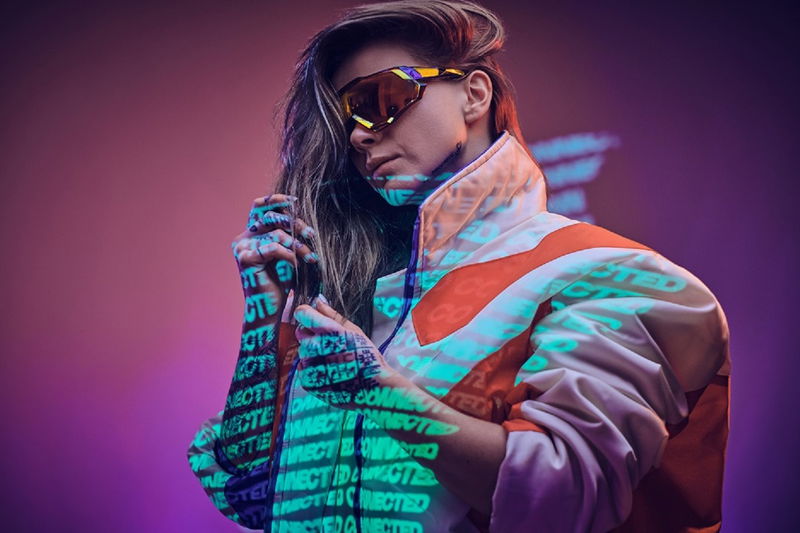
Lean inventory management involves controlling labor and time by continuously improving production processes, eliminating waste in material handling operations and increasing value within an organization's stockpiles. Manufacturers traditionally used demand forecasting before initiating lean inventory management strategies or created items based on what consumers expected would be desired (which might then become part of poor inventory management's mission statement).
Lean inventory allows manufacturers to keep only what they require within an allocated time while eliminating excess stock from their shelves.
What Is Lean Inventory Management?
The term "lean inventory management" refers to an inventory planning method that tries to eliminate waste and inefficiencies from production process and workspaces. Improvement opportunities can take the form of teaching staff members how to follow a strict first-in, first-out policy to reduce the loss of perishable items or eliminating production bottlenecks that increase the cost of storing inventory that is still being worked on. Businesses that understand lean inventory management systems only retain what is required at each stage of manufacturing, saving them time, money, and energy.
The Five Main Ideas Of Lean Inventory Control
Companies can achieve lean inventory management by employing five fundamental key principles.
Value
Under the five Lean approach, value refers to what customers desire and are willing to pay for. When managing inventory, businesses must factor in customer demand when deciding how much and what kind of goods to stock. Actual Demand planning - a cross-functional process that helps companies provide customers with what they want while minimizing excess inventory or dead supplies plays a pivotal role here.
Flow
Business process must understand organizational inventory flows to implement lean inventory techniques effectively. Three questions posed during materials requirements planning (MRP) practice determine its flow: "What, How Much, and When Does it Require Production." These responses drive production schedules accordingly.
Pull
Just-in-time (JIT) inventory management relies heavily on pull systems, where things are produced only as needed and in sufficient amounts. Push systems rely heavily on prior sales data for production forecasting purposes, while pull systems naturally emerge through flow processes.
Responsiveness
Responsiveness allows companies to quickly adjust to changing circumstances while lowering carrying costs. Reactivity can be increased through best practices in inventory management, such as ABC analysis, actual customer demand forecasting and Economic Order Quantity (EOQ).
Perfection
Lean technique can be best explained as striving for perfection in manufacturing process, inventory control or otherwise. Companies move closer to their ideal state when implementing changes that increase quality while eliminating wasteful practices that reduce inefficiency.
Effective Inventory Management Techniques
Make sure that your business can successfully implement lean inventory management techniques by considering these recommended practices:
Continue To Keep Precise Inventory Counts
With the correct inventory management system, this is very achievable. Moreover, you'll reduce stock outs, costing a normal shop up to 4% of total sales.
Put Cycle Counting Into Practice
Maintaining an inventory count helps reduce the waste caused by carrying excess goods by matching purchase orders to numbers in inventory. Furthermore, regular inventory counts provide early warning of theft or loss incidents and aid in their detection.
Partnerships With Suppliers
Maintaining adaptable partnerships with suppliers is key to keeping operations uninterrupted. Supply chain efficiency that enables smooth business functions by encouraging an interdependent view of planning, manufacturing and delivery can help companies keep regular operations moving smoothly.
Maintain Adequate Safety Stock
Maintaining sufficient buffer stock on hand will allow your business to avoid charging extra for expedited orders or informing clients their items have been back-ordered.
Lean Inventory Management Can Benefit Your Business
Here are a few benefits of Lean Inventory Management techniques for your business-
Increased Earnings
By decreasing out-of-stocks that frustrate customers and damage future sales, lean inventory management processes can significantly reduce holding costs while minimizing losses from spoiling, dead stock, and obsolescence.
Reduce Waste
By only moving efficient inventory management processes upon customer request, you reduce the chance of damage or harm, eliminating unnecessary movement of people, equipment and materials.
Producing Higher-Quality Products
Reducing flaws or reworks leads to higher product quality, decreased return/rework expenses, and happier customers.
Reduced Lead Times
Customer satisfaction increases as production moves faster and shipments reach customers sooner, while you can respond more rapidly to changes in demand.
Change In Stock
Increased inventory turnover reduces carrying costs, eliminates spoilage and obsolescence risks, and frees warehouse space.
Utilizing Sustainable And Eco-Friendly Business Methods
Sustainable methods help lower your carbon footprint and appeal to customers seeking eco-friendly goods. You could go paperless by eliminating packaging slips, pick tickets, and other documents through lean concepts.
Increases Staff Morale
Lean principles can transform your workplace culture to encourage continuous improvement; all teams and employees will have clearly defined roles that contribute value to the entire organization.
Also Read: Maximizing Efficiency: Top Warehouse Inventory Management Tips for Your Business
Lean Inventory Management Practices Qualities And Benefits
Six key components are necessary for developing and maintaining a lean inventory management principles:
Planning For Demand
Businesses provide inventory to their customers upon purchase, requiring sophisticated inventory forecasting techniques using past, present, and future event data to ensure enough stock to satisfy anticipated client demands.
Interorganizational Cooperation
Information availability and collaboration culture are critical factors here. To stay up-to-date with forecasts, teams require instantaneous access to real-time data from ERP, CRM, sales platforms or any other source.
Reducing Costs And Waste
One of the main motivations is to cut waste and costs as far as possible without diminishing customer value; our aim should be to provide high service levels while offering cost-cutting alternatives.
Standardization Of Processes
Employees waste less time, while firms increase repeatability, reduce errors, and find automation opportunities more quickly when they optimize and standardized work processes. A clear work procedure increases the chances of consistent adherence while aiding training efforts.
Standardization In The Industry
Reducing internal processes only goes so far; businesses must balance keeping proprietary processes alive while using components and procedures that meet industry standards. An automobile company using standard tyre sizes while customizing their rim design would exemplify this principle at work.
Shift In Culture
Research suggests that when lean culture is implemented effectively, employee engagement increases, and the culture improves. Employees who take pride in managing processes are more committed to further improvements over time.
Five Strategies To Foster Lean Inventory Management At Work
Assign Authority
Employees are motivated to participate in continuous improvement initiatives when they see upward mobility within the organization, are allocated appropriate responsibilities within their sphere of control, and know their ideas will be recognised and implemented.
Reevaluate Collaborative Projects
Negotiate supplier agreements that take a proactive approach to lead times, planning cycles and inventory ownership, especially in industries with high demand levels. Cooperative trade partner practices can greatly contribute to improving efficient inventory management.
Accept Metrics
What cannot be measured or managed without measures is unmanageable. Businesses that employ data-driven management instead of "feeling-based" approaches are better equipped to grow and maintain lean manufacturing; effective inventory control immediately correlates to information cycle time.
Include Customer's Voice in Business Planning Process
Lean inventory management software ensures consumers receive their goods promptly, without any complications or setbacks, at the right time and place. Businesses that view their clients as partners and actively pursue ideas for enhancement will experience increased customer loyalty and invaluable insights.
Write Down The Vision
Outline a mission statement for your business and put it in writing before breaking it into strategic goals, such as "We promise to provide high-quality products at affordable prices. Safety comes first. We plan on reaching 85% client retention." An OGSM model process planning tool may be useful; consider it part of your plan.
Lean Inventory Management's Obstacles
Lean inventory management offers many advantages but drawbacks, including slower response to supply chain disturbances. Other disadvantages may include:
An Extensive Amount Of Time And Resources Must Be Invested
Establishing an effective lean management system takes time and money, such as investing in modernized technologies or training courses.
Insufficient Customisation
Lean management does not permit much flexibility for product customisation or variety due to its focus on standardization processes, thus diminishing their benefits for companies seeking greater customisation.
Onboarding Of A Team
Convincing employees to embrace lean principles can be challenging, and managers, HR, and executive leadership all need to work toward changing the culture within an organization.
Conclusion
Controlling inventory levels is one of the key challenges of supply networks, requiring supply chain management companies to maintain an equilibrium between optimal inventory levels and demand to prevent overstocking.
Businesses consider lean inventory management an essential tool for controlling costs and optimizing supply chains. Implementing lean inventory practices such as minimizing surplus stock levels, optimizing operations levels, and continuously improving operations can reduce expenses while increasing customer satisfaction and revenue growth.