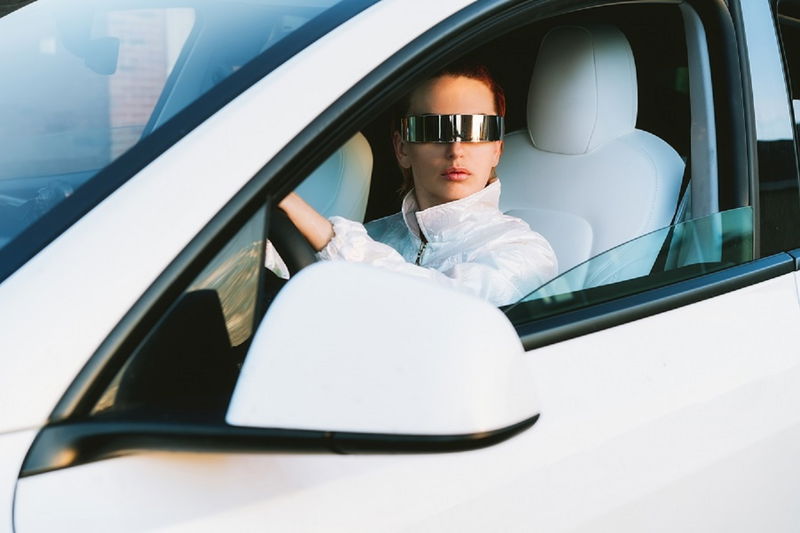
Warehouse management is crucial to ensure products arrive on time while reducing operational costs and increasing profitability. Of course, an organization is crucial. There are many ways to optimize warehouse operations, improve business profitability and increase profits. These include warehouse layout and organization.
What Exactly is Warehouse Management?
Warehouse management manages all aspects and decisions involved in warehouse operations. This includes order picking, warehouse organization, warehouse management, workforce management, and shipping coordination. Warehouse management aims to integrate all these factors effectively, reduce complexity, increase efficiency, and reduce costs without compromising quality or accuracy.
Warehouse Organization
The organization of a warehouse requires many variables. This is crucial to ensure smooth operations and timely order fulfillment. It is important to organize items in a way that allows them to be identified easily. Clear labels, efficient racking, bins, clean aisles, and designated picking/receiving zones can achieve a well-organized warehouse operation.
Warehouse managers increasingly use warehouse management systems (WMS), especially as their responsibilities and tasks grow. A WMS can help an online retailer expand its product ranges. It can also provide organizational strategies that allow the company to use its space better to meet growing customer demand.
How to Keep Inventory Organized
Inventory Management is managing all stock in a company, sometimes across multiple warehouses. This covers how goods are stored and handled, tracked, ordered, shipped, and returned. Inventory management aims to balance stock levels, consumer demand, and space and money savings.
It also helps reduce waste and saves money. Software that automates inventory management can be used to prevent loss, no matter how complicated a warehouse operation may be. It also streamlines order fulfillment and inventory processes.
Tips For Warehouse Management
Warehouse management can be complex, multifaceted, and challenging. It is not enough to ensure that everything is organized properly and that all items are placed where they belong. Warehouse managers must consider other factors such as how they organize their warehouse, label their items and how store them, what KPIs they should track, how to manage their workers, and which WMS to use.
Here is a complete list of tips to help warehouse managers make their operations faster and more cost-effective while still providing the best working conditions for employees. Warehouse managers can also improve their methods by following these tips.
1. Understand Your Goal
A warehouse operation must know its goals to succeed. The factors that impact your warehouse management strategy most are listed below. These might include incorporating refrigeration into your warehouse or addressing specific customer delivery needs.
2. Safety Is a Top Priority
Warehouse accidents can be avoided by too fast employees who forget about safety procedures. Employees should learn to avoid dangerous behavior and feel that they are working for a company that puts safety first.
Warehouse managers must be vigilant to avoid slips and falls. Warehouses that require repetitive manual labor are prone to muscle strains, lower back injuries, and other musculoskeletal conditions. Employers can lower the chance of injury by emphasizing ergonomics and short rest breaks.
3. Keep Track of KPIs
Continuous monitoring and measuring metrics is the only way to measure warehouse and warehouse staff performance. It will help if you track key performance indicators (KPIs), including general metrics like cost per order shipped and more specific goals like inventory error rates. Warehouse managers can foster a culture that rewards and measures these KPIs. This will result in a more productive and efficient operation.
4. Regularly Evaluate KPI Metrics
Businesses can use KPIs to understand their warehouse performance, how they are meeting goals, and what they can do to improve. It is important to keep KPIs current and aligned with an organization's evolving strategy. For example, an ecommerce platform with a next-day delivery policy should establish KPIs that encourage speed and efficiency.
5. Flexibility is Key
Warehouse operations are not like any other business. No two days are ever the same. Flexibility is key to being productive in the face of change. Warehouse managers can use many options to ensure their operation is flexible, from optimizing layouts to strategic inventory reserves.
6. Maintain Cleanliness
Clean warehouses are a great asset to warehouse organization. Clearing out obstacles that could hinder employees' work is a great way to find lost or forgotten items. If teams work well together, weekly cleaning is a good idea. However, monthly deep cleans are possible if they tidy their work area.
7. Cut Down On Clutter And Waste
There are three reasons clutter and waste should be avoided. It creates a safe and efficient working environment for warehouse workers, so they won't have to stumble on messes. It inspires confidence and shows visitors that the warehouse is in control. Staff may be more proud of their work if the space is clean and uncluttered.
8. Stackable Bins Should Be Used
Stackable bins can be one of the most versatile pieces in a warehouse. They can store small items, particularly high-demand items that must be readily accessible. These bins are small enough to be kept on the desks of warehouse workers or in their work areas. This is why they are frequently used to store labels, invoices, and other documentation. Bins are also useful for protecting items from dirt and other debris.
9. All Products Should Be Labeled
Labels can make a big difference in warehouse efficiency and employee morale. Companies can ensure pickers find the right inventory by labeling it according to industry standards. This reduces labor costs and eliminates frustrations such as being unable to find the right item or losing orders.
In recent years, labeling technology has improved tremendously. Businesses can now get heat- and cold-resistant labels that can be read electronically. This can also allow them to track their orders in their WMS.
10. Utilize Labeling Systems
Barcode labeling systems are a cost-effective and efficient way to label warehouse products. They also reduce human error. Warehouses face increasing demands and complexity.
Code-based systems such as SKUs make it easier for workers to label and record every product that passes through their warehouse walls. Barcoding software can also be linked to the WMS of the business, providing warehouse managers with real-time visibility into inventory and products.
11. Organize for Effectiveness
It's not just about locating the items. Organizing for efficiency involves more than just arranging them. Every stage of the picking, packing, and shipping can be streamlined. An efficient warehouse would store all packing materials, such as tape, scissors, and boxes, in one place, with clear labels for employees. You can also separate packing materials based on their size and the packed product type. These small efficiency gains can result in significant savings.
Want More Information About Our Services? Talk to Our Consultants!
12. Get Organized With Your Industry in Mind
The decision about where an item should be stored in a warehouse is influenced by who bought them and how often they were picked. This varies from industry to industry. A wholesaler may regularly ship multiple items to the same place at once. At the same time, a small retailer may only occasionally send out a few products.
13. Combine Like Items
Although it may seem common sense, similar items should not be stored far apart. A megastore selling office supplies should keep all its organizers and binders in one place and electronics in another.
14. ABC Analysis
Businesses use ABC analysis to establish a hierarchy for their products. High-value items are those that generate the most revenue. These items are usually big sellers and expensive, so they're stored in smaller quantities close to their packing area. C-level items are slower-moving and lower-value. For example, spare light bulbs might be needed by a lamp manufacturer. A shoe retailer may use totes bags. These items can be stored farther from the packaging area.
15. Organize Items According to Order Frequency
Some products are more popular than others, just as certain items have a higher value (A items vs. C items); the closer an item should be placed to packing areas, the more popular it is. A children's toy company might place its pool toys closer to the packing area during summer and then move its winter sleds further away until the season changes.
16. Take Into Account Traffic Patterns and Flow
A warehouse that is well-organized and easily accessible will allow products to move between receiving, storage, and shipping. This results in a cost-effective, smooth operation that produces minimal waste and maximizes fulfillment. Based on the specific business needs, many traffic patterns and layouts can be used.
Some businesses might place the most-moving items near shipping areas to minimize travel time. Some may group items that are often picked at the same place; this is why many ecommerce companies have warehouses that appear to be stocked randomly with random products.
17. Employer Input
Warehouse managers can see the big picture of their warehouse operations from afar. Still, employees on the ground will be able to spot the small obstacles that keep them from being productive. Managers can use this information to identify the root cause of traffic jams and address weak areas. They also can improve potentially dangerous processes.
18. Create Workstations
Designated workstations serve two purposes: They make sure employees have the right equipment for their jobs, which can increase productivity and engagement and help prevent injuries. Standing work surfaces are more comfortable for shipping, packaging, and receiving staff.
19. You Can Create Zones Based on The Type of Order You Choose
Different picking methods work well with different storage options. Zone picking, for example, logically separates SKUs into zones in the warehouse. To fulfill orders, workers are assigned to a specific zone. A picking bin is then passed from one zone to another.
20. Organize Aisles for Maximum Efficiency
Packaging as many products as possible in a small space can be tempting. However, this will lead to diminishing returns. If the aisles are too crowded, it isn't easy to find the product. It is important to label and identify aisles. Stock management is all about being able to locate inventory. This will ensure that your warehouse management system correctly places items upon receipt.
21. Reduce Barriers and Maximize Space
If a small obstruction, such as a shipping box or carton that is not in its proper place, becomes a big problem. These small obstacles can create bottlenecks, leading to delays in operations during busy times. It is better to be proactive and ensure that all inventory and boxes are well-organized so employees can move freely and be productive.
22. Allow Yourself to Receive
It is important not to treat inventory receiving as an afterthought or make it a part of a cramped warehouse corner. This can cause inventory management errors and bottlenecks. It also leads to inefficient receiving procedures that cost time and money. The receiving area should be large enough to accommodate all shipments and well-equipped to ensure that each item is accurately logged, stored quickly, and tracked from the moment it arrives.
23. Make The Most of Every Space You Have
It is important to balance warehouse space and ensure pickers can move easily through the aisles. However, efforts should be directed toward maximizing every square foot.
24. Make Use Of Vertical Storage Solutions
Vertical inventory solutions can be used to build upward before expansion or relocation. Stackable bins and shelving, which look like high-rise warehouses, allow businesses to store more inventory without taking up too much space on the roads. Vertical lift modules (VLMs) can also be used, similar to industrial vending machines. You can stack them up to 12 meters high. Each one can be electronically labeled so that it can be easily retrieved using a programmable moving shuttle.
25. Use Space Sparingly Whenever Possible
Storing the items in the right place is just one part of the battle. The best storage solutions can make your warehouse space more efficient. Warehouse managers must adapt the shelving size and type to their products instead of putting them all on the same pallet racks. You can also store items vertically in taller, stackable storage. Specially-adapted machinery can be used to pick these items. Consolidating and avoiding sprawl is the goal.
26. Digitize Your Paperwork
Missing paperwork can be a problem with paper-based systems. It can also make it difficult to translate information for digital storage. Warehouse managers can reduce the chance of losing information by entering data directly into a platform. Digital platforms also eliminate the need for paper and writing supplies, which can prove costly in large warehouse operations that rely on manual methods.
27. Automated Processes
Due to the boom in online commerce and sales, warehouses are under increasing pressure to improve their operations. Automation is the only way for warehouses to meet increasing demand and scale up. Automated tools such as robotic picking and cartonization software can choose the best packaging for each item based on its dimensions, shape, weight, and other requirements.
28. Make Use of Inventory Management Software (IMS)
With Inventory Management software, businesses can ensure they have enough inventory at the right places to meet customer demand. Customers can place high orders during busy retail or work orders at the company's manufacturing plant.
Many inventory management systems are scalable, meaning businesses can continue using the same system as they expand their warehouse operations, launch new products, or modify their fulfillment strategy and KPIs.
29. Make use of a Warehouse Management System (WMS)
Warehouse management systems can help warehouse managers simplify fulfillment processes. Warehouse management systems (WMS) include key features to manage order fulfillment, receiving and putaway, inventory control, and real-time visibility into warehouse operations. Warehouse managers use their WMS to create the most efficient workflows for all that happens in their warehouses or similar facilities.
30. Employ an Enterprise Resource Planning (ERP) System
ERP software allows businesses to connect warehouse management, inventory management, and a variety of other critical software systems, such as accounting, human resources, and more, all from one platform. Warehouse managers have a comprehensive view of their business operations and the whole company. They can find all the information they need with just a few clicks.
31. Invest in Pick-Aid Technology
Technology-driven and automated picking systems can speed up the process and reduce travel time. Pick-assisting technology constantly evolves, with advanced picking robots and drones, mobile barcode scanning, and pick-to-light technology.
Read More: Why is Inventory Management Important?
32. Use Conveyor Belts, Sorters, and Carousels
For all warehouse operations, conveyor belts, sorters, and carousels may not be the best choice. Vertical lift modules (VLM) might be better for warehouses with high product stacks. These automation technologies are appealing for many reasons. They are inexpensive and easy to maintain.
33. Choose the Right Order Selection Methods
There is no single method that works for all picking methods. Pickers will use one approach for each warehouse and order type. They travel through the warehouse, collecting all items needed for that order. You can collect items directly into shipping cartons, totes, or carts. Picker-to-part is a subset that records the dimensions and weight of orders before they are picked.
They then choose the right shipping container and place orders into it. This is another subset of picker-to-part. Workers pick up and place the items directly into a bag. The orders are then taken to the appropriate packing station and sorted before being packed for shipment.
Pick-assisting technologies such as robots or sorting systems allow products to be moved from storage areas into designated picking bays where the picking operator collects them.
34. Choose The Right Order Type
Companies can use various picking strategies to find the perfect balance between speed, accuracy, and cost. Each worker picks up the entire order and then takes them to a shipping area. Many orders are divided into smaller batches. For each order, workers pick multiples of each item from their lists.
This makes it impossible to pick the same items over and over again. Order pickers are divided into zones to pick products in designated areas. Workers complete picks at set times throughout the day, called waves. Waves are often aligned with other warehouse goals, such as shipping departures.
35. Continue to Evaluate Your Picking Strategies
Regularly evaluating picking strategies is necessary to ensure they remain the most effective option in current picking conditions. This should take into account customer demand and inventory requirements. A multi-order approach might be required to launch a new product line.
36. Travel Time Reduced
More than half of order pickers' time is spent moving around warehouses or traveling. Although it may seem small to have to go back a few steps to add an SKU, this can quickly add up over time, especially when multiple employees are involved. This is time lost for the business and an expensive drain on order pickers that can drive up costs. To reduce travel time, picking processes should be optimized.
37. Sequence Picking Orders Logically and Automated Pick Paths
Although warehouse workers can sequence pick lists independently, modern warehouse operations require a software-based approach. WMS automatically determines the best pick types and paths, regardless of how many or diverse orders they receive. This reduces both travel time and calculation, which increases productivity.
38. Reduce The Number of Shipping Containers
Although it may seem appealing to use shipping containers of different sizes to reduce waste (e.g., avoid large packaging for small items), this can make it more difficult to store shipping cartons in a standard way. Warehouse workers must also take the time to determine which container is best for each item. Storing too many containers may be a waste of time, especially if it slows down operations.
39. When Possible, Choose to Cart
Before picking a carton, selectors take note of the order's dimensions and weight. Based on this information, the appropriate shipping container is chosen, and the item is packed directly inside. This allows the company to save money on labor and materials, but it is important to implement this process strategically. Pickers should begin with heavier items and then work their way down to lighter items that are less fragile to prevent damage to boxes or products.
40. Create Receiving Policies And Procedures
A clear process is essential for effective inventory management. This includes how products should arrive at the warehouse and how they should be stored. While a simple policy sheet can be sufficient, it is better to outline a detailed procedure in your inventory management software.
For example, if a shipment of parts for cars arrives at the receiving area, the policy manual would outline who will be responsible for tracking the inventory, where they should be stored, and how to place them on the shelves.
41. Inventory Control and Accuracy Should be Prioritized
Businesses should invest as much effort into inventory management and tracking as they do in product layouts to make the most of a well-organized warehouse. An Inventory management system is a good tool for inventory control. It can keep detailed records. This will give warehouse managers a clear snapshot of their inventory and allow them to see their location.
42. Cycle Counting
In a world with changing product offerings and customer demands, relying on only taking inventory once a year is not a good idea. Warehouse managers should consider a cycle counting system that counts inventory multiple times per sales cycle. This will depend on the company's operating conditions. However, it will allow for more accurate inventory management and planning. It will also help businesses catch and correct errors quickly.
43. Use Lean Inventory Strategies
Lean inventory management means workers spend less time looking for products and are more productive when picking up or preparing orders. Lean inventory strategies also enhance a warehouse's ability to be more flexible. This includes stocking smaller quantities and less expensive items rather than too many slow-moving products.
Instead of planning supplier deliveries according to the expected demand over the next three months, it may be better to arrange three separate shipments each month, with volumes adjusted in response to market conditions and customer demand.
44. Prioritize The Replenishment of Frequently Ordered Items
A company's stock of the most popular products can quickly run out during busy or peak seasons. This happens because workers are picking the items. Warehouse managers must be proactive and ensure these areas are stocked to avoid downtime or stoppages. They might schedule shifts solely focused on replenishment, depending on the demand.
45. Keep Track of Inventory Errors
In a complex warehouse environment, errors are almost inevitable. A small item might be lost or damaged during picks. It is important to track inventory errors and learn from them to avoid them in the future. This is vital for retailers who want to retain customers and ensure their inventory meets customer expectations.
46. Use DeadStock to Make New Products
Deadstock, the inventory a company doesn't expect to sell, can be costly. Businesses can eliminate dead stock without having to pay the steep price. They can offer it as a gift, bundle it with complementary products, or partner with other companies to get it offloaded at a lower price.
47. Training Staff on Policies and Procedures
Warehouses are only as efficient and well-organized as the people who work there. Employees need to be trained to learn the procedures and use warehouse technology. This will help them appreciate the organization's value. People will see warehouse management as an opportunity to grow and learn, not a requirement for compliance.
48. Keep Up-to-Date With Staff Training
Training shouldn't be a one-and-done job. Regular training and upskilling are key to warehouse workers' safety and ability to use the latest tools, machinery, and technologies. Although there is no set frequency, staff must be trained in new technologies and tools before they can be used. Staff should also undergo regular refresher courses to maintain best practices.
49. Set Benchmarks
Setting warehouse goals is possible by setting benchmarks. Warehouse managers and employees can push beyond their limits by pursuing best practices. Instead of trying to increase efficiency by 10%, warehouse managers and their teams might set a record for shipment volume in a quarter. This will motivate staff members and encourage continuous improvement.
50. Incentivize Staff
Warehouse success is based on speed and efficiency. Motivated employees are key to both. Employee productivity is improved by offering incentives and rewards. It is possible to offer bonuses to encourage workers in pick-and-pack areas that see high traffic and need to operate smoothly. This can increase activity and foster healthy competition among colleagues.
51. Enhance Staff Comfort
High-intensity warehouses are prone to burnout and exhaustion. It is up to the business how to prevent this from happening. Every warehouse should have a rest area and a kitchen. Fans and air conditioning systems are a great way to make your work environment more comfortable in areas where temperatures can rise rapidly.
Last Thoughts
Warehouse Inventory Management does not have to be a constant cycle of picking up, packing, and shipping. It can be quite refreshing to take the time to organize your warehouse daily. With the right tools, employees will be more productive, product picks can be faster, and operations can run smoothly. Don't delay; take action today to improve warehouse inventory management!