using a computerized maintenance management system (CMMS), which centralizes their operations to streamline their approach. Enterprise Asset Management platforms (EAM) offer similar features and may also help track maintenance management.
Maintenance Management: Why is it Important?
Proper implementation of the maintenance process of a maintenance management program under maintenance departments can bring numerous advantages to any business. Any system must remain organized and up-to-date, as many organizations own hundreds or thousands of assets. Here are just some ways in which maintenance management programs can add value:
Maintain Optimal Efficiency: By exercising control of equipment maintenance, you can take a more preventative approach rather than only reacting when emergencies or repairs arise. A centralized platform gives your team full oversight of your operation - not only is this faster, but it makes detecting issues easier and implementing improvements more efficiently.
You are Reducing Downtime: Maintenance management must also account for all aspects of product lifecycle management. By understanding how age can impede performance, upgrading systems becomes simpler. By employing various maintenance strategies together, you can increase equipment uptime.
Unplanned Repairs: These can be expensive and cause production delays or other complications, making maintenance management in an organized fashion all the easier to control a wide variety of costs such as overtime labor inventory costs, operating costs, spare parts expenses. Planning can maximize space while optimizing stock levels.
Increased Safety: Most businesses must abide by various state and federal laws and regulations and follow OSHA guidelines. By centralizing information regarding warranty services and related warranty and service contracts, maintenance management can assist audits or regulatory reviews and contribute towards increased operator safety.
They Improved Decision Making: Failing to make the appropriate maintenance and equipment upkeep decisions can result in failures and safety incidents, making planning complex systems' life cycles particularly challenging. Maintenance management systems offer various reporting options that make accessing quality data essential in improving asset and maintenance decision-making processes.
What is Maintenance Management?
People often associate "maintenance" with working on equipment or providing services. However, maintenance management involves much more than this type of activity. An effective maintenance management function must encompass more tasks in addition to these - an electronic maintenance management platform may help combine several workflows; there should also be a consideration when outlining maintenance management's role within an organization. Below are important areas for consideration when setting out maintenance management's role within its ranks:
Asset Management: Asset management serves as the intersection between CMMS platforms and EAM. To be effective, asset managers must maintain an accurate database containing a full inventory of their assets tracking, by which assets are accurately tracked so work can be scheduled accordingly. Companies may save money through asset assessments that identify outdated or underused equipment that should be removed immediately from service.
Inventory Management: Inventory levels can include raw materials, packaged products, equipment, and parts - anything needed by companies dealing in goods must have an organized warehouse with accurate cycle counts of inventory; many utilize inventory management systems in this endeavor - they help companies maintain maintenance by overseeing spare part inventories or any critical assets required for servicing of facilities or vehicles.
Maintenance Work Order Management: One of the primary functions of software for maintenance management is organizing work orders. A team of field technicians working remotely is often required to schedule, assign, and complete maintenance tasks within tight time constraints - having a centralized system allows teams to stay on task while decreasing Downtime and errors.
Facility Management: Every building requires maintenance to maintain an inviting workplace for visitors and employees alike, with equipment such as HVAC systems, chillers and data centers needing regular maintenance to operate optimally. Facilities managers need to use maintenance management as an efficient means to make sure service plans and scheduled maintenance align with usage patterns.
Reporting and Metrics: Experienced managers know the value of reviewing high-quality data to enhance decision-making, especially asset and maintenance management. By closely scrutinizing maintenance data, a manager can reach a more balanced budget balance while increasing department transparency. Furthermore, by improving cost projections with improved equipment data, they can also simultaneously examine many aspects of their operation, like facility and factory overhead costs and maintenance resource requirements, as part of this holistic analysis.
Maintenance Management is a business system in which multiple functions must work harmoniously to succeed. While their exact functions will differ based on an organization's structure and objectives, its overall work process remains similar. For success to occur successfully, all resources involved must have alignment and transparency across their processes and daily operations.
Different Types Of Maintenance Management
Companies across industries are innovating new approaches to improving equipment performance. In this section, when multiple forms of maintenance need to be applied simultaneously to optimize tool use, not all tools may suit every type of maintenance. We discuss which factors you need to consider before selecting tools that best suit you.
Reactive Maintenance: Reactive maintenance, as the name implies, involves performing maintenance when there are clear indicators that it is needed - visual inspections or other indicators often help identify this need for service. Reactive maintenance plans often consist of periodic audits or inspections, which help predict when servicing components whose lifespan cannot be predicted according to factors like usage; additionally, reactive maintenance provides emergency repair options in cases of sudden failures.
Maintenance: Pre-planning is essential when identifying potential failure points and when maintenance needs should occur. Some factors, including time and operating hours, can help determine this need; At the same time, proactive maintenance might sound appealing initially, but its risks include overdoing it by doing extra work, which doesn't enhance optimal operation. Systems must be meticulously examined while multiple data sources help refine service plans on an ongoing basis - preventive and predictive maintenance fall under this heading.
Time-Based Preventive Maintenance: Preventive maintenance should be scheduled based on specific time triggers; each piece of equipment usually determines its schedule using anticipated usage patterns and system wear data as the foundation for scheduling maintenance activities. Preventive maintenance tasks also entails monitoring the consumable life span and replacing parts as soon as they reach the end of their useful lifespan (but without incurring unnecessary operating time losses).
Predictive Maintenance or Condition-Based Maintenance: Predictive maintenance (condition-based or predictive maintenance) is a newer form that uses sensors and inline monitors to collect data to control equipment operation and determine when maintenance activities should occur.
Predictive Maintenance: Typically applies best when it involves costly systems with higher risks of failure due to its significant upfront capital outlay costs for hardware and software components required in its implementation.
Maintaining service history and tracking activities for each asset are among the many advantages maintenance management offers. Doing this makes selecting and planning maintenance more straightforward while giving a place for ongoing improvement - no system or method is flawless. Therefore, an iterative process with continual optimization during maintenance should always be practiced to achieve lasting success.
What Makes a Good Maintenance Supervisor?
Maintenance managers play a crucial role in the relationship between the maintenance director, other top executives, supervisors, and techs who do most of the service work. It is a job that requires technical and business skills to look at the bigger picture and address day-to-day needs. Let's look at some of the effective maintenance manager's essential skills and job requirements to gain a deeper understanding.
The job duties of a Maintenance Manager can be broad due to the complexity of the maintenance activities carried out by many businesses. The following are some of the key areas that a maintenance manager should focus on:
- Manage all Maintenance-Related Work.
- Coordination of work to meet regulatory requirements.
- Maintaining a suitable spare parts stock
- Manage service technicians, other employees, and staff.
- Comprehensive maintenance programs.
- Reporting the effectiveness of Maintenance Activities.
- How to increase asset productivity.
- Staff training should be adequate.
Maintenance managers can be many things. There are also some similarities between their responsibilities and those of an asset or facilities manager. Maintenance managers are expected to have various technical and soft skills. The most common include:
- Demonstrated ability to inspire others.
- Time management is a priority.
- Adaptability and the ability to pivot are key.
- Communication skills are essential.
- Problem-solving abilities.
- Teamwork is important.
- Basic knowledge of relevant equipment.
Maintenance managers must balance business goals for performance and equipment limitations, especially those in highly-specialized industries such as aerospace or healthcare with multiple clients. To be an effective maintenance manager, one requires both technical and soft skills - this collaboration between departments helps establish effective maintenance management programs; managers should seek feedback from technicians, operators and staff that interact directly with equipment for maximum success.
Many businesses have prioritized maintenance management as an efficient way to consolidate multiple functions into one asset and management framework. Computerized Maintenance Management Systems offer flexible platforms which can combine with asset tags or scanners for facility management to automate maintenance work orders and facilitate work orders being submitted electronically. Its future will largely be determined by technological innovations and innovative approaches that lead to new work processes being created and adopted by organizations.
Software That Allows You To Manage Your Maintenance
Software that optimizes asset performance, such as maintenance management software (a computerized management system or CMMS), centralizes your information on maintenance and offers tools for optimizing it. Any maintenance management software aims to improve your equipment's availability, efficiency, and reliability.
Maintenance management software provides a comprehensive solution to maintain physical assets in your facility. A CMMS allows you to manage, automate and streamline maintenance operations. Maintenance management software, which was traditionally on-premise, is now increasingly being hosted in the cloud. The information you need to manage your facilities is easily accessible on any device.
What Are The Four Fundamentals Of A Maintenance Management System?
Budgeting, task scheduling, compliance with regulations, optimization of workflows and safety standards are the four basic principles in maintenance management. Most programs can be tailored to train personnel in best practices or use work order software for complex maintenance requests.
Budgeting
The budget of the facility can be a constraint for maintenance managers. They will require better transparency to determine how these funds should best be used. It is important to prevent unplanned Downtime that small problems can cause. If these are not addressed, they will spiral out of hand.
Damaged machines can lead to operational costs, as they reduce the quantity and quality of your products. Not all expenditures are created equal. Maintenance managers will need to replenish MRO inventories to get assets back up and running. They must consider the functionalities of each item and weigh the cost versus durability tradeoff.
Schedule Tasks
It is important to balance different personalities in a daily or weekly schedule. It is a way to reduce costs in reactive maintenance. As work orders pile up, assign responsibilities to technicians and engineers to deliver a product on schedule.
The completed request will act as placeholders to record when and what procedures have been performed, allowing you to estimate how long the equipment is still usable. The calendar should include activities based on time and labor and notifications that remind staff.
Optimizing Workflows
Thirdly, automating workflows is the key to maintaining efficiency in every production phase. It will keep equipment running longer and make it less likely to experience sudden failures. A good maintenance strategy can maximize your processes, whether preventive, prescriptive or "run-to-failure".
When establishing procedures and workflows, there is always room to improve. Determining which administrative tasks should be performed urgently and by whom is crucial. It is important to reduce setbacks caused by a lack of coordination and to conduct regular inspections on machines to determine the production rate. Modifications can improve the durability of heavy-duty equipment.
Standards
Your industry's quality standards are always changing. Suppose you don't update your records to reflect new FDA and EPA policies. In that case, it can be very easy to forget about regulations. Many organizations use quality assurance checklists to ensure product safety during production or distribution.
Compliance is a multi-layered concept that includes local, state and federal laws. Training your employees on safety and the proper use of equipment is important. You should save all electronic records, including approved work orders or documented incidents. This will help you prepare for any future audits. One example is correctly labeling food and drinks before leaving the supply chain.
The Best Ways to Manage a Maintenance Team
It would be best to proactively communicate with your staff by listening to their feedback. Also, be open to suggestions and ideas for improving the processes. It is best to test scenarios based on failures before approving any request.
You should store all your written documentation on a CMMS. This includes policies, procedures, user guides, and the hierarchical flow of mechanical systems. The main goal is continuous improvement, so maintenance should be planned around machine availability.
Maintenance management is based on the following principles:
- Leading
- The Foundations
- The Processes
- Improve your life with the help of.
- The results of the study are:
Before you start gathering results, define your scope of work. Cost-benefit analyses based on previous outcomes can help you identify the implementation challenges. It is important to ask yourself: what results will be meaningful, and how can we overcome these challenges?
It's a fact that maintaining assets of high priority takes a great deal of effort and time. Therefore, it is sensible to aim for a higher quality performance while keeping the amount spent on time and money to a minimum. Your team will no longer be hindered by unpredictability with a plan.
Top Features of Maintenance Management Software
Software solutions for maintenance management offer many features, such as:
- Automated maintenance and preventive management.
- Centralized Asset Management throughout the Lifecycle of an Asset.
- Automated Work Order Management and Automation.
- Automated reordering, inventory management and tracking.
- Condition Monitoring and Analysis for Predictive Maintenance and Prescriptive Maintenance.
- Reporting & analytics dashboards.
- Digital record-keeping for audit preparedness.
- Compliance & Safety Management.
An intuitive maintenance management program with an easy-to-use interface allows users to easily access information and tools to help them do their job more efficiently.
Maintenance Management Software: What Are the Benefits?
There are numerous benefits of maintenance management software (CMMS) in your maintenance operation.
Centralizes Maintenance Information
Communication is key to the success of your business. A CMMS is a central repository for information and maintenance activity. It reduces miscommunications and allows maintenance teams to work together on the maintenance program.
Reduce Costs And Increase Asset Uptime
A maintenance management program can improve the efficiency of your maintenance programs by helping teams to fine-tune operations. A CMMS, for example, aggregates data from critical condition monitoring and sends alerts whenever a problem is detected. The maintenance team can then respond quickly when they're needed most. Maintenance management software can reduce unplanned costs and Downtime using proactive approaches like predictive maintenance.
The Streamlined Work Order Management For More Efficient Workflows
Asset management software is primarily concerned with automating and managing work orders. It reduces errors caused by manual work order management and increases technicians' efficiency.
Digitalizes And Automates Record-Keeping For Compliance And Audits
A CMMS can replace spreadsheets and manual filing, making it much easier to maintain and stay organized. For example, a maintenance management system can be used to log all information on assets in your facility into a central location. This digital record is easily exportable into a report or file in the event of an audit. It not only helps to ensure compliance but also speeds up audits.
Maintenance Management Software: Why You Need It
Software designed to manage maintenance is intended to give a complete overview of critical infrastructure data across multiple locations. Condition monitoring offers many advantages to businesses of all types and sizes, helping to inform decisions while simultaneously cutting maintenance costs and increasing uptime. Eliminating time-consuming manual processes enables organizations to better plan for any possible downtime events and ensure continuous operation.
Dashboard features include tracking MRO inventories, so you know which items to purchase when replacing damaged parts, auditing features for keeping up with SOP updates, and creating an asset maintenance history complete with photographs and certificates.
Utilizing computerized maintenance system software can bring numerous advantages to the lifecycle and efficiency. Teams can coordinate activities and maintenance practices across departments more effectively using this data-sharing mechanism - thus making their workday more efficient overall. A CMMS can provide greater insight into your facilities. Plus, integration with project management or accounting apps will increase productivity further and give a true picture.
How To Choose A Maintenance Management Software
It's not enough to consider features and functions when selecting the software for maintenance management; you must also consider whether the vendor provides adequate support in implementing its solution into your company. Furthermore, its technology should expand beyond core functions into other maintenance features, like vibration sensors or online condition monitoring techniques.
Maintenance management solutions providers must also offer comprehensive support and training services both before and after software implementation to shorten learning curves and enable continual improvements. Integrating legacy systems into new software applications is vitally important to ensure database integrity and reduce time wasted attempting to manage incompatible systems.
Conclusion
Arion ERP's computerized maintenance software enables large and small organizations to efficiently maintain preventive, corrective, and reliable assets like vehicles, equipment, buildings, or vehicle fleets.
Arion ERP's innovative maintenance management software will assist in leading and controlling your entire team efficiently while remaining within budget, performing daily maintenance duties, and making informed decisions for budget allocation. Get in touch with the most appropriate maintenance management software solution to increase efficiency.