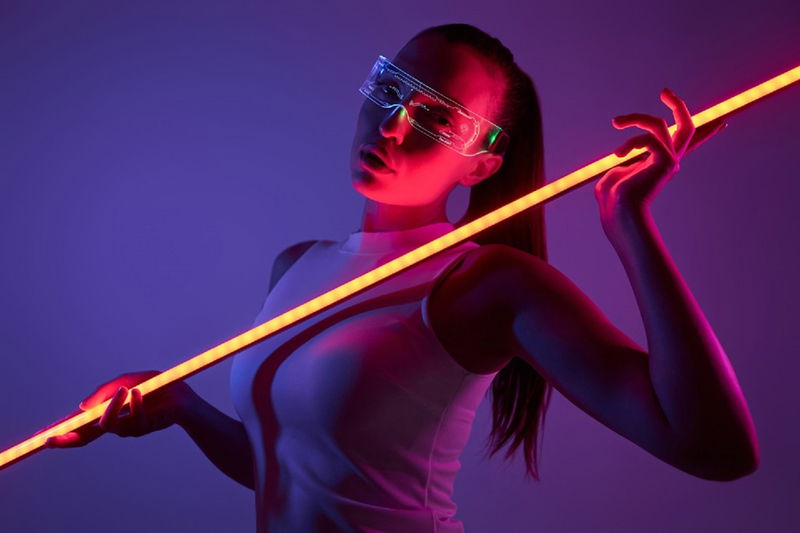
Manufacturing is an integral component in bringing products to market. Manufacturing efficiency can dramatically affect a company's performance, whether producing consumer goods or automotive parts. Operating costs in today's increasingly competitive global market strive to find ways to streamline processes while cutting costs, improving product quality, and being responsive when responding to customer needs.
The Role Of ERP Systems
Enterprise Resource Planning systems have revolutionized how companies manage their ERP manufacturing process. ERP solutions offer integrated software solutions that unify aspects of business such as finance, human resource management, inventory, and manufacturing under one umbrella centralized platform for data management and process control - helping organizations make informed business decisions while improving operations to drive growth and maximize returns on investments.This blog will delve into the world of ERP and its potential to transform manufacturing companies. We will examine its role in helping these organizations overcome common manufacturing challenges, its tangible advantages for manufacturing firms, and why implementing ERP systems makes sense for any organization looking for transformation. This guide is for anyone wanting to know more about ERP.Start the adventure now to discover how an ERP can transform your manufacturing processes, streamline operations, and set you on the path toward success in a highly competitive environment.
Read More: 5 Real-Life Success Stories: How ERP Transformed These Companies into Industry Leaders
Understanding ERP Systems (Enterprise Resource Planning Systems)
What is an ERP System?
Before discussing the benefits of ERP systems in manufacturing, it's crucial to understand what they entail and their operation. Enterprise Resource Planning refers to an integrated set of software programs designed to manage various organizational business functions - from human resources and finance management through supply chain management and procurement processes.An ERP system serves as a central data repository that facilitates seamless information access and sharing among departments and teams within an organization, thus eliminating information silos to ensure all stakeholders have access to accurate and current data.
Key Features and Functions
ERP systems have various features and functionalities designed to increase operational efficiency and productivity, making them an invaluable asset to manufacturing businesses.
- Inventory Control: ERP software allows manufacturers to monitor real-time insights inventory levels, optimizing stock levels and reducing carrying costs while avoiding overstocks or stockouts.
- Production Scheduling and Planning: ERP systems enable manufacturers to create schedules tailored to customer demand, available resources, and any potential production bottlenecks that might arise, thus improving on-time deliveries.
- Quality Control: ERP Systems provide powerful tools for tracking and maintaining quality standards during manufacturing processes to ensure products meet regulatory and customer expectations.
- Resource Allocation: These systems allow for an effective allocation of labor, machinery, and materials, resulting in cost savings and increased production capacity.
- Integration: ERP Systems integrate data from multiple departments into a holistic view, facilitating better decision-making and greater agility when responding to changing market circumstances.
We will explore how ERP features and functions can overcome common manufacturing hurdles and enhance manufacturing operations.ERP systems can revolutionize manufacturing operations. From streamlining processes to real-time data-driven decision-making, we will demonstrate their potential.
Manufacturing Faces Difficulties
Common Manufacturing Challenges
Manufacturing can present numerous obstacles that impede efficiency, profitability, and competitiveness - these must be identified and overcome to reach financial operations excellence. These can include:
- The Complexity Of Supply Chains: Modern manufacturing often relies on global supply chains that involve multiple suppliers and partners, leading to complexity in logistics, coordination, and inventory management.
- Production Bottlenecks: Inefficient processes in production can result in delays and blockages that interfere with meeting customers' demands and meeting deliveries on time.
- Quality Issues: Maintaining consistent product quality can be a formidable task since defects or deviations could result in expensive recalls, dissatisfied customers, or irreparable damage to a brand's image.
- High Operational Costs: Manufacturers often experience rising energy, labor, and raw material prices, which strain profit margins and thus make cost control an absolute priority.
- Compliance Issues: Manufacturers must abide by an extensive array of standards and regulations that vary based on industry. Navigating this compliance maze can be time-consuming and expensive, taking years of training to get up to speed.
- Lack Of Real-Time Visibility: Without proper real-time visibility, responding swiftly to changes in production or demand can be challenging.
ERP Addresses These Challenges
Here is where ERP systems shine. They offer comprehensive solutions to these manufacturing hurdles.
- ERP Analytics: ERP software provides analytics tools that streamline entire supply chains from procurement through distribution. This enables manufacturers to optimize inventory levels, shorten lead times, and enhance supplier collaboration.
- Production Optimizing: ERP systems' production planning and scheduling capabilities help identify and remove bottlenecks within manufacturing processes, improving efficiency and on-time deliveries.
- Quality Control: ERP software empowers manufacturers to implement and enforce quality controls throughout the production cycle, helping reduce product defects while guaranteeing consistency and ensuring greater supplier returns single source.
- Cost Control: ERP systems provide manufacturers with extensive financial and cost accounting features, enabling them to closely monitor expenses, allocate them correctly, and identify cost-cutting opportunities.
- Compliance Management: ERP software often includes features to track compliance with industry-specific regulations, ensuring that products meet required standards.
- Real-Time Data Access: ERP Systems offers real-time visibility of key performance indicators and critical business requirements metrics, providing decision-makers with accurate, up-to-date information to enable proactive decisions.
We will explore each ERP solution in-depth and discuss its advantages to manufacturing companies looking to optimize processes and gain an edge in an increasingly competitive market. Keep an eye out as we discuss how ERP systems transform manufacturing operations.
ERP to Optimize Operations
Inventory Management
A thriving manufacturing operation relies on effective inventory quality management to meet customer demands and manage costs. Balancing levels, minimizing carrying costs, and assuring access to finished goods and raw materials when required all play an integral part in keeping costs under control - these areas in which ERP systems excel.
Real-Time Inventory Tracking:
ERP systems enable real-time visibility of inventory levels, which helps manufacturers make informed decisions regarding restocking and production planning.
Optimized Resupply:
By automating inventory replenishment processes, ERP systems can help minimize overstocks and stockouts while cutting costs and disruptions.
Demand Forecasting:
Many ERP systems incorporate demand forecasting modules that use historical data and market trends to accurately predict future demand, helping manufacturers plan production and purchases more precisely.
Production Planning And Scheduling:
Manufacturing efficiency is at the core of business operations. ERP systems provide robust production planning and scheduling analytics tools that help manufacturers optimize operations.
Demand Driven Scheduling:
ERP Systems consider customer orders and inventory levels when creating production schedules that reflect actual demand, thus minimizing the risks of underproduction or overproduction.
Resource Allocation:
Manufacturers can wide range maximize production capacity by allocating labor, materials, and machinery more effectively - this reduces idle time while increasing production output.
Real-Time Monitoring:
An ERP system offers real-time monitoring that allows for quickly identifying issues that could interfere with production schedules.
Quality Control
In manufacturing, maintaining product quality is of utmost importance. ERP systems ensure consistency in terms of quality throughout production processes.
Quality Standards Enforcement:
ERP Systems allow manufacturers to set and monitor quality standards during every production stage, thus lowering risk and recalls.
Traceability
ERP Systems provides manufacturers with features that enable them to locate quality issues, facilitating targeted corrections quickly.These ERP-driven manufacturing solutions streamline processes and can lead to lower costs, increased customer satisfaction, and greater competitiveness. In the following sections, we'll examine how ERP systems use data integration and analytics to make real-time decisions and their contribution towards supply chain quality management improvement - all key elements that could revolutionize manufacturing at your company.
Real-Time Data And Decision-Making Are Integral Parts Of Success.
ERPs excel at data integration by connecting information from across departments and functions within an organization, including production, inventory, sales, and analysis data from warehousing to sales instantly and analyzed within manufacturing. Here are a few ways that ERP systems excel at data integration:
ERP Systems Are Repositories:
ERP systems serve as a centralized repository for all relevant data, eliminating data silos within an organization. Hence, all employees have access to up-to-date information.
Integrating Data To Maintain Consistency:
Manufacturers can utilize integrated data integration techniques to maintain consistency among their product specifications, pricing strategies, and customer records - helping reduce errors and discrepancies that arise as a result.
Real-Time Updates:
Any modifications made to one department or phase of production are instantly reflected throughout the system, providing better visibility and helping make better decisions.
Data Analysis and Reporting
Manufacturers can efficiently utilize ERP systems to perform data analysis and reporting, taking advantage of their available information.
Key Performance Indicators (KPIs):
ERP allows manufacturers to track and define KPIs most crucial to their business, such as production efficiency rates, on-time deliveries, and inventory turnover.
Customized Reports:
Manufacturers can create tailored dashboards and reports that provide insights into various aspects of their businesses, giving visibility into trends, bottlenecks, and potential improvement areas. These reports can assist them in pinpointing regions requiring attention or improvement.
Predictive Analytics:
Some advanced ERP systems incorporate predictive analytics, allowing manufacturers to anticipate future demands, maintenance needs, and market trends.Manufacturing companies can gain an edge by harnessing analytics and real-time data. With this information, manufacturing firms can make informed decisions, quickly respond to market fluctuations, and optimize their processes for continuous improvement. Next, we'll explore how ERP systems can enhance supply chain production management, lower costs, comply with regulations, and more. We will also cover practical aspects of choosing, implementing, and measuring the ROI of ERP systems within manufacturing organizations. Stay tuned for further valuable insights about ERP and manufacturing excellence.
Improving Supply Chain Management
Supply Chain Visibility:
Effective supply chain production management has become essential in today's globalized marketplace. ERP systems play a crucial role in increasing supply-chain visibility - the ability to track and monitor every aspect of its functioning in real time.
End To End-To-End Visibility:
ERP systems offer comprehensive visibility over supply chains from procurement and supplier relationships through ERP in production and distribution, allowing manufacturers to identify inefficiencies while making strategic choices.
Demand Forecasting:
Manufacturers can minimize excess inventory and stockouts by employing real-time data and accurate demand projections.
Supplier Collaboration:
ERP software often includes financial management tools to assist suppliers, which helps streamline communication and reduce lead times while strengthening relationships between key business partners.
Supplier Relationship Management
ERP systems make Supplier Relationship Management simpler. A vital aspect of supply-chain management, it makes the relationship between suppliers and companies simpler to oversee.
Supplier Performance Monitoring:
ERP software allows manufacturers to monitor supplier performance on delivery times, pricing, and quality - essential when selecting and negotiating suppliers.
Automated Procurement:
ERP can automate the procurement process to ensure materials are ordered in sufficient quantity and at the proper times, thus cutting costs.
Supplier Portals:
Many ERP systems now feature supplier portals where suppliers can gain access to orders accounts receivable, accounts payable, shipments, and payments directly. This increases transparency and efficiency.
ERP systems help manufacturers increase agility by improving supply chain financial management tools . In this session, we'll explore how ERP systems can reduce costs and optimize resources - ultimately making manufacturing operations as profitable and efficient as possible.
Resource Optimization and Cost Reduction
ERP - Managing Costs
Manufacturers emphasize managing costs effectively, and ERP systems offer tools and capabilities that can assist them with doing just that.
Cost Visibility:
ERP systems offer manufacturers clear visibility into cost components like materials, labor, overhead, and maintenance expenses - giving them the power to identify cost-cutting opportunities and find ways of cutting expenses.
Cost Allocation:
Allocating Costs Precisely By giving costs accurately across products or processes, manufacturers can ascertain their actual production costs, providing essential insight for pricing strategies, profitability analysis, and other business growth decisions.
Waste Reduction:
ERP systems assist organizations in identifying and eliminating unnecessary expenses such as extra materials, operational processes, or unneeded labor hours.
Resource Allocation and Utilization
It is vital to allocate and utilize all available resources effectively to maximize production efficiency and profitability. Labor, machines, and materials all play crucial roles.
Resource Allocation:
An ERP system assists in resource allocation by allocating them according to production schedules and predicted demand, thus maximizing resource use efficiency while minimizing downtime.
Maintenance Schedule:
Many ERP systems feature modules for preventive maintenance that track and schedule activities to reduce unscheduled downtime and extend asset lifespan. This will reduce unscheduled downtime while prolonging asset longevity.
Labor Management:
ERP software helps manufacturers manage their labor resources more effectively by keeping track of hours worked, skills employed, and assignments made - leading to improved employee productivity and results in cost reductions and higher turnover.Manufacturers can increase operational efficiency and profit by optimizing resources and cutting costs. ERP systems act as essential tools to make these enhancements possible.
Next, we will explore how ERP systems can ensure compliance with industry standards, provide product traceability, and provide real-life examples. Look out for further insights about ERP's transformative power in manufacturing industries.
Traceability And Compliance
Compliance with Regulatory Standards in Manufacturing:
Manufacturing industries operate under numerous regulations and standards that vary based on what they produce and where they work, so adherence is crucial not only legally but also to maintain product quality and safety.
Tracking Regulatory Compliance:
ERP can assist businesses in tracking and managing compliance to industry-specific standards and regulations, offering essential tools to ensure products comply with all requirements.
Document Management:
ERP software allows manufacturers to maintain an extensive library of compliance-related documentation, making it more straightforward to demonstrate compliance during audits or inspections.
Quality Audits:
Many ERP software systems feature features to facilitate quality audits and inspections that help detect compliance issues quickly and implement solutions quickly.
Product Traceability And Enterprise Resource Planning
Tracing products is an integral manufacturing component, especially in the food, pharmaceutical, and aerospace industries. Traceability involves documenting every production history for every item produced during its lifecycle.
Tracking Serial And Lot Numbers:
ERP software allows manufacturers to assign unique serial or lot numbers for each product, providing complete traceability from raw materials to finished goods.
Recall Management:
In case of recalls, ERP systems quickly identify affected products, suppliers, and customers to reduce any negative repercussions for the company and its customers. It is vitally essential that recalls are managed effectively to minimize any impact they might have on the reputation of both.ERP systems mitigate risks and enhance product safety and quality by ensuring regulatory requirements compliance and traceability of products.
Selecting An ERP System
Factors to Keep in Mind
- Selecting An ERP System: is crucial to the operation and competitiveness of any company, and here are some essential considerations when making this selection:
- Industry Fit: When searching for an ERP for manufacturing industry, ensure it comes equipped with industry-specific modules and features that could prove highly beneficial. Manufacturing ERP solutions often contain these valuable extras.
- Scalability - Choose a scalable one to ensure that your ERP system can grow with your company. When your business expands, its capacity should increase to accommodate additional users and production and any new features or modules that arise.
- Integrity Features: When considering purchasing an ERP system, its integration capabilities should be thoroughly examined to ensure a smooth implementation with minimal disruptions and downtime.
- User-Friendly Interface: The user interface must be user-friendly to encourage employee adoption, and training requirements should be manageable.
- Customization: Select an ERP system that offers customization features to meet your manufacturing operation's unique core business processes and needs. Prefabricated solutions may not provide the needed solution.
- Reputation Of ERP Vendors: When researching ERP vendors' track records and importance, look for reviews from customer relationship management as well as case studies and references that provide insight into support and performance.
- ROI and Cost Analysis: Determine your total costs associated with ownership for software license, implementation, ongoing maintenance, and training, as well as an expected return on investment (ROI) to assess whether or not a system is financially sustainable.
Vendor Comparison
Make an informed choice by comparing multiple ERP offerings of vendors. Create a shortlist of vendors who meet your needs, perform detailed evaluations on them, and request demos or speak with vendor representatives directly before seeking input from key stakeholders.As we proceed through this section, we will explore best practices for implementing ERP systems in manufacturing companies, identify common implementation obstacles, and explore source of truth strategies for user adoption. Be on the lookout for tips to make your ERP implementation a success.
Read More: Unlocking the Power of Efficiency: Exploring the Inner Workings and Key Functions of an ERP System
Implementing Manufacturing ERP
Plan And Prepare
- Planning and Preparation: A successful implementation of ERP in your manufacturing organization relies heavily on planning and preparation. Here are some key points:
- Needs Analysis: Conduct an in-depth needs analysis to understand what challenges your organization needs an ERP system to solve.
- Selecting A Project Team: Establish a project team of representatives from departments like IT, finance, production, and procurement - this team is essential in successfully implementing any plan.
- Establishing Requirements: Collaborate with your team to outline detailed requirements encompassing workflows, processes, and data integration for an ERP system selection or customization project. These specifications will guide the selection or modification processes within an ERP solution.
- Select an ERP vendor according to your budget and requirements, considering their manufacturing experience, customer service offerings, and module/feature availability.
- Configuration And Customization: Work closely with your vendor to personalize and configure your ERP system to accommodate your organization's processes. Setting up data structures, workflows, and user permissions may be necessary.
Adopting Best Practices
- Adherence: to best practices will facilitate a smooth transition.
- Training: Invest in comprehensive staff training to make the most out of an ERP system. Users must understand its capabilities to use it efficiently and reap its full benefits.
- Change Management: Successful ERP implementations often necessitate production process modifications. Communication of these alterations to employees is of utmost importance - any resistance or concerns must be dealt with immediately.
- Data Migration: Data transfers must go smoothly between existing and an ERP system, with accuracy playing an integral part in its success and implementation.
- Testing: Before going live with the ERP system, conduct extensive tests to detect any glitches or issues that might arise.
- Phased Implementation: Take an incremental approach when rolling out an ERP system across your organization. Begin with a small pilot group before expanding its use throughout your business.
- Support after Implementation: Plan on providing ongoing maintenance and support for any issues that may arise post-implementation, as well as updates and optimization of the system.
Overcoming Obstacles
ERP implementations may present numerous obstacles, from budget overruns and timeline delays to staff resistance. Anticipate these hurdles early and address them directly - working with an experienced ERP partner or consultant may prove particularly valuable here.As we progress, we will discuss strategies to ensure user adoption of ERP, evaluate ROI, and keep up-to-date with future trends. Keep an eye out for more helpful insight on maximizing the benefits of your manufacturing ERP system.
Measuring ROI
Key Performance Indicators
You must measure the Return On Investment (ROI) of an ERP system to understand its effect on manufacturing. Key performance indicators (KPIs) provide a great way to measure its success; manufacturing ERP ROI can be measured using various KPIs.
- Cost Reduction: Determine any possible savings within an ERP system, such as labor expenses, inventory expenses, and maintenance expenses, as well as operational expenses.
- Production Efficiency: Assess changes to production cycle times, throughput rates, and overall equipment efficiency (OEE) before and after ERP implementation.
- Inventory Optimization: Assess improvements to inventory turnover rates and reduce carrying costs to optimize inventory optimization strategies.
- Quality Assurance: Monitor improvements in product quality, customer satisfaction levels, defect, rework, and scrap rates over time.
- Timely Delivery: Evaluate improvements or decreases in on-time delivery rates and order lead times.
- Revenue Growth: Assess revenue growth that results from enhanced customer satisfaction, faster order processing times, or increased market presence.
Calculating ROI
An ERP Solution: You can use this formula to calculate the return on investment (ROI) for an ERP system:
- Benefits to ERP include all cost of ownership and revenue savings directly attributable to ERP systems.
- Total costs: This category encompasses all costs related to ERP system implementation, training, and ongoing maintenance.
An ERP has proven its worth by producing more key benefits than costs incurred, making it a worthwhile investment.
Continuous Improvement
Measuring return on investment (ROI) should not be undertaken once and left alone; rather, it should be seen as an ongoing manual process that needs to be reviewed regularly and KPIs adjusted according to your manufacturing processes and organization as they grow. Optimize your ERP system consistently using data to ensure it continues providing value.In our final sections, stay abreast of future ERP manufacturing trends, such as their integration with Industry 4.0 and artificial intelligence. Stay up-to-date with manufacturing excellence.
Future Trends of Manufacturing ERP
Integrating Industry 4.0 with IoT
Industry 4.0 represents a transformation in the manufacturing sector driven by digital technologies, the Internet of Things (IoT), and automation; ERP systems must adjust accordingly.
- IoT Connection: Manufacturing SAP systems are increasingly integrated with IoT sensors and devices on the shop floor, enabling real-time equipment monitoring, predictive maintenance, and data-driven decisions.
- Big Data Analysis: ERP Systems are taking advantage of Big Data analytics to analyze and process vast amounts of manufacturing information, giving manufacturers access to insights, revealing patterns, and optimizing operations.
- ERP Cloud: Cloud ERP solutions have become more prevalent, offering scalability and flexibility for distributed operations. Access can be gained anywhere with an internet connection - which makes these systems especially helpful to manufacturers who operate from multiple locations.
Artificial Intelligence And Machine Learning:
- Manufacturing: ERP systems have increasingly integrated artificial intelligence (AI), machine learning (ML), and other cutting-edge technologies into their designs.
- Forecasting Demand: AI algorithms and machine learning techniques can significantly enhance demand forecasting accuracy by examining market trends and historical data.
- Predictive Maintenance: AI-driven predictive maintenance models can identify equipment issues before they lead to downtime, helping reduce maintenance costs while improving uptime and availability.
- Quality Control: AI-powered image recognition and product quality control systems detect anomalies and defects automatically, helping ensure their quality and consistency.
- Natural Language Processing: ERP systems with natural language processing features allow voice activation and natural language queries, simplifying users' interaction with the software.
Mobility And Accessibility
Mobile ERP has quickly become more prevalent among manufacturers to enable real-time data access and functionality.
- Mobile ERP Applications: Mobile ERP applications empower employees to complete tasks and access crucial data on smartphones and tablets, increasing flexibility and responsiveness.
- Remote Monitoring: Mobile Access allows users to remotely observe manufacturing processes even if they're not physically on site.
- Field Service: Mobile ERP solutions explicitly designed to support manufacturers with field service teams provide efficient scheduling, real-time updates, and seamless communications.
These future trends for manufacturing ERP can help your organization remain flexible, competitive, and efficient in an ever-evolving industry.ERP systems can be invaluable in optimizing business processes, increasing efficiency, and increasing profits for any manufacturing business. Stay abreast of industry trends while optimizing your ERP software to drive business expansion and excellence in manufacturing businesses. Feel free to reach out if any additional questions or material requirements for further details.
Conclusion
ERP system for manufacturing industry play a pivotal role in improving operational efficiencies. Their robust functionality enables manufacturers to create efficient production processes, increasing productivity and customer satisfaction. Focus MRP can help any manufacturer optimize business operations and achieve lasting success over the long haul. Please fill out the form below to gain more information.