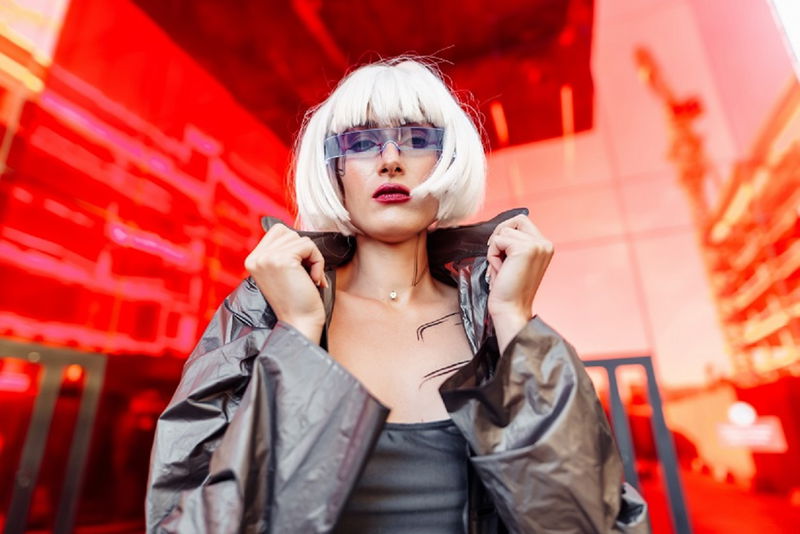
Manufacturers in today's dynamic and fiercely competitive business world face unique challenges that require efficient processes, adequate resource allocation, and real-time insights to stay afloat. One of the most transformational tools at their disposal for industry-specific Enterprise Resource Planning (ERP) software.
Enterprise Resource Planning (ERP) systems have emerged as indispensable tools for organizations looking to maximize productivity, reduce costs, and gain a competitive edge, but one size does not fit all; an all-encompassing ERP manufacturing may not satisfy manufacturing industry-specific needs; therefore, this blog explores industry-specific ERP solutions with particular attention paid towards how tailoring ERPs specifically to manufacturing can transform operations while driving sustainable growth over time.
Staying competitive and efficient in today's ever-evolving manufacturing landscape has never been more essential. Manufacturing industry sectors, including automakers, aerospace engineers, food processors, and electronics, all face unique obstacles and complexities; they increasingly rely on specialized tech solutions to face them head-on and exploit growth opportunities. We will delve into this world and show how tailoring ERP systems specifically to the manufacturing sector can revolutionize operations, drive sustainable growth, and help maintain a competitive edge for manufacturers.
From understanding the core functionalities of ERP systems to discussing manufacturing industry-specific challenges and exploring the benefits of tailored solutions, this comprehensive exploration into ERP customization will lead us to an in-depth exploration. By its conclusion, you will know intimately why Industry-Specific ERP Solutions have become such an essential element of modern manufacturing companies striving for excellence in an ever-evolving marketplace.
Understanding ERP Systems
Enterprise Resource Planning (ERP) systems are sophisticated software systems designed to streamline and optimize the management of various business functions within an organization. ERP has become essential in today's data-rich environment, providing one centralized platform connecting disparate departments and functions and facilitating seamless data sharing for efficient coordination. At the core of ERP for manufacturing industry is their comprehensive set of functions, typically including finance, human resources, supply chain management, production scheduling, and inventory control, customer relationship management (CRM) as well as inventory control - these functions are seamlessly integrated into one software system to eliminate data silos or redundant processes.
ERP systems' primary advantage lies in their capacity to centralize data. Instead of maintaining individual databases and spreadsheets for every department or function, all relevant information can be stored centrally - thus eliminating duplication risks and making data accessing, analysis, and reporting much more straightforward. ERP systems excel at automating and streamlining business processes. Routine tasks like order processing, payroll management, and financial reporting can all be automated for reduced manual effort and human errors, resulting in faster, more consistent processes across your organization. Real-time insights are one of the hallmarks of ERP systems, providing real-time updates on various aspects of the business to allow informed decision-making and quick problem-solving. Managers and executives can access essential data regarding sales levels, inventory levels, production progress, and financial performance for making timely and data-based decisions.
Customization is one of the primary strengths of ERP systems. While they provide an array of standard functionalities, ERPs can also be tailored specifically to an organization's requirements, such as configuring workflows or adding specific modules. They may even integrate seamlessly with other software systems for seamless operation. mEnterprise Resource Planning (ERP) systems play a vital role in modern business operations, providing a holistic and centralized method to oversee multiple functions within an organization's functions. Over the years, these systems have advanced significantly and now form the backbone for many enterprises. To gain more insight into ERPs' inner workings and functions, examine their essential components and functions in more detail.
ERP systems automate core business functions like accounting, human resources, supply chain management, production planning, and inventory control - providing seamless data sharing and improved organizational decision-making. At its heart lies an ERP system's core function - aiding with core functions like finance, human resources, supply chain management, production planning, inventory control, and customer relationship management (CRM). These functions come together seamlessly on one centralized platform at their best, allowing seamless information exchange among teams while supporting better decision-making across organizations.
Integration: ERP systems place great importance on integration. In traditional business operations, separate departments use separate software applications that do not communicate between themselves, leading to inefficiency, data discrepancies, and no real-time insight. By consolidating all functions into one centralized platform for ERPs, data flows smoothly between departments for greater accuracy and efficiency.
ERP systems' key advantage lies in data centralization: instead of maintaining multiple databases and spreadsheets for different functions, all relevant information is kept within one centralized repository, making access, analysis, and reporting on this data much more straightforward and decreasing duplication risk and errors. ERP systems are specifically designed to automate business processes. This means that repetitive tasks, like order processing, invoicing, and payroll, can be automated to reduce manual effort and human error - leading to faster and more consistent processes overall.
Real-Time Insights: ERP systems offer real-time visibility into an organization's operations, giving decision-makers immediate access to sales figures, inventory levels, production progress updates, and financial performance reports. Real-time insights allow quicker and more informed decision-making - helping organizations respond rapidly to changing market conditions and customer demands effectively.
Customization: While ERP solutions come equipped with many standard functionalities, they also feature highly customizable capabilities that enable organizations to tailor them specifically to fit their organization's unique requirements and industry norms. Customizing may involve configuring workflows or adding specific modules; other customization may involve developing integrations between ERP solutions and other software systems.
Scalability: ERP systems are tailored to evolve along with any organization they serve, adapting to increased data volumes, users, and business complexity as a business grows. To remain effective in long-term investments. Scalability is, therefore, vital.
Reporting and analytics: ERP systems offer robust reporting and analytics tools, allowing users to generate numerous reports and dashboards to gain an in-depth view of business performance. With such powerful tools, organizations can better identify trends, opportunities, or areas requiring special consideration.
ERPs, or enterprise resource planning (ERP), systems provide comprehensive software solutions that integrate and streamline an organization's core business functions, from data aggregation and automation through real-time insights and customization/scalability to real-time market adaptation and expansion. As businesses adapt their strategies to evolving market conditions, ERP solutions are vital in remaining agile in an increasingly volatile landscape.
Read more - Types And Features Of Manufacturing ERP Software
The Manufacturing Industry's Unique Challenges
Manufacturing industries are complex and dynamic entities that produce various goods ranging from cars and electronics to food and pharmaceuticals, creating many employment opportunities and confronting unique challenges that distinguish them from other sectors. It is vitally crucial for manufacturing firms to fully comprehend these obstacles to develop effective strategies and solutions to overcome them.
Complex Supply Chains: One of the primary obstacles to manufacturing lies in managing its intricate supply chains. Manufacturers frequently depend on multiple tiers of suppliers - domestic and international - for raw materials and components; managing this complicated web of relationships requires complex coordination efforts between domestic and foreign vendors; on-time deliveries must occur, and inventory levels must be managed effectively. Otherwise, delivery delays or shortages could severely affect production schedules and customer commitments.
Production Variability: Manufacturing encompasses many different products with unique production processes and requirements for mass or custom orders, necessitating manufacturers to adapt their operations in response to product lines or variations presenting unique production challenges and needs. Such variance can create complex challenges to production planning, resource allocation, and quality control efforts.
Quality Control: Manufacturers recognize the importance of adhering to high-quality standards when producing goods for sale, as subpar quality issues can lead to product recalls, customer dissatisfaction, and damage to their company's reputation. Manufacturers should implement stringent quality controls at each production stage to guarantee consistency with industry regulations and comply with industry standards and legislation.
Compliance Issues: Manufacturing industries must abide by various laws and standards ranging from safety regulations, environmental concerns, product certification requirements, or industry-specific guidelines. Assuring regulatory compliance is legally mandated and essential for building strong customer relations.
Global Competition: Manufacturing companies operate in an intensely competitive global environment. Competitors from all corners must compete while maintaining quality, cutting costs, and remaining cost-competitive. Remaining on top requires constant innovation, efficient operations, and a continued focus on meeting customer demands - the three cornerstones of staying profitable today and tomorrow.
Adopting Technology: Rapid technological innovations like automation, robotics, and the Internet of Things (IoT) are revolutionizing manufacturing. While adopting these technologies may bring increased efficiencies and productivity benefits, their implementation often comes at significant expense and necessitates significant alterations to processes and worker skills.
Workforce Management: Skilled labor is essential to manufacturing. Attracting, training, and retaining talented personnel remains a continuous challenge as technology changes the industry landscape. Successful workforce management strategies that address skills gaps while simultaneously encouraging employee engagement should be prioritized as vital strategies.
Sustainable practices in manufacturing: Manufacturers face increasing pressure to operate sustainably and reduce their environmental footprint, including by cutting waste production, energy use, and emissions. Sustainable practices are not just moral imperatives; consumers and regulatory authorities increasingly demand eco-friendly products and processes.
The manufacturing industry is distinguished by its complexity, diversity, and unique challenges. Effectively managing complex supply chains, accommodating production variability, meeting quality standards while adhering to regulations, and competing globally as a manufacturer can all present distinct hurdles requiring strategic planning, technology adoption, workforce development programs, and commitment towards sustainability as a solution.
Benefits Of Industry-Specific ERP Solutions For Manufacturing
Industry-specific ERP (Enterprise Resource Planning) solutions tailored for manufacturing offer many advantages over generic systems in terms of meeting industry-specific challenges and business goals. Such custom ERPs have proven invaluable when explicitly applied to this sector's particular challenges and requirements; such benefits have an incredible positive effect on the efficiency and profitability of manufacturing businesses.
Industry-Specific ERP Solutions Offer Enhanced Efficiency: Industry-specific ERP solutions can streamline manufacturing processes. By streamlining resource allocation, production scheduling, inventory control, and automation process optimization, manual intervention reduces production downtime while improving overall operational efficiency, resulting in cost savings and enhanced productivity, resulting in cost reduction and efficiency resulting in cost savings and productivity increases.
Real-Time Insights: ERP system for manufacturing industry offer real-time data and insights into all facets of production, such as production progress, inventory levels, and equipment performance. With real-time insights, businesses are better prepared to quickly adapt to market changes or production issues as soon as they arise.
Cost Control: ERP solutions tailored for manufacturers provide accurate cost controls by automating processes, optimizing resource allocations, reducing errors, and eliminating wasteful practices, thus providing improved cost management that ultimately increases profits and drives more profit for them. Manufacturers can take advantage of tailoring ERP systems specifically for cost reduction by finding opportunities, eliminating wasteful practices, or allocating resources more effectively - ultimately increasing profit and their ROI.
Quality Assurance: Manufacturing quality control is of utmost importance, so industry-specific ERP solutions must include modules to monitor and oversee quality at every step of production. This helps identify quality issues quickly to limit defective products, recalls, and customer dissatisfaction - ultimately increasing customer loyalty by consistently producing products of higher quality.
Scalability: Manufacturing businesses looking to grow or diversify their product lines need ERP systems that adapt to changing requirements, accommodating increased production capacity and complexity over time. Industry-specific ERP solutions have been tailored specifically for manufacturing businesses to keep pace with business development by accommodating increased scalability, ensuring long-term benefits from investing in such an asset.
Compliance monitoring and reporting features: Manufacturing companies must abide by numerous industry-specific regulations. ERP solutions often feature compliance monitoring and reporting features designed to assist manufacturers with adhering to these laws - decreasing acceptable risks, improving corporate responsibility, and strengthening reputation.
Supply Chain Management: Manufacturing-specific ERP systems excel at managing complex supply chains. Their tools offer solutions to track raw materials, components, and finished goods through every stage - from procurement to delivery - for improved visibility, shorter lead times, and reduced disruption risks in supply chains.
Customization: Industry-specific ERP solutions offer manufacturers many customization options that enable them to tailor the system to their manufacturing processes and needs. This may involve configuring workflows, adding modules (for handling variants, for instance), or connecting other manufacturing technologies - everything necessary to create an ERP system that fits seamlessly within the unique processes of each manufacturing business.
Industry-specific ERP solutions provide essential benefits for the manufacturing sector, from optimizing efficiency to real-time insights, cost control, quality improvement, regulatory compliance, supply chain management, and managing complex supply chains. Their scalability and customization options make these powerful tools indispensable in an increasingly competitive and evolving industry environment. Manufacturers can achieve sustainable growth by investing in one while remaining ahead in global marketplace competition.
Selecting The Right Industry-Specific ERP Solution
Selecting an Industry-Specific Enterprise Resource Planning (ERP) system for your manufacturing business can dramatically impact its efficiency, profitability, and competitive edge. To make an informed selection process, you must consider several critical criteria to select an ERP system that best meets your manufacturing enterprise's unique requirements and goals.
Industry Expertise: Search for ERP vendors with an in-depth understanding of manufacturing. Experience and knowledge specific to your manufacturing industry (i.e., automotive, aerospace, or food processing) are invaluable; vendors who understand its challenges and requirements are more likely to provide tailored solutions tailored to fit.
Customization: In manufacturing, one size only sometimes fits all. Evaluate your ERP system's flexibility and customization capabilities as a critical consideration; tailor it precisely to match your processes, workflows, and business rules to adapt to current operations and growth plans for optimal success.
Integration Capabilities: Your ERP system should integrate smoothly into the software and hardware infrastructure in which it exists, including manufacturing equipment, Internet of Things devices (IoT) devices, and any software systems you are already utilizing. Successful integration ensures smooth data flows as well as minimizes disruption during implementation.
Scalability: Manufacturing businesses evolve. Therefore, any ERP solution chosen should be flexible enough to adapt to them as your company expands, production volumes change, or more complex requirements arise. Furthermore, it should support expanding into new product lines or markets without requiring an extensive system overhaul.
Support and training: When considering which ERP vendor is right for your organization, take note of their level of support and training offerings. Implementation and ongoing system maintenance can be complex, so having reliable assistance during installation and ongoing system upkeep is paramount. Ensure they offer comprehensive training programs and customer service that swiftly responds to any issues or queries.
Total cost of ownership (tco): To accurately budget and evaluate the return on Investment of ERP system investment, assess TCO over its lifespan. This should encompass licensing costs and implementation, customization, maintenance, and upgrade expenses. Gaining insight into TCO will allow for accurate budgeting and return on Investment (ROI) assessment.
Usability of erp: Usability is significant; an ERP system should be easy for employees to navigate to encourage widespread adoption among your staff and maximize effectiveness. A complicated or hard-to-navigate system could cause employee resistance and reduce its efficacy significantly.
Referrals and case studies: Research the ERP vendor by reviewing customer references and case studies from manufacturing businesses implementing its ERP solutions to gain valuable real-world perspectives of its performance. Speak with other manufacturing businesses implementing similar ERPs to gain insight into the experience, outcomes, benefits, etc., of using such solutions in business environments. This information could provide vital real-world perspectives into its operation.
Compliance and security: Be sure that the ERP system you select complies with industry-specific regulations and security standards, particularly with manufacturing, where sensitive data, trade secrets, and proprietary processes must remain protected at all costs. Make sure it offers robust features to safeguard this sensitive data.
Future Proofing: Evaluate how easily an ERP solution will adapt to future technological innovations and industry trends, such as artificial intelligence, machine learning, and data analytics, keeping manufacturing operations competitive in today's environment. The software should be built to work alongside these emerging technologies - keeping pace with them will keep operations profitable!
Selecting an industry-specific ERP solution for your manufacturing company requires careful thought. By carefully considering factors like expertise in your sector of operation, customization options, integration capabilities, scalability, support costs, user-friendliness, references compliance, and future-proofing, you can make an informed choice that supports both your goals and is future-proof against an ever-evolving manufacturing landscape.
Related article - What is Manufacturing ERP? Everything You Need To Know
Real-World Case Studies
Real-world case studies provide invaluable insights into the practical advantages and results of adopting tailored ERP systems in manufacturing businesses. Let's look at several examples that showcase how these bespoke systems have impacted manufacturing enterprises' operations, efficiency, and profits.
Automotive Manufacturing
An auto manufacturer was experiencing production delays, quality issues, and supply chain inefficiencies that hampered productivity. They sought an industry-specific ERP system tailored to automotive manufacturing to streamline production processes while improving real-time monitoring of quality controls for real-time monitoring of quality standards as well as supply chain management - the results being an upsurge in production efficiency of 30% with defect rates decreasing by 20% while realizing significant cost savings that led to enhanced customer service satisfaction and market expansion.
Aerospace Industry
One aerospace manufacturing company sought a tailor-made ERP system tailored explicitly for aerospace manufacturing compliance that could meet stringent regulatory demands while upholding high-quality standards, helping track complex paperwork management needs while optimizing erp in production scheduling and lead time reduction by 25% - as a result of which, they met all industry-specific regulatory demands successfully and expanded customer bases significantly.
Food Processing
One food processing company faced supply chain difficulties, increased food safety regulations, and the desire to minimize food waste. They implemented a custom ERP system explicitly tailored for food industry use. It enabled them to optimize their supply chain performance, reduce inventory waste through better inventory control practices, ensure compliance with food safety laws, increase profitability, and strengthen competitive standing within their market.
These improvements led them towards enhanced profits, enhanced traceability of products, and a more decisive competitive edge - leading them to increased profits, enhanced product backbone, and a more substantial overall market presence. These real-world case studies illustrate the tangible advantages of industry-specific ERP solutions in manufacturing. Such systems go beyond generic ERP software by meeting each industry's distinct challenges and requirements - leading to increased efficiency, better quality control, better cost management, and regulatory compliance - among many others. Such success stories underscore how selecting an industry-specific solution that aligns with company goals and needs can drive sustainable growth while driving sustainable competitive advantage for any manufacturing business.
Want More Information About Our Services? Talk to Our Consultants!
Conclusion
Industry-specific ERP solutions tailored for manufacturing are an integral development in business technology, providing numerous advantages that directly address manufacturers' unique challenges. Within this blog post, we explored these benefits in more depth; these range from increased productivity and real-time insights to cost control measures that improve quality control and regulatory compliance measures. Manufacturers investing in ERP solutions gain an edge in an ever-evolving global marketplace by taking advantage of these tailored ERP systems' seamless integration, scalability, and customization features and adapting seamlessly to changing circumstances like production shifts or technological innovations while meeting industry standards adaptably.
Real-world case studies discussed in this blog highlight the significant impact of industry-specific ERP solutions on manufacturing businesses. Their success stories show how industry-specific solutions have helped overcome challenges, boost efficiency, and realize significant cost savings - in sectors as diverse as automotive manufacturing, aerospace, aerospace, or food processing. Industry-specific ERP has genuinely proven its worth! Finding an ERP solution should be treated as a strategic decision that should consider factors like industry knowledge, customization capabilities, integration capabilities, scalability capabilities, support needs, total cost of ownership costs, user-friendliness, and future-proofing features. By doing so, manufacturers can increase sustainable growth and position themselves for long-term success.
As technology develops, manufacturers who take advantage of industry-specific ERP solutions will become better prepared to navigate the complexities of manufacturing environments, meet customer demands, and maintain competitive advantages. Such systems enable manufacturers to streamline operations, make informed decisions, and achieve maximum efficiency and quality to contribute towards continued industry expansion and success.