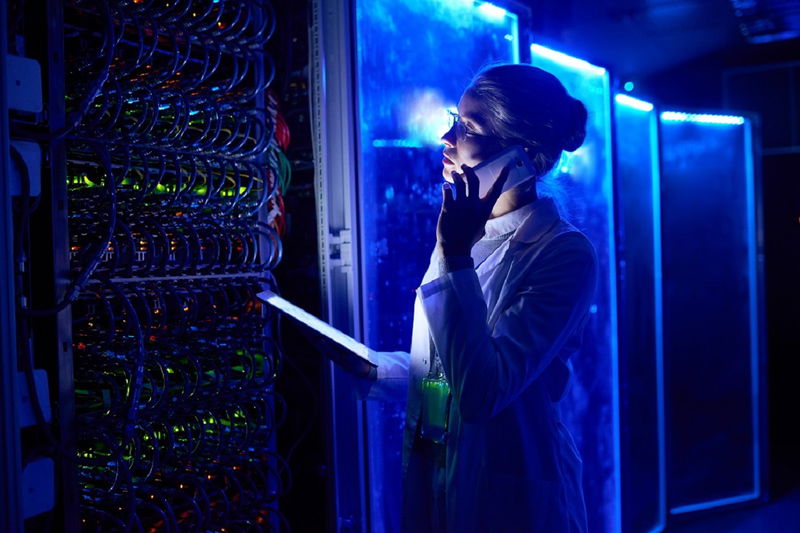
ERP inventory management refers to the practice of using an Enterprise Resource Planning (ERP) system to track inventory levels and movements within an organization. An ERP system integrates all aspects of an organization's operations into one centralized platform, including accounting, finance, inventory control and human resources administration, among others.
ERP inventory management enables businesses to effectively control inventory levels, speed up procurement procedures, optimize warehouse operations and increase supply chain efficiency by offering automatic stock replenishment, real-time tracking of inventory levels across locations as well as interfacing with sales/purchase orders for improved tracking capability.
ERP inventory management assists organizations by ensuring the right products are available at the appropriate times and in quantities at a low cost, minimizing stockouts, increasing turnover rates and improving customer service levels. ERP inventory management solution facilitates operational efficiency while improving overall performance, allowing firms to make well-informed decisions regarding inventory management.
Inventory Management: Optimizing Inventory Control With ERP
All businesses operations involved with the manufacture, distribution and sale of goods must implement inventory management. This involves keeping an eye on raw materials, completed goods and work-in-progress inventories.
Businesses may ensure enough inventory meets consumer demand while minimizing expenses by employing an effective inventory management system such as enterprise resource planning (ERP). ERP provides a centralized database for inventory tracking, which enables companies to track movements, manage levels and automate certain inventory-related tasks.
ERP systems for inventory control provide many advantages to companies and increase overall productivity.
Improved Accuracy In Inventory Tracking
ERP systems offer real-time visibility of inventory levels for firms, giving them more accurate tracking of goods flow while preventing stock outs or overstocking that would result in decreased sales or greater holding costs.
Better Demand Forecasting
ERP systems aggregate data from various sources, including historical sales, customer orders and inventory-related specifics. By using this information to accurately forecast demand estimates, businesses may use it to optimize inventory levels and lower stockout risk.
Automated Inventory Management
ERP systems feature automated inventory management features that reduce time and labor spent processing orders, tracking inventories and replenishment, freeing businesses up to focus on other essential tasks or more pressing matters. This enables organizations to address urgent matters more easily.
Enhance Supply Chain Management
ERP systems give distributors of finished goods access directly to raw material suppliers, providing visibility across the whole supply chain process and shortening lead times while optimizing supply chains, driving profitability and customer satisfaction in tandem.
Lower Operating Costs
ERP systems can help businesses reduce operating costs by increasing inventory accuracy, raising stock levels and automating processes associated with them. By decreasing stockout risks and expedited delivery charges, ERP can assist businesses in cutting expenses significantly.
Enhance Productivity
Organizations that implement ERP systems can increase their productivity by decreasing time and labor requirements for inventory management, freeing employees to focus on more valuable work thereby increasing production and improving business outcomes.
ERP systems are essential tools for businesses seeking to optimize inventory control. Through automated inventory tasks, enhanced supply chain management, and real-time inventory monitoring capabilities, ERP solutions help businesses reduce expenses, boost productivity, and enhance customer satisfaction.
Also Read: Inventory Management: A Key Component of POS Efficiency
ERP Inventory Management Features
ERP inventory management refers to a range of tools used by companies to maintain, improve, and monitor supply chains by overseeing inventory levels. At its core lies:
Demand planning and forecasting
This method projects future product demand using historical data and analytics. It uses a range of forecasting techniques, such as trend analysis and seasonality, to produce precise demand projections. ERP systems, in particular, use seasonality analysis algorithms to precisely forecast demand. Businesses may reduce the risk of overstocking or understocking, optimize inventory levels, and raise customer satisfaction by forecasting demand.
Order Management
By automating each phase of the order management process, from placement to delivery, ERP systems help businesses fulfill orders more quickly and efficiently. For bigger companies, this means faster lead times, better order accuracy, and happy consumers.
Purchasing
This approach automates every step of the procurement process, from inventory receipt and inspection to supplier management, by utilizing ERP systems. Companies can handle purchase orders, manage suppliers, receive goods for inspection, and reduce the cost of keeping inventory on hand by employing this approach. Procurement delays can also be expedited.
Warehouse Management
ERP systems are used by business models to handle the picking, transporting, and location of merchandise in warehouses. By reducing errors and improving order fulfillment, this technique boosts efficiency and accuracy.
Inventory Tracking and Control
ERP systems that provide real-time inventory management and control enable businesses to monitor inventory movements and levels across many locations, thereby mitigating the risk of stock outs or overstocking, which can result in lower sales or increased inventory carrying costs. Businesses may lower the danger of stockouts or overstocking by using this technique.
ABC Analysis
ERP systems can use ABC analysis to arrange inventory products based on value and consumption, which helps organizations prioritize management tasks and optimize inventory levels. Managers must devote more time and effort to managing higher-value commodities than to lower-value ones.
Just-In-Time (JIT) Inventory
Just-In-Time (JIT) inventory management, when implemented by businesses utilizing ERP systems, can be an inventory strategy that accurately and on time satisfies customer demand while also reducing costs by extending the shelf life of items and optimizing supply chain performance.
Just-In-Time (JIT) systems are able to meet customer demand while retaining less inventory overall by maintaining inventory levels low enough to meet demand rapidly while holding less inventory than would otherwise be needed for customer fulfillment.
Inventory Reporting
With configurable ERP reports, businesses can efficiently analyze inventory data, identify trends, and make wise decisions about inventory management. By using this method, companies can quickly detect shortages, overstocked goods, or slow-moving items and take the necessary steps to raise levels.
Enterprise Resource Planning inventory management encompasses numerous strategies that companies can employ to increase supply chain effectiveness and optimize inventory levels, thus lowering expenses, increasing customer happiness levels and creating a competitive edge in the market.
By employing such strategies, businesses reduce expenses, raise customer satisfaction levels, and gain a competitive edge over their rivals.
Implementation Of ERP Inventory Management
Installation of ERP inventory management requires careful preparation, coordination, and implementation. Here are the main steps involved:
- Establish Needs: The initial step of implementing ERP inventory management is defining its business requirements, such as implementation schedules and budgets, inventory standards and benchmarks.
- Select an ERP system: It is important that an ERP system that meets both your organization's needs and budget is selected. An ideal system should include demand forecasting, order management, inventory reporting, real-time tracking capabilities as well as real-time updates on inventories - these should all be features of an ideal system.
- Plan the Implementation Process: In this stage, planning involves creating a project plan, assigning roles to team members, and setting due dates.
- Migration: Field mapping, validation and correctness assurance methods should be employed when migrating inventory data from current ERP systems into future ones.
- Configure Your ERP System: After identifying inventory locations, policies, and control criteria, the next step in setting up an ERP system should be to customize it to meet those needs.
- Training Passengers: In the second step, users should be instructed on the best practices and inventory management strategies of their new ERP system.
- Test and Validate: To ensure it satisfies business requirements and performs as planned, its performance must be thoroughly examined and validated.
- Go-Live: Once deployed and launched successfully, an ERP system becomes fully functional in its intended setting. This stage completes its task.
Implementation of ERP inventory management includes a number of phases, such as determining the needs of the business, choosing an ERP system, organizing the implementation, moving data between systems, configuring the systems according to user instructions, testing and validating the systems, and going live.
By taking an organized approach, businesses can successfully incorporate inventory management into their supply chains, leading to higher levels of inventory, cheaper costs, and increased supply chain efficiency.
Conclusion
ERP inventory management holds great potential to increase supply chain efficiency, lower costs, and maximize inventory levels-which in turn has an immense positive effect on any business's performance. An ERP inventory management system may enable businesses to optimize inventory levels to reduce expenses while increasing revenues.