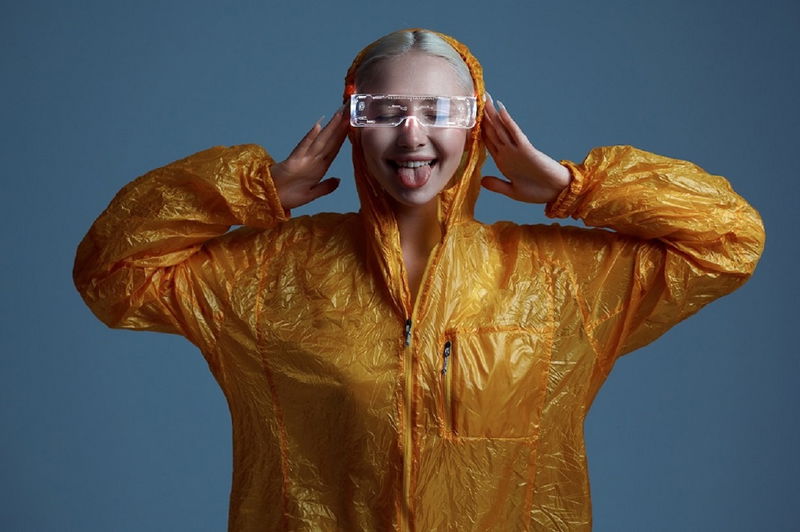
Recently, facility managers have sought new Maintenance Management practices to reduce operating costs. According to estimates by industry professionals, maintenance expenses account for 15-40% of production expenses; which makes sense considering equipment is often operated continuously or at long intervals to optimize production - without properly prolonging equipment lifespan, companies would find it challenging to operate profitably and remain profitable.
This guide will delve into maintenance management. Maintenance is an integral component of doing business that must consider several factors, which this post intends to discuss in more depth. Precisely, it will discuss what maintenance management entails as a practice and why it is essential, as well as ways companies can establish roles, responsibilities and procedures that maximize asset performance.
Maintenance management is an essential element of business that relies on machinery and equipment for daily operation. Mastering its fundamentals will allow you to maximize asset lifespan, reduce Downtime, ensure efficiency, and reduce cost. This beginner-friendly guide covers both the ABCs and critical concepts of maintenance management.
What Is Maintenance Management?
Maintenance management provides order and structure to the planning, scheduling, completion and monitoring of work related to maintaining equipment. Maintenance requires more than simply working directly on equipment - it requires comprehensive processes and controls to track work orders correctly for care and other activities. Suited software/hardware combination solutions must also be employed to monitor work orders for maintenance activities effectively.
Asset barcodes and scanners are an efficient way to increase productivity in any facility or office environment. Many organizations rely on computerized Management Information Systems (CMMS), which centralize their operations for better, streamlined performance. However, Enterprise Asset Management platforms (EAM) with similar features can also track maintenance management.
Maintenance management encompasses various processes and strategies designed to preserve, repair and optimize assets within an organization, including equipment and facilities. Maintenance management plays a crucial role in maintaining productivity and minimizing Downtime; more than simply fixing broken things, it involves taking proactive measures before problems emerge and responding promptly and appropriately to unexpected obstacles.
Maintenance management aims to maximize asset performance and reliability. A preventive maintenance approach relies on regular equipment inspection, service, and upkeep visits to avoid potential failures and disruptions that could otherwise disrupt productivity or disrupt operations, thus increasing productivity while decreasing operational Downtime. A regular schedule for preventive maintenance inspection can reduce unexpected breakdowns while increasing productivity while decreasing Downtime significantly.
Reactive maintenance, while not ideal, remains an integral component of equipment maintenance. Reactive maintenance entails quickly addressing unexpected failures or breakdowns to return the equipment into complete functioning order speedily and at a minimal expense; although such efforts may result in shorter downtime periods; often, this form of service becomes much more costly as its effects undermine overall efficiency and the impact on efficiency is further compounded over time. Ideally, however, preventive measures aim at decreasing reactive maintenance by mitigating unpredictable events altogether.
Technology's impact on maintenance management has seen dramatic advancement in recent years. Computerized Maintenance Management Systems, or CMMS for short, provide organizations with software platforms for automating their maintenance processes and tracking assets such as work orders or scheduled maintenance tasks more easily while monitoring equipment performance data relating to equipment performance analytics - helping companies optimize maintenance schedules while efficiently allocating resources.
Maintenance management applies not just to assets but also includes people. Trained maintenance employees that can complete maintenance safely and effectively are critical components of successful maintenance management programs, so investing in their training and creating a culture of continuous improvement is vital for long-term success.
As a multifaceted discipline, maintenance management ensures an organization's equipment, assets, and buildings run seamlessly. Implementing preventive maintenance plans using technology like CMMS while prioritizing employee expertise are among the many practices within maintenance management that help minimize disruptions in operations while increasing asset lifespan and improving efficiency - paying dividends through improved productivity, reduced costs and enhanced overall performance.
Maintenance Management: Why Is It Important?
Maintenance management in any organization, which relies heavily on assets and equipment for its operations, must be balanced. Maintenance managers play an invaluable role in ensuring reliability, longevity, efficiency and productivity of critical resources - something vitally important across industries, sectors, businesses and enterprises of every stripe and type - including manufacturing plants, infrastructure assets and any other related operations that rely on reliable assets or equipment for smooth functioning and success.
Maintenance management is critical in minimizing Downtime. Unplanned equipment failures can cost the organization dearly by forcing production stops, service delays, and reduced productivity. Implementing an organized maintenance plan enables organizations to identify any minor issues before they become major ones - helping maintain operational continuity while also helping prevent unscheduled failures from occurring unexpectedly.
Maintenance management is vitally important from both financial and logistical perspectives. Reactive maintenance may sometimes be required; however, its costs can quickly spiral out of control with emergency repairs, parts replacement needs and overtime hours needed for work planned ahead of time. Preventive maintenance is essential in controlling costs by scheduling maintenance during Downtime - helping minimize unexpected failure impacts on resources.
Maintenance management plays an instrumental role in prolonging asset lifespan. Regular inspection, cleaning and maintenance help avoid damage to equipment so it runs more efficiently for longer. In turn, this saves on replacement expenses while increasing return on investments.
Safety should also be prioritized during maintenance management; improperly maintained equipment poses severe threats to employees, clients and the surrounding community. Undergoing safety inspections is part of effective maintenance management and serves to ensure equipment conforms with regulations while not endangering those working on it.
Maintenance management is a technology-enabled discipline that takes full advantage of today's data-driven world. Computerized Maintenance Management Systems, or CMMS for short, allow organizations to monitor and coordinate all maintenance activities systematically with automated tracking capabilities resulting in seamless workflow management with optimized task distribution and data analyses to inform future strategies to increase efficiency and performance.
Maintenance management is essential to customer satisfaction and reputation management, leading to more consistent service or product delivery and building customer loyalty. Reliable organizations with high-quality offerings tend to retain and attract more clients.
Maintenance management cannot be underestimated: its role is central to operational stability, efficiency, safety and customer satisfaction. By actively meeting their maintenance requirements, companies can better position themselves for sustained success while creating resilience within their markets and developing an edge against rival businesses.
Implemented correctly, maintenance management programs can bring numerous advantages to any business. This system must remain organized and current, as many organizations possess hundreds or thousands of assets. Here are just a few ways maintenance management programs may prove valuable:
Optimize Performance. With proper equipment maintenance management, adopting a proactive approach rather than only responding to emergencies or repairs becomes much more straightforward. A centralized platform gives an entire team control over every operation, speeds things up faster, makes detecting problems more detailed, and improves upon them more readily.
You are reducing Downtime. Maintenance management must consider all product lifecycle stages when planning maintenance programs, making upgrading easier when understanding how aging affects performance. By employing multiple maintenance techniques simultaneously, you can extend equipment uptime.
Unplanned repairs can be expensive and cause production delays and other issues, so managing maintenance in an organized manner helps control costs such as overtime, spares and labor. Better planning allows maximum space utilization while optimizing stock levels.
Safety Enhancement. Businesses are subject to multiple state and federal laws and regulations set by the U.S. Occupational Safety and Health Administration. Hence, maintenance management helps companies comply with audits or reviews from regulators or auditors while simultaneously contributing to operator safety by centralizing information such as warranties or services available through them. A properly maintained machine also contributes directly towards operator protection.
Failing to make sound maintenance and equipment upkeep decisions may lead to failure or safety incidents, making asset lifecycle planning challenging for large industrial equipment or complex systems. Maintenance management systems provide tools for reporting quality data and enhancing asset management decision-making processes.
Read Also: Important Features To Have In An Effective Maintenance Management Software
What Is Maintenance Management?
Maintenance management is pivotal in organizations' growth, success and sustainability across industries. Maintenance goes beyond simple equipment upkeep - its scope extends beyond simple equipment upkeep to encompass resource optimization, risk mitigation strategies and operational excellence initiatives.
Maintenance management's primary objective is to preserve asset availability and reliability. Any downtime caused by equipment can result in production stops, service disruptions and financial losses for organizations. Preventive maintenance helps organizations detect any emerging problems early and resolve them before becoming significant issues; in doing so, interruptions and lifespan extensions become far fewer, while operational efficiency also improves significantly.
Cost control is another essential aspect of maintenance management. Reactive maintenance (also referred to as reactive repair) often incurs high repair costs and unexpected expenses while increasing Downtime, while planned maintenance allows companies to plan tasks during Downtime, better managing resources and mitigating financial impacts caused by unexpected failures.
Management of maintenance can also decrease risks and enhance safety. When equipment is maintained appropriately, its likelihood of malfunction decreases drastically, reducing risks such as accidents and creating a safer working environment for all involved. Effective maintenance management practices involve regular safety inspections and compliance with industry standards for maximum effectiveness and cost reduction.
Maintenance management can play an essential role in environmental sustainability. Equipment with proper care and maintenance uses fewer resources while producing fewer emissions - thus decreasing an organization's ecological footprint while saving money through reduced energy use.
Technology plays an integral part in managing maintenance in today's digital environment. Computerized Maintenance Management Systems and predictive analytics allow organizations to make more informed decisions, optimize maintenance schedules and allocate resources more effectively while streamlining processes and including data.
Maintenance management encompasses much more than mechanical repairs: this function ensures asset reliability, reduces Downtime and costs, enhances safety performance and promotes sustainable operations for an organization to gain a competitive edge, boost customer satisfaction and achieve long-term business success. By investing in maintenance, organizations can earn a competitive advantage, enhance customer experience and ensure long-term business success.
Maintenance Management involves performing repairs on equipment or performing services for an organization. Still, it must include more tasks to be genuinely effective. A computerized maintenance system and Enterprise Asset Management platform may help combine several workflows into an effective maintenance program; additionally, its role must cover several key areas within an organization, such as those detailed below.
Asset Management. Asset management serves as an intersection point between CMMS platforms and EAM solutions. It must include accurate databases which include all assets adequately labeled. Doing this allows work to be scheduled accordingly while saving companies money through asset assessments by eliminating unused equipment or surplus supplies.
Inventory management. Inventory includes raw materials, packaged products, equipment and parts - any business that deals with goods must maintain an organized warehouse with accurate inventory cycle counts to succeed in this business. Inventory management systems can help companies meet this need efficiently by controlling spare part inventories and assets needed for performing maintenance duties on equipment or support required for running repairs and upkeep.
Maintenance Work Order Management. A key feature of software for maintenance management is organizing work orders. A large team of field technicians who operate remotely requires an effective way to assign, complete and schedule maintenance tasks that reduce Downtime and errors while keeping everyone organized and productive. A central system to do just this helps the entire team stay on track without losing momentum due to Downtime and mistakes.
Facility management. Buildings require maintenance to keep visitors and employees safe in a work environment. At the same time, equipment like HVAC systems, chillers and data centers must also be regularly serviced for peak operation. Facilities managers need to use maintenance management as an instrument of control by ensuring service plans correspond with usage patterns and scheduling regular servicing accordingly.
Reporting and Metrics. Experienced managers understand that reviewing high-quality data is critical to effective decision-making processes; asset and maintenance management is no exception, where examining maintenance data may help improve budget balance and department transparency. Companies may also enhance cost projections through better equipment data allowing for simultaneous examination of various aspects of operation, including costs associated with facility overheads and maintenance resources - among many other data points to consider.
Maintenance management is an intricate system in which several functions must operate simultaneously for successful performance. While specific roles may change based on an organization's structure and goals, work processes follow similar patterns. Achieving success through maintenance management programs requires collaboration among resources and transparency between them all.
Read Also: Quick Overview of a Efficient Maintenance Management System
Different Types Of Maintenance Management
Companies across industries continually find innovative and cost-cutting strategies to maximize equipment performance. Multiple maintenance types may need to be combined simultaneously to get maximum use out of one tool; only some devices may suit all forms of upkeep - and in this section, we'll outline which factors to keep in mind before choosing tools as maintenance partners.
Maintenance management encompasses an umbrella term encompassing various approaches and strategies designed to meet an organization's unique requirements and goals. Maintenance management types may include:
Reactive Maintenance. Reactive maintenance refers to any work carried out when visible indicators indicate service is needed. For instance, visual inspections or other hands might show this need. It's typically managed through periodic auditing or inspection programs, and it can be beneficial with parts with unknown lifetimes due to factors like usage. Reactive maintenance also covers sudden failure repairs as required. For instance, a sudden power outage would need emergency work performed immediately in this scenario.
Preventive Maintenance. In order to anticipate potential failure points and service needs accurately, pre planning is critical. You can use various factors, including time and operating hours, to establish when service should occur. While proactive maintenance may seem ideal in theory, it can quickly turn into extra work that doesn't benefit an optimal operation if conducted without properly inspecting and using multiple data sources to optimize service plans - preventive and predictive maintenance fall under this heading.
She timed Preventive Maintenance. Preventive maintenance should be scheduled around time triggers; each piece of machinery's schedule usually depends on usage and wear patterns. Furthermore, timed preventative maintenance also involves monitoring consumable life expectancies to replace parts as quickly as possible without losing operational time.
Predictive Maintenance. Predictive or condition-based maintenance (often known by its initials: condition-based or predictive maintenance) is a relatively newer form of maintenance that uses sensors and inline monitors to collect data about equipment operation to control it, then uses this data to establish when maintenance activities must occur. Due to the considerable investment in hardware and software components for predictive maintenance activities, its usage should generally be reserved for equipment with a higher risk of breakdown, which is costly or requires regular monitoring activities for preventative purposes.
Maintenance management offers many advantages for every asset, one major one being keeping track of service histories and activities for everyone. Doing this allows a more manageable selection of maintenance types and opportunities for continuous improvement - an iterative approach is recommended when planning maintenance activities.
Each maintenance management approach offers its own advantages and disadvantages; organizations often combine different kinds to develop an overall maintenance strategy tailored to their objectives, available resources and operational needs.
What Makes A Good Maintenance Supervisor?
Maintenance managers require an amalgam of leadership, technical, and communication abilities to oversee an organization's maintenance activities. A good maintenance manager must possess an in-depth knowledge of equipment systems, processes and maintenance practices they control, allowing them to make well-informed decisions, diagnose any potential problems accurately and direct their maintenance teams effectively.
Leadership skills for maintenance managers are also paramount; those that possess them should have no difficulty motivating and leading their teams while creating an atmosphere of accountability, teamwork and continuous improvement. Maintenance managers with extraordinary abilities in this regard set clear expectations with delegated tasks while offering guidance as required and motivating team members effectively. These abilities are vital components to smooth maintenance operations.
Successful maintenance managers possess exceptional communication skills. Interdepartmental communication and higher management meetings require excellent verbal skills; effective verbalization will allow goals, tasks and priorities to be understood while decreasing chances of miscommunication which could cause errors. A maintenance manager must also communicate technical data that non-technical people can comprehend effectively to enable decision-making and resource allocation more easily.
Another critical characteristic is adaptability. Maintenance operations are frequently unpredictable due to shifting priorities and unexpected obstacles; successful managers must remain calm under pressure while adapting quickly to changing conditions.
An effective maintenance manager takes a proactive approach. They anticipate issues before reacting to them, optimize schedules and allocate resources efficiently. This approach reduces cost while improving operational efficiency, decreasing Downtime, and decreasing operational expenditures.
An effective maintenance manager combines technical proficiency, strong leadership, flexibility and adaptability with strategic thinking to lead teams and maintain equipment reliability. Their skills also enable them to contribute towards an organization's overall success by streamlining operations while optimizing resources efficiently and continuously improving processes and practices.
Maintenance managers play an essential role in connecting maintenance directors or top executives with supervisors and techs that perform most service work. It requires technical and business skills to see big-picture needs and day-to-day demands effectively. For better insight, let's examine some essential skills required of an effective maintenance manager.
Due to the complexity of maintenance activities carried out by many businesses, a Maintenance Manager must perform many duties that vary in scope and focus. Here are some areas they should prioritize for consideration in this position:
- Maintenance-Related Work Coordination of maintenance-related activities to meet regulatory requirements
- Maintain a suitable spare parts stock. Manage service technicians, other employees, and staff. Implement an extensive maintenance program.
- Reporting Effective Maintenance Activities
- Increase Asset Productivity Sufficient Staff Training Should be Provided.
Maintenance managers can be many things. Additionally, there are some parallels between their duties and those of an asset or facilities manager. Managers of maintenance are expected to possess a variety of hard and soft abilities. The most common include.
Time management skills must take precedence, adaptability and the ability to pivot quickly must also be an asset, communication abilities should also be strong while problem-solving and teamwork abilities need to be in place as part of a team effort, as is basic knowledge regarding relevant equipment.
Maintenance managers must reconcile company goals for performance with equipment limitations in a company, often the case with highly-specialized industries, like aerospace or healthcare, with many clients. An efficient maintenance manager requires having both technical and soft skills. Companies can create effective maintenance management programs through solid collaboration among many departments - technicians, operators and staff who interact directly with equipment should all have feedback for managers on this.
Many businesses have made maintenance management an integral component of their assets and management framework, using computerized Maintenance Management Systems (CMMS) to efficiently integrate various functions under a unified asset and management umbrella. Flexible platforms created by these CMMSs combine well with asset tags or scanners used for facility management to automate maintenance work orders; its future will depend on technological innovations and creativity in designing innovative processes to be deployed for maintenance management work orders.
Conclusion
Understanding the ABCs for effective maintenance management is the key to achieving operational excellence, cost-savings, and increased asset reliability within an organization. Asset Management is the foundation of any organization. It includes the tracking and evaluation assets, as well as their identification. The Best Practices guide the maintenance strategy, balancing preventive and proactive approaches to reduce Downtime and increase efficiency.
Computerized Maintenance Management Systems, or CMMS (C), are vital to modern maintenance management. They enable streamlined task management, data analysis and better decision-making. Data-Driven decision-making (D) provides managers with valuable insights from trends in equipment performance, maintenance histories, and predictive analytics. This allows them to fine-tune maintenance strategies.
Employee Engagement and Training (E) is the most critical aspect of maintenance management. It is essential to recognize the value of highly-skilled and motivated maintenance teams. Encouragement of open communication, continuous education and empowerment allows individuals to own their tasks. It fosters a culture that values proactive problem-solving and continual improvement.
Remember that as you begin your journey in maintenance management, these principles are interconnected and not isolated ideas. They form a strategy. Implementing Asset Management, using Best Practices and CMMS to make data-driven decisions, and fostering employee involvement and training, will equip you with the necessary tools for navigating the maintenance challenges effectively.
In a dynamic environment, learning and adaptability are essential. Your organization will remain at the forefront regarding asset reliability and operational efficiency if you regularly assess and adjust your approach based on industry trends, data and experience. Mastering ABCs for effective maintenance management will help you create a future where your company is resilient and prosperous. Maintenance becomes more than just a necessity.