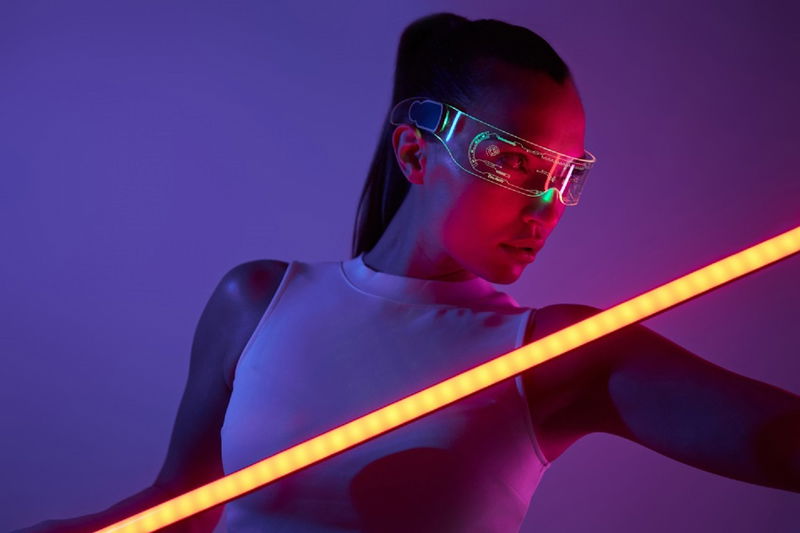
Suppliers and producers are moving quickly to embrace lean Manufacturing. According to automotive industry insiders, this trend will continue. This is due to a growing labor shortage, shifting employee attitudes, rising costs, and renewed interest in digital technologies Lean.Output, effectiveness, contentment, and productivity have all greatly increased.
What is Lean Manufacturing?
Lean Manufacturing is a technology process that maximizes productivity and minimizes waste in Manufacturing operations. According to the lean principle, waste does not add value to customers.
Lean manufacturing procedures and processes are streamlined to minimize waste and increase production. Lean is described as "a technique of doing more and more with less and less - less human effort and less equipment - while approaching closer and closer to the ideal state of delivering customers what they want".
The Key Benefits of Lean Manufacturing
- Eliminate Waste: Waste can negatively impact cost, timelines, and resource utilization. It does not add value to products and services.
- Quality Improvement: Keeping companies competitive and meeting customers' changing demands and desires is possible with improved quality. You can stay ahead of your competition by designing processes that meet customer expectations and needs. Quality improvement is at the forefront.
- Lowering Costs: Storage costs can be increased by better materials and processes.
- Time Reduction: Inefficient work practices can also waste time and money. More efficient methods create shorter lead times, which allows goods and services to arrive faster.
What are The 5 Principles?
These five core principles are value, the value stream, and flow. They can also be called pull, perfection, flow, pull, and value. These principles are used to implement lean.
- Value: This is the value that the customer sees. It refers to the price they will pay for products and services. The manufacturer or service provider then creates this value. They should eliminate waste and cost to achieve the best price for the customer while maximizing their profits.
- Map The Value Stream: This principle involves analyzing materials and other resources needed to make a product or service. It aims at identifying waste and making improvements. The entire product's lifecycle, from raw materials to disposal, is covered by the value stream. Every stage of the production process should be examined for potential waste. Everything not adding value should be eliminated. This step can often be achieved by using chain alignment.
The joint efforts of engineers, scientists, and designers are often required to complete the complex manufacturing streams of today. One part of a bigger activity stream is the actual production of tangible goods.
- Create Flow: To improve lead times, core functionality barriers must be removed to create flow. This allows processes to flow smoothly and can be completed with minimal delay. Disorganized production can lead to production delays and other costs. Creating flow is a way to ensure a steady stream of production or delivery.
- Create a Pull System: A pull system is one that only starts work when there's demand. This contrasts with push systems used for manufacturing resource planning (MRP). These systems calculate inventories and set production to meet sales forecasts or other production goals. This can lead to a shortage of products or too many products being produced due to inaccuracies in many forecasts. This can increase warehousing, schedule disruptions, and poor customer satisfaction. Pull systems only work when there is demand. They rely on flexibility, communication, and efficient processes to succeed.
A pull system allows teams to move on to new tasks after completing the previous steps. This allows the team to be flexible and adapt to any challenges, knowing that most of the work is still relevant to delivering the product or service.
- Perfection: Continuous process improvement is what Toyota Motor Corporation (See 'When and Who Invented Lean Manufacturing?' above). Continuous improvement and assessment of processes and procedures are required to ensure that Lean Manufacturing produces the best possible value stream. Continuous improvement is a key technology concept that can make a lasting and meaningful impact on an organization's culture. It requires measurement metrics like lead times and production cycles, as well as cumulative flow and cumulative flow.
To foster a culture of continuous improvement at all levels of an organization, from project managers and team members to the top, they must spread this culture to all levels.
ERP and Lean Manufacturing Hand in Hand
Since the beginning, manufacturers have worked to improve their lean manufacturing processes. Toyota, an automotive company, created lean manufacturing. Any industry can benefit from lean principles. Lean manufacturing is a way to eliminate waste and put the customer experience and the final product at the heart of every corporate operation. Lean manufacturing, a successful product strategy, increases output and reduces costs.
How can someone improve the efficiency of their business? The first step is to implement excellent enterprise resource planning (ERP). Many people think that ERP, or lean manufacturing, is inherently competitive. The ERP System is the lifeblood of your company. You can use it to manage the processes on your shop floor, get current information about client wants, and make plans. These elements are necessary for trash disposal.
You might consider implementing an ERP system to support your company's shift towards lean principles or restructuring your ERP strategy for Manufacturing efficiency.
Want To Know More About Our Services? Talk To Our Consultants
Advantages and Disadvantages
Lean Manufacturing has many advantages and disadvantages, depending on where and how it is implemented.
Advantages
-
It Saves Time and Money
Lean Manufacturing is known for its cost savings. Businesses of any size can benefit from more efficient workflows, resource allocations, production, and storage, regardless of their output. This allows businesses to provide products faster and with lower lead times. It can also save time and money by having a more efficient workforce.
-
Environmentally Friendly
Reduced waste of time and resources, as well as removing redundant processes, can help to reduce fuel and energy costs. This can have a clear environmental benefit, and use more efficient equipment that can save you money.
-
Increased Customer Satisfaction
Customer satisfaction is improved by ensuring that the product or service is delivered to the customer at the right price. Happy customers will more likely recommend your products or services to others.
Disadvantages
-
Safety and Well-Being of Employees
Lean critics argue that it is dangerous to employee safety and well-being. It is possible to ignore the stress placed on employees with little room for error at work by focusing on streamlining and reducing waste. Lean can be compared to 19 th century scientific management techniques, which were opposed by labor reforms. They were considered obsolete by the 1930s.
-
Hinders Future Development
Management can cut corners in areas that aren't essential to their current strategy because of lean manufacturing's focus on reducing waste. These areas may still be essential to the company's future and legacy. Lean can lead to a tendency to focus too much on the past and neglect the future.
-
It isn't Easy to Standardize
Some critics argue that lean Manufacturing is more of a culture than a method. It isn't easy to establish a standard model for lean manufacturing. This can lead to the perception that lean manufacturing is not a solid technique but a loose one.
Read More: Why It's Time To Switch To ERP System For Your Business
What's Digital Lean?
There has been lean Manufacturing for almost a century.When conducted properly, it has been a very successful practice. Industry 4.0's digital revolution increases the possibility of reducing operational expenses, enhancing working conditions, and streamlining procedures.
Lean Manufacturing is about improving operational components that add value and eliminating those that don't. Digital-Lean, which uses the latest technology, accelerates the process. Distributors and manufacturers have seen significant improvements in automated 3-way matching, paperless inventory picking, and supplier collaboration portals. Machine monitoring systems and many other programs can help manufacturers reduce waste and save money.
What Should You Know About
These five guidelines can help distribution or manufacturing organizations adapt to a new operating environment.
Find Out The Value Of Your Customer
Your success is dependent on your customer. Your customer's needs and requirements will determine the product's value.
It Is Crucial To Map The Value Stream
Determine the value of your customers next. You may then map out your value stream as a result. Doing this will deliver your product or service to the customer's door from the quote. Steps that don't offer value can be eliminated.
Change to a Pull-based Approach
Because businesses only stock and manufacture what they need, a pull-based strategy reduces inventory waste. Make to Order (MTO) is a pull-based manufacturing system. A consumer order initiates the cycle. MTS manufacturers often base their replenishment levels upon customer initiatives, long-term contract terms, and market conditions. Material is shipped from stock when customer orders or releases are received. This pulls on the value stream to restock. This isn't easy because replenishment levels depend on past and future data. In every situation, a solid supply chain strategy is essential.
Keep Going
Lean Manufacturing is not a one-time strategy to optimize a company's operations. Lean manufacturing is a continuous process that optimizes workflows. This principle should be embedded in your company's culture and communicated to all employees. It is the basis of your business.
How ERP Improves Lean Manufacturing
Let's start by briefly defining lean Manufacturing for those who are unfamiliar. The goal of lean Manufacturing, sometimes referred to as "lean," is to reduce waste in the production process. This holds for lost money, time, and resources. These are the origins of waste in lean Manufacturing. ERP may enhance lean manufacturing by giving you visibility and the necessary tools to find and stop unnecessary operations. These are just a few of the numerous ways that ERP may enhance lean manufacturing processes.
-
Transport Waste Reduced
This occurs as resources or goods are transported from one location to another. This could be a dock, a series of shelves in a warehouse, or a staging area. Resources, people, and equipment are needed for these tasks. The client or manufacturer cannot gain further value from this action because it does not result in income. There is less waste since material handling takes less time. Lean manufacturing is made possible by ERP by providing users with resources to enhance production and logistics. Teams may track how resources are being used with the help of ERP, which also offers suggestions for streamlining or accelerating operations. They can track inventory and monitor how much equipment is being used.
-
Reduction in Inventory Waste
Suppose your business is a mixed-mode or make-to-stock (MTS) manufacturer. In this case, you will need to ensure that you have sufficient raw materials and finished goods. On the other hand, make-to-order businesses have raw materials, semi-finished products, and finished goods related to inventory. Capital is therefore tied to stock at all levels. A lot of merchandise isn't good unless your stockpile is unprofitable. ERP systems are the foundation for maximum effectiveness. ERP systems can help manufacturers eliminate inefficient production planning and distribution techniques, allowing them to keep production going while retailers increase food replenishment cycles. ERP can improve lean manufacturing through the ability to forecast, analyze historical sales, and provide accurate product data. It also allows for automatic reordering and setting minimum and maximum stock levels.
-
Motorcycle Waste is Less
Equipment and personnel are considered motion waste. It's when motion or effort is made that doesn't add value. Poor plant layout is the leading cause of motion waste. Poor plant layout can lead to excessive wear and tear on machinery and traffic bottlenecks. It is difficult to make changes to a production floor without affecting production. ERP Solution can improve lean Manufacturing by providing data on machinery utilization, job planning, scheduling, and other floor information. Manufacturers can collaborate with engineers and suppliers to see which processes are slower or operate at a lower efficiency.
-
Less Time Wasted Waiting
If nothing is happening, time is lost. This could be caused by production bottlenecks or machine downtime. Or, it could simply be that production teams need to work together. ERP can help improve lean manufacturing by giving teams one source of data they can trust to retrieve the needed information. It helps identify bottlenecks and plan jobs and schedules better, and it can also help identify bottlenecks. It facilitates decision-making with the data required to execute mission-critical strategies.
-
Avoiding Over-Production
The main source of all waste is overproduction. This is the root of all waste in lean production capacities. This indicates that you either generate more things than consumers require or that consumers won't need goods till production is underway. This may lead to issues with inventory. Overproduction may result from poor Time to market demand planning, procurement, or supply chain management. Lean Manufacturing is improved with ERP. It offers advanced technologies specifically designed to improve supply chain management, streamline procurement procedures, and properly estimate demand based on market trends.
Read More:- Efficient ERP System helps Manufacturers Face The Challenges of 2022
-
Avoiding Over-Processing
Over-processing refers to the practice of doing work that is not valuable. You could be painting the car's front fender on the production floor. It will not be visible to a mechanic. This is not a valuable activity for the customer and requires more time from your production staff. Paint is expensive. Over-processing could also impact your field service or sales teams. It can be a waste of time to enter data manually. It can be costly for customers if you make errors in order entry. These processes can be automated with ERP, which increases lean manufacturing. One-click can convert a quote into an invoice. You will also get critical insights into your sales and production goals.
-
Avoiding Defects
Defects can cause time and material waste as well as consumer irritability. Defective products could further harm the reputation of your industry sector if they end up in customers' homes or businesses. The elimination of flaws must be a top priority. It might be challenging. By automating checks and coordinating production with your requirements, ERP may enhance lean manufacturing. Raise any issues you have with product development or procedures that need to be ERP-aligned so that your teams can take care of them before they become a problem.
-
Quality Management
Lean manufacturing tactics and quality management strategies are likely to collide. Lean concepts are meant to cut down pointless procedures. However, quality management can urge you to enhance processes and verify. ERP systems come with quality control modules that let you maintain the quality of your products without adding waste to your operation.
This lesson will allow you to evaluate your quality plan from a lean producer's perspective and with a critical eye. Use your ERP's metrics and tracking programme to order each stage. What element has the most impact on the end product's value? When should you concentrate on decreasing returns in terms of time and money? Your attention should be on your customers and how they use your goods. When you have a quality strategy, customers anticipate specific services. ERP enables you to develop superior products while cutting costs while maintaining quality and lean manufacturing concepts.
-
Demand Planning
It is crucial to accurately plan your demand to minimize waste and reduce product stagnation. Many companies view demand planning as a guessing and sometimes luck-driven game. This kind of thinking can cause serious damage to your business as well as your client relationships. If your product is unavailable or you delay client payments, customers will move on to more reliable businesses.
An ERP system well implemented and combined with lean manufacturing methods can help you accurately forecast your stocking and purchasing requirements. To create well-informed quotas for each season or period, you can use historical demand data. This planning allows you to account for price fluctuations, availability and expected storage space. Using "reasonable guessing" to plan your market demand strategy is unacceptable. ERP and lean Manufacturing are a natural combination. ERP data gives you the information and forecasts to support your lean principles.
Want To Know More About Our Services? Talk To Our Consultants
Conclusion
In today's unstable economic environment, a business needs to be adaptable without breaking. This can be accomplished using the digital transformation strategy known as digital Lean. The ERP system from Arion ERP gives your manufacturing facility quick returns and profits.
Lean Manufacturing is a method that streamlines and improves manufacturing processes and other services. Customers get enhanced benefits and time savings by eliminating waste.
Every organization that practices continuous evaluation and improvement can implement lean. Lean adoption is supported with the help of all employees. Innovation of TWO may help with various manufacturing and production-related product design and process development support operations.