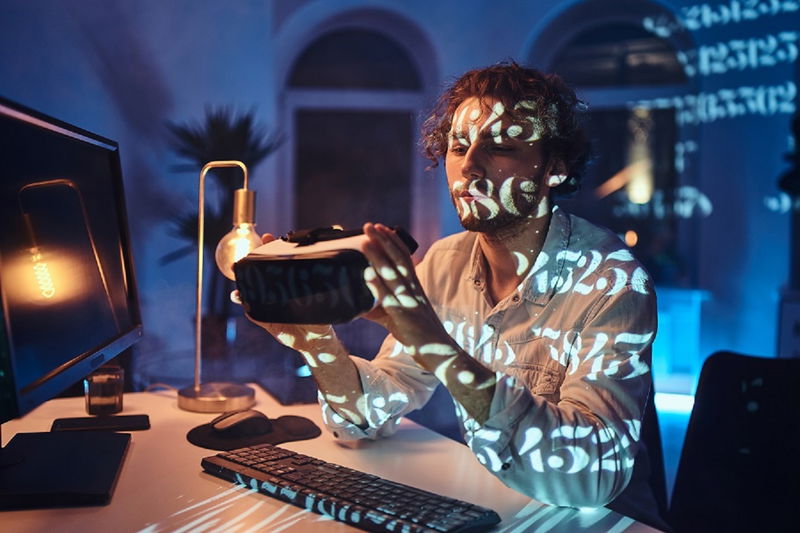
What Is ERP Inventory Management?
Inventory management with Enterprise Resource Planning (ERP) enables companies to manage all areas of their operations from a single platform. This encompasses logistics, finance, and planning. ERP inventory management solutions give the entire business access to real-time inventory data. This is a crucial capacity for businesses that want to expand, have intricate supply chains or processes, need advanced automation, operate in "just-in-time" mode, sell a variety of items, or want to get the most out of their inventory investments.
When selling things online, it is essential to have a dependable and scalable inventory management system. When scaling your online business and growing it, there are many things to consider. It can take time to choose suitable systems and processes. Making the proper judgments today and tomorrow is crucial-quarter two and year two. You must maintain efficiency as your company expands and becomes more complex. It cannot be easy to find new technologies or processes. The most expensive component of an investment is not the software or the application. The most costly aspect is frequent implementation. Project implementation is frequently the most expensive phase. Selling online requires software for inventory management. There are two types of software on the market. These options will be examined and compared to scale for rapid growth.
Which Is Better: ERP Or Inventory Management?
Inventory Management System
When you search online for inventory management software, you will find a website that compares the features and prices.
Your options fall into two main categories.
- A platform can be used with other media, such as an ERP or Supply Chain Management Platform.
- Software for inventory and warehouse management.
- A Full-In-One solution offers the best of both worlds and allows multiple processes to be managed in one program.
- A platform for inventory management that is specialized in this function can be integrated with much other software.
- You have two options: a program that does all but isn't specialized in one area or a specialized stack that integrates well with each other.
The Dangers Of Using An ERP
- ERPs, which can be all-in-one systems to manage everything, have limitations. Many ERPs need the settings that you need.
- A multifunctional device can challenge managing settings like channel account, quantity, and pick list. As a result, inventory errors, midships, and mis-picks will increase.
- A customizable reporting feature is another option that ERPs often need to improve. Although the provider will provide the data you need, it can often take time to customize sales channels and depends on the service level.
- Here you can identify potential problems in your company.
- Many companies then move to stacks that better suit their needs.
The Benefits Of An Inventory Management System
Your IMS will have all the features you require for your business so that you can feel more secure.
You have more control with a dedicated inventory management software program. You can modify channel settings, create pick lists, and get valuable reporting insights. This will make sure you get enough stock. This will reduce inventory errors like mis-picks or mis-ships.
You can choose which integrations to add to your stack. An all-in-one package keeps the outcome the same.
Each component of an integration stack can be tailored to your company. Each integration can handle one aspect of your company very well. This is more attractive to businesses than an all-in-one solution that only offers functional features but could be better.
An Integration Stack: Importance And Usefulness
Companies with an integrated stack will experience a higher ROI.
Each user is unique, so the setup is more straightforward and customizable. This level of detail is not possible with all-inclusive software packages.
When you clearly understand your requirements and are clear about what you need, it is much easier to create an integration stack.
Given the price, it might seem counterintuitive to spend the money and period of time to build an integrated stack. This shouldn't fool you. Remember the hidden shipping costs involved in implementation.
A stack of integrations allows you to pay only for the functionality you need, not extra features. This will help you save money over the long term. This will allow you to save money over time by avoiding inventory cost mistakes resulting from insufficient detail.
What Are The Major Functions Of An ERP Inventory Management System?
Consider the long-term potential of any new system: A system that touches so many areas of your business and takes time and effort to put in must be able to meet your current and future needs. You should only use systems that are limited in functionality and will be obsolete within three to five years.
Here are five steps that will help you find the right system for your business.
Step 1: Identify The Desired Outcomes
Make sure you consider the goals of your stakeholders and develop a business case. Strategic planning involves analyzing business trends, core competencies, and external opportunities.
Ask yourself these questions: How does the purchase of the proposed item align with long-term goals, both previously established and newly revised? What insights will it provide that are not available today to help us plan our inventory strategy?
Step 2: Identify The Project
Which data sources are required to integrate critical metrics into ERP inventory management software? What suppliers and partners will have access to the ERP inventory management solution? Make a list of all the capabilities and features that are required to achieve the desired result.
Step 3: Perform An ROI Analysis
Don't just focus on cost-cutting. Instead, think about how the investment will increase your company's profitability, efficiency, and customer satisfaction. Particularly, explain how technology will allow your business to grow by better managing its inventory.
Step 4: Draft A Vendor list
- Are the systems flexible, scalable, and easy to integrate?
- Are there any testimonials from other companies in the industry?
- What type of training is required? Is the company able to support training?
- Is there a free trial version or a paid version that can be used for testing purposes?
- How much does software cost upfront? Or monthly for cloud-based applications? How about maintenance?
- How long will it take before we are up and running again?
Step 5: Look Ahead
Use your chosen platform and deliver the new business system plan to your company; across every team member necessary. Ensure the information provided within the system notes is always accessible to those it is relevant to, in case they need to refer back to it at a later date.
What's The Difference Between WMS And ERP Software?
Warehouse Management System (WMS), Enterprise Resource Planning (ERP), and Enterprise Resource Planning Software (ERP) are frequently used interchangeably to refer to inventory management software for enterprises. ERP software can be used to manage warehouses, but they are different and have unique features. When talking with software providers, knowing the difference and definitions of these terms is essential.
WMS and ERP systems are essential for any wholesale or distribution business. Without them, it wouldn't work. This blog post will explain the differences and similarities between ERP software and warehouse management.
Warehouse Management Systems (WMS) track inventory movement within warehouses. It records the inventory items' activities, such as when they were received, put away, picked, packed, and shipped. WMS and ERP are different because WMS systems can provide real-time intelligence to optimize inventory movement in your warehouse. The system can generate reports indicating where each item should go based on historical data and trends. It also helps to determine the best location for product placement within a warehouse based on the shelf and bin utilization. Other functionality includes:
- You can set up stocking or non-stocking locations to display the inventory count. This allows you to separate a product available from a product allocated to an order.
- Ability to assign stocking locations priorities and ratings to make picking more efficient
- You are tracking the exact movement of your product from the shelf to the cart to specific stations, etc.
- Cross docking allows employees to ship and receive the product from one location without storing it.
- WMS systems, which control warehouse operations, are often standalone. They need accounting, customer relationship management, and other range of features necessary for an ERP system. WMS is often integrated with an ERP. Small firms don't need WMS functionality because many ERP packages provide built-in warehouse management capabilities.
Business activities in all areas, including accounting, order input, processing, purchasing, and inventory control management, are automated using enterprise resource planning (ERP) software. It also integrates eCommerce channel integration with customer portal relationship management. ERP software's primary purpose is to allow information to flow between all business functions. It is important to remember that ERP software can have many of the same capabilities and different warehouse and inventory management levels. An ERP system can track inventory items received, picked, packed, and shipped. It will also be able to manage bin, shelf, and location management, but it will need help to make recommendations for warehouse layouts. ERP software is a good choice if your business needs the best inventory management software. WMS functionality is typically included in ERP software but to a lesser extent. WMS and ERP are both parts of supply chain management. They are designed to assist companies in resource management that is as cost-effective as feasible. They can be used both on-premises and in the cloud and report real-time data in various ways. Each system and module has a unique price tag, which can be anything from a few thousand to hundreds of thousands of dollars. ERP software will include some WMS key features, but they won't be as complete or dependable as a genuine WMS. However, ERP software is often sufficient for small to medium-sized wholesale and distribution companies.
Warehouse management software is often more expensive than ERP software. This is why using the correct terminology when talking with vendors is essential. The requirements for warehouse management, shipping and receiving, inventory functionality, and WMS software are different. WMS systems are optional for some warehouses. They're meant to be used in complex operations and can be costly. Many cycle counts ERP systems offer the same functionality as WMS systems but at a much lower price. A well-designed ERP system should be capable of handling most inventory-level requirements, including essential warehouse management, at a much lower price. There are many levels of inventory management software. Understanding your business requirements is critical before looking for the right system.
Challenges Of Inventory Management
Inconsistent Tracking
It can be time-consuming, redundant, and prone to mistakes to maintain inventory across various programs and spreadsheets manually. An accounting-equipped central inventory management system can be even more advantageous for small firms.
Warehouse Efficiency
Warehouse management is labor-intensive. It involves many steps, including picking, packing, shipping, and receiving. It is important to complete all of these tasks efficiently.
Inaccurate Data
It is essential to be able to count your inventory at all times. No longer can inventory be counted only once per year using an all-hands-on-deck approach.
Changes In Demand
Customers' needs are constantly changing. You want to keep only a little inventory. This could lead to obsolete inventory that you are unable to sell. However, you need more inventory to fulfill customer demand. To compensate for changing demands, order strategies for core products and the technology to create an inventory plan can be helpful.
Limited Visibility
If inventory is difficult to locate or identify in the warehouse, it can lead to delayed, incomplete, or incorrect shipments. It is crucial to receive and locate the correct stock to ensure efficient warehouse operations and customer experience.
Manual Documentation
It is difficult and insecure to manage inventory using paperwork and manual processes. It is also difficult to scale across warehouses that hold a lot of stock.
Problem Stock
Specialized plans are needed for the storage and care of fragile and perishable stock. High-value inventory requires special loss prevention strategies and inventory control.
The Complexity Of The Supply Chain
Operations for inventory planning and management are strained by the daily changes in global supply networks. Wholesale distributors and manufacturers, who determine when and where your merchandise goes, need flexibility and unpredictability.
How To Manage Warehouse Space
It can be daunting to manage space efficiently. With inventory management platforms, you can plan and design warehouse spaces to better manage the delivery times of new stock. It can take into account important factors such as space availability. Find out more about the distinctions between inventory management and warehouse management.
In Order Management
Avoiding overselling and stock shortages is a necessary component of effective inventory management. Using historical and seasonal data trends might help in forecasting client orders.
WMS vs. ERP Software System
Warehouse Management Systems (WMSs) are used mainly to manage inventory storage and movement. This system records every stock item's campaign, including the items received, picked, and packed. WMS and ERP are different because WMS systems allow inventory optimization based on real-time data. Based on historical data and trends, information can be used to determine the best place for each item. WMS can be standalone and require other modules like accounting or customer relationship management.
On the other hand, Enterprise Resource Planning (ERP) automates all organizational activities, including accounting, customer relationship management, inventory management solution, and stock control. ERP software solution facilitates information flow between all functional areas. ERP software offers many of the same capabilities as WMS software, such as tracking the picking, packing, and shipping of inventory levels items. ERP software can be used as an integrated, all-in-one system. Having multiple software applications running your business is not a good idea. Various applications can lead to lower productivity and decreased efficiency due to duplicate entries and to rekey mistakes.
Making The Right Choice
The right inventory management software is the most crucial decision in your supply chain. It will significantly impact your company's day-to-day operations, customer relations, and financial health. It is up to you to decide whether your ERP System will use a warehouse module or a best-of-breed WMS.
The distinctions between traditional enterprise resource planning and vendors of warehouse management systems are becoming hazier. While WMS companies improve supply chain visibility and other management capabilities, several ERP vendors are extending the capability of their systems.
Chief Financial Officers (CFOs), when faced with the decision of whether to upgrade their WMS or keep using an existing ERP function, will choose the latter. On the other hand, the Chief Operations Officer (COO) is primarily concerned with adaptable, multifunctional, and risk-averse systems. This entails selecting the greatest WMS available. The chief information officers' top concerns if they are making the selection are the current workload, the IT staff's skill set, and the hardware investments. Who will be in charge of the budget is a much simpler question than who will choose the WMS/ERP. It takes a team to balance the objectives of the entire business with those of IT, finance, and operations. The selection process must be focused on increasing business value and achieving essential performance goals. It is important to define your business's long-term goals and functional requirements clearly. Then, match these goals with the implementation and integration costs.
Many businesses mistakenly believe that it is expensive to implement a current module for warehousing in an ERP system. This is false. Ask anyone who has attempted to follow this process. It is impossible to assume that your warehouse module will seamlessly integrate with other parts of your ERP system. These are the factors to consider: What is the cost of workarounds to replace missing functionality? What will be the impact on customer service? It may surprise you that your ERP does not include a warehousing module.
Flexibility
ERP systems are based on transaction-based logic. This logic can be found in order and financial management systems. ERP systems work best in linear environments with consistent order and few exceptions. Warehouse Management Systems are the best choice if your business is susceptible to frequent priority changes.
Functionality
ERP warehouse modules can force significant operational compromises in complex operations. Enterprise Resource Planning systems may not allow barcode scanning for in-depth product tracking. Complex procedures may call for a WMS that is best-of-breed.
aValue
Your final decision should be based on the system's value. While sticking with an ERP module may work in the short term, what about its future value as your business grows? In your return-on-investment (ROI) analysis, it is essential to ask the tricky question: What do you gain or lose by investing in best-of-breed WMS solutions?
A significant problem for organizations with a vital supply chain component is the dilemma of WMS. The company must decide whether to use the WMS module included in their ERP software or if they want to purchase a better, more robust WMS package.
There is no one-size fits all solution. Everything depends on your business operations, future goals, and financial situation. It is also crucial to consider aspects like the simplicity of system integration, potential effects on customer relationships, and the cost of workarounds if the WMS lacks the needed capability.
Conclusion
Many businesses opt for an All-in-1 or ERP because it provides everything in one place. An All-in-one may be overly concerned with juggling several tasks at a time. They frequently need more specificity to manage inventory software or warehousing operations. Additionally, they need to be more adaptable to scale up.