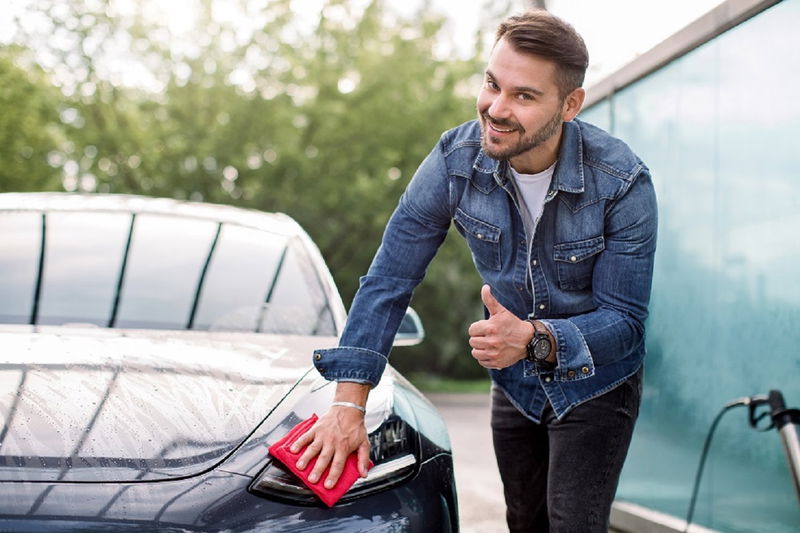
Simplifying business procedures is critical for companies hoping to expand and small businesses trying to become more efficient and productive. When procedures have been simplified, they are known as being "streamlined workflow/streamlined processes" or current workflow. This often means eliminating steps that add no value or are unnecessary to reach an objective and employing automation or technological techniques to speed processes up.
However, business processes are anything but straightforward. They involve any number of procedures related to running an organization and informed decisions, such as hiring staff members and handling finances, operating efficiently while adhering to management structures, and communicating effectively with clients and customer relationship management. One key characteristic of these processes is that they often involve several steps and several people before reaching completion - giving businesses more time and energy for actual work by ensuring all procedures run as effectively as possible.
Streamlining Business Processes For Effective Growth
What are the most efficient approaches for streamlining processes in business procedures, and why is their implementation essential? Streamlining business procedures is critical for long-term business success for various reasons; simplified processes offer reduced risks, higher productivity, better time management and decreased costs - providing businesses with more human resources and time for meeting overarching business goals while freeing them up from cumbersome processes that take away time from leaders and employees alike.
Assess Your Value Chain
Analysis of value chains is nothing new; typically, this involves evaluating each phase in a process's lifecycle and calculating costs and profits associated with each step, an integral practice in many companies.
Although businesses with profitable processes might find this strategy advantageous, its success ultimately rests with individual businesses or processes themselves - some might define value in terms of observable profits, while for others, it may make more sense to consider which procedures or activities contribute towards reaching overarching business objectives; asking yourself where you envision the company will be in several months/years/etc will aid this analysis process immensely!
Companies can assess their current procedures to identify which ones add value and which don't. When adopting this perspective, analyzing business processes becomes much more straightforward: determine what parts or processes help move a company from point A to point B more efficiently, cutting any that don't contribute toward that end goal, etc.
Identify What Works And What Doesn't
Figuring out which processes are working and which aren't may be the starting point for some businesses when streamlining current business processes. This might require creating a list of all currently implemented procedures to see where each could be improved, or alternatively identifying specific processes that have yet to be enhanced and optimizing those further.
Either way, one key aspect of streamlining processes involves recognizing individual or collective functions that work well while others don't; understanding bottlenecks (points where momentum gets blocked or slow down occurs in processes) helps identify what does and doesn't.
Barriers arise for various reasons - insufficient funds, authority, knowledge, or technical proficiency are a few examples - so by identifying bottlenecks, you can determine which areas require the most excellent care and attention. By getting input from those using your process every day - such as critical stakeholders using it daily- keystone players are in an ideal position to identify bottlenecks quickly and provide insightful analysis of what functions well and poorly for their processes. Executives know precisely where and how to act based on this feedback.
Look For Areas To Automate
Business process automation and step reduction have never been more straightforward, thanks to modern technological tools available today. Automate wherever possible for maximum business efficiency and ensure manual tasks are carried out swiftly and competently. Executives and staff alike benefit when processes are partially or wholly automated; especially helpful are automated administrative tasks that take considerable time and energy to perform manually. Businesses often underestimate their abilities to automate more processes than people realize. One essential step towards efficient and productive business operations is researching which automation tools will benefit your company and determine which will fit in most effectively with its operations.
Regularly Assess Goals And Milestones
Receiving feedback on the effectiveness of recently implemented or revised processes is paramount and must occur regularly. No process can ever be completely perfect, and there's always room for improvement, hence why continuous process improvement exists as part of a solution to problems. But steady progress alone won't do; more is necessary.
Ensuring the procedures you have implemented still align with and contribute towards meeting your overall business objectives forms the other half of this equation. A process's effectiveness can be assessed according to how effectively it moves a company from point A to B, as discussed in the value chains segment. When priorities and goals change within your business, ensure the established procedures still reflect those shifts, adapting as necessary to maximize value creation.
Manufacturing ERP (Enterprise Resource Planning)
Manufacturing ERP software automates and streamline key business and manufacturing processes using features tailored specifically for manufacturing industries. ERPs for manufacturing can integrate directly with business databases used for other operations and apps to provide an all-encompassing management platform for running operations smoothly and profitably.
ERP Software: The reason Is It Used In Manufacturing
ERP (Enterprise Resource Planning) systems are manufacturing management software which increase organizational effectiveness of manufacturing businesses by better resource optimization and management. ERP allows manufacturers to increase productivity without increasing costs by either increasing or decreasing resources as required without impacting quality or performance; manufacturing firms using this type of ERP can manage supply and inventory planning as well as shop floor operations with this tool.
Who Needs Manufacturing ERP?
Manufacturing ERP software provides manufacturing businesses of all sizes with tools they need to effectively oversee, automate, track, collaborate and connect throughout all stages of their dynamic manufacturing processes - from customer service order receipt through shipment and delivery - so as to facilitate growth. Manufacturing businesses require ERP with industry-specific features and capabilities for successful management and operation of their processes.
Small Business ERP
ERP provides small manufacturers with one system that functions across their company, eliminating the need for multiple tools. ERP offers comprehensive business operations management using best practices; modern cloud ERPs have quickly deployed times, lower ownership costs, easier accessibility from any location and ongoing updates - which make them especially appealing among small enterprises.
Mid-Market ERP
Mid-market manufacturers can benefit from ERP software's built-in analytics, quick deployment and best practice support across an array of business operational processes/operational excellence such as accounting, HR management, supply chain management and financials by taking advantage of modern ERP applications. Modern ERP programs give expanding companies access to resources they need in order to become more cost effective, productive and agile in the digital transformation marketplace.
Enterprise ERP
Large manufacturers whose operations span multiple geographies require an ERP with integrated analytics, AI and machine learning in order to transform financial processes through intelligent automation. Installation may occur either on-premise, in the cloud or hybrid; modern in-memory databases or existing ones could work effectively as databases can both operate simultaneously in this scenario.
The Best ERP For Manufacturing
Process manufacturing ERP software systems allow Adaptive wide range Manufacturing companies/Businesses the agility needed to take advantage of disruptions and change and gain a competitive edge.
Based on the size, purpose, and requirements of manufacturing organizations today there is an assortment of ERP system types and deployment solutions currently available to them.
- Once installed, an on-premise ERP system provides cost of ownership, control and support that cover both price and risk that manufacturers incur when managing hardware and system infrastructure.
- Manufacturers can benefit greatly from adopting an intuitive cloud ERP system with continuous support, updates, training and customizable capabilities from their ERP provider.
- Manufacturing firms could benefit from using "Hybrid ERP", an on-premise and cloud based deployment model with flexibility for switching delivery models or adding features not currently found in current implementations. ERP users could take advantage of hybrid deployment's flexibility when choosing which solutions best suit their business requirements/material requirement.
Why Is Manufacturing ERP Important For My Business
ERPs tailored specifically for manufacturing offer small and midsize manufacturers lasting value, from daily finances and accounting management, to managing core processes, manufacturing operations and inventory levels. Manufacturing ERP offers numerous benefits over generic ERP solutions in terms of controlling daily finances, inventory levels management and managing core/current processes - giving your manufacturing business the competitive advantage it needs for success.
- Keep an eye on raw materials, distribute resources and plan out manufacturing processes efficiently.
- Keep an eye on shop floor activity and manage the manufacturing process more effectively from its inception to conclusion.
- Schedule job shop/production scheduling according to labor hours, machine time, and available raw materials.
- Make it easier than ever before to keep tabs on job costs, generate custom reports and manage daily finances by keeping an accurate count of job expenditures and taking charge of finances in everyday life.
- Keep track of finished goods inventory as it enters and exits.
- Acquire, barcode and store goods while being mindful of each item's precise position within your warehouse.
- Use quality control checkpoints to make sure the products meet customer demand/expectations and fulfill them completely.
6 Main Benefits Of Streamlining Your Business Processes
Streamlining business processes is one effective strategy to cut expenses and save time. Doing this may result in reduced costs while simultaneously improving productivity at any organization - this might involve eliminating redundant tasks, automating repetitive ones or creating entirely new responsibilities - all of which have the power to enhance both work produced by staff members as well as their clients' experience of your services.
Reducing waste within your business processes has many benefits of streamlining processes; here are six of them.
Increased Efficiency
Integrating business processes more smoothly helps employees understand their roles more readily, increasing productivity. If you know Haven Systems, energy efficiency comes to mind. Haven Systems specializes in EPOS systems for retail businesses looking for help managing deliveries or controlling inventory levels - solutions they specialize in being EPOS solutions themselves!
Haven Systems excels at developing convenient store point of sale (POS) systems. Through HavenPOS systems, retailers can instantly manage deliveries, stock levels, and business analytics while taking full advantage of cloud apps, solutions, and mobile solutions to create cutting-edge solutions tailored to any store size. Implementing business process restructuring helps employees understand their roles more readily, increasing employee productivity while improving everything from deliveries to stock control.
Increased Productivity
Once optimized, business processes no longer include any unnecessary steps; only work that immediately produces results will become priority work for yourself and staff members, increasing individual and organizational productivity instantly!
Productivity growth boosts company profitability while simultaneously raising employee expectations of pay raises and higher salaries. Your staff must be productive for you to be productive, using available resources efficiently to complete tasks within time constraints, thereby saving both resources and time for you. Your business processes can be improved to save time and identify areas where resources are wasted. By applying what has been learned above, adjustments can be made that make things better.
Improved Communication
Everyone within an organization is affected by business processes, so streamlining them will prove advantageous for all involved. Say a department manager trains staff on how to complete tasks more rapidly - in such an instance, they could inform other managers and staff members throughout their organization of this information.
Staff who become aware of newly simplified business procedures will understand exactly their roles, leading to improved communication. Streamlining processes within your organization and improving information flow throughout can significantly cut costs while making operations run more smoothly and increasing communication within.
Better Time Management
Optimizing the procedures at your company leads to improved time management. Employees will have more time for other responsibilities when there are fewer complex tasks they need to do - saving both absenteeism and increasing productivity over time, not to mention helping new hires adapt faster! Incorporating simplified business processes also assists new employees who might otherwise feel intimidated.
Employee training can be more efficient when fewer learning processes are involved; that way, more important aspects can be covered without covering every facet of it all. This approach may prove valuable if new techniques are being introduced into work environments or entry-level staff turnover is high. If your organization employs multiple managers or locations, having consistent business procedures across them is critical to enable senior managers to oversee the entire operation effectively.
It Minimizes Risk
Reduced processes lead to fewer opportunities for human error, which in turn helps lower business risks. Employees completing more tasks regularly with few or no errors means fewer opportunities for errors to creep through. Simplified business procedures also lower risks by helping identify possible issues before they escalate further.
One of the best ways to prevent errors is through proactive rather than reactive approaches, like streamlining business processes; regular monitoring will enable you to detect issues before they escalate into bigger ones. Plus, with fewer processes and items needing monitoring, less supervision will be needed, and more time will be dedicated to ensuring the business runs profitably.
It Helps To Analyze The Outcomes Of Business Operations
Simplified business procedures make it simple and effective to monitor and assess the outcomes of your company's operations. By monitoring areas where mistakes arise and tracking which new hires need additional training or whether outdated procedures must be updated, simplified business procedures allow companies to keep an eye on quickly and measure outcomes of day operations more closely and evaluate results accurately.
As well as keeping tabs on areas requiring modernization or enhancement in your company, benchmarking also offers valuable real-time insights into your advantages and disadvantages in comparison with rivals so you can adjust future tactics more precisely.
Consider employing automated project management software to quickly import real-time data into spreadsheets from your website and social media accounts so you can quickly analyze positive and negative customer experience comments to address appropriate responses. Not only can companies that optimize their workflow experience the above benefits, but streamlining business intelligence processes should be of interest to any entrepreneur or owner as it could help lower operating expenses significantly.
As has been noted above, increasing improved efficiency through streamlining business environment processes will bring long-term key benefits. Integrating new tools and technology into the workforce may encourage workers to assume greater responsibilities at work and be proactive about taking the initiative - leading core business processes to avoid time-consuming repetitive tasks that drain resources.
Want More Information About Our Services? Talk to Our Consultants!
Conclusion
Though streamlining business processes is no simple undertaking, companies of all sizes could find it a worthwhile investment. Business performance may improve customer satisfaction while simultaneously cutting cost saving time by eliminating ineffective tasks or procedures that reduce operational efficiency and waste time and resources.
Process simplification carries some inherent risks, including diminished product quality assurance and employee resistance; however, companies can minimize them and maximize their advantages by following this article's advice and considering these potential problems. Overall, business process management can use process simplification to boost productivity, morale and creativity. Before streamlining processes, material planning out your project and conducting research carefully is advisable; otherwise, it could become a fruitless and even rewarding experience.