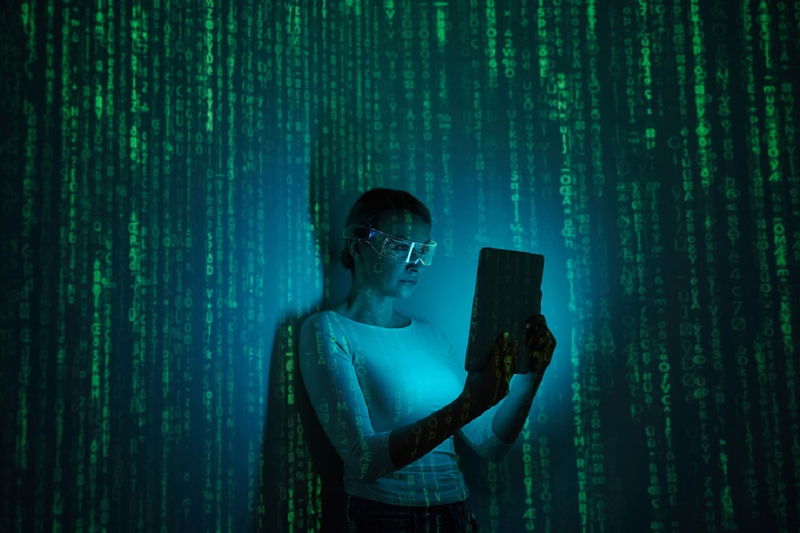
Maintenance management involves maintaining assets and managing costs and time to ensure maximum manufacturing process productivity.
What Is Maintenance Management?
Maintenance management can be defined as the maintenance of a business's resources and assets while controlling costs and time, thus ensuring the maximum efficiency of manufacturing. The old, manual, archaic maintenance process has been replaced by a computerized system that tracks, measures, and optimizes the entire maintenance program.
It's not just software -- maintenance management involves a mix of best practices, software and well-trained personnel working towards the same objective. The maintenance management program is highly customizable and based on the types of maintenance performed at an industrial plant. Tailoring your maintenance management program based on your reactive maintenance type and role is crucial.
There are many solutions to improving maintenance management. You may need some additional charge or assistance in shifting the maintenance management practices of your company. Bringing in reliability and maintenance specialists like IDCON can be a great way to identify opportunities and develop attainable plans for improvement.
Why Maintenance Management Is Important
Maintaining assets and equipment in optimal condition is essential to the success of any maintenance program. Well-maintained assets and resources help to maintain your production and reduce the risk of unplanned downtime. Snowballing costs can result from unplanned downtime, including repairs, overtime labour and spare parts. Delays in shipments can lead to lost revenue, or machines may completely break down.
Maintenance management improves the efficiency of manufacturing facilities. It increases revenue through lower operating costs, improved quality (and quantity), and reduced human error. Other benefits, besides cost reduction, include increased workplace safety, improved productivity, and reduced human error.
Maintenance Management: What Are The Objectives?
The ultimate aim of all maintenance is to inspect, analyze and interpret The production process. Analyzing reports generated by a CMMS allows you to control costs and schedule work efficiently. It also ensures that failures and breakdowns remain at a minimum. Maintenance management has three main goals:
- Budgeting/Cost Control: Maintenance Management Tools give managers the information they need to allocate budget funds for proper maintenance. Control costs are crucial because the business uses certain expenses better than others. A maintenance manager may need to purchase a new part for a particular asset. She may have to decide between an inexpensive, less durable, or more costly part with a longer lifespan.
- Allocating and Scheduling Resources: Planning work and allocating labor and time resources to maximize productivity is crucial to efficiency. The manager can use maintenance management to completely decipher the process and determine what activities are most important. Suppose the manager of maintenance needs to confirm the accurate delivery of a certain product, To ensure that the merchandise can be delivered without delay from the warehouse to the delivery vehicle. In that case, she can give the forklift priority.
- Regulations and Compliance: Maintenance Management Tools help organizations to comply with local, state and Federal regulations. It may appear cheaper only to assign one employee to an asset, even though the law requires two for safety.
- Reduce Downtime/Loss. Establishing an organized maintenance program, a good maintenance plan can help mitigate productivity loss due to equipment failure. More production stops mean more revenue lost.
- Increase Asset Lifespan: Organizations make large investments in machines. Maintenance management programs help ensure that equipment and infrastructure are always in a good state. Regular maintenance can extend the life expectancy of equipment and facilities by minimizing wear.
- Improve Equipment: Building on the goal of increasing the lifespan of assets, Maintenance Management also improves equipment by modifying, extending or adding new, low-cost products.
- Training: Maintenance Management Programs should incorporate training staff in maintenance-specific skills, enhancing operational safety, providing advice on acquiring, installing, and operating machines, and enhancing quality.
- Discover Maintenance Trends: Analyzing historical data gives managers a better understanding of day-to-day activities. Software like CMMS can help uncover why an asset is consistently performing poorly.
Asset Management And Maintenance Management
Working with assets and ensuring their reliability is a major component of maintenance. The two are distinct in some ways:
- Asset management: Refers to an organization's activities and practices to track and manage its assets. This information is then utilized for production improvement. To ensure success, asset management systems must align with the business strategy. Businesses can use asset reliability management to see if their equipment performs as expected, if preventative maintenance costs are reduced, and if a better return on investment is achieved.
- Management of Maintenance: We've described the term as using the intuitive software, such as CMMS, as tracking a company's resources, like its labour force, equipment, and materials. This system provides the information needed to make an informed decision about improving or creating maintenance activities. Maintaining your equipment in excellent working condition will minimize downtimes and unplanned repairs.
What's the Difference? Asset management and maintenance are both different in terms of their technical aspects. Still, they often work together to complement one another. Asset management is more concerned with the key performance indicators of the equipment and its maintenance. At the same time, Maintenance Management focuses on the actual physical condition of the physical asset and the critical assets' reliability. Contemporary CMMSs merge both processes so that maintenance staff can view the statistics from each in one central location of the database in customer relationship management.
Computerized Maintenance Management Systems
A computerized maintenance system (CMMS) is a software platform that simplifies predictive maintenance management is a computerized maintenance system (CMMS) used by maintenance personnel. The software can be used to create detailed reports, status updates and summaries about maintenance.
Once this data has been analyzed, it will assist maintenance workers in doing their duties more effectively and help maintenance management make defensible judgements. Organizations can organize all parts of their business in a single central digital place using CMMS software, which eliminates the need for human data entry. Because CMMS can be widely customized, businesses can add elements like equipment data management and preventive maintenance job management.
The two primary types of CMMS are on-premises (traditional) and cloud-based (modern). On-premise software must be installed on the server owned and managed by the buyer. In contrast, an external server (often the software vendor) hosts cloud-based software. On-premise servers have various disadvantages, such as greater prices and difficult implementation. They also need regular backups (updating hardware and software) and maintenance:
- Management of work orders A CMMS with work order management features simplifies the maintenance work order process. Maintenance managers can create, prioritize, review, track, and assign work orders from their mobile or desktop devices while operators submit requests.
- Use of time, usage or condition triggers can alert software automatically when scheduled tasks must be completed. It allows automatic scheduling and alerts inventory so that parts are always in stock.
- The software allows technicians and managers to interact with each other and view real-time updates. The software allows technicians to view their tasks and mark them as completed. They can also switch an asset's status from offline (offline) to online. Managers can also see completed jobs.
- Asset performance/reporting An enterprise asset management CMMS allows the company to easily collect and analyze information from all assets so that maintenance managers can identify areas where efficiency and productivity can be improved. Tracking the performance of assets is a major part of maintaining them. It's important to look at the operational hours of your assets, as well as time-based gauge measurements, mileage, and other factors.
- A CMMS creates asset profiles automatically using this data. These asset profiles include asset-specific information such as maintenance checklists and failure codes. They also contain safety and single-point lesson information. These profiles allow you to get an overview of your maintenance operations by creating customized reports that include asset downtime and the impact each asset has on inventory costs.
- Inventory Management keeping track of all the spare parts can be difficult. A CMMS can help you stay organized and get the right parts at the right time by automating your inventory purchases.
- CMMS software allows you to log spare parts, including where they're stored, the date they were bought, their use and availability across all locations. The technicians will know which parts they need to perform a preventive maintenance or repair task. They'll also be able to locate them and use them.
- A CMMS can help you keep an optimized inventory by tracking costs and referring to order histories, cycle counts, usage information, first-in/first-out details, etc.
- 4 Audit capability The audit preparation can be made easier by having an ongoing, searchable log of all tasks. The maintenance team can then audit the asset's history of maintenance. Some CMMS systems allow you to create profiles for users that monitor the certifications, renewal dates, and embedded standardized videos. This is useful for people who need to stay up-to-date and compliant. You can archive all work orders, task lists, and photos, providing you with any evidence you need for ISO certification.
- Mobile features virtually every modern cloud-based solution in CMMS with facility management software with real-time visibility and equipment details for customer satisfaction has a remote access feature that allows users to use their smartphone or tablet. It is important to have this feature, as maintenance technicians spend the majority of their workdays in the field or on the factory floor. Maintenance technicians can record their work as they go. It's possible to take pictures or management requests help on-site with required human resources. These updates can be made without a WiFI connection using a CMMS with an offline mobile app.
- Integration abilities of modern CMMS software can be integrated with other company systems. Integrating your sales software into your CMMS, for example, gives your sales team access to data they wouldn't normally have. Good CMMS providers offer a range of integrations, allowing you to create the perfect combination.
Who Should Have Access To Your CMMS System?
In some organizations, there is a debate about who has access to the CMMS. This can lead to several problems over time. As fewer users use the system, more work falls on those who do. This small group is responsible for everything, from entering work orders to running and analyzing reports.
It also limits everyone's impact. The team members that can't get a clear picture of the maintenance operation are more likely to make mistakes, be less productive, take more time off, and have lowered morale.
Similarly, allowing different team members or departments to access your CMMS is beneficial because maintenance management is shared across the organization. The maintenance team can then focus on improving other aspects of the business. This allows other departments to make data-driven business decisions using analysis of all parts of the organization.
Look below at the different groups who should be able to access your CMMS:
- Maintenance Manager: The maintenance manager is also the system administrator. The system administrator oversees the CMMS daily and is heavily involved with choosing, implementing and optimizing the CMMS. The maintenance manager is responsible for almost all maintenance aspects, including creating work orders, prioritizing them, managing assets, and creating reports.
- Facility/Operations Manager: By giving access to facility managers, they can see information about maintenance, schedules and metrics, as well as the overall performance of multiple locations. These data will help improve their efficiency, make budget decisions, plan for audits, and buy inventory.
- Engineers of Reliability: The engineers take the information from CMMS and convert it to actionable data. By giving them all of the data from a CMMS, they can create more accurate reports and make process improvements.
- Inventory Managers: As mentioned, CMMS plays a major role in inventory management. Inventory managers can use a CMMS's information to track and log information about spare parts, review historical data, establish minimum quantities, and send purchase orders. This benefits the entire maintenance department since improved inventory management and purchase help ensure that the parts are always available at the correct location. This also helps to keep records better and monitor spending.
- Safety Personnel: By having all the safety and health data in one place, an organization can stay compliant. All employees can access certifications, policies and checklists.
- Technicians: This is a no-brainer. Technicians should be added to the CMMS as users who use its features most. You don't have to grant all technicians access to the administrative side. Still, they need to be able to see and receive work orders and notifications. They should also be able to add data to asset profiles and do other tasks directly related to inspections and repairs. This information allows them to work more efficiently and accurately while also allowing them to record data in real time.
- Production Personnel: The group comprises machine operators, supervisors on the line and others involved in daily operations. Often the production staff is the first to detect impending problems, and having access to CMS allows them to add more details to the work order, thereby improving the efficiency of the repair process. The CMMS allows maintenance managers to assign basic and autonomous maintenance tasks, such as cleaning equipment.
- Contractors and Technicians: Not directly associated with your business but who perform routine maintenance tasks should be granted guest access to the CMMS. They can then see the work orders, task lists, and resources available. The mobile app will allow them to communicate better with the maintenance manager.
- Senior Leadership: Senior management and the executive team use data to drive decisions. CMMS access is a great way to stay updated on performance, KPIs, and other important information.
You Can Now Adopt The Latest Trends In Maintenance Management
-
Cloud-Based Applications That Are Accessible On The Move
This is because it's not the newest trend in maintenance management, but it's one of the most popular, which is why this trend is on the list. Why is this maintenance management trend so common among maintenance managers?
On the other hand, maintenance managers have many things to do daily. They have to, for example, assign work orders to technicians, monitor them, and travel around the facility. Because they are usually on the job and not at a desk, they need a portable system to make their jobs easier. Arion ERP-CMMS is a solution that fits the bill.
Smartphone, tablet, and PC maintenance teams can access Arion ERP's CMMS solution. Arion ERP's CMMS software solution is accessible to maintenance teams via smartphones, tablets, and PCs. Arion ERP is a great option because it can be customized to fit the company's needs. Arion ERP is, therefore, one of the most flexible solutions on the market.
-
Augmented Reality
It's hardly unexpected that augmented reality (AR) is one of the newest maintenance trends. Technology like augmented reality has countless applications. It is employed throughout various sectors, including construction and manufacturing. While seated in front of a machine, a user can view operation instructions. Equipment maintenance specialists can also employ computerized checklists.
A second advantage is an ability to upload a current asset condition that management can view without visiting the site. The maintenance managers can use augmented reality for their team training. Providing training sessions without waiting for the machine to idle is advantageous. This saves valuable time. It may be some time until augmented reality becomes mainstream. This is especially true for the maintenance industry, as it's a relatively new technology.
-
Data Collection Accuracy For Optimal Analysis
Information is key today, and the right information, combined with a thorough analysis, can improve any maintenance management system. Maintenance managers know that more precise information will lead to more accurate projections and better equipment maintenance decisions.
One of the latest trends in maintenance management involves maintenance managers including more information on assets, such as their current status, EOL date, needed replacement parts, assigned technicians, etc. This information helps paint a picture of the effectiveness of maintenance and what changes may need to be made in the future.
-
Inventory Management Is A Better Way To Manage Your Inventory
Maintenance managers need to ensure spare parts are always available to avoid unexpected downtimes and disruptions in production. To improve inventory management, one of the latest advances in maintenance is to increase it.
Modern CMMS technology has made inventory and spare part management more efficient. Maintenance managers and technicians can use a robust CMMS solution such as Arion ERP CMMS to determine which spare parts will be required for which machines, the expected time frame when a machine component needs to change, etc. Data-driven inventory management reduces waste, increases costs and expedites the transportation of products.
-
Internet Access Is Available Throughout The Entire Facility
5G coverage, although now widespread, could be improved. The majority of countries still need to get 5G. Maintenance management, like most operations, requires the use of the Internet. On the contrary, many organizations place a high priority on ensuring that their internet connections are consistent throughout all of their buildings. With a reliable and fast connection, the maintenance team can perform these tasks:
- Work orders can be completed on the move.
- Install maintenance management software on all sites.
- They are not confined to their desks regarding new orders, updates or work.
- Update, download and access information more quickly.
- Reduction in response time.
Maintenance Management Is Constantly Evolving
These are the latest trends in maintenance management, but they're always changing. These trends are also based on expensive and new technology (5G and AR) and will be mainstream for a while. More firms are implementing maintenance management software, however. They understand how they can help improve maintenance management and the return on investment they provide.
Conclusion
The maintenance management process is maintaining the business's assets and resources. The main goal of the software is to protect and streamline business processes. There are many examples of both maintenance management performed correctly and incorrectly.
Maintenance management comes in many forms. The initial cost and time it takes to implement maintenance management solutions are worth your investment if you want your business to reach its maximum potential. The leading software company offers the most efficient and effective maintenance management solution for the smooth functioning of businesses.