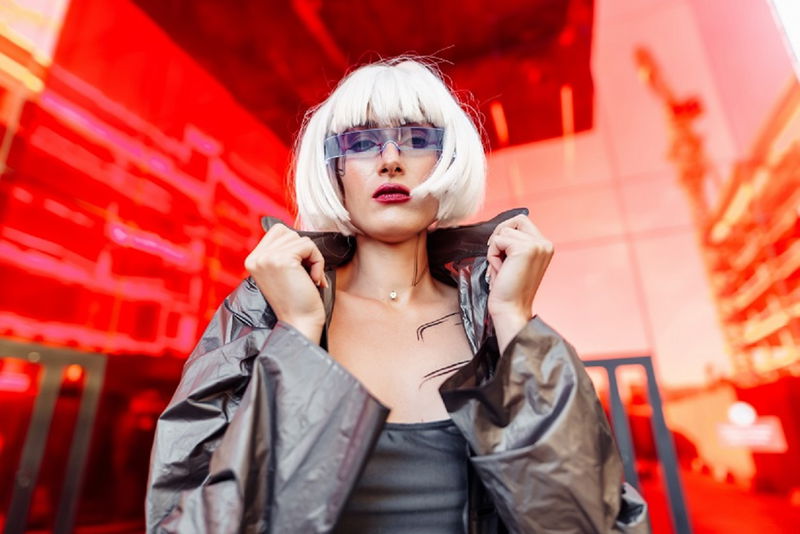
Software for maintenance management has never been so crucial, thanks to global competition or increasing pressures to digitize processes; all factors contribute towards improvement.
We speak to many managers navigating complex operational environments who face new operational hurdles every week. Maintenance teams in small to large organizations face growing pressure to increase efficiencies and productivity and reduce costs. These issues must all be mastered to stay afloat in any economy.
Over the last two decades, companies have experienced unprecedented product production levels at unprecedented speeds. Maintenance teams face considerable pressure from management to minimize costly interruptions to equipment that halt production without warning - the more automated an installation is, the greater its significance for using work order management tools to effectively prevent, diagnose and resolve complex asset failures efficiently.
Studies show that organizations can save 12-18% by consistently employing preventive maintenance as part of an integrated maintenance strategy, saving one dollar invested per dollar saved with preventive maintenance programs.
Managers, supervisors and operators face many difficulties optimizing maintenance programs, such as lacking knowledge about process details or historical data or meeting required analyses on time in conjunction with top management support. Making preventive maintenance part of an overall maintenance strategy saves dollars per dollar invested (two dollars for preventive maintenance is equivalent to saving five).
Maintenance management software can be an indispensable resource, helping users reduce stress. This guide explores the connection between software, team leadership and maintenance strategies; in doing so, readers should feel more at ease combining maintenance software with specific upkeep strategies.
What is Maintenance Management?
Maintenance management refers to prioritizing and strategizing to preserve company assets. It includes monitoring, controlling, and optimizing equipment life spans to enhance profitability, efficiency and reduce downtime.
Unplanned or reactive downtime can have detrimental repercussions for organizations, ranging from unanticipated costs and delivery delays to decreased customer service levels and satisfaction scores.
Common Challenges
Why is maintenance management so difficult? Maintenance management is often hampered by the following:
- The complexity of the production technology.
- Maintenance schedules are not in place.
- Work Requests are not properly processed.
- Staff with low technical skills.
- Insufficient historical data on equipment.
- Automation is not available.
- CMMS is not available
- Mobile apps for iOS and Android are not available.
Successful maintenance departments use automated software to organize tactical and operational actions for maintenance based on business priorities while adhering to relevant best practices.
Identifying "critical assets targets" allows organizational leaders to quickly assess those assets with the greatest influence over operational goals by performing analyses and automating workflows for strategic maintenance.
Enterprise Asset Management and Maintenance Management
Asset Maintenance and Enterprise Asset Management (EAM) are often confused. There are, however, key distinctions. Maintenance management takes an integrative approach to running facility operations, including asset and equipment management, labor/part inventory, and safety procedures.
On the other hand, asset management aims to optimize asset performance relative to output. Software for asset management monitors equipment efficiency and life cycles of assets to assist capital decisions, as well as depreciation estimates provided to accounting teams. Some asset management programs also include maintenance schedules, although these tend not to present work orders in an easily understood format; an administrator typically handles data entry.
What Are The Benefits Of Maintenance Management?
An Accurate Budget
Effective maintenance management systems can assist your organization in better comprehending where its resources go. An effective maintenance management program can help identify where staff time is being spent. Reports generated from such software allow maintenance managers to reorganize workflows or convince management to hire more staff through customizable advanced reporting key features that facilitate this task.
Schedule Work
Organizations often need an efficient preventive maintenance program for multiple machines and systems that entail extensive preventive maintenance needs, with many using Excel spreadsheets or whiteboard calendars that hang prominently in managers' offices to determine what work needs to be completed next.
Software designed specifically for maintenance management ensures all parties involved remain informed on what needs to be completed, when, and how, supported by digital audit trails for full accountability.
Manage Compliance
Are You Facing OSHA or Regulator Inspection? Are You Feeling Confused and Stressed Out by Document Retrieval Needs? With instant retrieval through any connected device and the ability to create customized reports to satisfy regulators. You no longer need to feel like this.
Maintenance management systems go beyond being used to share documents with regulatory bodies - they also ensure compliance standards are upheld, work isn't falling behind schedule, digital audit trails validate if tasks were completed on schedule by authorized personnel and more.
Iterate & Optimize
Each organization, and even each site, is unique. A one-size fits all approach is not realistic for any team. Managers must monitor real-time data to identify trends and gain actionable insight. Your senior maintenance technicians may be spending too much time on routine tasks that other team members can do. It can lead to bottlenecks in more complex maintenance activity and tasks.
Increase Safety
If you had your way, the team could follow a video about safety on their very first day at work and perform flawlessly. This is not realistic. Maintenance management software, in addition to optimizing assets and managing time efficiently, can also provide reminders for safety when performing tasks. Your team may not perform every task assigned. Safety instructions on mobile devices can help save money and lives.
What is Maintenance Management Software (MMS)?
Monitoring dozens or even hundreds of analog assets can be challenging. Hence, leading organizations employ Maintenance Management Software for everything from inventory tracking to repair operations management.
These platforms, Computerized Maintenance Management Systems (CMMSs), enable operational managers to assign and track recurring tasks; catalog assets by serial number, location and service dates; enhance compliance through digital audit trails; identify cost-saving opportunities with advanced reports; monitor conditions via sensor technology.
What is Maintenance Management Software Used for?
The following industries use maintenance management software:
- Manufacturers
- Fleet Management
- Facilities Management
- Hotel Accommodation
- Healthcare
- Food Service
- Property Management
- Municipalities
- Oil & Gas
- Utilities
- National & State Parks
- Storages
Plant Engineering Study found that 44% of companies still rely on paper records for recording maintenance plans, leading to many questions about why all PM programs don't utilize maintenance management software solutions. One common belief about maintenance management platforms is that they would be too complicated or time-consuming, but these beliefs no longer hold water. It is good news to see this is no longer valid.
Does Maintenance Management Software Have a Difficulty Use?
Regardless of technical abilities, workers at organizations of any kind can learn quickly how to use mobile maintenance apps on smartphones, tablets and desktop computers. Maintenance management platforms offer comprehensive maintenance management.
Few programs are tailored specifically for mobile use; most providers boast great desktop software program user experience via user-friendly interface instead. But given most workers always carry their smartphone around with them - no matter where they may be working from -- selecting an effective and user-friendly mobile solution may make sense; MaintainX is among the leading options here, offering both desktop software functionality and its popular and user-friendly mobile solution.
What Maintenance Strategy Should You Choose?
It's now response time to examine maintenance processes and strategies. Remember that the best maintenance organizations use different strategies depending on what physical assets asset managers manage.
What Is A Maintenance Strategy?
Maintenance strategies are used by companies as an approach for keeping assets working at peak condition by performing regular checks and analyzing KPIs (Key Performance Indicators), failure rate metrics, cost analysis etc., before replacing or repairing defective equipment. High-level programs combine strategies based on individual equipment needs for maximum asset upkeep.
Maintenance strategies must be tailored specifically for every piece of equipment to match its unique requirements, budget and goals. Every business has a different ideal balance between costs and performance that they strive for; often, switching from preventive to corrective maintenance is enough to improve that ratio.
Select an effective maintenance strategy to:
- Increase equipment availability and reduce downtime.
- Predictable maintenance costs and low operational costs
- Optimize the performance of your facility and its production.
- Keep a high standard of safety.
- Increase customer satisfaction
- Equipment life extension
Customize Maintenance Strategy
However, selecting an effective maintenance strategy can be challenging. Equipment types vary significantly across industries, facilities, and locations, as does return on Investment (ROI), so companies must employ multiple strategies to protect their assets effectively.
Consider the mining industry. According to statistics, 82% of machines fail randomly, resulting in ineffective scheduled maintenance programs. Recently, however, many mining companies have made considerable investments in technologies supporting predictive maintenance.
Specifically modern sensors which monitor machines' temperature, vibration and humidity in real-time for more cost-effective maintenance measures; PDM can often cut maintenance costs by 10-20 percent. However, preventive maintenance is usually not cost-effective in most instances. Sensor technology - while relatively new on the market and still expensive - often has high upfront costs.
Maintenance management software system or a centralized platform with primary function helps organizations in field balance reactive and preventive strategies; for instance, a facility might use run-to-failure maintenance on easily replaceable light bulbs while using preventive maintenance on $10,000 forklifts. Step-by-step, we will guide you through comparing values and costs tracking before selecting an effective maintenance strategy for your building.
What Is The Best Maintenance Strategy For You?
The best way to choose a strategy for maintenance is as a process that involves two levels:
- Maintenance Strategy For Your Whole Facility: You can determine your global maintenance strategy by comparing the proportion of proactive to reactive maintenance and the approaches you use.
- What Maintenance Method Do You Use For Each Asset: Each asset has its unique maintenance method adapted for its importance, cost, and consequences of eventual failure.
Maintaining all pieces of equipment uptime requires creating a maintenance plan and strategy, considering each piece's value and cost of failure when choosing an optimal plan for them. Consider reactive and proactive maintenance; reactive is after an incident, while proactive preventive maintenance occurs before it occurs, and reactive response is after a malfunction. These two maintenance categories may also be divided further into specific methods (which we will cover later on).
Choosing an optimal maintenance strategy involves considering both the asset's value and the cost associated with failure in making this decision. When making these choices, it's also wise to factor in value and cost when choosing the optimal maintenance strategy (more about that later). In choosing an optimal plan, one must consider both the asset's value and the cost associated with failure when making this decision (more about that later). When making this choice between reactive vs. proactive or reactive, maintenance should also take into account as much of the impact this decision makes on performance as much impact it has:
- Costs of replacing or repairing equipment.
- Downtime can cause financial loss.
It is important not to try and alter maintenance strategies beyond what you can handle now.
How Does Your Organization Compare To Others?
Asset tracking will vary depending on your equipment and its importance to your business. The level of care you give a lightbulb on the supply shelf is not the same as the attention given to a piece of critical equipment in your production line.
Actionable KPIs:
- How much maintenance is proactive compared to reactive?
- How should reactive maintenance be balanced with preventive?
- Do you use a platform for CMMS? Does it work for you?
- What is your team's biggest challenge?
To choose the right maintenance strategy, you must assess existing organizational data, such as asset performance/criticality, uptime/availability, maintenance costs, and failure rates. After obtaining the "big picture" of your company's current operational and maintenance structure, it is recommended that you review maintenance strategies before conducting FMEA or a criticality assessment.
Understanding The Types Of Maintenance Strategies
-
Reactive Maintenance (Corrective)
Corrective maintenance takes three forms, either planned run-to-failure maintenance (PLGTF) or unplanned, run-to-fail maintenance (UNPLFTF), with both being administered as unscheduled activities that run until failure has been reached or as unscheduled run-to-fail maintenance (ULTFM). Corrective maintenance may take an erratic or unscheduled form. Still, its objective should always be the same.
Identify, isolate and address a problem as quickly and cost-effectively as possible. With reactive maintenance (fixing defects that caused production shutdown), defects that caused malfunction are corrected as quickly as possible. In contrast, reactive maintenance will restore equipment but does not necessarily guarantee optimal functioning compared with corrective measures (for instance, Reactive maintenance only brings equipment back online but won't ensure optimal working).
Corrective maintenance refers to repairs made when an issue has been detected. Still, it has yet to cause the machine to exceed its range of performance. An example would be replacing oversensitive sensors. At first, correctional maintenance may save money with no preparation required. However, over time, downtime and asset depreciation costs increase and unplanned expenses become unmanageable.
Corrective or reactive management may not always be the optimal approach, with preventive maintenance often not worth its costs if equipment failure does not result in downtime or safety hazards.
-
Preventive Maintenance
Preventive maintenance should be conducted regularly to avoid problems from developing. It can include monitoring parameters, time intervals or usage metrics. Scheduled downtimes for repairs or component replacement may also be scheduled under preventive maintenance plans; regulatory obligations often necessitate this practice. Preventive maintenance also serves to identify failures earlier, thereby decreasing reactive maintenance needs - preventive work orders prevent you and your team from being caught unaware by sudden issues that come up unexpectedly.
Time-based or usage-based maintenance interval schedules require only domain knowledge and awareness for effective management. A CMMS will assist in organizing preventive maintenance schedules and empower team members by informing them when to perform work. Managing such an exhaustive schedule could quickly become tedious and cost prohibitive - leading to "over maintenance." Finding balance in life is vitally important.
-
Predictive Maintenance
Predictive maintenance aims to decrease the frequency and costs associated with preventive maintenance programs by monitoring equipment conditions using techniques such as tracking. Predictive maintenance allows just-in-time equipment maintenance by optimizing availability while decreasing maintenance times.
It works best with assets with periodic or irregular failures; for this task to be accurately performed by your team, you may require monitoring and control tools that monitor/measure changes accurately over time. Though some companies find predictive maintenance too expensive or time-consuming to pursue effectively, as IoT sensor costs continue their rapid decline, it has never been more possible or affordable than ever.
-
Prescriptive Maintenance
The new generation of maintenance methods uses equipment conditions to determine the optimal maintenance period. The temperature profile of a component will help you predict when it is most likely to break down. A prescriptive evaluation could tell you you have 20% more running time before failure if you reduce the temperature by 10%. The development of prescriptive monitoring has also just begun. But artificial intelligence (AI) and machine learning are progressing toward prescriptive maintenance.
-
Reliability Centered Maintenance
It is an enterprise-wide method. All of these common types can be included. The goal is to optimize the maintenance plan so that all equipment parts perform at their best. The maintenance plan must be continuously improved.
Perform A Criticality Analysis
Criticality Analysis measures each asset's significance within your facility. Items will be organized as follows. Conduct a criticality analysis to better manage your resources and identify items of high importance, such as conducting an inventory.
Your first preventive maintenance task should be identifying your critical assets. Maintaining them is of vital importance as malfunctions of equipment could have severe repercussions for safety, profitability or environmental impact - even equipment with spares in stock is typically not considered vital - keeping a matrix of criticality handy may help keep track of them all effectively.
Maintain Each Asset According To Its Maintenance Strategy
After establishing your criticality assessment, evaluate each piece of equipment based on two factors: cost of failure and ease of monitoring. This will help match every asset to its optimal maintenance strategy.
Explore The Costs Of Failure From Multiple Perspectives:
- What will be the impact of downtime on your business?
- Is the health and safety of your team at risk?
- Replacement parts are readily available.
You Can Ask Similar Questions About How Easy It Is To Monitor:
- Do you know how to recognize leading indicators that can help to prevent unplanned downtimes?
- Is monitoring the asset worth the investment?
- Can you track this asset compared to other assets within your operation?
Secondary assessments help determine which maintenance program best matches each asset. Assets with difficulty to monitor may have low failure costs that are easily replaced or repaired; in such instances, run-to, failure maintenance would likely be best; for critical equipment with regular monitoring capabilities, predictive maintenance is ideal, while preventive maintenance task guidelines and regulatory compliance from manufacturers should also be strictly observed and adhered to as part of any prioritization effort. Once identified as assets requiring prioritization, ensure you follow them.
Get Real-Time Information
Maintaining and servicing assets are vital parts of success for any team, which requires real-time updates maintenance information to stay abreast of.
Useful sources of information include manufacturer guidelines, data, historical trends, and best industry practices. Utilize this knowledge to draft Standard Operating Procedures (SOPs) so your team performs maintenance correctly; additionally, consider additional training if required.
Important data sources and knowledge to use as information include manufacturer data, guidelines and historical analysis. You can then use this knowledge to develop Standard Operating Procedures (SOPs), so your team performs maintenance correctly. Furthermore, consider additional training if required.
Take Into Consideration The Availability Of Resources
It's important to take into account the accessibility of resources when updating your maintenance strategies. The majority of companies only allocate a limited amount of resources to maintenance. To successfully implement new strategies, managers may have to mobilize additional resources:
- Budget
- Workforce
- You can also find out more about.
- Inventory
- You can also download the software platform.
Every industry faces pressure to produce more with limited budgets and increasing workload demands; thus, prioritizing maintenance resources according to asset criticality is essential for success.
Your organization could be unknowingly wasting time and money by relying exclusively on reactive repairs. In such an instance, switching from reactive maintenance to proactive can save both money and time while increasing efficiency - even if most routine maintenance tasks are being conducted proactively, they can still be modified for maximum ROI.
Your assets could be receiving excessive maintenance. This may involve equipment rarely used yet still serviced regularly or parts that pose a minimal risk but require replacement - elements that are best left under an ongoing program until failure arises. Unfortunately, changing maintenance schedules for every asset at once is impossible, as doing so would overwhelm teams or consume the necessary resources.
Assess the Return On Investment of Maintenance Services provided for Assets. This will allow you to identify which items are of the highest importance, which would result in the greatest breakdowns or maintenance expenses if neglected properly, and begin by prioritizing high-risk/high-value assets before gradually adding other equipment into your maintenance strategy.
All Aboard
Teamwork and communication are key to the most effective maintenance strategies. It's crucial to involve your whole maintenance team when planning a maintenance strategy. It will ensure that:
- It's not as if you are missing important information.
- Your team will be fully committed to the change you are making.
- The team must know the extent of the work.
- It is a smooth business process from start to finish.
Establish a committee or team to implement some of the most significant changes to your overall maintenance strategy. Be sure to include maintenance personnel from engineering, operations and operations to maximize adoption and acceptance across your organization.
Maintenance Management Software: Track your progress
Final Step - Evaluate Progress. Make adjustments if things aren't progressing as intended; for instance, additional training for team members to implement your maintenance strategy or purchasing of tools, materials or spares might be required to execute it effectively.
Utilize a Computerized Maintenance Management System (CMMS) to track progress, measure key performance indicators and create meaningful reports. SaaS provides different advanced features of its CMMS as well as customization options dependent on company pricing plans and software CMMSs. Before changing strategy at your facility, collect benchmark data that measures its performance - likely, your most beneficial KPIs include the following:
- Equipment Performance
- The Mean Time Between Failure (MTBF),
- Time Mean to Repair (MTTR).
- Maintenance costs
This will allow you to draw meaningful conclusions from your new KPIs after launch. After the launch, you can draw valuable conclusions from this preliminary work. You should review your strategy frequently to identify realistic improvement opportunities that can be achieved in the near-medium term.
Summary
CMMS (computerized maintenance management systems) are computerized maintenance management systems used to plan, control and monitor maintenance and asset life extension costs. Their purpose can include keeping assets in excellent condition across one or multiple sites or upholding high priority levels of availability and technical quality for groups of equipment like vehicles or machinery. Get in touch with the most reliable maintenance management solution.