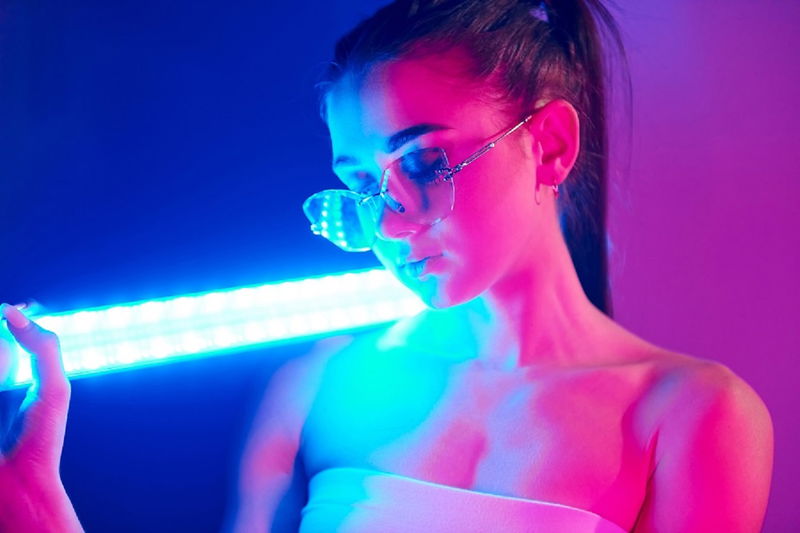
The face of maintenance has evolved dramatically over time due to new technologies such as cloud, IoT and AR/VR, AI and machine learning, IoT, and mobility. These technologies can be combined to create powerful software for computerized maintenance.
The CMMS centralized platform allows maintenance providers to collect data from equipment and then generate automated service requests based on detected anomalies or patterns.
We will explore CMMS and its benefits, including how it was created, its rapid growth in the maintenance services industry, its features, and its functions.
Why Businesses Need CMMS
CMMS can help businesses with a high asset base to solve complex maintenance issues, which leads to a more streamlined and transparent process. Productivity has also improved. Here are some reasons why you should use CMMS.
Preventive Maintenance
Preventive maintenance is the practice of scheduling maintenance to minimize downtime. A maintenance strategy helps to ensure that assets perform at their best. Scheduling preventive maintenance as a recurring event is easy. Just schedule it once, and you will be reminded as needed.
Continuity of Operations
A costly event could occur if an asset is down. The CMMS was developed to help reduce the downtime of assets and maintain smooth operations. Software is used to perform regular asset health checks, ensuring critical assets are always available and that operational disruptions are controlled.
Data Silos
A disconnected or isolated data structure can obstruct visibility, affecting decision-making. Software for computerized maintenance management provides 360-degree transparency into processes. This allows leaders to make informed and accurate decisions.
Problems with Productivity
A low level of productivity is a sign that profits are being lost. Regarding production, it is essential to ensure that each team member works optimally. CMMS provides data-driven insights into which factors affect productivity and which ones do not.
Experience Management
Excellent experience today isn't just for customers but also employees. Whether it is a customer or an employee, they all deserve a good experience. A CMMS can help to remove redundant tasks from work orders, increase downtime through preventive maintenance schedules, and empower staff with data analytics. This directly impacts the user experience of both customers and employees.
What are the Features of a CMMS?
CMMS features to cover most asset management functions. The technology on which the software is built will determine the level of advancement in the features. The more technology you have, the better the features.
The majority of computerized maintenance software systems include machine algorithms, AR/VR, cloud, mobile, IoT, and artificial intelligence. A typical CMMS includes the following features.
Work Order Management
The process includes all the small tasks required to resolve the service request. This is because the CMMS makes handling work orders easy, leading to a faster resolution. CMMS offers an integrated view into every aspect of the service management process, including
- Service Requests: What is being done?
- The current status of your job
- Technicians assigned to the task
- How much time does it take to complete a task?
- Materials used
- Documentation
- If you have any feedback from customers, please let us know.
A single software can summarize your services, so you have an accurate view and can make informed decisions.
Assets and Equipment
Maintenance software, used extensively in industries with a high asset concentration, allows them to monitor the availability and performance of assets and equipment. It's the backbone of their asset management.
This software has an asset management module that allows key users to store all information related to assets in a single location. Information can include:
- Hierarchical structure of assets
- Asset Conditions
- The asset's location
- Schedules of preventive maintenance for assets
- The documents that relate to assets, such as SLAs, videos/image files, and warranties
CMMS has a database that can store, process, and report this data for granular reports and KPIs.
Maintenance
CMMS is a preventive maintenance system that triggers work based on calendar intervals or usage events. CMMS can fully automate preventive maintenance schedules depending on technologies.
For instance, if the software is integrated with IoT and AI capabilities, it could directly process the skills-availability-tools data put into the system, the equipment's sensors create data, detect patterns and abnormalities, and schedule preventative maintenance for them.The software can also manage the sequencing of PM work orders and maintenance logs. It will send notifications about scheduled appointments to technicians via push notification.
Mobile CMMS App
Mobile maintenance apps are an integral part of the CMMS. CMMSs include mobile maintenance apps, which allow access to CMMS information from iOS and Android devices.
These data can range from information about scheduled maintenance to articles in the knowledge base, contracts, warranties, and service manuals. This information is easily accessible by the technicians at the site in real-time, allowing them to make intelligent decisions.
Inventory Management Of Spare Parts
CMMS automates the management of all spare part inventory aspects, from submission to approval. It is now possible to use the CMMS software for sending POs, RFQs, and RFPs. You can also set up minimum stock levels and get alerts when the volume exceeds thresholds. The user can add spare parts and receipts and find the inventory at different locations.
Management of Workforce
The benefits of CMMS in workforce management can be viewed from two angles: first, the role that CMMS plays in workforce management. The software that schedules jobs assigns routine tasks to technicians based on their skills. CMMS tools generally contain AI-based engines that run skill-technician-availability-location algorithms to select the right person for the job. This makes an otherwise time-consuming task simple. The CMMS tool also has a wide range of core features for managing technicians' timesheets and shifts.
Indirectly, CMMS tools can increase motivation, reduce frustration, and improve communication. It also increases trust between employees and the company since fewer people are involved, which means fewer opinions and biases.
Reporting
Tools like CMMS allow users to create custom Key Performance Indicators (KPIs) based on which they can generate reports, update them automatically, and then view or download them in different formats, such as Excel and PDF. CMMS solutions have data analysis capabilities that can turn data into useful information.
CMMS and How to use it?
Many companies need help with CMMS implementation. They buy this software believing it will fix all maintenance problems. The computerized maintenance software helps to ensure reliable maintenance. A successful CMMS implementation requires several steps and plans. Before implementing the CMMS, it is essential to know the steps involved in the process.
Find the Future of your Project
It is often the case that implementations fail because of incorrect selection. Before you choose a CMMS, check the scope of the project. Ask questions and get to the bottom of the matter. What exactly is the CMMS trying to do? What core features and implementation plan with detailed reports are needed by your company? What are the benefits of a CMMS for your company? Does it allow for interfacing with other systems?
Support from Management
The management team must understand the project's initial work and ongoing resource requirements correctly. In addition to the price of the software itself, there are also charges for maintenance, data entry, and training. Be sure that these charges are included when estimating the budget for your project. It is essential to ensure that the entire project team commits.
Prepare for Change
Plan the implementation of your system from beginning to end. Decide who will receive the data and which types of data you want to store in the system. Make a table of all the parts and add notes for each part to avoid confusion. Do not assume that all employees will accept CMMS software. Some fear the system could replace them. Give workers the knowledge they need to understand how CMMS can have a positive effect in the future.
Instructions to the Primary Users
This sophisticated software requires that employees who use it be trained. They can then help each other understand different terminologies to suit their needs. The main element of user engagement is training. The maintenance software will only be successful if users are engaged and adopt the program.
Data Collection And Entry
The implementation plan's key element is to gather the necessary data with committed resources (model type and serial number; costs; warranty information on parts, procedures, maintenance preventive, etc.). Determine the most effective way to enter the values in the CMMS after the data has been successfully gathered.
Go Live
After you've laid out your projects, the time has come to go live. It is crucial to discuss with your CMMS provider any issues you may have with implementation. This includes analytics, reporting, and user adoption. The implementation team must collate and prioritize all requirements. They should also recommend the next steps.
Read More: Quick Overview Of Maintenance Management Software
What is the Best CMMS?
Choose the best Computerized maintenance management system for your business by following these simple steps.
Defining your Goals HTML0
Identifying all maintenance departments involved in the system is essential. This insight will allow you to quickly compare the features of CMMSs and choose the one that best supports the maintenance activities in your company. Identify what problems CMMS will solve. Some suggestions include the following:
- What maintenance issue are you trying to resolve?
- Do you want to know more about preventive maintenance for your vehicle?
- What type of report are you looking forward to?
- Are you in charge of managing spare parts?
- What are your software needs?
You can easily find the best CMMS software if you know how to solve these issues.
On-premise or Web-based
It is essential to make the right choice as it will affect your implementation cost and time. We'll take a look at the two types of CMMS.
Cloud-Based Cmms
- No software or hardware is required to install.
- Reduced upfront costs
- Vendors handle backups, upgrades, security, and other issues
- Your internal IT department can be involved without being involved.
On-premise CMMS
- All software updates are your responsibility
- Additional features are available at an additional charge
- Support from IT professionals is needed
- Internally control all sensitive data
Find Out All Features You Need To Know About
Make sure the CMMS software features meet all of your needs. CMMS should have the following features.
- Asset Management
- Maintenance preventive
- History of maintenance work
- Order management
- Schedule maintenance for Preventative maintenance
Ask for a demonstration and thoroughly discuss features, cost of maintenance, and pricing with the vendor.
Scalability and User-Friendly
Software should be easy to use, understand and have a perfect interface. It must also require minimal training. You can save a great deal of money by choosing the scalable software.
Mobile Compatibility
You can save a lot of time by choosing software to manage and track maintenance tasks from any location. The team's efficiency will increase. Ensure that your CMMS provider has apps for both iOS and Android.
CMMS Trends - Future of Industrial Maintenance Automation
Suppose you have seen a positive return on investment from your computerized maintenance systems (CMMS). In that case, the future of CMMS is brighter for you. CMMSs must be constantly updated to remain competitive as technology changes. The latest trends and maintenance management methods are discussed.
Utilizing Cloud Computing
Cloud-based software is becoming more popular among companies due to its accessibility. Software is available 24/7 on multiple devices. The service provider ensures data security, and the installation process is simple. Cloud-based solution for maintenance management allows you to make faster decisions because of real-time data.
The software sends technicians push notifications via SMS and email. Maintenance teams can perform better because technicians, managers, and customers exchange information more effectively. Communication is improved because technicians can set priorities using the data in the work orders. Through API or application programming interface, data sharing is possible between devices that are internet-enabled and cloud-based CMMS.
Assets can be used to create maintenance requests, whether onsite, on mobile devices, or globally distributed. By assessing the actual asset's condition, you can increase the effectiveness of your preventive maintenance maintenance process.
Predictive Maintenance Is Better Than Preventive Maintenance
Since its inception, CMMS solutions have gradually shifted from reactive maintenance to preventive. This preventative management strategy can help businesses save between 12% and 18% on their budgets, allowing them to deal with issues immediately. Predictive maintenance may replace this method with one that is more efficient.
In the same survey, 59% of respondents said that predictive maintenance was one of the top features of CMMS. These systems provide real-time information to facility managers, business owners, and maintenance professionals. It helps determine what assets need more attention in repairs and maintenance because it is a more reliable CMMS tool than other CMMS.
This tool can help your staff save time and energy by eliminating the guesswork involved in determining the priority of maintenance for your assets. It is advantageous for companies with a lot of equipment to manage.
Artificial intelligence, the Internet of Things, and Internet 4.0
The future of maintenance automation in industrial plants results from modern technologies like Internet 4.0 and artificial intelligence. A CMMS that integrates with autonomous machines must have artificial intelligence or be able to regulate itself to maintain human factors.
Internet 4.0 allows computers to communicate without human intervention. Smart devices are capable of monitoring themselves and don't need technicians. Maintenance managers can access real-time data and take appropriate action to prevent unforeseen issues.
Businesses are using IoT to maintain assets. The use of predictive maintenance allows for real-time decisions to be made about asset management. Maintenance will become a profitable function instead of a maintenance cost center. Data gathered by IoT can be used to help you make long-term decisions. Data-based maintenance is becoming more popular. IoT allows for faster maintenance audits.
Intelligent Data-driven Maintenance
According to previous reports, the use of machine learning and artificial intelligence algorithms in maintenance management is increasing among CMMS companies. It will be possible to use more data-driven alternatives for maintenance. With these advanced options, you can streamline future certifications, audits, and root-cause analyses in company operations.
Adding Value
Regular features give real-time updates to keep the CMMS system relevant. Significant upgrades are welcome but don't make the system more valuable. To build future-ready companies with CMMS, the provider must stay connected with their clients and see what they're doing. What changes has the industry experienced? Does the CMMS meet the new requirements? A CMMS must consider features that apply to different industries. Is it willing to work with one client to provide a unique feature?
The CMMS should also be flexible. Custom CMMS must have enough flexibility to accommodate the expansion of smaller organizations or enterprises. They will have different needs than central grain elevators and utility corporations.
Mobile Use
A desktop-based CMMS allows you to easily create, track, assign, and manage work orders. However, to view them, you will need a computer. Why not make use of the mobile phones that everyone carries? It would be best to have a CMMS with a mobile app. A mobile CMMS offers many advantages to technicians. The CMMS aims to simplify the use of features and functions for mobile devices.
Build A Culture That Values Reliability
The shift to Industry 4.0 covers many topics. But putting the new technology to work begins with your people. You must also prepare your maintenance staff for any changes that new maintenance procedures and systems will bring about. It would be best to start immediately establishing a culture of continuous improvement in your company.
The first item on your list should be to establish guiding principles supporting best maintenance practices. The next step to promote data integrity and ensure good habits is to create official processes in each area, from purchasing to work orders. Communication is critical to building trust and accountability. Recognizing and rewarding employees who embrace new practices is crucial to encourage others to do the same.
Other Languages
As more companies expand abroad, a CMMS that can speak the local language can benefit all. Newer and better can sometimes mean more complex and complicated. Build on what is already working well. A complete redesign is only sometimes necessary, even in software. The CMMS should continue to be easy to use, well-organized, and intuitive. To keep up with the needs of new users, training is required. Clients appreciate training on new features and applications and refresher sessions.
QR Codes Can Be Used To Organize Maintenance Information
Maintenance crews can easily find information when each asset has a unique QR code. The QR code is all they need to know the type of work or the priority and inspection level with operational efficiency on maintenance program and maintenance planning with real-time tracking. It is easier to access and organize maintenance information.
Safety at Work
The future of industrial maintenance automation will primarily be based on safety. The goal will be to enhance communication and collaboration between daily operations, maintenance, and safety departments. Using company-wide technologies rather than isolated ones can improve data exchange. By utilizing the data from the safety team, they can perform the correct duties at the appropriate times. This will improve the compliance and effectiveness of the safety team and create a safe environment.
The Conclusion
Many businesses depend on software to run their maintenance operations smoothly. Making predictions about CMMS and other related industries is a good idea. It would be best if you always considered the future of maintenance automation to make the best of your company, both short-term and long-term.
Maintenance automation is a great way to reduce human error and collect and evaluate machine performance metrics and conditions data. The maintenance manager of tomorrow
Intelligent CMMS can automate and streamline maintenance tasks. Get in touch with the best and most reliable software solution for repair management.