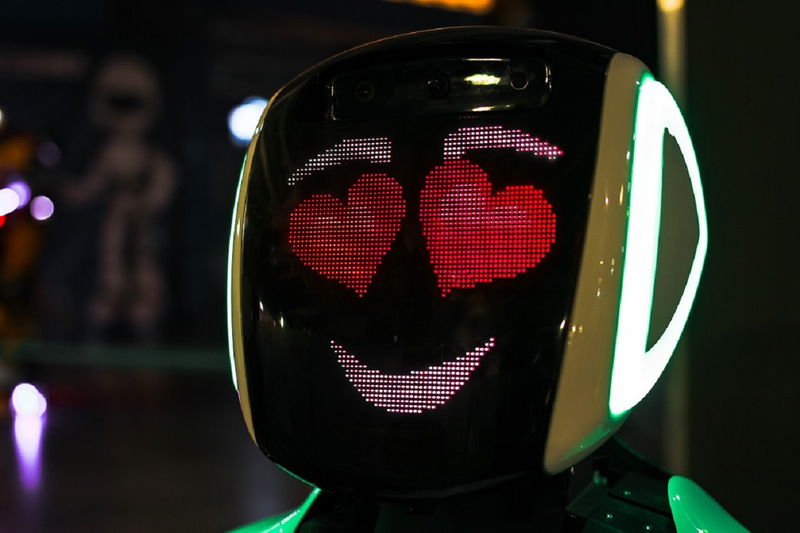
Overview of Warehouse Management System
A Warehouse Management System (WMS) is software businesses use to help manage daily warehouse operations. This involves overseeing what products enter or leave warehouses or fulfillment centers and their removal - providing real-time insight into supply chains through real-time inventory visibility within both physical and transit locations. WMSare not limited to inventory control but include tools for picking, packing, resource utilization analytics, and many more processes that improve operations and efficiency in any organization.
Warehouse management systems (WMSs) provide companies with an effective method for controlling daily warehouse operations from when goods first enter a distribution or fulfillment center to when they leave again.
Wholesalers, 3PL providers, and shippers face increased pressure from Amazon's fast omnichannel order fulfillment capabilities to fulfill and ship them as fast as possible via all channels available - or face consequences! E-commerce sales also saw significant growth last year, with Statista reporting U.S retail online sales reaching US$343.15 Billion during 2019. By 2024, online sales are projected to surpass $476.50 billion as online sales increase and demand for quick shipping grows simultaneously with shrinking labor pools. Before COVID-19 began, it was challenging to hire warehouse staff; temporarily, more were available until mid-March 2020, but after that, finding staff will become difficult again - all factors that necessitate more effective, faster, and more efficient warehouse management procedures and logistic processes.
Sound WMSsystems can streamline warehouse management from receiving, putting away, picking, packing and shipping processes through inventory tracking and replenishment to stock control and organization - all from one central interface. WMSalso integrates seamlessly with tools like barcode scanning, RFID technology wearable devices, or even Augmented Reality (AR).
Five Benefits Of An Inventory Management System
Any business units with inventory on hand should invest in effective digital warehouse management software to reduce costs while increasing efficiencies. Some of the key WMSbenefits for your company may include:
- Increased Efficiency In Operations: Warehouse management systems streamline and automate warehouse processes from receipt at the door through delivery outbound for increased efficiency and smoother operations, from receiving goods at reception through packing/shipping packages outbound, assuring higher efficiencies with smaller amounts. They can handle larger volumes while eliminating redundant work. WMSs share data with ERPs/TMSs for an all-encompassing view that expedites goods movement more effectively.
- Reducing Waste And Cost: WMS software will identify items that need to be picked up immediately or need an extra push to reduce waste while helping determine how best to utilize warehouse space from inventory placement down to optimal routes and routing simulations. Simulations also enable floor planners and designers to design floor plans or place equipment, pallets, or shelves at their ideal spots on optimal floor layouts for efficient operations.
- Inventory Visibility In Real Time: Warehouse management systems give you real-time information about how your stock enters and moves through your warehouse, giving you real-time visibility of it entering and leaving. With such information, demand forecasting becomes much more straightforward as just-in-time strategies become available, and traceability increases significantly when something needs recalling.
- WMSs Offer Improved Labor Management: WMSs can help forecast labor needs, optimize travel times within warehouses, and assign employees tasks based on skill, location, and other considerations. A sound WMSsystem can create an atmosphere that encourages employee morale by creating an atmosphere that is safe, relaxing, and orderly, making workers feel valued knowing their time has been used efficiently.
- Customer And Supplier Relationship Improvement: WMSwill increase customer satisfaction while reduced wait times at docks and loading bays will boost supplier relations, ultimately strengthening ties.
What Can A WMS System Do?
A warehouse management system (WMS) can optimize any activity inside or outside a storage facility and its extended supply chains - including receiving, storing, picking, packaging, and shipping activities. Warehouse management systems support each exercise listed below in various ways.
Receive And Store Process
WMSs enable companies to receive, process, and store items more efficiently by following warehouse flows and ecommerce business rules. Before WMS software was available to companies in 2018, things were handled manually to reconcile with purchase orders or physical receipts using a pen. Some smaller warehouses continue using this method today. In a Peerless research survey conducted in 2018, 87% of participants admitted to handling materials manually when receiving them.
WMSalso integrates with other billing software for easy validation and reconciliation with digital purchase orders by scanning barcodes; labels may be printed for more accessible storage and retrieval.
Inventory Management
Using barcodes and RFID, warehouse management software offers real-time visibility over inventory in all locations - even transit or retail settings. Some systems also support Demand Forecasting and cycle counting with advanced analytics insights for cycle counting purposes, allowing businesses to adjust inventory accordingly to customer demands in stores or online.
Inventory tracking can be essential in improving order rates, as it ensures orders arrive on time, undamaged, with correct invoices attached. With inventory tracking tools, orders arrive timely and in excellent condition with accurate invoices attached. Furthermore, inventory allocation tools enable warehouse personnel to allocate stock more effectively using custom workflows or picking logic to move inventory faster into or out of warehouse storage facilities.
Picking, Packing And Fulfilling.
According to a Logistics Magazine survey, warehouses are preferred for packing and fulfillment activities. According to ResearchGate estimates, order picking accounts for about 55% of overall warehouse costs.
WMSs provide guidance and technology solutions that optimize product retrieval, storage, and packaging operations - including radio frequency with or without scanning; pick-to-light technology (with voice pick up); pick-to-voice technology; robots; and algorithms. These costs can be cut significantly using WMS.
Some warehouse management systems make fulfilling orders simple by employing techniques like single order picking (SOP), batch picking (Batch Picking), zone picking, cross-docking, and wave picking - as well as "put to order" systems to streamline this process.
Shipment
Many warehouse software systems integrate Transportation Management and Logistics Software, which enables them to automate many aspects of the fulfillment process. For instance, they can automatically generate bills of lading, packing lists, and invoices as shipments come through or send automated shipment notifications.
Companies can now track packages live to ensure they arrive on schedule at their destinations.
Ensuring this process runs smoothly pays dividends; best-of-breed warehouse operations ensure that most shipments leave on schedule and make their way through transit systems.
Labour management
Labor management for warehouses can improve efficiency by offering insight into labor costs. A warehouse management system (WMS) gives real-time visibility of workers and the fees they accrue and insights into response times, productivity gaps, and trends that allow warehouse operators to run more effectively and efficiently.
In addition to providing critical insights, many systems permit task interleaving based on factors like priority or proximity - helping reduce travel times and "deadheading," equating to lost productivity for workers. Such methods may help plan and schedule directly or by interconnecting with other systems.
Management Of Docks And Yards.
Truck drivers can quickly locate loading docks using dock and yard management features. Cross-docking software makes the task even simpler when grocery items arrive directly into the warehouse and need to be immediately packaged into orders; by matching scans of products received to those already ordered, it notifies recipients if any need to go directly into the cross-docking area.
Analytic And Warehouse Metrics.
WMSs allow businesses to automatically collect real-time data rather than manually input, thus eliminating errors during data collection and speeding up processes. By combining real-time and historical data with analytics capabilities, a WMScan monitor metrics such as order fill rates, accuracy of inventory levels and distribution costs, and order cycle times and create visual reports easily shared among stakeholders.
Warehouse Management Systems In Action
Warehouse management tools and systems are widely employed by distributors, third-party logistics providers and e-commerce fulfillment centers, cold storage providers, pharmaceutical healthcare companies, and others who utilize WMSsolutions to increase transparency and efficiency and reduce costs. WMSsolutions can be integrated with transport or logistic systems to increase transparency, efficiencies, and savings for their facilities.
These companies have implemented advanced technologies and management systems within their warehouses to maximize efficiency.
Digital warehouse tracking system helps them stay ahead of their core business processes. Now, they have fast ways of improving quickly while understanding exactly how their warehouse performs.
Different Types Of Warehouse Management Systems
Warehouse management systems come in three primary varieties, which may or may not include legacy homegrown systems, cloud-based, and integrated ERP and Supply Chain Management platforms. Which solution best meets each business will vary accordingly.
-
Standalone WMSs (WMSs):
These systems can be installed directly at a company using its hardware, providing more customization while being more expensive than their standalone counterparts. Regarding data and software control, standalone WMSs offer greater access to more specific solutions, allowing greater control. While initial costs for purchasing them might be higher, once an organization owns it, they take full responsibility for updates, maintenance, prices, and updating when new platforms emerge that make usage difficult or incorporation more challenging than with stand-in systems like these WMSs.
-
WMS in the Cloud:
WMS cloud systems can be cost-effectively implemented rapidly and delivered as software-as-a-service (SaaS). SaaS providers often invest significant effort and capital in disaster recovery and security features of these cloud warehouse management solutions, making for easier scaling when companies expand. Warehouse management on the cloud also enables faster innovation through regular updates since someone else is responsible for keeping everything current - including average disaster recovery measures from SaaS providers - making integration easy between different systems.
WMS Integration With ERP And SCM:
Some Warehouse Management Systems (WMSs) are developed as applications or modules that seamlessly connect to supply chain platforms like ERP. Such WMSs offer more excellent compatibility with solutions overlapping in areas like business intelligence and accounting; such solutions also enable an end-to-end view of logistics chains with coordinated warehousing processes and execution, which ultimately helps optimize operations while creating swift fulfillment experiences.
Also Read: Tracking The Future And Scope Of Warehouse Tracking Systems
Smart Warehouse Technology
Innovative warehouse technology can meet customers' ever-evolving needs by accommodating their changing habits, channels, and expectations, keeping up with emerging markets, disruptions, and technologies (like artificial intelligence, machine learning or autonomous robots ). It may include artificial intelligence, machine learning, or autonomous robots.
Storage Automation
Automated technologies have had a dramatic effect on distribution centers and warehouses. Automation technologies streamline processes related to data collection, barcoding, and scanning while streamlining picking, packing, and shipping operations for maximum efficiency - as well as eliminating human error when entering addresses incorrectly or wrong SKU numbers into inventory system software.
The Technology Of Voice-Picking
Voice picking (also referred to as voice-directed warehouse and pick-by-voice) allows an operator to complete tasks without using paper, eyes, or hands - provided by their WMS, which communicates spoken directions about when and where incoming orders should be collected; workers are then able to share real-time updates using natural language updates when their batch has been finished completing orders quickly and efficiently.
Mobile Devices
Warehouse staff rely heavily on mobile devices to perform their duties more effectively, according to the 2020 Warehouse DC Equipment Survey results, which showed 73% were using smartphones and tablets as part of their work, 55% used barcode scanners, 18% utilized GPS services (with 28 % planning on adding GPS in 12 months), therefore making a WMS capable of accommodating cutting edge technologies essential.
Warehouse management using AI and the Internet of Things (IoT).
Artificial Intelligence and IoT technologies are becoming an ever-increasing part of warehouse operations, offering businesses more excellent responsiveness to changing warehouse conditions without adhering to rigidly predefined rules. IoT sensors collect data while AI analyzes it to predict outcomes - all used together to shift companies to an on-demand model warehouse model.
WMSs collect IoT data from numerous sources, such as material handling devices such as conveyors and smartphones, passive radio beacons (such as passive RFID tags and passive Bluetooth beacons), handhelds with radio beacons that transmit passively radio beacons) handheld radio beacons transmit passively radio beacons, passive radio beacons, RFIDs, etc. Artificial Intelligence systems then utilize this data to provide valuable insights such as trend analysis predictive models algorithms, which enable businesses to make better business decisions based on current conditions - these may assist with routing, labor movements, dynamic slot inventory requirements, etc.
Storage Robots
Warehouse robots use AI and machine-learning techniques to make decisions based on their environment, measuring temperature using video, audio, thermal, and haptic sensors combined. WMS software may then direct their actions accordingly if integration has been enabled.
Robots have increasingly become a mainstay in warehouses and distribution centers to automate some tasks or enhance others.
AGVs use magnetic stripes or tracks to move inventory around in warehouses. Autonomous mobile robots rely on sensors, computers, and maps onboard for navigation; when necessary, they change routes. Autonomous Mobile Robots have sensors installed that help them navigate routes relatively easily. At the same time, autonomous Mobile Robots utilize deep learning technologies in tandem with visual sensors mounted onto packages to identify package information that aids in inventory control or sorting. In contrast, drones with optical sensors use deep learning technologies for fast scanning/counting in high or dangerous locations. Finally, Automated Storage/Retrieval Systems are used by software directing their operation, whether in cranes/shuttles/climbers, etc.
Robots can significantly boost warehouse operations' speed and efficiency while improving workers' safety and morale as more strategic ones take over mundane and hazardous jobs.Apps that combine virtual and augmented realitiesAugmented Reality Technology uses a camera that captures real-world environments such as an aisle in a warehouse and then overlays information with instructions using mobile devices, like AR smart glasses for operators to perform tasks hands-free using apps that display bin locations or map routes - or make delivery routes safer through VR technologies such as this.
Your business process could only suffer with a WMS tailored to its individual needs and explicitly customized to its supply chain and operations processes. Ineffective processes could hinder supply chains and operations immediately and in the future, further jeopardizing both current and future success.Optimize supply chains to exceed customer expectations regarding delivery, quality, and consistency. A warehouse intelligence dashboard will assist in monitoring business requirements health while making critical decisions that help keep it moving in the right direction.Warehouse management systems (WMSs) can help your supply chain and warehouse to overcome numerous issues: productivity, accuracy, and visibility are just three.
How Can We Address These Concerns
Supply Chain Junction can assist your supply chain in managing more efficiently by helping identify issues that impede efficiency in its operation, offering practical solutions, and making its processes more streamlined. Monitor the performance of your warehouse so you can compare data over time and lower costs while increasing staff morale and customer satisfaction - it always pays to simplify things.
First, we will explore how your warehouse can become your company's transformation center.WMSs have several impacts on warehouse operations; Real-time access to quality data gives your supply chain greater transparency.Sales and management teams can easily monitor orders and stay informed on the status of goods in real time - providing an order management system that is mobile and efficient at problem-solving.Visibility allows quick, corrective, and preventive decisions to be taken quickly to optimize business functionality and warehouse efficiency.
WMS helps reduce warehouse labor costs due to efficient labor allocation. Managers can access comprehensive reports detailing all activities within the warehouse, with KPIs and accurate data providing insight into when, where, and how long labor demand might arise; employee management becomes easier while downtime decreases significantly.Labor costs will decrease dramatically as employees are tracked and targeted to maximize their working hours, leading to better employee and business satisfaction.
Warehouse Management Systems streamline processes:
A WMS allows for accurate inventory record-keeping and quick finding of items for shipping or assembly; its efficiency increases from receiving items inward through shipping out. It ensures smooth operations from the inbound process through outbound.Warehouse managers can manage expectations by tracking goods' locations and responding to any delays in arrival time.Reduce energy and use fewer resources to increase performance.
WMS Optimizes Warehouse Layout: A WMS can assist your picking process by optimizing its layout.Search less and spend more time packing, shipping, and fulfilling your dreams!WMS enhances inventory accuracy and pick times with decreased time between picks. Inventory management software can be enhanced through streamlining operations such as staff management, space allocation, inventory control, and pick accuracy monitoring to produce a faster turnaround for any department.Faster order fulfillment times allow more orders to be filled simultaneously, increasing profits and new clients.
Automating and streamlining processes to increase flexibility and responsiveness: It can decrease human errors while decreasing administration times; this allows a quicker, more effective response to sudden changes, errors, or upheavals in process flow. Introducing Warehouse Management Systems into this workflow may increase flexibility and responsiveness by automating them more thoroughly than manual methods would do alone.By effectively managing time, businesses can save on labor hours, administrative costs, and costs associated with rushing orders to delivery.
Safety and Security in Warehouses: The less precise your inventory, the easier it will be for thieves and intruders to attack your warehouse.Knowledge is power in combatting theft in a warehouse, and tracking stock accurately can reduce theft significantly. Manual keeping track of it all may result in mistakes when conducting frequent stocktakes.
Cut back on shrinkage and theft: Keep inventory within your warehouse or with customers to prevent it from being stolen or misappropriated.
Logistics plays an integral part: It is used in deciding the success or failure of battles, campaigns, and wars - Dwight D. Eisenhower Each impact contributes towards creating an optimized warehouse that runs more smoothly while producing higher quality goods at consistent KPI targets.Your warehouse operating at peak performance will profoundly affect sales, financial planning accuracy, and the level of customer service provided to clients.
What Are The Secondary Impacts of WMS Implementation on Supply Chain Operations?
Data collected over previous periods can help business management make informed decisions that drive growth. Your business can forecast demand and hire enough laborers in preparation for its predicted period; additionally, ensure clients, suppliers, and support staff understand effective strategies to handle busy periods.
Avoid making poor decisions due to inaccurate data and save on administration expenses.
Better Supplier Relationships Avoiding last-minute panic that plagues production and manufacturing businesses will help build lasting supplier relationships that offer accurate requests with on-time delivery.Pleased customers will bring you more revenue.
Increased Customer Service Levels
When your suppliers deliver on time, more time can be allocated towards customer service - leading to faster deliveries and reduced complaints from your clients.
Substitutable parts and logistics costs could be decreased with reduced errors.
Implement an Ongoing Optimization Strategy
Every second counts when running a warehouse:
- Reviewing processes.
- Changing ways of working.
- Training employees.
- Making sure a high-quality product reaches clients.
A WMS will reduce the time spent managing inventory system software, personnel, and storage space so your energy can go toward building teams, training employees, and optimizing processes.
More time means more earnings potential.
Critical Impact of Waste Management Software on Spending
WMS implementation aims at "REDUCING OVERHEADS." To justify your investment and explain return-on-investment calculations accurately.
These effects will lower costs across your operations, including staff complement, storage, and inventory costs, supplier relationships, customer service performance, or inadequate supply chains.
Below are a few benefits and cost savings associated with installing a WMS:
- Labour Utilisation 10-55%
- Stock Reduction 5- 40%
- Utilization Rate for Warehouses 10- 40%
- Picker Productivity (10-50%)
- Reduce shrinkage 50-99%
- You can now increase the shipping accuracy to 95% or greater.
- We have significantly raised supplier compliance to more than 97%.
- Inventory Increase by 10--50%
- Customer service 10-50%
Conclusion:
Logistics is no exception - digital technology has permeated every industry, and the warehouse management system plays an integral part in expanding supply chain businesses quickly.
WMSs have many benefits that will elevate your business, from inventory control processes to accounting processes and beyond. When selecting one for yourself or a colleague's use, be aware of all factors discussed, but remember, regardless of how accurate a WMS may be, it will only make money if it makes some.