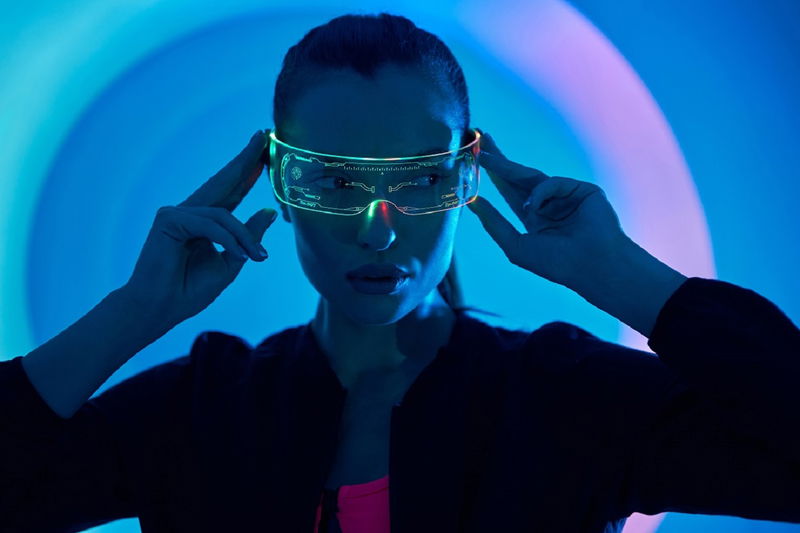
Manage the journey of your products for retail and e-commerce success. Customers expect their purchases to be delivered promptly according to their specifications, without delay or alteration. How can you ensure the inventory on your shelves aligns with your current list? How can you guarantee that refrigerated products are packed and sent off before their delivery driver arrives to reduce spoilage?
This comprehensive guide on warehouse management will address these and many more of your questions about managing a warehouse. Discover new terms in warehouse terms, or gain more knowledge with these top tips and strategies from companies of any size! We recommend software providers and services providers alike as recommended software/service provider options in this guide.
Warehouse Management : Introduction
Warehouse management encompasses receiving, stocking and protecting inventories before being transported to their final destinations. Businesses dealing with physical products should understand this aspect of supply-chain management well; warehouses serve as gateways from which orders arrive on customers' doorsteps quickly or slowly, depending on warehouse operations and delivery teams' efficiency. Warehouse management refers to a group responsible for running an area storage facility as part of supply chain management processes.
Warehouse Management is Crucial to Your Business
Warehouse management will increase how products get to customers (and maintain customer retention). Online shopping continues to expand; recently Arion ERP released statistics collected from users within retail and restaurant industries that enabled us to understand current consumer trends better and anticipate those to come in future years.
As companies encounter economic obstacles due to reduced product and service demand, optimizing routes to maximize delivery workers' efficiency while recovering margins is important. Maintaining high delivery volumes per driver while cutting mileage costs should help companies remain financially resilient in an unpredictable economy.
eMarketer predicts that direct-to-consumer ecommerce sales are estimated to hit nearly 18 billion this year - an increase of 24% year over year! To take full advantage of this opportunity, effective warehouse management systems must be installed.
As Amazon remains one of the market leaders for ecommerce sales, to compete against it effectively, it's crucial that both your warehouse team and last-mile delivery team work in tandem. Your warehouses can assist your delivery teams by helping efficiently dispatch orders while improving customer service and satisfaction ratings.
Why Last Mile Delivery is Important
Combining warehouse management and superior last-mile deliveries is key to shortening turnaround times, improving product deliveries, and offering outstanding customer service. The last mile is at the core of logistics forward processes - what customers see most directly.
Your customer experience could be negatively impacted if your distribution center or warehouse operates efficiently but does not deliver goods on time. At the same time, even if deliveries can occur on schedule.
However, there is too much stock in storage. In that case, their experience may still be diminished by delays caused by crowded warehouse space. Your business depends on optimized warehouse management and last-mile delivery, or you risk permanently losing customers. Learning more about Arion ERP can assist businesses.
Use Arion ERP to Nail Last-Mile Delivery
No one cares more for you or your product than yourself, so doing last-mile deliveries yourself may often be the optimal strategy. At Arion ERP, we support retail and ecommerce businesses worldwide to increase revenue through key performance indicators.
Arion ERP can integrate seamlessly with third-party applications and warehouse management systems via API integration, so all members of your team remain aligned during product packaging, loading and final delivery.
Arion ERP allows fleet managers to strategically optimize delivery plans by creating optimized delivery routes. Upload orders with specific constraints before clicking "Plan Routes." Additionally, "Return To Depot" enables multiple deliveries at once or coordinates them with warehouses that use wave-picking scheduling.
Arion ERP lets you keep customers up-to-date in real-time via SMS or email notifications, greatly improving customer experiences while decreasing phone calls asking where packages are. Notifications sent can be fully tailored according to the customer's needs; each notification provides live tracking links showing when orders should arrive at their destinations.
This article presents useful strategies and advice to reduce shipping costs when choosing courier or shipping service companies. In contrast, our guide of package tracking tools from some of the world's most prominent couriers may help track down packages quickly.
Warehouse Management: 7 key Responsibilities
The warehouse management process overseas logistics supply chain operations' seven main fulfillment processes.
Receive + Inspect
Warehouse management teams conduct inspections of raw materials or goods incoming for storage before storing. Warehouse employees then examine pallets to ensure the products match what was ordered without damage occurring in transit; should any discrepancies arise, they issue new orders immediately.
Warehouses sometimes receive products of the wrong size, color or material - although an occasional mistake should not be taken too seriously. Managers should identify suppliers that consistently deliver defective goods or miss deadlines so brand leaders can address repeat incidents and determine whether a different vendor may be necessary.
Stores
Warehouse workers then transport products thoroughly inspected to a designated area within their warehouse, where they will remain safe until a customer places an order. Special attention must be given to the location and method for storing these products to ensure safekeeping; heavy products should never be placed atop lighter ones or placed into temperature-controlled environments without prior consultation; all merchandise needs to be treated carefully when handled by warehouse staff members.
Warehouse layout and space allocation have a greater bearing on processing times for orders in larger, more complicated warehouses. Store products are frequently purchased together so pickers do not need to travel long distances for them; popular items should be stored nearer the front (lower shelves are better); expiring products should also be organized by priority, with those coming due first being stored there first.
Picking
Pickers are responsible for retrieving orders from shelves when a client places an order. They then bring the order to pack. Pickers should be fast and accurate (they will pull out the correct item, size or color almost every time). Pickers can do their job better if you follow best practices in your distribution center or warehouse. The following are some of the most popular picking methods:
One-Order Picking: It is the go-to strategy in small storage or warehouse facilities with low order volumes. This involves picking items from one order at a time before taking them directly to packers for packing. Wave Picking works similarly to single order picking, with one key difference: picking occurs at set intervals at specific times and days of the week, which helps avoid congestion in warehouses and coordinate loading trucks with packing. This strategy could be employed as part of an overall logistics management strategy for loading vehicles at delivery depots.
Batch Picking: Involves gathering multiple orders (or "batching") from storage rather than individually collecting each SKU or order number. Doing so reduces time spent gathering popular products; for instance, if one group of five orders includes three bags of flour for pastry use, that could all be collected simultaneously from storage.
Cluster Picking: Works similarly to batch pick, where pickers simultaneously work on multiple orders without prioritizing similar ones over other orders; picking isn't always conducted according to SKU; items from one nearby order may be selected together to minimize travel time.
Zone Picking: Can be applied in large warehouses with clearly demarcated sections like refrigerated and non-refrigerated zones and for warehouses that feature demarcated refrigerated and non-refrigerated sections. Pickers in this method are allocated an individual zone in which they are responsible for picking, along with cluster, wave or batch-picking techniques that work alongside this system. Orders may even move from zone to zone before being delivered directly for packaging. The first stage in the logistic process is picking, and the clock starts to tick as soon as a client places an order. Delays and inefficiency directly impact delivery times from this point forward.
Packing
Packers receive items from pickers and ensure they have been picked correctly before performing one last check to ensure all products remain undamaged (and non-expired). Once packed up for shipping safely and updating warehouse inventory records, packers pack fragile or fragile goods to prevent damage during transit; in certain instances, they must also meet specific courier packaging specifications. Packer's print labels for shipment while helping couriers load vehicles.
Last-Mile Coordination
The last-mile delivery involves transporting the goods to the client from the warehouse. It can be done in two different ways:
- Warehouses have an established relationship with several couriers for long-distance and international shipping. These include USPS, UPS and FedEx. Depending on the weight and distance of the items to be shipped, freight, rail, or air transportation can be utilized. The warehouse management team ensures that orders are safely delivered to couriers and provides customers with tracking information.
- Self-delivery can be a good option for businesses with small territory or local orders. Using delivery management software like Arion ERP, you can easily guide a group of couriers in delivering an excellent customer experience. This stage in the product life cycle has many benefits, and we will explore them in more detail later in this article.
Warehouse management and last-mile delivery must work together, regardless of your selected option. Packing must be timed to line up with a courier's arrival so that delivery trucks can be loaded immediately and temperature-sensitive items aren't sitting out too long.
Auditor
Inventory control and quality assurance in warehouses are accomplished through audits to detect minor inventory discrepancies or damaged products before they escalate into major problems. Audits may take place periodically by managers depending on the complexity and size of their operating floor.
Auditors often employ digital manifests for spot checks on inventory levels so as to accurately forecast forecasted numbers; they also check expiration dates to make sure nothing needs to be removed and replaced in inventory forecasting calculations; additionally they check expiration dates to make sure nothing should be disposed of/restocked in case any unexpected issues arises with products in inventory forecasting or forecasting calculations; auditing takes place as often as necessary depending on these variables and complexity/size factors of operation/warehouse operation/size.
Audit frequency/manager depending on complexity/size/ size/complexity/complexity of operating floor/warehouse management depending on size/complexity/complexity level/size requirements/size requirements/complexity level/size requirements/location depending upon complexness/size requirements depending upon complexity/ size/ warehouse facilities require disposal/restock.
Audits of large warehouses often consist of inspecting personnel, product layout, scheduling or any aspect related to day-to-day operations - this helps identify any potential problems before customers experience service disruptions or injuries occur on the warehouse floor.
Restocking and Returns
Warehouse management is not only about restocking and returns but also about restocking. A seamless reverse logistic process (returns) is essential to a supply chain. Returns happen, no matter how well your team and product are designed. The warehouse management team is responsible for receiving returned items, restocking them and picking up new products to exchange.
Warehouse Management: The Challenges
Software or outsourcing can address all of these challenges. The following challenges can be addressed:
- Material Handling: Each member of your team must handle packages carefully. Never throw or stack goods in a way that can damage them.
- Storage: Finding enough storage space for products is daunting for many small businesses. After you have secured warehouse space, the next step is to organize products to maximize efficiency while maintaining product safety.
- Process Efficiency: Each aspect of warehouse management and last-mile deliveries must be streamlined to maximize efficiency. This is almost impossible if your company relies on manual scheduling and paper-based records.
- Experience of Customers: The success of a business is ultimately determined by the satisfaction of its clients and the ability to meet their needs. This is why a great warehouse strategy keeps the customer informed about their order status and works to deliver the product as soon as possible.
What Can Be Done To Improve Warehouse Management?
There are simple ways to deal with these problems.
Create A Fantastic Recruiting Process
Warehouse management teams should prioritize hiring top talent. Missed deadlines or failure to properly handle products could cost businesses dearly; to avoid hiring and recruiting issues, you should adopt an employer brand strategy with an effective recruiting process and offer competitive salaries; additionally, you might work with an agency dedicated to finding warehouse manager talent.
You Can Outsource Warehouse Management
Some businesses find hiring a 3PL (third-party logistics company) as the perfect solution to handling their products beneficial. No matter your business's size or inventory requirements, a third-party logistics provider (or 3PL) exists that meets them all.
No matter their speciality! Warehouse management companies specialize in keeping inventory safe while creating positive experiences for clients while being cost-effective; most 3PLs maintain direct relationships with major courier services like UPS or FedEx, who may deliver these locally as part of a delivery network or provide additional teaming options when necessary to reach clients directly if desired by business owner-suppliers for in local deliveries if desired by hiring local courier teams of couriers that manage inventory as 3PLs offer.
Software Usage
Enterprise Resource Planning Software (ERP) or Warehouse Management Software can help your daily operations and plan for future ones more easily than ever before. SaaS software offers easy access to up-to-date information that everyone in your organization is privy to.
WMS (warehouse management software) acts as the center hub of warehouse operations to reduce human errors. Warehouse managers can utilize WMS from any mobile phone, while pickers use it to quickly find SKUs they need quickly; packers use WMS for relaying order updates when an order has left, and you use combined with route optimization software like Arion ERP it creates an effective logistical success system.
Top Warehouse Management Systems
With a WMS warehouse management system tailored to meet your needs, you can streamline the fulfillment and logistic processes and keep your products in-house. You'll see a list of four software packages, their best-suited businesses, and a description of their features and functions. What's the best part? The best part?
We Are A Partner In Logistics And Beyond
Arion ERP will assist with reaching the final mile for any journey managed through warehouse management software or 3PLs, such as delivery capacity optimization software such as Arion ERP, that optimizes efficient routes to reduce operational costs, distribute drivers evenly, or combine both aspects. Input the constraints unique to their business, save them, and then utilize analytics from this application's capabilities to plan future strategies.
At our core, we aim to deliver exceptional customer service so you can provide it for your clients. Want to find out more about delivery management software or integrations? Send an email or call us anytime - feel free to get in touch if any queries arise and take advantage of a 30-day free trial too.
Benefits of WMS
Faster, More Accurate Fulfillment
Today's fast and reliable deliveries are essential if e-commerce businesses wish to compete successfully, with customers expecting performance comparable to Amazon. Deliver on this promise, and you will enjoy positive customer reviews and repeat business; fail; however, you risk negative feedback and reduced repeat business from unhappy clients.
Human error remains an issue when running any ecommerce operation - whether small or large. Mispicks, bad reviews and returns can all result from simple human mistakes; with Work Order Management Systems (WMSs), errors will be minimized to speed up fulfillment while increasing accuracy and speeding the fulfillment process.
Integrates Your Warehouse With Your Entire Online Business
To succeed in today's ecommerce market, your inventory and warehouse management must align with the sales channels you use. You can then accurately fulfill your customers' orders without worrying about mispicks, overselling or returns.
Fill More Orders Using A Smaller Staff
The size of a warehouse can grow as a company grows. This can lead to an inefficient and expensive warehouse. A warehouse management system will be valuable by helping you streamline processes and do more work with less staff.
Manage Several Warehouses At Once Or Multiple Locations
You may need to store your inventory level in multiple places as your business expands. The warehouse management system can link all these locations, providing you with a single source of information for each.
Increased Visibility
Software for warehouse management should provide the transparency and real-time visibility that everyone needs to perform their jobs accurately. Some examples are a live dashboard that everyone can view, an audit trail of all stocks or real-time inventory counts under inventory control with reliable inventory accuracy.
Features of Warehouse Management Systems
Choosing the right warehouse management solution for your company can be difficult. Here are some key features to consider when choosing a warehouse management solution.
Automatism
Automating your ecommerce site can help you save time and make it more efficient. Automating your process of fulfillment should reduce human error. Once set up, the rules determining what happens with products are predetermined. Your picking and packaging team will then only need to implement the rules.
Digital Picking
As ecommerce companies grow, they may want to switch from paper to digital picking. If you want to make your warehouse management system future-proof, it must accommodate digital picking.
Easy To Access Reports
Ecommerce has become a highly data-driven business. It is easier to make correct decisions when you have more information. All these data will be available in an easy-to-access format with good warehouse management software.
The WMS provides many ways to monitor and track different warehouse aspects, including pricing, taxation, cost management, the best-performing product sales channels, peak season sales, picker efficiency, etc.
Inventory Tracking & Control
Modern, integrated WMSs will allow you to track your inventory anytime. Live inventory tracking. It is the beginning of gaining control over your stock. This guide will teach you more about the inventory management process.
Cloud-Based
Cloud-based systems allow you to access your WMS from anywhere you want. Cloud-based WMS systems let you access it from wherever you are.
Demand Forecasting
Many leading WMSs include demand forecasting as a standard function. This is essential to avoid processing excess orders. Arion ERP has a robust reporting and forecasting tool.
Summary
Warehouse management can be an intricate undertaking with many moving pieces to keep in balance at once. Yet, its success or failure in retail may hinge upon getting this right.
All it comes down to is this:
- Arrange your inventory to create the ideal layout.
- Establish a process your staff can rely on when receiving inventory and fulfilling orders.
- Measuring efficiency allows us to identify potential problem areas.
- Assuring an appropriate electronic Warehouse Management System investment.
By taking these steps, your warehouse should run like clockwork and fulfill customer orders more rapidly and accurately than ever. Get in touch with the best and most reliable warehouse management solution.