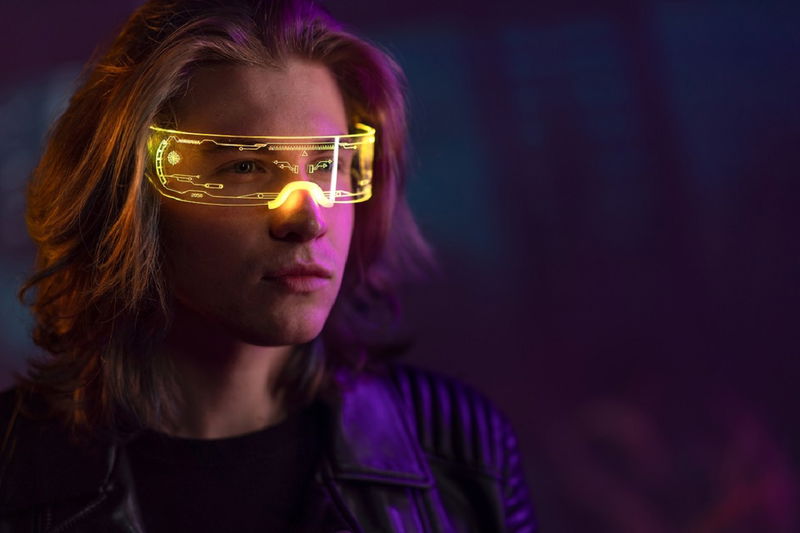
Many businesses today have adopted the most recent systems and adapted to technologies and concepts they never thought they would use in the future. These changes are often driven by digital disruption and digital innovations. Take this example:
- The Internet of Things (Iot), which simplifies data collection around the globe, has been a game changer.
- Running Equipment with a Non-Required App that Controls Key Operating Parameters
- Customers will pay for uptime availability and usage rather than a product outright under the Products-as-a-Service model.
- Parts made from recycled material are essential for sustainability.
These may seem "optional" right now, but they could be essential. Considering how rapidly technology has advanced over the past few years, IM & E-businesses need to address existing problems and prepare for new problems quickly.
What is Enterprise Resource Planning (ERP), and How Does It Work?
Enterprise Resource Planning, at its core, is an application that automates business operations and provides insight and internal controls. It draws on a central database that gathers inputs from various departments, including accounting, modern manufacturing business, and supply chain management.
Each business has to complete work that involves multiple stakeholders, each with different responsibilities. Finding the right information across disparate systems can be difficult, making it more difficult for businesses to complete their work. Employees may not have easy access to the data they need, whether it is stored in spreadsheets or basic business management software. The accounting and FP&A departments could have different spreadsheets containing different expense tracking numbers.
Because of the disparity of data sources, it is difficult to keep everyone on the same page. This can lead to poor Collaboration and productivity, especially as an organization expands. Because there isn't one place that provides current information about all aspects of the business software, staff waste time searching for documents or creating duplicate work. It is also difficult to understand the true cause and effect of changes that affect your individual business requirements.
An ERP system solves this problem. It compiles information in a central database that grants managers and employees cross-departmental access. It eliminates conflicting data sources and allows employees and managers to analyze scenarios, identify process improvements, and make major efficiency gains. This results in cost savings and improved productivity because people spend less time searching for the needed data.
ERP software tailored to the specific needs of a business pays big dividends. This makes ERP software a crucial tool for all industries and sizes. ERP has been a key tool for many of the world's most successful and well-respected companies over the past quarter century. This software is now configurable and priced to suit the needs of any size business growth.
What is an ERP System?
ERP systems operate by using a standard data structure. All authorized users can access information entered by one department immediately. This helps everyone stay on the same page. Let's say, for example, that a local food distribution chain has multiple locations which often share stock or personnel. The ERP system formats the data to indicate where it came from, as it feeds in quality, sales, and employee data.
The real-time data can be integrated into core business processes across departments and workflows. Leaders can determine if one site is performing better than another and work with operations to determine why. Executives can use finance to compare rents and sales to decide whether to consolidate.
ERP systems are most valuable when modules exist for every major business function. This ensures that data entry is accurate and timely. The more stakeholders that have access to ERP systems, the better.
Integrations can allow data to flow automatically into an ERP if a company has business systems from different vendors. These real-time data can be used in the ERP instance to improve any process or workflow.
Machine and Equipment ERP Software
ERP Software is a cloud-based, automated software system that can be used for Machinery and Equipment Industry solutions. It helps you to meet your needs and to manage the industry smoothly. Absolute ERP Software allows you to improve and manage your business intelligence, allowing you to grow your operations.
Our vision is innovative and helps us design solutions for manufacturers. Industry-specific ERP solutions for Machinery Manufacturing Software is the most suitable choice for the machinery and Equipment industry. It can be used in all production modes and caters to service spare parts.
The machinery and equipment manufacturing industry is complex due to the large inventory of machines and spare parts. Absolute ERP Software for the Machinery and Equipment Industry allows you to manage workflow and multi-level assemblies easily. The Best machinery and equipment ERP software will allow you to track your inventory and schedule shop floor functions.
You can also calculate the corrective cost for each raw material so that you can become a great machinery & equipment manufacturer. ERP Software for Machinery & Equipment aids in the management of all business tasks. Our dependable ERP Software offers corrective methods that result in consistently modernized manufacturing/production for Machinery & Equipment operations.
Challenges
The pandemic brought many operational challenges to the forefront and a host of new challenges.
Product Design
Industrial machinery and equipment manufacturers often deal with complicated specifications and production problems. It can be difficult to translate engineering requirements into machine specifications, whether for new orders or modifications to existing machines. A structured change process must be implemented, supported by the appropriate software, to convert specifications into working designs.
They must also consider production plans and inventory requirements. Expert product design relies on the details provided by suppliers. Without timely feedback, making the best design decisions cannot be easy.
Planning And Managing Production
Manufacturing teams face challenges keeping track of jobs and planning new orders. The visualization of the production process allows you to evaluate the progress of each job and give you an indication of potential delays. This is necessary to ensure a partner for manufacturing runs on schedule, and that deliveries are made on time.
These are critical manufacturing operations management and supply chain management tasks with a lot of responsibility overlap. They can, however, solve manufacturing problems when they collaborate. Critical resource management is a major issue in job planning. Manufacturers must connect people and materials to jobs in order to deal with unexpected changes like escalations, interruptions, and absences.
Want More Information About Our Services? Talk to Our Consultants!
Management of Quotations
This is a challenge for IM&E manufacturers because the majority of their work is based on quotations. Manufacturers want to reduce the cost of creating quotes while increasing conversion rates. However, calculating costs in order to provide accurate quotations takes a long time. The promptness of a request for quotations determines its success rate. However, inaccurate quotations can cost the manufacturer money due to their low margins. A real dilemma!
The quote could be rejected if the information is inaccurate, including costs, production details, and other pertinent information. This can lead to lost sales. Therefore, sales personnel must have access to all details to ensure they can provide a competitive quote for their customers.
Forecasting And Inventory Management
Manufacturing companies often lack visibility into operations outside their factories, leading to complex supply chains. A better understanding of the supply chain and all of its nuances will help with planning and inventory management.
It takes a lot of effort to keep track of the large inventory of parts and stock that IM and E companies must maintain. It is critical to ensure that resource consumption is balanced and that delivery times are met by dispatching this inventory accurately and on time to the shop floor.
Accurate demand forecasting is critical for accurate, timely, and efficient production. To meet the customers' delivery dates, optimal inventory levels were required. Forecast accuracy is dependent on this data. This data is usually based on historical trends or seasonal patterns. Collecting this data requires Collaboration from all stakeholders and across the entire supply chain, including customers.
Traceability And Quality Control
Manufacturers are increasingly being held accountable for their products' quality and safety. This is done to ensure that products meet the minimum requirements. Customers expect suppliers to be able to trace any issues back to procurement, production, and delivery.
Customer-Centricity
Understanding customers' immediate problems can help manufacturers reap the benefits. This will aid in regulatory change planning and response. The Collaboration should result in increased profitability for both companies. Companies can use customer data to segment customers. This will allow them to understand their customer's needs better and help them choose the best offerings.
Life Cycle of Product
Manufacturers should think beyond the physical product and consider how their customers will use it over the course of their lives. This entails careful planning and evaluating the necessary support tools. This may necessitate the creation of apps and other digital services. Sometimes products have physical and digital launches. This will require separate planning.
Sustainability
Manufacturers must be aware that consumers are more concerned about the environmental impact of their products. Sustainable manufacturing refers to producing goods or services with minimal negative environmental impacts and conserving natural resources. Many environmental regulations must be considered in many countries when developing future products.
ERP and IM: How it Helps
companies in the IM & E industry should pay close attention to the most recent technological advances.
- A fully Integrated System: A fully integrated system is required by businesses to ensure that different manufacturing functions do not operate in isolation. Change orders and new specifications should not only affect design plans but should also be communicated to resource planning (e.g., At the same time Bill of Materials and Master Collaboration with suppliers online is essential to ensure design specifications are communicated accurately and changeover plans are executed).
- Shop Floor IoT Devices: The traditional retail floor is evolving. Some manufacturers have realized that these new digital technologies can significantly reduce costs, increase productivity, and reduce errors. Data from interconnected systems, including IoT devices on factory floors, can be used by businesses to optimize production and improve end-to-end manufacturing processes.
- Sales Order Process: Sharing sales order processes with other departments can help you get accurate and timely quotations. Although it may be difficult to make a sale in complex IM & E environments, sales staff can see the status of inventory availability and production orders, which allows them to provide better customer service.
- A Supply-Chain Portal: An ERP system integrates data from all business units, giving better information to help manage inventory and parts availability. An ERP solution that includes an online portal for suppliers allows for Collaboration on pricing, stock availability, and planned delivery. This can help to build an agile supply chain.
- Traceability: An ERP system that provides a complete traceability system allows you to quickly identify, trace, report, quarantine, and place affected products on hold. It provides visibility across the value chain, ensuring regulatory requirements and quality compliance. In today's manufacturing environment, the customer expects the supplier to manage the asset.
Connecting to digital services is critical in the new world of manufacturing, where products are packaged with services. Although many applications can support this, integrating and consolidating information within an ERP system is becoming easier. An ERP Solution can connect to a variety of systems, allowing customers to access the services they require from a single point.
Businesses must be able to monitor their production processes in order to determine which resources are being used and how to recycle them most effectively. This is essential to sustainable manufacturing. An ERP system will help you monitor material consumption by process and support sustainability planning.
Read More: 5 benefits of ERP Software in the Manufacturing Industry
The New Norm For Manufacturers
Many companies have begun to become more digitally literate and well-organized. Take, for example:
- 91% of respondents have invested more in digital transformation over the past year.
- 95% of respondents believe digital transformation is crucial for future success.
- - 54% of respondents want to speed up product innovation by adopting digital technologies.
- 40% - 40% of respondents say they prioritize investments in sustainable manufacturing processes.
This is a significant segment of midsize businesses. Manufacturers should ask these questions.
- Is it possible to remain in the minority that resists change simply because it seems too risky?
- Are old business models changing? Are business models changing? Are our business performance models changing? If so, what ones and how are they changing?
- What technologies should be prioritized for adoption to support new business activity models?
Six Problems Facing Industrial Machinery Manufacturers: How ERP Can Solve Them
Most industries have experienced a rollercoaster ride over the past two years. We've seen supply chain challenges, scrambled logistic networks, global health crises, and unemployment.
The new normal has been established, but the pandemic created many operational challenges for the manufacturing industry. Most industrial manufacturers now use the latest technology, like IoT and Big Data analytics, to remain competitive. This is after they have experienced difficult times due to increasing material costs, product management complexity, and falling productivity. How to prepare for the future of manufacturing in 2023.
The manufacturing of industrial machinery involves the production of heavy industrial equipment as well as custom-engineered goods in a variety of industries. Because each project is unique, the processes can change often. It cannot be easy to manage industrial manufacturing production.
This is the right time to search for solutions that will enable digital transformation and help you overcome your business challenges. Let's look at how ERP can help industrial machinery manufacturers overcome their many challenges.
Engineering Challenges
Because of the unique requirements of each project, manufacturing industrial machinery (IM) is complicated. It doesn't matter if you need to order new machinery or change an existing product. Translating project requirements into a production workflow can be time-consuming and difficult. Technology that streamlines processes can save valuable time. To record production instructions and items, engineers can use Manufacturing ERP to create a Bill of Materials. Manufacturing ERP uses the BOM to prepare for production quickly. It reduces errors and saves time. It allows engineers to concentrate on design and engineering tasks.
Production And Planning Problems
Machinery and equipment manufacturers must establish project timelines like in every other provider of industry. Many companies employ the critical path method to determine the most efficient production workflow. They then compare the timeline to see if there are any bottlenecks. The critical path method first identifies all tasks required to complete the project. It then determines the tasks that must be completed on time, which can be delayed if necessary, and how much float/slack is available.
This method cannot address resource changes like interruptions, escalations, and absences. An integrated manufacturing ERP allows industrial machine manufacturers to monitor the status of jobs, whether they are in progress or just beginning, and can also see how jobs have been completed. This gives them visibility into shop floor performance. The integrated scheduling feature of ERP coordinates all job operations' start and stop times. Find out how scheduling and advanced planning can help manufacturers reduce production costs.
Management of Demand, Inventory, and The Supply Chain
Complex supply chains are common for manufacturing companies. Due to the high number of custom orders, industrial machinery manufacturers face challenges in their supply chains. Because it is difficult to predict demand, managing inventory can be challenging.
A manufacturing ERP integrates industrial machinery manufacturers with the ability to track and manage their inventory in real time, prevent material shortages, optimize supply chains, and meet delivery deadlines.
Quotation Management
Industrial machinery manufacturers face a lot of challenges, including frequent quotation errors. IM manufacturers always look for ways to decrease errors, time, and costs in calculating quotations. Automated solutions can provide accurate and timely responses to quotation requests. ERP allows industrial machinery and equipment manufacturers to track and respond quickly to Requests for Quotations (RFQs).
It enables IM manufacturers to generate accurate quotations based on real-time visibility of material, labor, vendor processes, inventory and Bill of Materials (BOM), profit margins, and resource availability. If authorized, these quotations can be swiftly submitted to customers and transformed into sales orders.
Resource Management
Manufacturing companies want to maximize their resources. Effective planning and scheduling are essential for this to happen. Industrial machine manufacturers face several challenges in resource management. They must coordinate resources (materials and people, machines, and people) and manage interruptions, absences, and breakdowns.
A manufacturing ERP system integrates information about production personnel, machinery, and other important resources. Manufacturing ERP systems can be linked to production equipment via sensors to get notifications about machine faults and preventive maintenance. IM manufacturers can receive real-time reports to monitor machine capacity, equipment efficiency, and staff performance and ensure that resources are used efficiently. Corrective actions can then be taken if there are any problems.
Service Flow Issues
IM manufacturing projects do not end after the equipment has been produced. Customers will need service for their products. Industrial machinery manufacturers require service management software to view service tickets, past orders, service history, and warranty details, and view service history.
Service personnel can set up service visits and requests on a shared calendar. Personnel can then be assigned tickets according to their experience, availability, or priority. Modern ERP systems allow for instant service support via mobile devices and tablets.
Take A Bow
The challenges facing industrial machine manufacturers in 2023 will be greater due to the changing business environment and global competition. Modern ERP Systems can address these issues by increasing Collaboration, security, reporting and forecasting, planning, compliance, and reporting.
By utilizing innovative ERP software, industrial machinery manufacturers may easily overcome numerous manufacturing obstacles and meet client expectations.