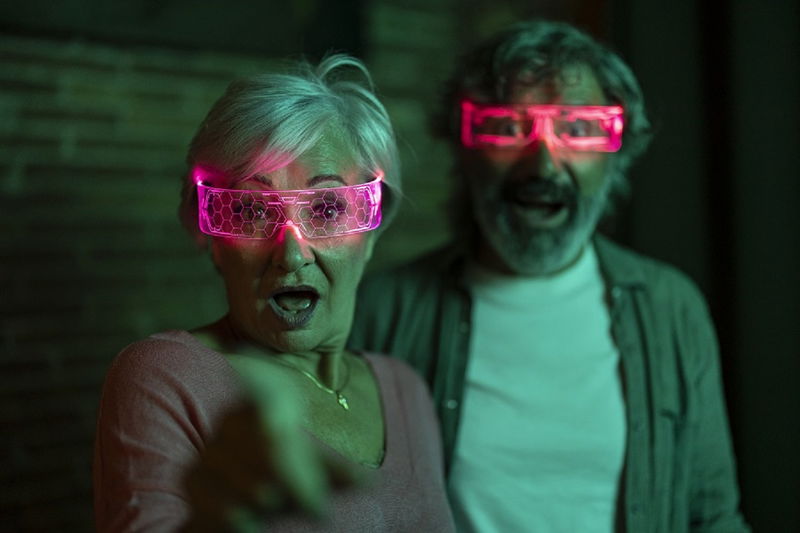
The role of the CFO for manufacturing and distribution has changed significantly over the past decade. CFOs were traditionally seen as financial risk managers and back-office numbers crunchers. Many organizations are going through rapid changes to adapt to new supply chain opportunities and challenges.
The modern CFO will be expected to serve as a strategic partner for the C-suite, helping to develop and execute the company's strategic agenda and driving change within the organization. Technological innovation and the ability to access massive amounts of data within and outside of an organization are changing the role of the CFO.
Modern CFO
The 2021 Arion ERP survey found that 57% of manufacturing CFOs believe that knowledge and proficiency are the most important factors in transforming a business into a digitalized, automated manufacturer. Modern CFOs must be able to comprehend digital technologies and how they impact their business. Those who can do this will make their organization more dynamic, agile, and successful.
Manufacturing and distribution CFOs must increase their adoption of digital technology as strategic leaders. This will improve efficiency, customer experience, control, and control throughout the supply chain. The ERP solution will give the CFO access to centralized data and visibility over the entire business operations. This will allow him or her to make better decisions that can drive growth and profitability.
Here is the ERP ROI for manufacturing and distribution CFOs:
1. Maximizing profitability and cash flow management
CFOs can help businesses develop a more reliable and responsive supply chain by acquiring and integrating additional information. CFOs need to have real-time visibility into production and raw material prices, shipping and transport costs, as well as information about their suppliers' activities. This information will allow you to guide your company through unknown waters, manage cash flow, and maximize profitability.
An ERP system can also guarantee accuracy, which is important for cash management as anomalies and errors can easily be identified. ERP allows CFOs and other executives to identify potential efficiencies that can be used to reduce costs across the company.
2. Diversification of business operations
According to the Arion ERP study, disruptions from the pandemic had a significant impact on the diversification of manufacturing companies. According to 65% of respondents, CFOs have increased their spending in new markets, product lines, and technologies in order for them to succeed. Manufacturers must be willing to reinvent themselves and make a conscious effort to improve the way they sell, customize and design products and services for their customers. Otherwise, they will be outcompeted by others.
The ERP system provides the CFO with intelligence and knowledge that allows them to integrate across platforms, systems, and processes in real-time. This allows them to create new products and services that are as adaptable as customers.
3. Industry 4.0
New goals and challenges have been set for the CFO by the race to digitize business operations. CFOs face increasing pressure to modernize outdated systems and increase digital connectivity at a reasonable cost. Respondents were asked to identify future investment areas to ensure success. 56% of the manufacturing and distribution CFOs responded that they would invest in warehouse automation. 37% said they would explore migration to cloud-based services, while 37% indicated they would look into SMART technologies, such as 3D printing and IoT. 37% also stated that they would consider exploring Artificial Intelligence (AI) and Machine Learning (ML).
ERP solutions can foster innovation and collaboration, while also creating transparency and breaking down silos between departments and teams. An ERP system can also provide data to the CFO regarding financial, technology, and market analysis. This allows them to drive digital transformation initiatives and assess risk and digitization opportunities.
4. Data-driven decision making, risk management
CFOs can access real-time, accurate data to understand their business operations. They can also share this information cross-functionally and use it to make strategic decisions and manage risk. Dashboards, KPIs, and other business metrics provide CFOs with visual access to the data they need to transform their businesses. These metrics can be monitored continuously to help the organization measure performance and identify trends.
Manufacturing and distribution companies have been able to adapt and shift their operations in response to ongoing supply chain disruptions. Companies are expanding their production lines, exploring new territories, and rethinking their business models. These shifts are being driven by the CFO, who is changing the face of distribution and manufacturing as we know it.