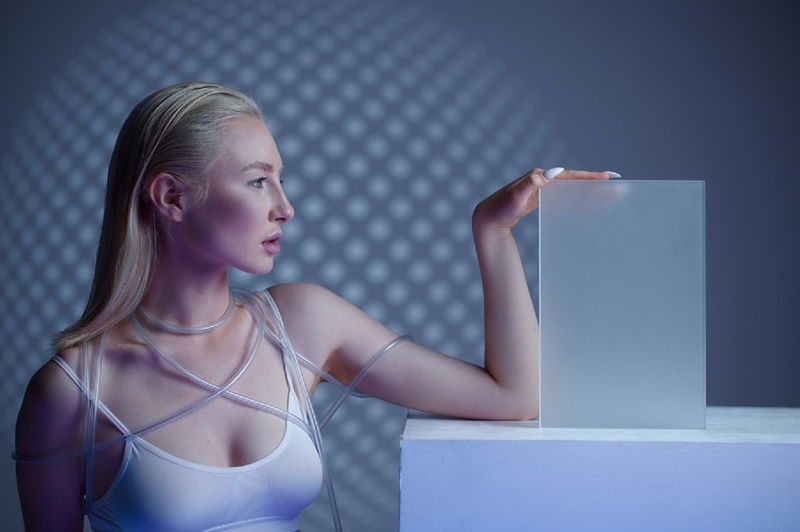
There are many options available for enterprise resource planning today. It can be challenging to choose the right package for your company. Many Industry-leading companies believe that any software will work and their businesses will conform to its functionality. However, the widely reported ERP failures show there are better options than this.
Enterprise Resource Planning is a business initiative that transforms your company and provides critical competitive advantages. This decision should not be taken lightly.
What is ERP?
Enterprise resource planning, or ERP, is a comprehensive application that addresses critical business components such as accounting, supply chain management, and procurement.
ERP systems were traditionally used by distribution and manufacturing companies. They covered so many aspects of supply chain operations. These systems were developed from different supply chain applications that address all businesses' comprehensive accounting and financial needs. They also provide industry-specific functionality.
Top Tips For Choosing An ERP System
Once you understand the differences between today's ERP systems and those of the past, it is easy to see why choosing an ERP system can be challenging. What does ERP selection look like today?
First, there are better ways to decide if you only look at a list. The decision must be approached from a strategic perspective and should consider the company's needs.
Most ERP applications are capable of handling accounting and financial functions. Some ERP applications excel in certain areas, such as specific industry-leading companies. However, you can expect the same level of accounting functionality from all ERP apps. They all need the ability to connect with other systems, scale up and grow, or adapt to organizational changes.
1. Outline Your Goals For Your ERP
Knowing where you are now and why you want a new ERP system will help you decide what you need. It is essential to clearly define why you are looking for an ERP system and what you expect to gain.
2. Set your Goals
Understand The Why Behind Your Decision to Implement an ERP System. Investing in an ERP system is a significant investment of time and money. Understanding WHY your company will invest in the new ERP solution is essential.
A new ERP solution should bring real value to an organization. It should also be a strategic decision with tactical benefits.
3. Imagine Your Future State
Consider where your company should be in five to ten years. You should consider the company's size, employees, branches, geographic areas, and revenue growth goals. Consider the technology trends in your industry and any new products or services your company might offer.
4. To Drive The Selection Process, Recruit an Executive Sponsor
The selection team will require people, financial resources, and executive sponsorship to provide support at the top of the firm. The CFO, COO, or CIO/CTO often serves as the executive sponsor of ERP selection.
Sometimes, it's all of them and the CEO. The executive sponsor is responsible for supporting the project at its highest level. They also help identify and eliminate obstacles that could hinder the project's progress. This person will likely assist in selecting ERP team members and can resolve conflicts when they occur.
The executive sponsor should designate a project leader to oversee the selection team to ensure team coordination. This includes scheduling meetings, meeting milestones, and giving regular updates to the leadership.
5. Create The Software Selection Team
The goal and vision stages can be part of your premises software selection team. They can also be assembled after these points are established. A team that includes representatives from all functional areas involved in developing and implementing the software Market is the ideal group.
Managers are just some of the people you need to hear from, but the actual software users. This could include sales, finance, marketing, operations, and warehouse management representatives. These people will use their expertise to identify the essential features and functions that the software will provide to their teams. This team is often responsible for selecting the vendor/partner to implement the add-on software.
While some team members will be part of the selection process, others will continue to assist with implementation. The team should include representatives from all departments using the system, such as IT and Finance. However, they can also be drawn from other departments.
Define Your Requirements
To properly determine your requirements, evaluating your goals and process is crucial. This is an essential step as it will help guide your decision-making. You can start by listing what isn't working in your current system.
When defining requirements, research best practices and examine your goals. Create a central list that all team members can add to, and set up meetings to discuss workflows, process items, and company goals in the context of each team member's goals.
Get Started By Evaluating Your Current Business Processes
The natural tendency for each functional area of the selection team to base its requirements on existing processes is to define what the new system must do. This can lead to inefficient business processes designed to overcome limitations in the existing system.
The new ERP applications have many powerful capabilities that allow you to personalize the application and create automated workflows. This can often make your company's manual processes obsolete. It is also an excellent time to pause and ask, "Why aren't we doing it this way?" Why are we doing this?
You want to identify the business value of existing processes and streamline those that are not necessary or efficient.
This is a great time to meet with a business analyst for business analysis. They will help you find inefficiencies and determine your actual needs. This will help the team identify the fundamental requirements for the new ERP system.
Requirements For The Desired Future State
This is a sad statistic that can be avoided. Most companies don't spend the time to plan what their business functions will look like after implementation. Knowing the best way to get to where you want to be is almost impossible.
When defining your requirements, you should also define your future state. You will be grateful that you were as specific and measurable as possible. The ROI will be immediately apparent.
What is the ERP Solution Right For Your Company? How To Determine The Right "Tier"
ERP systems are often classified into Tier 1, Tier 2, and Tier 3. There is no one right way to determine the differences between tiers.
Tier 1
Tier 1 ERP systems are typically intended for enterprise-level corporations. These systems can be complex, feature-rich, and challenging to implement. They are also expensive, often costing millions of dollars.
Tier 2
Small to medium-sized businesses can use Tier 2 ERP systems. While Tier 2 systems are often more robust regarding financial and operational capabilities than tier 1, they have fewer features. Tier 2 systems can support companies in different countries, including international subsidiaries and branches. Tier 2 software is typically easier to use, more straightforward to learn, and less costly than tier 1. There are many options in Tier 2 project management software tools.
Tier 3
Tier 3 ERP systems are small software programs designed for small businesses with accounting and operational needs. Tier 3 ERP systems are less feature-rich than their tier 1 or tier 2 counterparts but come at a lower price.
Remember that large corporations can use many tier-2 products. Not all large corporations require the same capabilities as a Tier 1 system. This blurs the line between what is a Tier 1 system and what is a Tier 2 system.
Large corporations are made up of smaller companies. It is common for the parent company to run on a system of tier 1. At the same time, smaller entities operate on a system of tier 2. You must thoroughly understand your company's requirements to determine the correct tier.
ERP Requirements - Features and Functions
Although your ERP selection plan shouldn't be centered on features and functions only, it is essential to understand what functionality you need. This includes industry-specific requirements. The selection team should provide the requirements of each department.
Your selection team should ensure that they get input from those who will use the software. These people can give valuable feedback about what works, what doesn't work, and what they'd like.
Affordable And Long-Lasting Results: Any ERP system is a significant investment in time and money. You want your ERP system to support your company's operations and finances for many years. You must ensure that it can handle your immediate and future needs.
This means that the vendor who created the software must be available for the same timeframe. Your needs will change as your company grows. It is possible to track inventory sales online or manage inventory in multiple warehouses. As your business grows, you will also need to add new users.
You should look for an ERP system that allows unlimited user access. Also, keep in mind that costs to add users to ERP systems vary depending on what level of access they require. You will need to consider all your needs to find an ERP system that is flexible enough for your company.
The Ease Of Customization: No ERP system is perfect for every business requirement. Each solution will require some customization. The difference between ERP systems is the ease with which you can customize your business logic and the ability to upgrade these customizations, regardless of whether you use an on-premises solution or a SaaS one.
Industry-Specific Capabilities: Tier two markets offer the most industry-specific ERP solutions. You must choose if you want an industry-specific ERP solution or one that is best in class.
You can tailor your ERP Solution to suit your needs. Still, it may save you money on development by choosing an ERP solution that is already well-suited for your industry and contains modules that provide most of the required functions.
This has the downside that you may be tied to a support partner or vendor for specific industry-specific solutions. These solutions may be created by smaller software vendors that need more resources to keep up with technological changes or add new features.
Add-On Goods (ISV Support): Most ERP software packages are serviced by network independent software providers (ISVs). These ISVs create specialized applications that enhance the capabilities of the base product.
ERP platform providers often certify these apps and can be found on an app marketplace. These applications cover a broad range of capabilities including EDI and warehouse management, credit card processing and eCommerce, business intelligence, reporting, manufacturing, payroll, and many more. Ask your ERP vendor about app/ISV support and whether your company will need apps or ISV products.
Data Handling: Data handling. Your ERP system will need a database to store, access, and modify your business data. Not all databases will be the same, and not all ERP vendors will give you access to your data. It is up to you to find out where your data is stored and how it can be accessed. Also, it will be easy for you to back up and transfer your data. If you are considering changing ERP systems, you don't want your data held hostage by the vendor.
Ask your partner or software vendor how they would back up your data. If you are considering a cloud deployment, you should be aware of where customer data is kept and your responsibilities concerning data privacy. If you choose cloud deployment, your hosting provider should be able to provide SOC 1 or SOC 2 reports to show how they handle data privacy and security.
Reporting: Reporting. An ERP system can manage all aspects of your business operations. You will be able to generate reports showing your company's current state and provide real-time information. Most ERP systems can generate standard financial reports. However, most ERP systems allow users to modify or create new reports.
It can be challenging to make changes in ERP software. Some ERP software makes it almost impossible. Ask your software vendor how easy it can be to modify existing reports or create custom reports.
Flexibility: agility to grow with your basic business processes. It is also essential to consider whether the software can grow with your business environment. Some ERP solutions restrict the number of concurrent users, while others limit financial, international, or industry-specific capabilities. It would be best if you were sure your chosen software would allow your company to grow over the next five to seven years.
Scalability: You will need more computer power as your needs change (memory and disk space, data usage, transaction volume, etc.). These needs must be anticipated and addressed in an on-premises deployment. You will need to purchase the appropriate computers and staff to support them. Cloud deployments offer the advantage that you can have these resources added by the hosting provider as you require. You only pay for what you use.
Financial Capabilities: ERP software is designed around financial capabilities so that most accounting requirements can be met. Not necessarily.
ERP Requirements: Infrastructure
Selecting the right ERP solution is more than a list of features and functions. Your ERP system will touch every aspect of your business issues. It is, in many ways, the engine of business management. Therefore, it must perform well now and into the future. This requires the proper infrastructure.
Take into account the following areas.
- Transaction Processing: What volume of transactions do you need the system to process? Is there a charge for high-volume transactions
- Reporting: Do you have any reports that the system must produce? Are you using AI or business intelligence apps that need to be able to communicate with your ERP system
- Integrations: Can it be integrated with other business applications (CRM and HCM, eCommerce, productivity tools such as Microsoft Office, etc.)? )?
- Compliance: Do you have specific compliance regulations? Are you a public company?
- Data Storage: How big does your database have to be?
- Availability: Do you require remote access 24/7 for your company?
- Security: What are the user permissions and roles?
ERP Requirements: Deployment Options
Not too long ago, companies bought computer hardware with ERP software installed. They then maintained these systems in their corporate computer room (on-premises). To access the software, users had to be present at their desks.
Modern ERP systems can run on remote computer hardware and be accessed via the internet. This is sometimes called a cloud-based solution, Software as a Service, or SaaS.
Modern ERP systems can run in hybrid configurations. Some applications are hosted on servers on-site, and others in the cloud. Cloud deployments are the best option for most companies.
Accessibility: Cloud-based ERP apps are accessible from any location with an internet connection. This allows remote workers to be able to access the applications.
Security: Many top cloud-based software providers, such as Amazon and Microsoft, offer high availability and enterprise-grade intrusion detection. They also have servers in different locations to prevent failures from natural disasters.
Flexibility: Because hosting providers are leasing their computer hardware for cloud applications, they can scale your hardware usage to meet your current requirements. However, on-premises deployments require you to make an upfront payment for the hardware you'll need for peak demand, even if you don't use those resources 99 percent of the time.
Predictable Expenses: This monthly fee covers most of the maintenance and management of your cloud application. It reduces your toughest IT issues, IT costs and makes budgeting for a fixed amount each month easier.
Requirements Other ERP System Considerations
After the final ERP candidate has been selected and implemented, your selection team's requirements document will be used as the basis for acceptance testing by your company. This will ensure that the product meets your specifications. Your selection team should produce as detailed and complete a requirements document as possible.
Create A Short List Of ERPs
After you've narrowed your list to three to five potential ERPs, you can start to look into the details of the product and whether it is right for you. These are some tips to help you assess the potential candidates.
Where Are They Now in The Future? Where Will They Go Next?
Roadmap: ERP vendors publish a roadmap every year. The roadmap will show the product's direction over the next 3 to 5 years. Roadmaps will include ongoing bug fixes, support for the latest standards, future enhancements, and new features and technologies currently in development. Modern ERP solutions will include artificial intelligence (AI), machine learning (ML), and blockchain in their roadmaps.
Major and Minor Release Schedules: Software vendors all have a continuous release schedule that updates the software with new features, bug fixes, security patches, and enhancements to existing functions. The releases are sometimes referred to as "major and minor releases" (sometimes "point releases," like "Release3.2")
Major releases include significant enhancements to your application such as a new user interface, or an additional module that was high in demand. Minor releases include minor adjustments to the application such as bug fixes and adding a form to enhance usability.
The preliminary release schedule of an application can indicate how active the product development is. Software manufacturers are motivated to invest in their products for the future if they have significant releases at least twice per year.
Support: How Successfully Do They Assist You With Your Operations?
Integration Models: Integrating ERP systems with other business applications is becoming more critical. Look at the integrations for external business applications (CRM/HCM/BI, etc.). You are currently using or plan on using.
Support: Typically, you will be charged a maintenance charge (roughly 15-20% of your purchase price) for software that includes support and updates.
Subscription plans include updates to the core ERP system. The partner who installed the software might offer an individual support plan. These plans may include support for software usage, performing upgrades, or restoring service in case of outages. Each support plan's details and prices may vary. It all depends on whether you require 24/7 support or problem resolution within a shorter time frame.
It is essential to assess your business model and determine your needs. Your business solutions needs will determine the support plan that works best for you. Ask your partner in implementation to explain your options.
Flexibility And Scalability: Modern cloud-based ERP systems (and some on-premises deployments) allow you to toggle modules on or off, add or delete user licenses, and increase or decrease bandwidth, hardware resources, and transaction volume.
It is essential to find ERP solutions supporting your business strategy, including eCommerce, multi-warehouse distribution, manufacturing, Inventory Management, Human Resources payroll software options, and distribution. You don't want to be unable to access a market due to limitations in your system. Training should be provided to all key employees using the software.
Analyze How Do They Compare?
You will need to research to ensure you hear the product's good and bad aspects.
Industry analysts evaluate all major ERP systems. Analyst reviews give expert comparisons between ERP systems, highlighting the pros and cons. An implementation partner should be able to provide current analyst reviews for their product.
Customer Reviews: Although analyst reviews are great, it's also a good idea for actual customers to review your purchase.
Get References From Companies in Your Industry: Ask each implementation partner to give references to companies using the product. Learn about their opinions and how it has helped companies in your field.
Usability: Can You Adapt?
How simple the Enterprise resource planning system may be to implement and use doesn't matter. However, it will require a fundamental shift in your company's operations. There will be bumps in the implementation and complaints from staff about the software's functionality. You want to minimize the impact on employees who use the software daily.
Easy Implementation: Your implementation team must work closely with your ERP partner to plan the implementation. You are also evaluating ERP partners when you evaluate them.
Make sure to understand the implementation process, including the tasks that your team will need to complete and the expected timeframe.
Easy To Use: Every ERP vendor will tell you that their software is easy to learn and use. Let the vendor show you how to accomplish a few moderately tricky tasks your company faces daily. You can give them a list of these tasks and sample data to show how simple it is for your staff.
It is crucial to include suggestions from the staff who will use the software so that they can have a say in the selection process. It is essential to get their feedback on how the software should perform.
Easy Upgrades: Most modern ERP systems have made upgrades a routine task. Some ERP software upgrades are complex and time-consuming. Whether you decide to use the cloud or install it on your premises, it is essential to understand how to upgrade the software.
Pricing: Different Purchasing Methods
ERP software solutions can either be leased or purchased. You must understand the pricing models.
ERP software is yours when you buy it. You'll usually have to pay a portion of the purchase price for support and maintenance. This is typically between 15-20%. You will receive bug fixes and new features as they become available in the new releases.
Many ERPs charge by the number of users who need logins to the software systems. You might pay by the number of users that can log in at once ("concurrent users"), or by the name of users who have access to the software ("named users") for licensing. Users can also be charged different fees depending on how much access they need.
Vendors of cloud-based ERP will charge a monthly or annual subscription fee. The fee covers maintenance and software updates, but you're leasing the software rather than purchasing it. You will lose access to the software if you stop paying the fee or end your contract.
Prices Aren't All
While cost reduction is often a goal for many, it shouldn't be the driving force behind your decisions. Consider first that doing nothing is costly. You are not able to afford the cost of replacing an old system.
Second, remember to consider the price of modern ERP software for Businesses.
Ultimately, you are looking for an ERP system that will allow your company to grow in the next five years and beyond. Although it may not be the most affordable initially, this software can save you money through improved processes, scalability, and adaptability.
Conclusion
No matter how you deploy your ERP System, it is a significant investment. Your ERP system is the foundation of your business. It is the backbone of your business. Your employees rely on it to perform their jobs. It is essential for financial and accounting professionals to ensure money flows in and out. It is essential for your leadership team to make well-informed strategic decisions that will affect the future of your business. The right ERP can make the difference between success and failure, short-term and long-term.