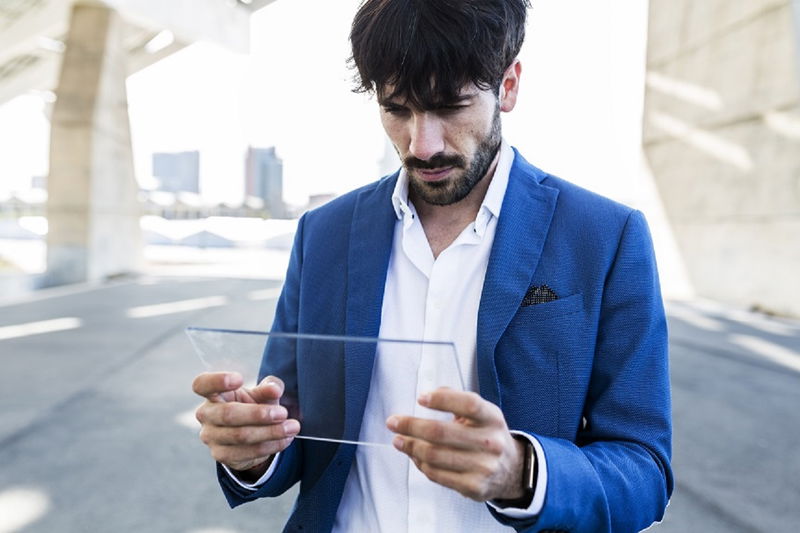
By planning routine maintenance and conducting routine inspections, preventive maintenance is a strategy used to increase the lifespan of equipment, structures, and other assets. Preventive maintenance also lessens the need for reactive maintenance, which includes expensive interruptions, unplanned equipment failures, and reactive repairs brought on by unplanned interruptions and equipment breakdowns.
Businesses can better plan and schedule preventive maintenance jobs utilizing real-time operating data by utilizing a computerized maintenance management system (CMMS) to improve their preventative maintenance methods. Preventive maintenance refers to scheduled tasks that are organized ahead of time to prevent unscheduled malfunctions from occurring in the future. Simply put, its goal is to fix items before they break.
Examples Of Preventive Maintenance
Here are some best preventive maintenance examples.
Cleaning
Cleaning is vital for preventive maintenance plans because it keeps assets and equipment clean, which can save time and money. Maintain your equipment on a regular basis to keep dust and other particles from building up and requiring future costly maintenance or replacements. To prevent any potential issues in this region, stick to your cleaning schedule.
Lubrication
The majority of individuals agree that lubrication is a crucial type of preventative maintenance that reduces friction and wear on mechanical components, hence reducing the chance of premature breakdown or excessive part wear. Maintaining proper lubricant levels also lowers the expenses related to early component failure or excessive wear.
A way that proper lubrication can improve efficiency is by reducing the amount of energy that machinery needs to run on. In some cases, proper lubrication can increase the lifespan of equipment by protecting it from corrosion and other types of harm.
Repairing
Proper is crucial for extending the life of your assets and preventing more costly and time-consuming repairs. Maintaining your products on schedule will help them last much longer without requiring costly replacements down the road.Furthermore, by preventing the need to take an asset offline for major maintenance, you'll save both cash and hassle.
Replacing
Preventive maintenance can be accomplished by regularly replacing asset parts. This strategic approach to maintenance is often recommended for certain kinds of machinery and HVAC equipment.According to experts, however, specific asset categories such as machinery and HVAC (heating, ventilation, and air conditioning) should not be frequently replaced.
Software Update
Maintain all software's latest releases and versions with preventive maintenance software updates. As companies may fear new versions would compromise current functionality or introduce security risks, many wait to release improvements until their use can be fully assessed. However, not updating puts users at greater risk of identified and unknown hazards by not updating.
Evolution Of Preventive Maintenance Software
Preventative maintenance software dates back to its creation during the 1960s as part of the early phases of computerized maintenance management systems (CMMS). Their primary function was managing work orders, inventory, and equipment records.
Predictive maintenance, which employs sensors and other technologies to track equipment performance and forecast faults, became more popular during the 1980s and 1990s. Yet, this technique requires more technical know-how and costs than preventive maintenance methods. Preventative maintenance gained ground again as software processing power increased.
Mobile applications and web-based software have revolutionized tracking equipment performance and performing maintenance duties.
Software designed for preventative maintenance now includes scheduling, work order management, asset tracking and reporting, and analytics. Artificial intelligence (AI) and Internet of Things (IoT) capabilities are available to boost equipment performance further.
When To Use Preventive Maintenance?
Implementing the instructions from each asset or equipment manufacturer is the ideal way to decide on the inspection and scheduling of their assets or pieces of equipment. Preventive maintenance schedules help companies care for their support before they fail altogether.
Preventive maintenance ensures equipment like HVAC (heating, ventilation, and air conditioning), water, sanitation, electrical safety devices and other mechanical pieces comply with safety regulations while running at peak efficiency.Your equipment's needs will determine its requirements for preventative maintenance scheduling.
Advantages Of Preventive Maintenance
Preventive maintenance offers many advantages to businesses, industries, and individual equipment users when appropriately performed. Some of its main benefits of preventive maintenance software are as follows
Decreased Downtime
By preventing unplanned equipment failures from interfering with operations and causing delays, scheduled maintenance helps safeguard operations from such disruptions.
Extended Equipment Life
The lifespan of equipment and machinery can be substantially extended with routine maintenance and repairs.
Cost Savings
Even while there may be upfront costs, preventive maintenance can save businesses a substantial sum of money over time by preventing emergency repairs and replacements that would otherwise result in higher costs.
Increased Safety
Machines which are kept up with are less likely to break down and endanger workers or users.
Enhanced Efficiency
Regular maintenance guarantees that machinery and equipment run as efficiently as possible, which frequently results in improved performance and energy savings.
Types Of Preventive Maintenance
The four main types of preventive maintenance are:
- Time-based maintenance
- Usage-based maintenance
- Predictive maintenance
- Prescriptive maintenance
Time-Based Maintenance
Time-based maintenance adheres to manufacturer recommendations by occurring at predetermined calendar intervals. This system generates work orders as each deadline approaches, enabling immediate maintenance action to begin.
As part of your organization's time-based maintenance plan, include essential utilities, tools, equipment and technology necessary for its success.
Usage-Based Maintenance
Usage-based maintenance considers two factors when scheduling preventive maintenance jobs: the average operating hours and how long it has been since the last care.Utilization-based maintenance offers many advantages over time-based schedules, particularly setting an exact date and allocating resources efficiently.
Predictive Maintenance
Predictive maintenance gathers information through sensors containing pressure, temperature, humidity, vibration and security sensors.
Predictive maintenance sensors are typically installed on delicate equipment to provide data for predictive maintenance programs that can initiate work orders for inspection, repairs or upgrades as soon as they detect necessary inspections, repairs, or promotions are required.
Prescriptive Maintenance
Prescriptive and predictive maintenance have similar goals; however, modern technologies employing machine learning and advanced analytics allow predictive maintenance to anticipate and speculate upon events that could cause equipment breakdowns.
Artificial Intelligence can predict asset failure and the operational conditions that might precede it by analyzing operational problems, hazards, and equipment performance - helping you spend less on costly reactive maintenance as Artificial Intelligence becomes part of your machinery's daily life.
Prescriptive maintenance software assists with asset performance analysis, project results evaluation and recommendations, and automatically initiating and tracking maintenance work orders.
What Is Preventive Maintenance Software?
Software for preventive maintenance tasks is made to help businesses plan, monitor, and manage maintenance work in an anticipatory manner. By automating processes, generating schedules, and enabling inspections, this software lowers the cost of maintenance, asset downtime, and malfunctions.
Organizations can more efficiently and economically handle work orders, spare part inventories, asset information, and regulatory compliance with the use of preventive maintenance software. Software for preventative maintenance can increase an organization's asset longevity, dependability, and operational efficiency.
Also read: Maximizing Efficiency: The Must-Have Features of an Effective Maintenance Management Software
How Preventive Maintenance Software Helps?
Although maintaining records might be time-consuming, it's crucial to monitor the functionality and history of your machinery to keep it running well and prevent costly repairs.
Specifically made software for preventive maintenance tasks is the secret to extending the life of your machinery. This programme makes everything easier, from making work orders and keeping track of equipment efficiency to tracking progress against the budget and keeping track of it over time.
Scheduling
Scheduling work orders with software can help you finish activities quickly and avoid scheduling conflicts or overlaps for maintenance. Order scheduling becomes significantly easier for field technicians when CRM or ERP systems give them instantaneous customer booking data.
Preventive maintenance programs can also be implemented using information about the kind of work to be completed, client details, site-specific instructions or access route directions.
Tracking
Please maintain a history of each piece of equipment so that you can better understand when it might need to be replaced or serviced. Using this information, work orders can be made to guarantee that only necessary repairs or replacements are made.
Streamlining
A successful preventive maintenance programme can, at the absolute least, save your business money and time while making life easier for all parties involved, from management to staff. Because preventative maintenance software increases productivity and reduces equipment downtime, it is a wise investment.
Preventive Maintenance Checks
Making a preventative maintenance checklist is a wise move because regular inspections and service can prolong the life of your equipment and help avert unplanned problems.
No one can say that there is a single maintenance checklist that works for everyone; in fact, the items on it will vary depending on the specifics of your establishment or the machinery that has to be maintained.
Scheduled Preventive Maintenance
Scheduled service visits to clean, examine, adjust, test, and replace equipment parts and components are known as preventive maintenance. The goal is to prolong equipment lifespan and avert premature breakdowns. It shields it from potential premature failure and extends its useful life.
Schedules for preventive maintenance can vary depending on the type of equipment and level of risk involved, from simple visual checks every month to intricate overhauls every three months. You can make sure your equipment stays effective over time by developing and following a programme for maintenance and repairs.
What Does Preventive Maintenance Software Do?
Preventive maintenance activities often have other goals in addition to improving a company's productivity and simplifying equipment maintenance. These are merely a few of the duties you might expect a software application to perform.
Inspection
Inspection is the process of routinely inspecting machinery to look for possible problems, like performance threshold testing and wear and tear indications. The goal of evaluation is to find problems as soon as possible so that businesses may address them right away and save money on costly replacements or repairs. Best Preventive maintenance software can assist by automating checks, establishing warnings, and tracking performance information.
Servicing
Proactive maintenance activity is a priceless asset since it restores damaged or critical equipment to proper operational condition through servicing. To make this happen efficiently, these solutions include record-keeping tools, maintenance planning capabilities, and real-time performance monitoring features.
Reporting
Businesses need accurate and current information to monitor the functioning of their equipment, and preventive maintenance software may assist them with this task thanks to its extensive dashboards and statistics. These instruments give information about possible potential issues that need to be resolved, the operation of their equipment, and any more information required.
Preventive Maintenance Drawbacks
The following are the Drawbacks of preventive maintenance-
Time-Consuming
Compared to alternative solutions, preventive maintenance strategies may need more time. Utility companies without access to the right tracking technology that provide precise asset monitoring and history tracking may need to devote a substantial amount of time and money to the endeavor.
Demands More Resources
Teams that adopt preventative techniques typically require more resources over time because they handle more condition-based maintenance-related duties than teams that use reactive tactics.
Potentially Expensive
Purchasing the technologies required to maximize proactive approach to corrective maintenance operations might not be financially advantageous for smaller utility firms.
Organizational Challenges
Preventive maintenance services require keeping tabs on constantly shifting schedules and variables; this can be particularly challenging if your company still utilizes traditional practices.
Increased Mileage Costs
Assigning field technicians to customer sites often necessitates extensive travel time, incurring significant mileage expenses. This process can become highly costly without technology that optimizes routes for cost-efficient travel between jobs.
Conclusion
Cost-efficient Preventive maintenance programs can help businesses reduce downtime, boost productivity and decrease breakdowns while prolonging equipment lifespans. As with any program, however, companies must understand which circumstances and critical equipment types would benefit most from an established preventative maintenance schedule.
Carefully inventory all assets vital to the daily operations of your business, employee safety or environmental compliance. In addition, plausible causes of malfunction must be identified so preventive maintenance efforts can be closely tied with increased dependability.