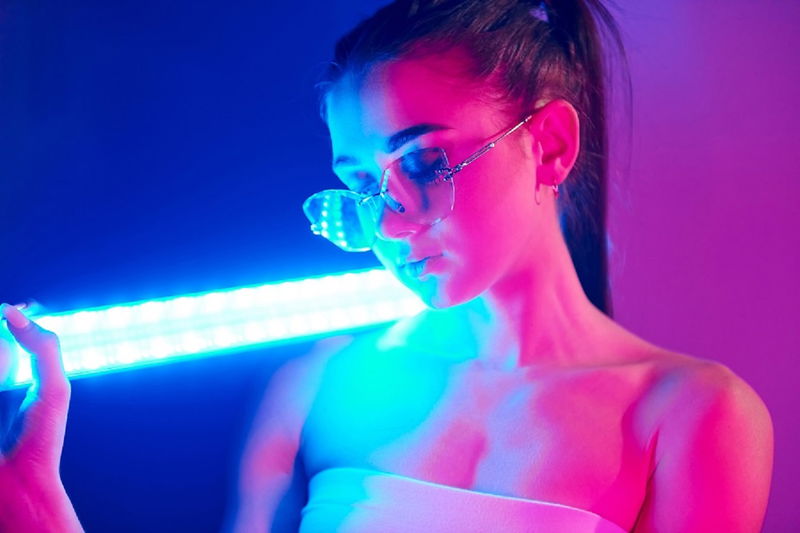
Computerized maintenance management systems monitor and oversee the condition of buildings and equipment used by an organization. Companies that own and manage buildings, equipment or other facilities typically engage in maintenance and repair activities as an integral component of keeping assets operationally efficient and turning over assets quickly.
Achieving excellence through routine preventive maintenance ensures technical availability for machinery; maximum productivity with minimum downtime for optimal asset turnover.
Maintenance and repair business processes are employed at various points throughout an asset's lifespan - from acquisition to disposal. Technicians perform direct maintenance work while managers (chief mechanics or repair managers) oversee its planning and execution. Many enterprises differentiate between the types of maintenance and repairs:
- Maintenance Preventive: The manufacturer will specify the frequency of maintenance in their operating documentation.
- Maintenance Predictive: This is done by analyzing the information that the equipment's sensors provide in real-time.
- Maintenance: It is the supervision and repairs performed by service centers.
- Routine Repair: The asset is kept operational by performing this repair.
- Medium Repair: The goal is to maintain the asset's good condition and extend its life.
- Overhaul: This aims to restore the service life and ensure that it can be used again.
Equipment can be costly, so maximizing its usage is essential for a positive ROI. Software for maintenance management:
- Keep detailed records of all your assets.
- Schedules and performs maintenance activities. Maintains documents and historical information. Keep track of completed work.
- All data, such as manuals, work orders, histories, etc., are stored in a central location. The personnel can access the information from anywhere via computer, mobile phone, or tablet.
- generates desired reports;
- HTTP, as an example, can be used to protect against cyber threats.
When a company needs to modify or expand its maintenance management software, it consults experts to see if additional software can be integrated. Upgrades can either be specific to an industry or expand categories such as inventory and asset management to enhance the database. A file-sharing platform that allows startups to share consultation documents and audits.
What is Maintenance Management Software, and Why do you Need it?
Systems for maintenance management are used to maintain and manage a database that includes information about the technical status of assets, their operating conditions, and any work performed on them. Software for maintenance management is typically a collection of modules that include:
- Manage data on the equipment.
- Maintenance and Repair Planning.
- Order management
- Tracking performance and results.
- The control of spare parts and tools.
- Logistic management.
- Storage of Maintenance Procedures and Reference Information.
- Information about equipment condition and technical data.
Maintenance management software provides an efficient tool to oversee multiple plant assets. Maintenance software may offer additional features like barcode or QR scanning, voice recognition technology integration and even intelligent equipment sensors for improved management.
Various solutions go beyond maintenance management systems that address specific functions. They're standalone products not necessarily classified as critical maintenance management software but that do integrate.
Maintenance management systems have many advantages:
- Equipment downtime is a major cause of production and logistics disruptions.
- You can increase employee productivity by planning activities according to resource availability.
- Maintenance management systems reduce unplanned downtime and travel time for field maintenance technicians.
- Companies can track assets in different locations and see where they are being used.
- Preventive maintenance can help companies avoid costly repairs and replacements of assets.
- This allows for increased equipment uptime and better use of assets.
Maintenance management software can reduce production mistakes, equipment breakdowns and labor costs while potentially helping prevent injuries. It uses various tools to meet key performance metrics, including data management, work order scheduling and calendar management tools, inventory tracking capabilities, and asset tracking analytics.
Look for software that provides consistent work orders and which is accessible on the cloud at all times, both locally and remotely. Make sure it can scale to meet future business demands, has an interactive and customizable user interface, and allows for custom modifications. If this concept is new to you, here is an outline of key features you should seek in a routine maintenance management software solution:
Here Is An Outline Of Features You Should Keep An Eye Out For When Searching For Software Solutions:
Preventive Maintenance
Imagine having to stop operating because a key piece of equipment failed due to poor maintenance; that part could easily have been replaced, while preventive maintenance helps prolong equipment lifespan while cutting costs; the software automatically generates service and inspection plans designed to maintain them.
Creating preventative maintenance schedules for electrical maintenance can save both money and customer service issues down the line. Plus, automatic status updates of equipment being serviced regularly help avoid expensive repairs and poor customer experience.
Work Order Management
An effective work order management solution can significantly cut back the time necessary for handling requests, saving both you and your client valuable time and effort. With this tool, you can synchronize work orders across devices such as laptops, smartphones and tablets for seamless work order tracking and management.
Automated tracking in real-time provides real-time updates of request statuses. Many businesses today need work order management software in their arsenal; choosing one should not be difficult, though. Be sure to select flexible work order software, which allows for quickly creating and assigning work orders to individuals for approval before manual process orders efficiently.
Maintenance Log
Maintenance logs help service technicians quickly identify critical asset problems and quickly provide solutions that best address them. This saves them both time and effort when resolving your issues quickly. Logs should document everything that happens or will happen about your assets, from repairs performed on specific assets (and when those repairs took place) to maintenance requirements and changes that arise over time.
Maintenance Checklist
Service agents often become so consumed by their work that they forget some basic maintenance steps, making a checklist an essential strategy. An efficient checklist will assist both you and your team in identifying all tasks required to maintain equipment efficiently, helping everyone involved stay focused on necessary tasks. Plus, its features offer information regarding the activities' current status so managers can inform all involved.
Inventory Tracking
Businesses and organizations had tracked inventory with spreadsheets for years before 2008. Unfortunately, spreadsheets weren't designed specifically for inventory tracking, so mistakes and errors often led to operational delays and further complications. Imagine, for instance, having a spreadsheet containing thousands of inventory records but finding out that there were only 100 when counted manually. Unfortunately, this issue arises frequently with spreadsheets.
Maintenance management software offers inventory tracking features to assist with keeping an eye on how stock moves throughout your organization. Your maintenance team can use this feature to perform their duties - tracking automatically in real-time accurately. When stock is low or running low, it informs staff who monitor it by automatically creating reorders and sending them directly back out when reorders become necessary.
Reports and Analytics
If you want your business to thrive, the ideal software for maintenance management should produce reports from multiple data sources, such as asset histories, maintenance schedules and labor skills.
Inspection reports or analytics allow your company to stay abreast of its overall performance by tracking assets that require enhancement or replacement and by showing you which skill sets need improvement or are lacking among team members based on results from prior months - this allows for continuous team learning that increases both productivity and efficiency.
Vendor Management
Keep track of all your vendors regularly; vendor management software provides this essential function. With it, you can easily create work orders without calling or emailing each one individually.
Logging in is made easier using your credentials provided, with vendors being able to monitor all activity quickly so that problems can be identified quickly and resolved as efficiently as possible. In addition, tools exist that track time taken for orders, calculate c most accurately, and integrate work order management for improved operations.
Which Is The Best Solution For Maintenance Management?
Maintenance management software solutions are readily available for businesses of all sizes. There is software tailored specifically towards industries like manufacturing, transportation and hospitals - it would be wiser to select an industry-appropriate CMMS like Arion ERP than trying one which doesn't meet your reporting and service needs; each industry may have distinct reporting and service demands, so choosing one which fits will make familiarizing yourself and your team members with it much simpler as well as guarantee compliance using templates or workflows that meet industry guidelines and ensure regulatory compliance more quickly and easily.
Popular CMMSs like Arion ERP's maintenance management software application that helps streamline maintenance procedures by easily turning work requests into work orders; its QR codes simplify scanning assets straightforwardly too.
Parts and spares should also be included when counting inventory items, simplifying the inventory count. You can easily create, use, and attach maintenance checklists to work orders while using a calendar to track details like costs and times.
Maintenance personnel now use smartphones to perform all maintenance tasks while taking photos to document completed work or issues encountered on site. Dashboard analytics enables managers to accurately estimate maintenance costs, equipment downtime and history to increase efficiency and profitability.
How Does CMMS Manage Tasks?
Mobile accessibility is becoming more important in CMMSs than a "nice-to-have". The ability to update, exchange and receive work assignments while moving is a major productivity boost for maintenance staff. Remote workers can quickly enter data into a central maintenance database using their smartphones, saving time and effort.
Work Orders
Work orders allow you to assign tasks/jobs to the appropriate personnel and monitor their execution. You can also use it to perform internal and external inspections.
Preventive Maintenance
The wide range of features of proactive maintenance, also known as diagnostic or preventive maintenance, allow predictive maintenance strategies based on data collected in real-time by intelligent equipment. The System's preventive maintenance features also let you plan your maintenance (either short-term or long-term) and repair work.
Inventory Management for Spare Parts
Inventory management for spare parts and tools is also available. You can also order spare parts and tools from the interface.
Asset Management
The Asset Management functions in the System allow you to use equipment models that are ordered according to their function or location. The 3D models of the equipment can be used to examine the relationships and repetitive tasks between components.
Geographic Information System
You can see the location of your assets using a geographic information system. It is easier to contact the assets in case of an emergency.
Documentation
The storage of technical documents allows for centralized storage and organization of repair and operational (technical documentation). The history of the maintenance performed on each equipment unit is also stored.
The Maintenance Management Trends of 2023
Tradition dictates making annual predictions regarding trends in regular maintenance service. Our brands' blogs regularly publish these predictions; in recent years, they were so unpredictably unpredictable as to be called unprecedented; 2023 looks promising with organizations adopting and implementing more innovative technologies, like software for data gathering or augmented reality applications, showing more positive trends ranging from how businesses get spare parts from suppliers to setting up maintenance programs.
Switch To Electric Vehicles For Fleet Managers
Do You Remember When Tesla Was the Only Company Producing Electric Vehicles (EVs)? Did Elon Musk Only Talk about Cars or Mars? Now there are multiple choices to satisfy a rapidly expanding market. More people are switching from combustion engines to batteries due to projected increases in gasoline prices that will take effect by 2025. Global sales of battery EVs, plug-in hybrid EVs and other types of electric vehicles are estimated to total $462. 8 billion by 2023.
What Does it Mean for Fleet Managers in General? It means fleet managers could fall victim to rising gas price volatility and look towards cost-efficient EV options such as those from USPS as they transition. They have even decided to convert by spending $10 Billion to make its fleet eco-friendlier.
Data is Brought to Life With Augmented Reality (AR) During Maintenance
Metaverse may have fizzled out, but that doesn't mean there is no use for technology; AR in maintenance has already seen great gains. Techs can use mobile connected devices to overlay information directly onto equipment or assets they are fixing using overlay instructions, with information floating above different parts of an asset in real-time.
Over the panel are instructions for opening it; gears have reminders to lock out and tag out before starting the machine. As we transition from paper maintenance records to digital data collection and maintenance management systems, these technologies should become increasingly used.
Onshoring and Nearshoring are the New Trends in the Supply Chain
3D printing promises to revolutionize our perception of inventory management. Once you can print spare parts as necessary, perhaps all they require will be parts for 3D printers - an exciting prospect for facility and maintenance managers who should keep an eye out for new developments within supply chains.
Supply chains may impair your ability to source and import parts. Onshoring and Nearshoring have become hot topics due to many businesses experiencing difficulties in global supply chains. Companies are shifting away from building factories abroad in favor of manufacturing closer to customers - whether within their country or neighboring nations. While moving offshore was cheaper in the past, manufacturing closer may result in greater reliability for products delivered directly.
How will local production affect maintenance? As maintenance departments expand, their maintenance requirements increase exponentially; the need for easily shared maintenance data will only increase as they grow larger.
The Latest In Sustainability Is A Trend That Has Been Around For Ages
Sustainability may be new to C-suite discussions, but environmental, social and governance procedures have long been standard operating procedures in maintenance operations. Their business goal is to get maximum value out of an asset by prolonging its life expectancy.
Predictions show that organizations will increasingly look towards installing charging stations for electric vehicles and switching to eco-friendly office cleaning products, among other strategies. With such trends on the horizon, facility managers may find making the case for enterprise asset management solutions easier.
Saving money through reduced supply usage and extended asset lifespan are great ways to lower expenses and extend business success. Switching from paper to electronic is not without its rewards - one often overlooked is saving trees.
Artificial Intelligence (AI) Can Predict The Future Of Maintenance
Modern maintenance management software makes gathering high-quality data much simpler by automating many steps of data collection. Instead of depending solely on technicians' faulty memories long after an inspection, data can now be entered directly into your System while they're still on-site.
Now employees can directly enter information onto their smartphones instead of waiting for an employee to return from work and write it down. When data gathering becomes impractical or cost-prohibitive, asset-mounted sensors provide constant streaming updates about temperature, vibrations, sound current or air quality conditions.
Data collection only resolves part of the issue; you must figure out what to do with it. Artificial intelligence can use your collected information to predict failures before they arise and offer digital solutions on what steps should be taken next.
You are more aware of issues much earlier on the pdf curve, even before flames appear or temperatures increase significantly. AI-based predictive maintenance alerts users as soon as something could go amiss - saving valuable time and resources when problems emerge.
Summary
Computerized Maintenance solutions allow businesses to oversee production equipment, tools, and other assets effectively. A software product that falls into this category must meet several criteria that must be fulfilled for inclusion:
- Manage multiple assets of different types in one location.
- Maintain an inventory of all spare parts, tools and materials required for maintenance.
- Plan your maintenance tasks, such as repairs and inspections.
- Maintain maintenance activities by managing and allocating resources (personnel, spares and equipment).
- Detailed Reports and analyses on maintenance costs, mechanic productivity, and asset utilization.
- Safety and environmental regulations must be adhered to by all assets.
- Field service technicians can use mobile apps or interfaces that are mobile-friendly.
Computerized maintenance management systems (CMMSs) help plan, control, and monitor maintenance costs associated with assets at a lower cost; it aims to extend asset lives at minimal unnecessary costs while keeping assets in excellent condition across various sites or ensuring availability and technical quality across a fleet of equipment such as vehicles or machinery.