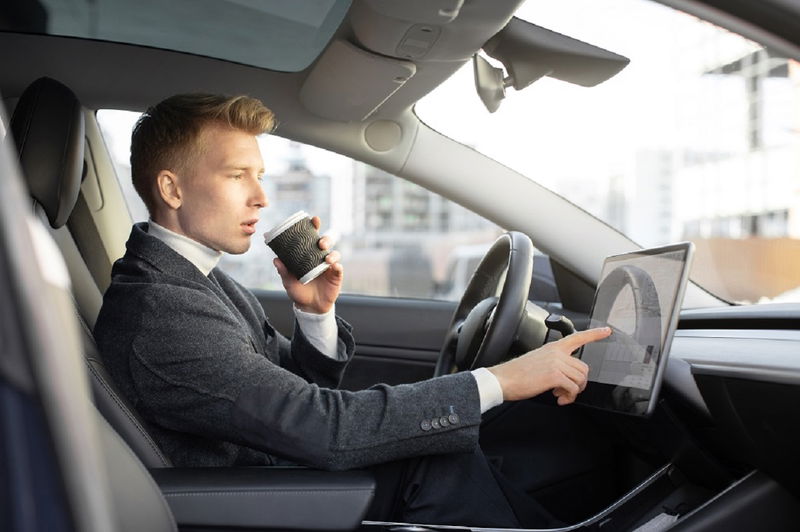
Manufacturing has become one of the most dynamic and competitive industries and is demanding manufacturers to meet the rapidly changing customer demands.
However, to accomplish these objectives manufacturers are focusing more on accelerating the processes and making everything more efficient and productive.
To elevate the graph of manufacturing businesses, the manufacturers have been utilizing ERP software is all about simplifying the entire operations of manufacturing while improvising deficiency and reducing the cost.
This ingenious ERP software delivers other prime benefits and, in this article.
We will have a look at these amazing ERP software benefits for the manufacturing industry.
1) Data storage with the greatest safety
Manufacturers have been eliminating manual processes that are completely error-prone. However, depending on paper records have proved to be very inefficient and unsafe because they can be easily stolen and can be torn very easily. The same case is with hard disks as well since they cannot guarantee data security when several people are using them. But with the implementation of ERP software manufacturers can easily get access to different data via a single centralized system. However, managers can also offer access rights to the staff that are solely responsible for managing the data. There are even cloud-based ERP systems available in the market that allow you to manage data at any time and anywhere. The additional advantage of today's ERP systems is that they can get access rights to manage the data as long as the devices are connected to the internet.
2) Enhanced inventory Management and Supply Chains
Inventory management is the most crucial factor when it comes to the seamlessness of manufacturing processes. With the help of ERP, software manufacturers can easily monitor their internal as well as external stock movements in depth.
However, these user-friendly systems also allow businesses to get the best and least marketable products so that they can easily manage the purchasing and procurement operations more efficiently. These benefits allow the manufacturing processes to bring consistent innovations to the market.
Speaking about the supply chain then complete visual transparency of the supply chain is quite pivotal. Because it helps avoid production disruptions as well as miscalculations in the manufacturing processes. With the help of this ERP software, you can easily manage and maintain business productivity and can optimize delivery times.
Also, you can identify the errors as well as lags in the areas that are undergoing problematic productions. Not least, the ERP system can also help you gain a complete view of the business operations and it can also establish HR modules with staff management.
3) Easy Connectivity of Different Departments
ERP software can be largely used to integrate and link different departments of a manufacturing company. These different departments include human resource inventory, sales, financial section, customer service, and more.
With ERP systems the organization does not need to separately keep track of every department. Here, all the departments will be connected with a single system and the managers can easily get access to complete data from each of the departments in a real-time phase.
4) Cost Minimization and Bottom-line Improvement
Getting an ERP solution for the manufacturing process helps reduce time as well as cost. It also helps slow down the manual operational processes that produce several legs as well as described in seas when it comes to reporting. ERP software offers seamless processes along with real-time feedback that can help optimize the overall workforce productivity along with reducing the total labor cost.
With this, you can easily enhance the reception required for the manufacturing processes while managing the supply chain and inventory cost in a much better technique. In short, all these benefits will deliver thorough transparency and control of the manufacturing business.
The system encompasses business intelligence features that allow it to manage, schedule, and keep track of the workflow without needing a production line. This helps in building more accurate decisions with lessened errors, improvised financial management, increased performance, and very fast execution of business processes.
5) High-Level Security
The topmost cloud-based ERP solutions offer end-to-end business protection as well as application security. These features can help improve the resilience to corruption as well as all data security breaches. Since servers are situated outside with numerous backups, the cloud system-based ERP helps to avoid disturbances due to natural disasters, shortage of power, and everything that could usually risk the integrity of the resources as well as data.
In a Nutshell
The skyrocketing advantages of ERP solutions for manufacturing businesses are very significant. However, while choosing ERP software, you must first align yourself with the most experienced person who can help you implement, educate, train, and incorporate the perfect application for your business.
How can Manufacturing ERP (Enterprise Resource Planning) Benefit you, and What is it?
ERP software and systems plan, manage and deliver specialized functions to support manufacturers and their business activities. Manufacturing ERP is an example of ERP software and systems. Modern industrial ERP systems offer a complete management platform and are adaptable enough to integrate with any company function.
ERP Software is Used in Manufacturing
ERP systems, a manufacturing management software, increase a manufacturing company's efficiency by controlling and optimizing corporate resources. Manufacturing businesses can develop and become more profitable by lowering or raising the number of resources needed without sacrificing quality or performance. Manufacturing businesses may control every area of their operations, including shop floor activities, inventory management, and supply chain management.
A manufacturing ERP system delivers support that enables manufacturers to expand their operations, boost revenue, and enhance quality.
What Distinguishes Manufacturing ERP from Standard ERP?
An ERP program that works with all types of enterprises is known as a standard ERP system. In many instances, a generic system is created as a one-size-fits-all. It may not have full manufacturing integration or essential functionalities for a business that focuses on manufacturing. Integration can result in limited data perspectives and may call for software development to address particular business or industry needs.
An ERP system for manufacturing is created especially for the manufacturing sector and offers cutting-edge capabilities for needs unique to the sector. ERP software for the manufacturing industry connects manufacturing operations with key business activities to provide you with complete control and insight over your manufacturing company.
What is the Best time to Get ERP ready for a Manufacturing Company?
- ERP for manufacturing has an operations management focus. Manufacturing organizations should consider an ERP solution for manufacturing management when current business procedures and systems are insufficient.
- No longer work, or work poorly (throttling/bottlenecking)
- Stop promoting the expansion of the business
- Inadequacy of security measures to reduce risk
- It is crucial to identify and fix broken processes to grow and find areas for improvement.
What does ERP Mean for Manufacturing?
ERP, which can be a game changer in the industrial sector where efficiency is sought but frequently hard to find, can have a significant impact. Payroll administration is just one of the many parts of the facility's operations that may be centralized with manufacturing ERP. Excellent operational efficiency results from ERP's unparalleled visibility and coordination across all corporate activities.
ERP in Manufacturing: How & Why-to Guide
Given the numerous tasks that need to be completed each day to keep a plant running, ERP is a perfect fit for the manufacturing sector. Here are a few instances of processes that ERP can speed up. Take notice of the various ways that these processes can "speak" to one another via ERP as well. This is a crucial advantage that will be covered later.
- ERP can be a central resource for tracking inventories, data analysis, and replenishment plans.
- ERP in the supply chain enables tracking of vendor performance visibility and organization. To assist with supply chain planning and management, it can also draw data from both internal and external sources.
- Maintenance: By centralizing ticketing, scheduling, and work order administration, the Manufacturing ERP software makes maintenance easier. Additionally, it enables excellent data tracking and analysis to raise the effectiveness of maintenance.
- Monitoring the performance of your equipment: ERP modules let you store, monitor, and examine data from sensors and reports. This makes it possible for greater preventative and focused maintenance.
- Enterprise resource management software can track QA findings and accumulate a sizable amount of data over time. This can assist in the early detection of maintenance needs.
- Purchases: The organization of purchases and requisitions is made simple by ERP. It also makes other aspects of the procedure visible.
- HR: ERP is not only beneficial for supporting manufacturing processes. Additionally, it can be used for HR tasks like goal-tracking and performance reviews.
Read More:- Comprehensive Guide on ERP in Healthcare Industry For 2023
Following your comprehension of the "hows," let's now examine the "whys" - the advantages of an ERP project.
- Greater process visibility: ERP is the system's central, easily-accessible "single source of truth" for all processes. Any department or procedure information is available to anyone. As a result, promoting cooperation, coordination, and communication is more straightforward, introducing advantages and innovations.
- Communication among departments: Improving process and function visibility can remove communication obstacles. Process silos, or "walls," that divide several groups and functions can result in duplication of effort, inefficiency, and the loss of cooperation opportunities. Through open channels and transparency, ERP can address these issues.
- ERP enables modern, data-focused facilities and all the advantages of this unmatched knowledge and information, including centralized data collecting and analysis for machine sensors, QA tracking, and many other activities. Making better, more educated judgments in areas like machine usage, maintenance, and purchase can be facilitated by data analysis.
- Process efficiency will increase: Productivity will increase as more data is gathered and people grow more comfortable using ERP. As processes become more efficient, cross-functional efficiencies will be recognized.
- Cost savings: The overall cost savings and efficiency that come with ERP investment go hand in hand with the advantages mentioned above.
Numerous procedures, such as maintenance planning, scheduling, and strategy, are streamlined by ERP software. The primary goal of ATS is to help manufacturers leverage data-driven technologies like ERP and CMMS to keep plants running while constantly improving. To learn more about the MRO asset management or industrial maintenance solutions provided by ATS, get in touch with a condition monitoring specialist right away.
The Ideal ERP for Manufacturing?
With the ability to adjust to disruption and change, manufacturing ERP solutions that support adaptive manufacturing enterprises have an advantage over their rivals.
There are numerous distinct ERP system types and deployment choices. Depending on the requirements and scale of manufacturing firms, these vary substantially.
- An on-premise ERP system offers ownership, control, and support once established. This covers a manufacturer's infrastructure and hardware maintenance costs and dangers.
- Manufacturers can benefit from a comprehensive and adaptable system that is updated, trained, supported, and customized by an ERP provider with the help of a cloud-based ERP system.
- A manufacturing company may benefit from hybrid ERP implementations that offer a combination of on-premises and cloud-based hosting and deployment services. These models enable ERP users to switch distribution methods or include advantages not present in the current implementations.
Cons of ERP - Important Factors and Disadvantages
ERP Software Costs
- Software add-ins from third-parties
- Implementation costs
- Maintenance
- Training for both initial and ongoing
Conversion of Complex Data
- It can be hard to develop a solid strategy for data conversion.
- Data sources must be identified, examined, and analyzed.
- Incorrect data conversion can lead to delays and higher costs.
Training is Required
- All features of an ERP system must be covered in training.
- Sessions for ERP training must be coordinated with operational procedures.
- IT users need to receive technical ERP System training.
ERP Projects demand a sizable time and financial commitment. Implementations of ERP software that are most successful require:
- Harmony between IT and business
- Executive backing and sponsorship
- Leaders of the internal team
- dependable partners (consulting firms and software vendors).
Other business technologies can be utilized in conjunction with ERP software. However, using the tool does not ensure success or failure. The corporate environment, leadership, and end users all affect the ROI of the ERP system, in addition to the installation, project planning, and methodology.
What are the Causes of ERP Implementation Failures?
- Data conversion
- A significant issue in an ERP implementation is data conversion. Data must be transferred from the earlier system and mapped to the new ERP.
- Integration
- Early in the project, you should consider different systems that will need to be integrated with your ERP system and develop an integration strategy.
- People
- Key business leaders and an executive must participate in the ERP project. Communication plans are also crucial.
- Training
- The ERP project should include training. Both end-users and internal teams need to feel comfortable using the new software.
- Planning a project
- The effectiveness of an ERP adoption depends on planning. A method can be used to prevent failure.
ERP for QAD Manufacturing Features
Manufacturers need to be flexible. The business environment is constantly changing, and strategies and practices used yesterday might not be applicable tomorrow. Manufacturers must be able to anticipate and prepare for disruptions and changes rather than reacting to them. QAD manufacturing ERP systems give companies the flexibility to adapt to change and keep up with emerging technologies, giving them an advantage over rivals.
In a dynamic business climate, QAD offers solutions that help manufacturers be creative, adaptable, and intelligent. This entails incorporating real-time reporting into your company's operations and giving consumers and the market visibility so you can make wise judgments. Using QAD enterprise planning software, manufacturing organizations can react rapidly and effectively to internal and external business changes. Manufacturing companies can acquire a competitive edge and respond to disruptions and change with QAD ERP systems.
Want To Know More About Our Services? Talk To Our Consultants
Conclusion
There are as many reasons for ERP implementation to succeed as for it to fail. However, the cost and timeliness of an ERP implementation are frequently used to gauge its success. However, the solution to maximize the system's capacity to enhance commercial procedures is frequently disregarded. To help firms comprehend the advantages of implementing enterprise resource planning, it should be described and measured. The numerous ERP deployment triumphs and disasters have taught us valuable things. Contradictory information has been provided in several cases. However, most people concur on a few guiding principles.
- Before you choose the software, define the operational procedures.
- Users and IT personnel will be on the project team.
- Make an implementation plan and follow it.
- Inform users of how to alter the information's flow and operation.
- With "go live," a project is not finished; it must still be kept under observation.