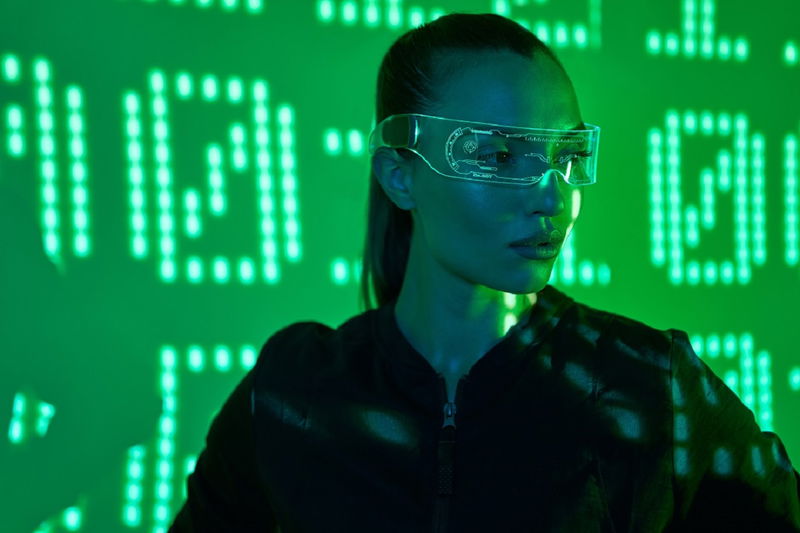
The manufacturing industry constantly strives to improve, identify efficiency, overcome obstacles, and find new ways of doing things. All the trends we have predicted for 2023 support this goal. Manufacturing industry trends in 2023 will continue to be driven by technological advancements, the needs of the marketplace, and business objectives.
The COVID-19 pandemic will continue to impact manufacturing in 2023. Some of the trends from 2022 are likely to carry on, but new challenges and opportunities await. Manufacturing trends in 2023 will, in part, be the result of the difficulties that have been faced in recent years. Technology, automation, and connectivity will continue to solve problems while presenting new opportunities.
The manufacturing industry is a crucial contributor to the global economy. Manufacturing trends are characterized by innovations that improve productivity and sustainability throughout production. In the manufacturing sector, the significant trends include factory automation, additive manufacturing, and artificial intelligence.
In the wake of the COVID-19 epidemic, manufacturers are now looking for ways to increase productivity while reducing human resources. Startups and scaleups develop intelligent sensors, wearables, and immersive tech gadgets to eliminate the requirement for workers' physical presence. Businesses are switching to greener energy and sustainable materials to reduce their carbon footprint.
Manufacturing is less visible to the general public than other industries, such as tourism or hospitality. The global pandemic caused the most severe disruption to the manufacturing industry in the past decade. A strong recovery has begun - according to a report, global growth is expected to reach 18.2% in 2023.
The key to changing the manufacturing landscape is resilience. As industries recover, this theme will continue to be a driving force. A survey of 200 C-suite executives at manufacturing firms revealed that 68% had listed increased resilience and agility among their top priorities for the next few years. Continue reading to learn about the major trends that will shape the future of manufacturing.
Ten Manufacturing Trends
1. The Smart Factory is Changing the Way We Make Things
It has existed for many years. The concept of "smart industry" or "smart factory" has been around for a long time. Still, it's seen a recent surge in popularity. "Industry 4.0" is a broader movement transforming production and operations in Europe, North America, and China.
The first and second Industrial Revolutions are associated with steam-powered mechanization and assembly line development. In the third industrial revolution, computers were introduced into manufacturing. The push for automation continues with technologies like IoT (Industrial Internet of Things), machine learning, AI, and advanced analytics.
Smart factories, as an example, could generate $160 billion of value for the automotive industry by 2023. Automotive manufacturers estimate that about one-quarter of their factories will become intelligent factories at the start of 2023. The industrial Internet of Things is a critical component of Industry 4.0.
IoT is based on connected sensors and machines to create a comprehensive data picture of the manufacturing process to help improve decision-making. Only 10% of manufacturing companies had IoT implemented at the beginning of 2020. By 2025, this number will rise to 50 percent. Some of the markets are already valued at more than $200 billion.
The amount of data businesses generate will explode with the increasing number of connected devices. Enterprises with advanced IoT systems have already found that one assembly line causes up to 70 terabytes per day. This needs large amounts of data to be transmitted, which also drives the rapid growth of 5G. The 5G standard offers speeds up to 10Gbps, wireless connectivity, and a near-zero-latency. This allows for a new level of flexibility in high-speed manufacturing.
Recent forecasts predict that the manufacturing industry will have at least 22 million 5G devices by 2030. Another study estimates that 5G will unlock $605 billion of revenue for manufacturing companies. Audi, a 5G early adopter, has contracted with Ericsson for advanced automation powered 5G in their production laboratories.
2. AI, Machine Learning, and Advanced Analytics Increases Efficiency
The typical oil rig contains more than 80,000 sensors that provide data on process parameters, such as temperature, pressure, and flow rate, to the status of machinery and equipment.
Data allows remote monitoring and focused manufacturing. But those sensors generate, on average, about 2 terabytes per day, which is far beyond what conventional data analysis methods can handle.
Because of this, advanced analytics powered by AI, machine learning, and deep learning are on the rise. In the five years before 2024, earlier projections predicted an eight-fold increase in AI investment for manufacturing. They also projected a three-fold surge in advanced IT like cloud computing and analytics.
In 2022, almost a quarter (24%) of the top manufacturing companies had already adopted AI solutions. By 2023, that number had risen to 79%. AI is being used in manufacturing daily in Europe. In Italy and Germany, this adoption rate was 80%.
The US, Japan, and Korea are behind in advanced manufacturing at 64%, 50%, and 39%. Most of the AI has been deployed in automotive, heavy equipment, electronics, chemical, and metals industries. AI-based decisions are used in these industries for quality control, supply chain management, production line inspections, and inventory management.
Machine learning and advanced analytics, defined as an autonomous or semiautomatic examination of data using methods other than traditional business intelligence, have been adopted at a higher level by manufacturing companies. Two-thirds attribute significant revenue generation or savings to these technologies.
The manufacturing analytics market will be valued at $28,4 billion by 2026. This is a significant increase from the current $ 8.45 billion.
3. The Digital Twin and Predictive Maintenance Reduce Errors
Equipment failures in manufacturing can be costly. For example, a petrol plant compressor failure can cost up to $2 million per day. Studies show manufacturers lose $50 billion annually due to unplanned downtime.
Combining IoT with Big Data Analytics allows for sophisticated algorithms that can predict failures in advance. Predictive maintenance has been shown to reduce machine downtime between 30% and 50%. It can also increase the life of machines by up to 20%.
The pressure of last year's shutdowns has only increased implementation. 35% of large US manufacturers are already using predictive maintenance methods. Airbus was an early adopter and helped its airline clients implement advanced predictive techniques.
Airbus and GE partnered this year to develop AI and ML-based software for predictive maintenance. This will allow Airbus to predict and replace part failures promptly to increase safety and profitability.
The market for Predictive Maintenance Solutions was worth $3.9 Billion at the end of 2022, and it is estimated to reach $13.9 Billion by 2026. Digital twins are another sub-trend that is part of the evolution of intelligent factories. Digital twinning is a simulation-based method that allows manufacturers to make better decisions by using a digital representation of an item.
A digital twin in the context of a smart factory can be either a component (like a tire for a car) or an entire product (such as a whole car with its thousands of subsystems and software). You can have a complete manufacturing process (with several assembly lines and workstations).
Digital twins can be used for various applications, from predicting product life based on a particular design (as GE demonstrated with jet engine aircraft) to optimizing the operations of entire factories through simulations.
By 2023, it was predicted that half or more of large industrial companies would be using digital twins. Businesses are predicted to save up to $1 trillion by using digital twins.
Want More Information About Our Services? Talk to Our Consultants!
4. The Supply Chain Restructuring is Changing the Places Where Products are Made
According to North America and Europe, the same demand for resilience drives dramatic changes in sourcing and shoring.
Globalization and the quest to reduce costs in all business areas have driven lean and offshoring supply chains for decades. However, Covid-19 is now causing disruptions that are reversing this trend. Reshoring began in 2010, and it is now a growing trend.
Reshoring has been driven by several factors, including the increasing cost of labor in offshore countries, the rising costs for shipping, and the growing pressures from social groups and regulators on sustainable logistics and sourcing.
These forces have significantly altered the sourcing landscape. KPMG conducted a study that revealed Canada has one of the lowest manufacturing costs in the world. This is far ahead of other countries, such as China and India.
Reshoring is expected to increase from 58% of US manufacturing firms in 2022 to 88% in 2023. Reshoring has an estimated $448 billion economic impact in the US. The location of a manufacturing facility does not limit strategic shifts.
The new strategy also includes new approaches to sourcing raw materials and parts. These include near-sourcing and multi-sourcing.
This is partly due to the excessive reliance on just-in-time inventory management (especially within the automotive industry) or, depending on whom you ask, a total misunderstanding of lean manufacturing principles.
The philosophy of inventory management, known as Just-in-Time, focuses on ensuring that the parts needed for a production line are there precisely at the right moment. To avoid expensive inventory costs, the goal is to minimize waste.
By design or misapplication, pre-Covid practices have led to a shortage of computer chip products in more than 169 industries. This global shortage is expected to continue at least through the year 2023.
5. As Commerce Evolves, Microfactories Emerge
Manufacturers are also beginning to feel the effects of this global pandemic. The micro-factory is a small and highly modular manufacturing setup that uses cutting-edge technologies like robotics, artificial intelligence, and big data to achieve hyper-autonomous production.
Microfactories combine all smaller trends, including the intelligent factories trend and the supply chain restructuring trend. In the quest for resilience, manufacturers have tried to increase their flexibility to handle small parts runs and quickly switch production lines when assembling new models.
Arrival, a startup manufacturing electric vehicles in 2020, made headlines when it announced a deal worth $110 million with Hyundai. It also received an order from UPS for 10,000 vans. Arrival builds its vans in micro-factories that are a fraction of the size and cost of conventional factories.
It has announced it will build over 1,000 micro factories worldwide before 2026. Microfactories can reduce time to market, improve efficiency, and change production more quickly than ever by harnessing IOT, robots, and AI.
Read More: Why ERPs are Advantageous for Manufacturing Businesses
6. To Combat the Labor Shortage, Manufacturers Are Raising Wages and Reskilling Workers
A recent Deloitte study estimated that the shortage of skilled manufacturing workers would reach 2.1 million by 2030. According to the survey, 38% of respondents said that recruiting new employees is their top priority in terms of production staff for 2022.
Finding talent has become more challenging for manufacturers than it was in 2018. A survey by The National Association of Manufacturers in August 2022 revealed that 76% of manufacturers said recruiting was their biggest challenge. Manufacturers are increasing pay as a way to attract talent.
Almost three-quarters of manufacturers stated that they would increase wages above an average of 3 percent by 2022. This is on top of the increases in 2021 when new hire wages grew by 6.8% and industry wages grew by 3.2%. The manufacturers are also investing heavily in retaining and upgrading their existing workforce.
According to a survey, 31% of respondents ranked employee retention as a priority, while 13% cited reskilling. According to the Manufacturing Institute, young workers are attracted by employers willing to invest in and train them. Manufacturing employees under 25 are more likely to stay with an employer offering these opportunities.
The skills of the manufacturing workforce will change as AI and robots become more prevalent. McKinsey forecasts that the demand for manual and physical skills will decrease by 30 percent over the next decade. The market for technology skills is predicted to increase by more than half.
In contrast, the need for high-level leadership and social/emotional abilities will rise by 30%. MxD, Manufacturing x Digital, has released a guide to help organizations reskill their workforce. The companion guides businesses in upgrading 247 jobs, including many in cybersecurity.
Another example is the ACE Program: America's Cutting Edge, launched by The Institute for Advanced Composites Manufacturing Innovation. This program uses virtual training to help teach machining skills. The training is entirely free.
7. DEI Initiatives Recruit Minorities And Women
DEI initiatives are also a priority for manufacturers when recruiting new talent. The Manufacturing Institute reports that 64% of manufacturing companies highly emphasize diversity and inclusion. The National Association of Manufacturers (NAM) and Manufacturing Institute created a Pledge of Action to improve equity and parity in the industry for minorities.
Manufacturers promise to take 50,000 concrete actions to achieve this goal in the pledge. They will also create 300.000 pathways for minority groups by 2030. Women are underrepresented in the manufacturing industry. Women make up less than one-third of manufacturing professionals.
Women are also 1.8x as likely to quit their manufacturing jobs than men. Zippia is a website that helps people find jobs. It also reports the underrepresentation of non-Whites in this industry. Only 11% of the workforce is Hispanic. 10% are Black, and 6% are Asian.
Dow, a manufacturing company in the United States, has made DEI a priority when hiring and retaining employees. The company launched diverse interview teams and an equivalency for military degrees program. It also has inclusive hiring standards. The company also invites employees to join Employee Resource Groups for different races, age groups, disability types, and sexual orientations. Over 18,500 employees are a part of one or more groups.
Since 2016, the company has been listed on DiversityInc's Top 50 Companies for Diversity and received a 90 percent rating on the Corporate Equality Index, published by Human Rights Campaign.
8. Governments and Private Manufacturers Push Industry Towards Carbon Neutrality
According to Research data, the manufacturing and industrial sector is responsible for 24 percent of the greenhouse gas emissions in the United States. Around the world, industry is responsible for one-fifth of carbon dioxide emissions.
More than 20 percent of the largest companies in the world have committed to achieving net-zero emissions of carbon dioxide by the year 2020. In the manufacturing sector, we can see a similar trend. The manufacturing industry, as well as government agencies, is pushing towards carbon neutrality.
According to the EPA, adopting sustainable practices has several advantages for businesses. The EPA cites several benefits, including building public trust, increasing productivity by reducing waste, and investing in the long-term viability of companies. Dalmia Cement was the first global manufacturer to pledge its commitment toward carbon neutrality in 2018.
Goals include achieving net-zero emissions by 2040 and running 100% on renewable energy by 2030. The company also wants to transition from gasoline vehicles to electric ones significantly. Klockner & Co is one of the world's largest steel and metal producers. They aim to halve emissions by 2030. The company launched Nexigen, a sustainable steel and metal brand, in September 2022.
Klockner & Co categorizes steel into five different levels, ranging between START (which has a CO2 footprint of up to 1,750kg per metric tonne) and PRIME (which has a CO2 footprint no greater than 400 kg per metric tonne).
It is said that by 2025, 30% of its products will be exclusively sourced from sustainable sources. In addition to private efforts to decarbonize the industry, the US government is also funneling funds to this sector. The Department of Energy, in April 2021, announced a $22,5 million program for projects that reduced manufacturing emissions and energy usage.
The White House released several initiatives in February 2022 intending to clean industrial processes. The "Buy Clean Task Force" will increase federal purchases of cleaner building materials and launch an emission-based policy to regulate dirty aluminum and steel.
9. Cyberattacks Cause Downtime And Information Leaks
IBM's X-Force Threat Intelligence Index ranked manufacturing as the sector that would suffer the most cyberattacks by 2021. For the first time since 2005, attacks on manufacturers outnumbered attacks against financial institutes. PwC reported that 49% of manufacturers listed cybersecurity as one of their biggest challenges in the coming two years.
IT experts say that manufacturing organizations make an attractive target for hackers due to their low tolerance for downtime. Cybercriminals are exploiting supply-chain issues that have arisen in the aftermath of COVID-19 to bring down businesses already suffering. Manufacturers are more susceptible to attack now as Industry 4.0 takes over. Cybercriminals may target software, firmware, or hardware.
IBM's X-Force Threat Intelligence Index shows that 23% of attacks on the industry in 2021 were ransomware. A ransomware attack on Denso Corporation in March 2022 resulted from a group specializing in manufacturing automotive parts for companies such as Toyota, Mercedes-Benz, and Ford. Hackers then released stolen Toyota information. The hackers then leaked stolen information about Toyota.
Nvidia is a leading manufacturer of graphics processing units and chips. In February 2022, the company was targeted. The attack was carried out by ransomware called Lapsus$, which released Nvidia schematics, drivers, and firmware. Employee credentials were also leaked. Over 50 organizations formed the Cybersecurity Manufacturing Innovation Institute in 2020 to address these increasing cybersecurity threats.
This $111 million public-private partnership is officially housed at the University of Texas at San Antonio. The Department of Energy plays an important role. The organization has announced that the Texas Manufacturing x Transformation hub will be built in February 2022. This hub aims to prepare 1 million manufacturing employees for cybersecurity by 2026.
10. The Additive Industry Has Gone Mainstream
3D printing (also known as additive manufacturing) was a new technology for many manufacturers. It is now an established method for saving money that can be applied to various applications.
3D printing allows manufacturers to produce parts on-site and avoid delays in the supply chain. The production of fixtures and jigs can be brought in-house, which saves time and money. Also, short-run productions, metal casting, and molding are possible.
Pankl Racing Systems is a maker of mechanical components for planes and cars. They used custom 3D-printed jigs. This process was 12x cheaper and 48x quicker than CNC-machined jigs.
Metal fabrication is a growing industry that uses 3D printers. The metal 3D Printing Market is predicted to increase at 19.5% CAGR through 2028. The total market value will reach $11.6 billion. The Mantle is a startup offering 3D printers that can eliminate or drastically reduce the time and money spent on steel toolmaking.
According to the website, their technology reduces lead times by 80% and costs by 50%. The use of additive manufacturing to create unique products is becoming time-saving and innovative. Limber Prosthetics and Orthotics, based in San Diego, digitally scans amputees' limbs and uses 3D printers to produce artificial limbs within hours.
The cost is about one-tenth of the price of conventional artificial limbs. 3D-printed bike helmets are made custom to the head shape of each biker. Kav manufactures bike helmets with a 25% higher impact resistance than the current safety standards.
These helmets offer enhanced safety and are made with a thermoplastic polyurethane polymer (TPU). They also contain carbon fiber. The material is 20% lighter and stronger than other materials. It can withstand temperatures as low as -30degC and even up to 70degC.
Final Word
In 2023, the convergence of IOT with advanced analytics and automation will lead to new trends in intelligent automation, predictive maintenance, and digital twins. All of this adds up to the megatrend for intelligent factories. The pressures relating to the supply chain have also been significant drivers of change. They have led to major shifts in the design of supply chains, globalization, and production models such as micro-factories.