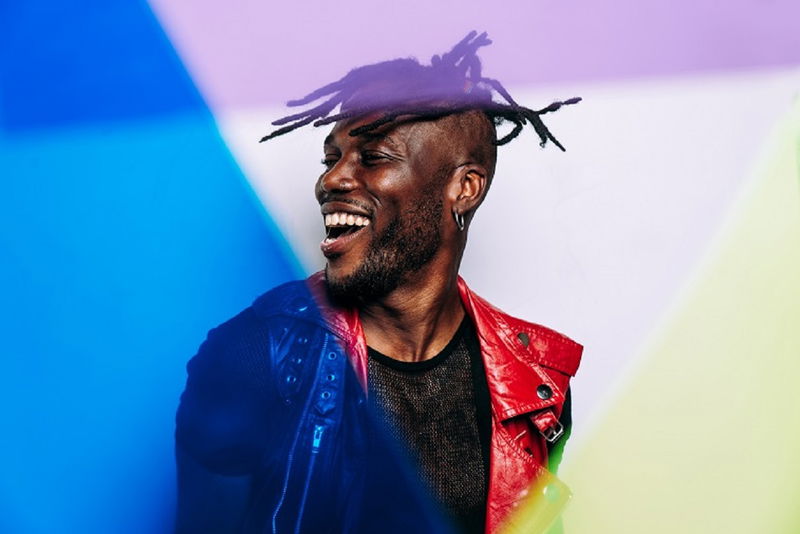
Inventory management is of utmost importance in any successful business. It must include tracking inventory from manufacturer through warehouse to point of sale, while effectively controlling product availability and delivery, thus lowering operating costs while increasing customer satisfaction. However, Poor inventory control management can have devastating results and disrupt supply chains, leading to fraud or financial loss from fraudulence.
Understanding Inventory Management
Inventory management system refers to ordering, storing, using, and overseeing an organization's stock, which involves raw materials, components, and finished goods and their processing, distribution, and warehousing - also referred to as raw material inventory control or material inventory. Optimizing inventory holding and guaranteeing that businesses have all required items on hand is achieved by identifying supply and demand trends.
Since inventory is a vital link between customer orders and production, its presence can make business operations run more efficiently. Inventory management entails adhering to best practices, maintaining an ideal stock level to satisfy customer demands, quickly responding to increased demand without incurring unnecessary costs, and avoiding downtime or running out of inventory, resulting in lost revenues; it involves understanding when, how much, and where extra stock should be stored to maximize revenue generation and minimize downtime or revenue loss.
Inventory Optimization
Holding on to goods helps businesses around the globe meet customer delivery on schedule while acting as an insurance policy should an emergency arise. Planners can lower production costs by mass-producing larger batches by keeping production and sales processes separate. Inventory policies only seek to achieve specific goals in context with our supply chains - providing an opportunity to find an optimal compromise between carrying too much or too little inventory by setting an achievable goal.
Cost-optimization in inventory policy only occurs if all costs, including opportunity costs, are included in our model. Inventory optimization solutions refers to ensuring sufficient stock is on hand to meet both present and future customer demand without incurring expensive inventory issues such as overstocking, backorders, or stockouts. By maintaining an optimal inventory level, businesses can satisfy customer expectations while preventing problems related to overstocking, backorders, or stock outs that might otherwise arise.
Companies seek to avoid negative impacts associated with inventory management, including decreased revenues, lost customers, manufacturing delays, and lost sales. Unfortunately, businesses sometimes experience difficulty when setting optimal inventory levels due to problems within other supply chain participants' chains.
Critical Strategies for Effective Inventory Management
Being saddled with too much inventory carries its own set of liabilities, from storage and insuring costs to spoilage risks to theft or damage that could severely impact cash flows and bottom lines. Inventory may be your company's greatest asset, making inventory management important in all supply chains and manufacturing processes. Employing effective techniques is critical for businesses with complex supply chains or manufacturing processes that need to strike an equilibrium between having too much and too little inventory on hand - to achieve this, several essential principles could form integral strategies of effective inventory strategies:
Establish Clear Inventory Procedures
To achieve greater operational efficiencies and prevent potential mistakes, business units, and branches must establish written procedures for efficiently handling inventory management across business units and branches - this includes purchasing, receiving, tracking, and selling of items.
Adopt an Inventory Management System
Reducing time spent managing company inventory could significantly reduce human error by adopting an inventory management software that utilizes modern technologies to automate tracking, alert when stock is running low, and predict future needs based on sales trends.
Implement Regular Auditing
To preserve the integrity of an inventory system, regular monitoring must include weekly or daily cycle counting (for high-value items with fast-moving volumes) in combination with stock takes at least every month; this ensures that inventory data matches up with what physically exists within stockroom shelves allowing early identification and resolution of discrepancies that arise in physical inventory real-time data.
Implement Just-In-Time Inventory (JIT)
JIT inventory involves placing orders only when needed to satisfy future demand rather than stockpiling items at all times. JIT can reduce depreciation costs as well as storage or warehousing fees; however, to prevent stockouts, accurate forecasting is crucial.
Optimize Warehouse Organization
Optimizing warehouse organization is critical for effective inventory control, improving warehouse and stock take efficiency via techniques such as ABC analysis that classifies items according to value or importance.
Plan for Unexpected Events
Maintaining 5 or 10% safety stock levels can help retail business owners prepare for unanticipated circumstances more efficiently and respond faster when customer demand shifts happen. Other challenges might arise from supply chain interruptions, seasonal variations in customer demand, or abrupt market shifts.
Track Key Performance Indicators (KPIs)
KPIs such as carrying cost, order lead time, stockout rate, and inventory turnover rate provide insight into how well inventory management is working for you and which areas require improvements - this allows for enhanced customer relationships, higher sales numbers and more significant outcomes overall. By employing these strategies, business models can increase their bottom line, reduce operating expenses, and boost efficiency.
Read More: Unlocking Success: The Top 10 Benefits of Inventory Management Software
Established Inventory Management Techniques for Businesses
Businesses utilizing inventory management techniques must utilize strategic approaches like inventory optimization techniques to optimize the movement and storage of goods through the supply chain. These procedures involve numerous steps and aim to strike an ideal balance between holding cost reduction and product availability - an outcome allowing businesses to reduce excess inventory while improving operational efficiencies and accurately controlling supply-and-demand dynamics.
Let's examine some effective inventory management techniques you could implement within your company.
Demand Forecasting
Demand forecasting is one of the critical inventory management strategies used in the e-commerce industry. This method forecasts future product demand using market trends, historical data, and other critical insights into buyer behavior. When performed effectively, it fosters responsive supply chains with reduced holding costs while optimizing stock levels for greater effectiveness.
Imagine a clothing store gearing up for winter: the retailer uses demand forecasting to analyze past winter sales data, isolate top performers, and anticipate rising coat demand projections. They order more coats while planning focused marketing strategies and actively managing inventory levels to match projected demand with their stock level; by doing this, they prevent stockouts while optimizing turnover by guaranteeing adequate and timely supplies of in-demand goods.
ABC Analysis
ABC Analysis is an invaluable inventory management strategy that groups finished products by how essential they are to the overall operations of your business. This systematic process ensures effective control over inventory that differs in significance levels.
Imagine an electronics retailer employing ABC analysis. Since high-end smartphones (Category A) make up such a sizable portion of sales, careful inventory management, evaluation, and calculated choices must occur for this category alone. Generic cables (Category C), although more frequently sold (Category B), receive less attention; accessories like chargers get special consideration by this classification system, ensuring optimal use of available resources while decreasing shortage risks and simplifying inventory control.
Just-in-Time Inventory
JIT Inventory management aims to minimize holding costs, streamline production processes and guarantee goods arrive precisely when needed. JIT emphasizes efficiency, waste minimization, and adaptability according to demand fluctuations.
Automobile manufacturers don't keep extensive inventories of various components; instead, they order just what is needed when production requires specific pieces. This strategy reduces obsolete inventory risks while simultaneously cutting storage costs and quickly responding to consumer preferences or market needs shifts. Adopting Just-In-Time (JIT) production allows a manufacturer to maintain lean types of inventory management systems while optimizing production efficiencies quickly in today's ever-evolving automotive marketplace.
Safety Stock Management
Safety stock supply chain management refers to keeping extra inventory beyond anticipated demand to provide valuable products in stock at all times, acting as a buffer against sudden shifts or delays in demand and supply chains.
Consider, for instance, how an online electronics retailer employs safety stock management: this retailer understands that demand can fluctuate unpredictably and delays may impede global supply chains; having safety stocks ready as buffers allows the store to fulfill orders while protecting customer experience efficiently - this innovative practice ensures no unexpected hiccups in an unpredictable industry like electronics!
Batch and Serial Tracking
Batch and serial tracking aims to keep tabs on individual product units or groups, improving inventory visibility and control in sectors of the economy where accountability and product traceability are of utmost importance. This service may prove especially advantageous.
Let me use an example to help explain this point further: batch and serial tracking is integral for pharmaceutical industries to meet stringent regulations, so each medication batch receives its own number, as does each unit within it. By tracking production, distribution, and sale in this way, pharmaceutical companies can follow each production run from start to finish - quickly detecting quality issues or recalls while meeting regulatory compliance.
Economic Order Quantity (EOQ)
Another popular inventory management solution model, Economic Order Quantity (EOQ), calculates an ideal order quantity that balances costs associated with placing and keeping inventory while simultaneously decreasing overall inventory expenses.
Imagine a retail company using Economic Order Quantity (EOQ) to determine how much of a popular product to sell simultaneously. They do this by considering demand, holding costs, ordering costs, and optimal order quantity (OQQ), which helps determine an order quantity with minimum overall expenses associated with an effective inventory management system - for instance, reducing holding costs while simultaneously keeping optimal stock levels while still meeting customer needs effectively. By employing this metric efficiently, they create an inventory system that efficiently meets both inventory management methods expenses and customer demand.
Return-Merchandise Authorization (RMA)
A structured procedure to manage product returns is known as Return Merchandise Authorization, or RMA for short. This approach ensures effective handling, transparent client relationships, and accurate product placement within an inventory system.
Let's use an example to illustrate RMA better: Consider an online retailer using RMA as part of its return management system, where customers initiate returns by filling out an RMA request and providing justifications for returns. Once assessed and qualified by an assessor, an RMA number is issued, and the updated inventory system marks it returned automatically. With its clearly organized returns procedure and insightful data for ongoing development purposes, businesses using this process increase customer satisfaction while gathering crucial intelligence needed for growth and development.
The Risk Of Not Managing Your Inventory
Inventory mismanagement poses severe threats to any organization, as evidenced by these examples:
Stockouts and Overstock: Without proper inventory control, companies risk running out of goods, which could result in lower sales, profits,, and damage to customer relations - both adverse outcomes. Meanwhile, an excess inventory can create resource waste, storage problems, and stock devaluation due to unsold obsolete items remaining unsold in storage facilities.
Cash Flow Issues: Companies must maintain balance in their inventory levels to free up funds for expenses such as marketing, payroll, and investment opportunities. Excess inventory investment could adversely impact a company's ability to expand and cash flow effectively.
Loss and Theft: Failing inventory management could result in misplaced or stolen products without detection or trackback mechanisms in place, leading to significant financial losses for your organization.
As part of an effective business strategy, dependable inventory management practices must be utilized to ensure maximum productivity, efficiency, customer service satisfaction, and reduced inventory costs. Proper inventory control helps mitigate these risks - an indispensable asset that, when managed effectively, can propel companies toward more tremendous success rather than becoming an obstacle in its way. It is time to reevaluate inventory as an asset rather than an obstacle and consider proper inventory management tool control as a valuable way of helping your organization thrive rather than an impediment to progress.
Get a Free Estimation or Talk to Our Business Manager!
Conclusion
Businesses of any size must effectively manage their inventory records to remain competitive and offer excellent customer service. However, staying abreast of emerging methods and finding cutting-edge inventory software management tools may present some difficulties.
Questioning inventory tracking levels can be complicated due to all the variables that influence warehouse availability. Effective inventory management resembles balancing your checkbook: too little inventory results in lower sales, while too much causes storage overspending and expiration dates to become at risk - striking the right balance can be challenging as consumer expectations continue to increase rapidly; one essential step toward real-time insight into consignment inventory items levels is having the appropriate number of products on hand and understanding what differentiates yours from theirs.