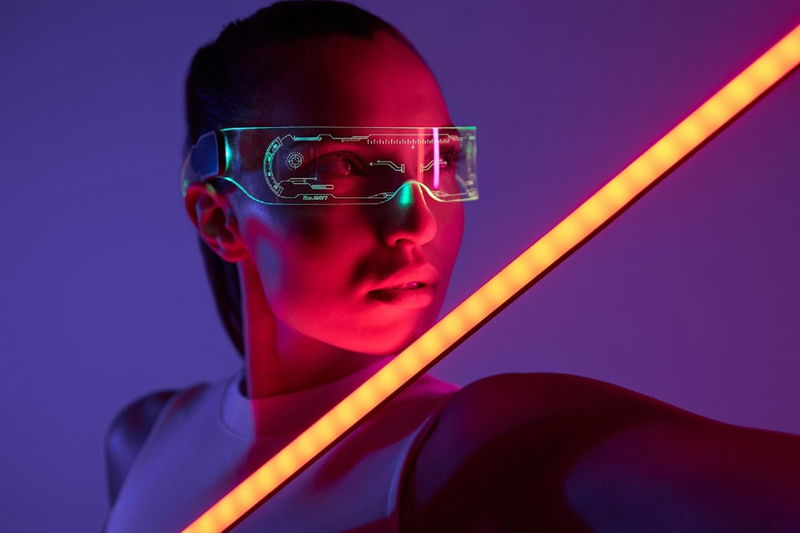
Manufacturing ERP (Enterprise Resource Planning) is a software program that can only be used by companies whose primary functions revolve around manufacturing. Many manufacturing companies have very specific requirements. These modules include planning, management, and procurement, among others.
These are the requirements for manufacturing ERP Systems. In other words, Manufacturing ERP is a more advanced version of the ERP system. It is focused on streamlining and automating all manufacturing activities. It employs the same proven ERP principles to improve the efficiency of the manufacturing industry.
What Are The Features of Manufacturing ERP you Need to Be Aware Of
Manufacturing is more competitive than any sector, and this is impacting core business model manufacturers around the world. It would be best to control all aspects of your manufacturing operations to adapt to today's agile supply chains.
Spreadsheets are obsolete once your production facility reaches an endpoint. ERP software will tell you whether your production facility can continue growing. For manufacturing business efficiency processes, it is necessary to buy dedicated ERP software.
Let's start by reviewing key features that every manufacturing-focused numerous organization should seek in ERP inventory management modules.
Below is a List of The Products on The Market
Before we get into the details of the ideal manufacturing ERP, let us first examine the available ERPs. These ERPs can be divided into:
Tier 1: Multi-billion dollar corporations can use these solutions if they have a decentralized, complex, and diversified organizational structure. These functions are complicated and require multiple steps before they can be performed.
Tier 2: Tier 2 ERP solutions are best for medium-sized enterprises/companies specializing in one industry. These vertically integrated systems rely on software integrations from outside parties to offer capabilities relevant to a given industry. The first year's ownership fees are $50,000. Tier 2 ERPs include, for example, Sage and Microsoft.
Tier 3: While Tier 3 ERP solutions might seem most intuitive, they aren't ERPs. These solutions are limited in their ability to perform related operations and focus on certain business functions like accounting. Tally, Quickbooks Desktop, and MYOB Desktop are just a few examples.
The Tier 2 and Tier 3 ERPs have a larger market share than Tier 1. These ERPs are popular because they offer lower prices and a wider selection. The value of an ERP is more than its price. How do you select the right manufacturing ERP for your business benefits? Let's begin with the list of manufacturing domains that ERP should cover.
Production Supervision And Quality Assurance
Manufacturing ERPs focus on production processes. It can also assist with accounting and related activities. It allows you to connect with your CAD software (to synchronize your bill of materials), plan projects, and generate quotes.
It should be coupled with your attendance management software to enable labor management and timesheet monitoring. Manufacturing ERPs will offer production-oriented features like total quality management (TQM) and statistical process control (SPC). A bird's eye view will allow you to monitor the progress of the operations on the shop floor.
Order Processing and Online Shopping
It is vital to be able to sell online if you want to use eCommerce capabilities. Manually accepting orders in today's digital world is not a good idea. This can cause confusion among staff members, increase operating efficiency, and make it easier for them to do their jobs. To ensure smooth user experiences, you should examine ecommerce.
This includes product bundling, shopping cart-based marketing, and other related services. It should be possible to integrate secure gateway integration and synchronize orders from 3PL partners. We recommend that you offer customers different payment options.
Inventory Management
The Inventory module in ERP systems allows you to track and adjust your inventory as needed. Companies can monitor stock levels for a variety of products using this module.
The inventory management module can monitor outgoing and inbound stock for various soaps or shampoos. The software predicts how long it will take for all inventory to be sold out.
Purchase Management
The ERP system's Purchase module handles the procurement of raw materials needed to produce the products. This module is vital for ERP manufacturing companies as it provides valuable information like vendor details, pricing details from software vendors, purchase order creation and tracking, and a Bill of Materials.
The purchase module can help companies manage warehouses and inventory better when used with the ERP's inventory module. This module is available in several versions that allow companies to track products at different stages of production and pinpoint their precise location.
Product Return Authorization
RMA is an agreement between the buyer and seller to return the item. Customers can get their money back or a credit equaling the purchase price. When a customer buys a product/brand, RMAs can be a great way of building trust. Customers can also return unfit or damaged items easily, ensuring a positive customer experience.
To resolve the issue, the customer can contact the seller by phone or email. Many brands ship products with pre-paid returns labels. The warehouse management system of sellers must consider returns. If the item is in good condition and can still be used, ecommerce stores may offer to return it. They can store the item in the nearest hub for future orders. This helps reduce losses and keeps old stock from building up.
Modern inventory software allows you to create your RMA and general returns policies. This allows automated approval of returns. This policy framework will retrieve the item condition and any other information. It is essential for a seamless user experience. This simplifies the returns processing accounting.
Manufacturing Financial Management and Accounting
Manufacturing companies need to be able to calculate their accounting costs accurately. It is directly linked with all physical activities. ERP integration systems will provide deep insight into features like activity-based costing or real-time data. Analyzing profitability can be done at different production volumes. It should support standard functions like forecasting, budgeting, and accounting.
You should integrate accounting software using Tier 2 or 3. As a rule of thumb, focusing on features closely connected to the production process is best. Accounting software can be used separately.
Supply Chain Management
As supply chains face volatile conditions, Supply Chain Management is an important area to be considered. Businesses must be more flexible when dealing with suppliers, vendors, raw materials, suppliers, and products.
You may need multiple functionalities depending on the size of your company and business requirements model. These include bill-of-materials configuration and dynamic editing, creating a request to proposals (RFP), and a self-service portal for channel partners and other stakeholders. Your system should be able to support models such as Procure-to-Pay (P2P), Order-to-Cash (O2C), or Record-to-Report (R2R) to streamline the flow and finance of goods and money across the supply chain.
Logistics And Transportation
Today's business owner demands that nearly all companies use multiple logistics commitments to provide customer service and meet their customers' needs. A properly-designed ERP system should allow integration with third-party logistics companies. This will allow you and your customers to select the right 3PL partner to fulfill orders. This is crucial if your e-commerce store sells products. Customers desire to be able to select their preferred partner for manufacturing in real time.
If you have vehicles, fleet management capabilities may be an option. All enterprise resource planning (ERP) modules should be integrated into your ERP.
Materials Management
The solution should provide insight into material management to complement your inventory management system. This involves using barcoding and RFID systems for consumption rate budgeting, inventory monitoring, and work tracking. Material requirement planning requires consideration of process-specific parameters like gross wastage. This should allow for extensive configuration. This will enable you to get the most out of the package without returning to spreadsheets.
Although we have already covered the main functions of your ERP for manufacturing, there are many more. You should also consider deployment time, learning curve quality and duration, training quality, compliance with ISO norms, and compliance with ISO norms. Review all products available based on these features before making informed decisions. This article will help you understand ERP manufacturing in its various components.
Cost-Effective
An ERP solution is a great investment in your manufacturing company, even though it might initially seem costly. Long-term efficiency gains and lower costs will offset the cost savings.
An ERP for manufacturing can streamline your workflow and give you real-time insight into every step of the manufacturing process, from inventory to logistics. This allows you to see the entire organization from one place and gives you complete control over your supply chain. This improves productivity and the quality of your output.
Making Decisions Based on Data
Many manufacturing companies need help to gauge customer demand, so they end up stocking too many or too few products. Overstocking can lead to warehouses needing more support, increasing logistics costs. Stock running out could lead to stock shortages and other competitors taking advantage. These can harm a company's financial health and lead to many operational problems.
Manufacturing ERP systems can be used to predict and analyze demand over time. These forecasts can be used to plan inventory and manufacturing activities and avoid overstocking.
Increased Security
As the world becomes increasingly data-driven, protecting your data is more important than ever. Data leakage and perversion can be caused by combining different technologies and software.
The ERP system eliminates data theft and corruption. All your data are securely stored in a central database with advanced access controls. You can control who can access what data, depending on their age and the nature of your work.
An ERP system for manufacturing provides superior data protection that can help you avoid malicious cyber attacks. You will receive regular updates from your service provider to keep you updated about new episodes.
Automation Increases Efficiency
Automation is changing the way that manufacturing companies use ERP systems.
ERP systems allow companies to automate repetitive tasks by setting triggers at key points. The software allows companies to automate repetitive tasks and redirect manual labor to more difficult tasks, increasing productivity.
Automation reduces the risk of human error. Automation has been one of the most important new frontiers over the last few decades. We have just scratched the surface. It is not an exaggeration.
Increased Team Cooperation
As companies grow, they often adopt a silo culture. This is when maintenance teams work in isolation and seldom collaborate. This can lead to incoherence, clarity, and consistency when all data has been compiled.
ERP software for manufacturers can tie your entire solutions organization together. Each dedicated team can see what's happening in the company and work together toward a common goal. This improves coordination and reduces disarray. This will impact your company's overall productivity.
Basic ERP Modules
Order Management
As the name suggests, the sales module helps companies keep track of all sales-related activities. When there is an inquiry, the sales expert team logs into the module and completes the required details.
The sales module will enter important data as the case develops, including project quotes, service agreement details, and tax bills.
Any organization that makes data-based business environments needs this real-time information. This data is then converted into reports regularly reviewed by the ERP system to chart the company's future actions.
Finance Management
The finance and accounting module handles all accounting functions. It tracks the company's balances and expenses. This module also records data related to various audits performed throughout the company.
Management of Client Relationships
Customer Relationship Management (CRM) tracks all interactions between customers, companies, and touchpoints. It tracks details like email chains, meeting minutes, and contractual agreements.
CRM can be paired with sales, making it a powerful tool that helps businesses close more deals and increase sales.
Modules for Manufacturing ERP
Operation Manager
Operation is the heartbeat of any manufacturing company. It is the heartbeat of a company. An ERP for manufacturing must include an operations management module that manages all manual processes.
A smooth supply chain can be achieved by well-run operations management. Customers receive their products on time and without delays. This improves revenue, reduces costs, and enhances the customer experience.
Project Management
Businesses that deal with multiple products or a single production line can use a project management system as an alternative. This is also important for companies that produce different items in small quantities. An ERP for Manufacturing will allow you to manage agile manufacturing projects using a variety of data-packed dashboards and analytics reports.
To get accurate and real-time information about project progress and forecasts, you will need to be able to connect to cyber-physical systems like AS/RS, barcoding, and attendance management software.
System for Managing Human Resources
The ERP system's Human Resources module makes human resource management easier. It tracks attendance and monitors performance against predetermined KPIs.
An ERP system includes an HR module which eliminates much of the paperwork required by HR departments. The company doesn't have to purchase separate HR management software, then worry about how to connect it with the ERP.
Asset Management
Asset management is becoming increasingly important. This term is now being used in greater detail. It used to be limited to the dates of purchase and commissioning as well as the maintenance costs. This is no longer the case. Asset management modules can be used to monitor and plan for asset health and capacity. They also guide you in the process of considering repairs or other spares.
These applications also have advanced functions like capital project management, energy management, and computerized maintenance planning. Searching for products that track production assets efficiently is also possible.
What is The Distinction Between Standard And Manufacturing ERP?
An ERP system is a mixture of generic and highly verticalized solutions. Each solution can be customized at different levels. Although the options seem similar to production-oriented companies, there are many variations.
An ERP for manufacturing can be greatly diversified to suit the needs of different production industries. How can you know if it works?
Your ERP option will depend on the organization's maturity, size, nature, competition, government policies, and customer affinities. We'll explain the differences and help you select the best Cloud ERP system.
This article will discuss why cloud-based ERP systems are essential for modern production planning models like lean manufacturing. Let's get started.
Standard ERP vs Manufacturer ERP
Original MRP (Materials Requirements Planning) solutions were used to develop ERPs. They can adapt to changing requirements and offer an integrated suite that includes HR, accounting, and performance management.
New ERPs (Tier 1, 2, and 3) were created focusing on manufacturing. There are two options: highly customized solutions tailored to manufacturing (at a premium price) or a production-focused ERP suite that offers a reliable, cost-effective solution.
Production-based companies can be modified to meet diverse requirements. To meet additional requirements, you can also choose third-party integrations. Let's see how we can choose between a standard or manufacturing ERP.
There Are Many Production-Specific issues that Manufacturing ERP can handle better than a Standard ERP. This section will address common issues that ERP-backed manufacturing operations can easily solve.
Manufacturing Defects
Poor manufacturing can result in product defects such as poor fit, finish, or inability. Manufacturing defects can also affect market prices. Manufacturing defects should be eliminated at the production stage using ERP-based operational strategies like Total Quality Management (or agile manufacturing). These types of defects will be minimized.
Incorrect Sales Forecasting-Led Production Goals
Failing to forecast sales is one of the biggest problems that businesses face all over the globe. Businesses are forced to acquire additional inventory called buffer or safety stock.
Companies can reduce inventory by accurately forecasting sales and using lean manufacturing methods such as JIT (Just in Time). This will reduce overheads such as inventory carrying costs, storage damage and theft, and other costs.
Idle Workstations
Any production-based business intelligence will need more efficiency. Inefficiency can cause revenue loss and hinder productivity. This indicates inefficiency across multiple areas, including sales forecasting, inventory management and logistics, and PPC. This is the most important area of lean manufacturing that needs to be eliminated.
Idle Workers
This is an indication of a serious failure to utilize human resources. It is equally alarming to see idle workers. They can decrease the efficiency of other workers and increase overheads.
Waste Produced During Therblig
Therblig is a collection of 18 basic motions that form the basis of most manufacturing processes. A motion study is often done using a camera to eliminate unnecessary movements. This is useful for quality control as it can identify unneeded movements associated with quality defects, misplaced parts, or faulty assemblies.
Material Waste During Material Handling
This can lead to a loss of time and misplacement of logistics priorities. Undesignated places can lead to a waste of technical resources and real estate blockage.
Inventory Loss
Inventory wastage can occur for many reasons. Economic backlashes can also cause inventory wastage. While inventory risks cannot be eliminated, they can be reduced by intensive audits and efficient utilization.
ERP Research must integrate all factors to provide a complete overview. Manufacturing is multi-organizational and requires access to all stakeholders.
Manufacturing businesses need an ERP solution that is flexible and adaptable to their unique needs. There may be better choices than standard ERPs because they cannot customize manufacturing capabilities.
Benefits of Implementing Manufacturing ERP within Your Organization
An organization can reap many benefits at different stages of its implementation. Here are some things you can expect:
- Software-induced elements can improve production and reduce inefficiencies.
- Human resources will be freed from unnecessary burdens once the redundancies are sorted out.
- This will lead to higher product quality, faster time to market, better margins, greater visibility of inventory (transparency), and can even help with future planning.
- Your business processes will be stronger because your products are more valuable than money over time. The strategy should focus on increasing the product's value and not raising its price. This will increase customer satisfaction.
- Manufacturing ERP reduces the environmental impact by reducing waste and environmental damage.
Modern ERP systems are more flexible than MRP systems. When implementing a process manufacturing sector-specific ERP solution, the solution must be tailored to manufacturing operations rather than follow an all-inclusive approach. An inventory management system can be more cost-effective than an ERP system if chosen well. This article will explain the differences between manufacturing ERPs and standard ERPs.
Conclusion
Any industrial company's backbone is unquestionably an ERP system. It connects all company departments and provides all information needed to run the business effectively, efficiently, and sustainably. It can manage customer orders, client relationships, procurement, PPC, and inventory management. It allows you to track all aspects of your business in real-time.
The right manufacturing software solution is critical to the success of your business. It can transform your supply chain. Enterprise resource management (ERP) software could benefit your company.