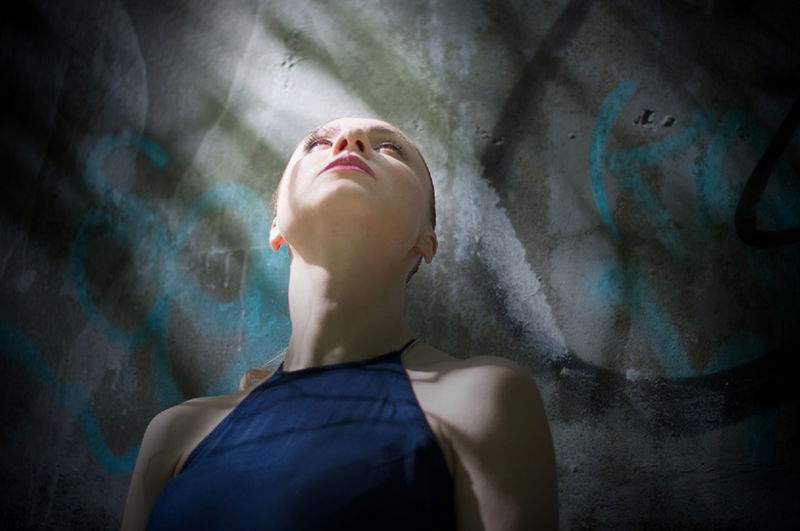
As companies grow, spreadsheets are no longer sufficient. Enterprise Resource Planning software is the answer. ERP systems organize and collect key business information to help organizations operate efficiently and effectively as they grow.
Although most business professionals are familiar with the term ERP, they may not know what enterprise resource planning systems can offer their employees. This article will explain what ERP is, how it works, and what it can do to your business. We also discuss how to select the right ERP solution.
What is Enterprise Resource Planning (ERP), and How Does It Work?
ERP, at its core, is an application that automates business operations and provides insight and internal controls. It draws on a central database that gathers inputs from various departments, including accounting, manufacturing and supply chain management.
Each business has to complete work that involves multiple stakeholders, each with different responsibilities. Finding the right information across disparate systems can be difficult, making it more difficult for businesses to complete their work. Employees may not easily access the needed data, whether it is stored in spreadsheets or basic business management software. The accounting and FP&A departments could have different spreadsheets containing expense tracking numbers.
These disparate data sources make it difficult to keep everyone on the same page. This can lead to poor collaboration and productivity, especially as an organization expands. Because there isn't one place that provides current information about all aspects of the business, staff waste time searching for documents or creating duplicate work. It is also difficult to understand the true cause and effect of changes that affect your business.
An ERP system solves this problem. It compiles information in a central database that grants managers and employees cross-departmental access. It eliminates conflicting data sources and allows employees and managers to analyze scenarios, identify process improvements, and make major efficiency gains. This results in cost savings and improved productivity because people spend less time searching for the needed data.
ERP software tailored to the specific needs of a business pays big dividends. This makes ERP software a crucial tool for all industries and sizes. ERP has been a key tool for many of the world's most successful and well-known companies over the past quarter century. This software is now configurable and priced to suit the needs of any size business.
ERP systems help unify an organization's core business processes, people, and technology.
The Key Takeaways
- ERP software is a critical business tool that gathers data from different departments into a single database. This allows leaders to view the pulse of a company with one vision of reality.
- ERP systems integrate critical business functions such as finance, manufacturing, inventory, order management, customer communication and project management. A major feature of ERP systems is the detailed reporting and analytics on each department.
- ERP can help you save time and money by allowing you to see across your organization. This visibility will allow you to spot inefficiencies and identify growth opportunities.
- There are many deployment options for ERP software. These include on-premises, cloud, and hybrid. Cloud ERP has been extremely popular in recent times. Still, the best solution for each company will depend on its specific needs.
- Before deciding on a winner, businesses should ensure they are fully informed about each software provider's capabilities, integration requirements, and cost of ownership.
ERP Explained
Enterprise resource planning, a term coined in 1990 by the Gartner research firm, can be confusing because ERP isn't a standalone application. ERP software is a type of business software. ERP systems comprise various modules that address a specific business need. Products-based businesses typically have modules that handle accounting, inventory, order management, Customer Relation Management (CRM), and manufacturing if they make or assemble products. Service businesses can use modules for project management, accounting, and CRM.
Each Module pulls data from the central database into the ERP system's main component. The common data repository gives leaders visibility into all areas of the organization. It allows them to compare and contrast the performance of different departments. Leaders can also see the full impact of their decisions. This common data repository can provide other ERP benefits, such as process automation and better internal controls.
Two main approaches are available to build an ERP system. First, you must find software capable of handling all core business functions from different vendors, including sales, inventory, and manufacturing. These software solutions can then be integrated with a central database (the E-Business Platform). You can also buy all modules from an ERP vendor and not have to integrate them since they are designed to work together.
Because of its simplicity, obtaining all or most of the ERP modules you require from one vendor is the best choice for large businesses. These disparate systems can be complicated to integrate and require a large IT team or partner. This is why it's not practical for small and medium-sized businesses. These integrations require ongoing maintenance once they are established.
On the other hand, a unified platform offers native integrations between modules and a common user interface for users to move between them. This simplifies ERP implementation. The information flows easily between modules, giving decision-makers a complete view of the company.
Why Is ERP Critical For Businesses?
ERP systems are now a key part of businesses that want to make the most of their resources. ERP systems can help business leaders allocate human and financial capital or create more efficient core business processes that reduce costs without compromising quality or performance.
Planning and coordination are also made easier by an ERP. An ERP allows employees to see the current inventory and customer orders and compare supplier purchase orders with forecasted future demand. They can also make necessary adjustments to avoid future problems. ERP software facilitates collaboration and communication. Workers can also check the status of other departments to make informed decisions.
An ERP system provides a comprehensive source of data and a variety of analytics that can make a difference in the business. ERP executives find it invaluable to convert a large amount of data into graphs and charts that show trends and help model results.
What is An ERP System?
ERP systems operate by using a standard data structure. All authorized users can access information entered by one department immediately. This helps everyone stay on the same page. Let's say, for example, that a local food distribution chain has multiple locations which often share stock or personnel. The ERP system formats the data to indicate where it came from, as it feeds in quality, sales, and employee data.
The real-time data can be integrated into business processes across departments and workflows. Leaders can determine if one site performs better than another and work with operations to determine why. Executives can use finance to compare rents and sales to decide whether to consolidate.
ERP systems are most valuable when modules exist for every major business function. This ensures that data entry is accurate and timely. The more stakeholders that have access to ERP systems, the better.
Integrations can allow data to flow automatically into an ERP if a company has business systems from different vendors. These real-time data can be used in the ERP instance to improve any process or workflow.
ERP Modules
An ERP system is made up of a variety of modules. These modules are tailored to various business areas, such as back- and front-office functions. This extends beyond financials, including other essential functions such as supply chain management and customer communications. Here is a list of the most popular ERP modules:
Finance: A finance module is the core of almost every ERP system. It manages all financial data and the general ledger. It records every transaction, including accounts payable and receivable (AR), and handles reconciliations and financial reports.
Procurement: The procurement module manages to purchase raw materials and finished goods. It automates requests for quotations and orders for purchase. When linked to demand planning, it helps reduce overbuying or underbuying.
Manufacturing: Manufacturing is a complex process. This Module assists companies in coordinating all steps involved in making products. This Module allows companies to monitor production progress and ensure that they meet customer demand.
Inventory Management: An inventory management module displays current inventory levels to the SKU level and updates these numbers in real-time. It measures key inventory-related metrics. This Module is essential for any products-based company to optimize stock handling based on forecasted and current demand.
Order Management: This application tracks the progress of customer orders through delivery and monitors and prioritizes them from all channels. A module for order management can improve customer service and speed up fulfillment.
Warehouse Management: A warehouse management module manages warehouse activities such as picking, packing, and shipping. This Module can help warehouses save time and money by finding more efficient ways to perform these tasks.
Customer Relations Management (CRM): CRM has become a very popular module for many businesses across various industries. It can track all communications with clients and assist with lead management. This Module can improve customer service and increase sales.
Professional Services Automation: Services companies often use a " PSA " module to plan and track projects and their resources. It is a great way to simplify client billing and encourage team collaboration.
Workforce Management: A module for workforce management (WFM) that keeps track of attendance and hours worked and can manage payroll. This tool tracks absenteeism and productivity for each department, team, and employee.
Human Resources Management: A human resources management (HRM), or human capital management, is similar to a workforce module. It maintains employee records and provides detailed information such as performance reviews and PTO. It can also provide insight into workforce trends within different departments and demographics.
Ecommerce: An eCommerce module allows brands and retailers to manage their online stores' back- and front-ends. This application allows them to modify the website's look and feel and add or update product pages.
Marketing Automation: This Module manages marketing efforts across digital channels, including email, web, and social. It allows organizations to personalize and optimize their messaging. Marketing automation tools can increase leads, sales, and customer loyalty.
Are you unsure of the modules that you will need? This guide will help you decide which modules to include in your implementation plan.
What Can ERP Do To Improve Or Help a Business?
ERP allows companies to spot areas that could be improved or expanded. Access is crucial for users: More employees will have ERP access, making spotting potential problems easier. These could include a spike in demand, late shipments, or cash flow issues. The employees can then take proactive steps to address the problem.
Executives tend to be focused on the outcomes. They use the information to reach objectives such as increasing efficiency, decreasing costs, responding to changing consumer or market conditions, and using that information to reduce risk.
ERP software is a great tool for automating many error-prone tasks in business units. For example, order processing and customer billing can be automated. It also provides the information that teams need to run more efficiently.
ERP's real strength is its ability to provide a detailed view of a company's health and insight into a particular process or KPI. It can store and organize data, identify patterns, and flag anomalies that need investigation. You can do the same with a spreadsheet.
There are other business benefits:
Employees Have Access to Data From Anywhere
They no longer need to shuffle through stacks of papers and files scattered around a computer screen. A warehouse manager can log into cloud-based ERP from his mobile device while on the floor. Or a salesperson can view inventory while at a customer's site.
The ERP system receives information continuously from different departments. The ERP system can update it immediately when inventory is pulled, payments are posted, or emails are sent. This is a significant advantage as decision-makers can base their decisions on current data.
All Decision-Makers Can Make Business Decisions Based on The Same Data
With a common database, everyone is on the same page. Companies can schedule and automatically distribute dynamic reports, so there are no duplicates or conflicts of information.
Who Uses ERP?
ERP has been a boon for companies with different business models in every industry. ERP solutions can be flexible and offer extensive functionality to meet the needs of many organizations.
These industries rely on ERP to manage their businesses:
Roles & Users
These organizations have ERP that benefits a variety of job functions, including, but not limited to:
- Finance/Accounting: The accounting department is often the first to adopt. This group will monitor and report on all financial transactions in the system, including accounts payable and receivable (AR) and payroll. ERP allows financial planning and analysis experts (FP&A) to turn financial data into reports and forecasts on revenue, expenses, and cash flow.
- Supply Chain: Operational employees, which include purchasing agents, inventory planners, warehouse managers, and senior supply chain executives, rely on the ERP to ensure that goods flow smoothly from supplier to customer. The ERP system provides detailed, accurate information to optimize inventory levels, prioritize orders and maximize on-time delivery. They also help identify inefficient or manual processes.
- Sales and Marketing: An ERP system can improve productivity and deliver better results for your sales staff by automating lead management and monitoring prospects' interactions with your company. Reps can record discussions and update status as prospects move through the sales process. Marketing can automate and manage all channels of outreach using the same records. This includes email, display ads, social media, and mobile. It can also measure the effectiveness and allocate its budget more efficiently.
- Human Resources: The HR department keeps track of all employee information and the ERP's wider workforce trends. It can quickly locate employees' contact information, benefits details, and other documents. HR can monitor metrics such as retention by department, average salary by title, promotion rates, and other metrics to help better allocate staff and support line-of-business leaders.
Why ERP is Important
While ERP software was originally designed for enterprises, as the name implies, today's cloud-based software-as-a-service (SaaS) ERP offerings have lowered entry barriers and helped countless emerging and midsize businesses increase their efficiency, visibility, and, ultimately, profitability.
These tips help you decide if ERP is right for you.
- Examine your technology regularly and ask: Does it help or hinder us? It's time for a new solution if outdated or inefficient systems cause inefficiencies, muddy data waters, or don't support the changes the business needs.
- Another sign that it is time to upgrade or start a new ERP system is inaccuracy. Unreliable data can lead to a lack of trust in the reports and insights that it generates. This is a serious problem.
- Do you find that errors are a constant problem? Unified systems can help you organize your operations and streamline processes to eliminate these problems.
- Another indicator that ERP is needed is over-reliance on spreadsheets and email to collect and share important information. Spreadsheets must be updated manually and frequently, so they can become outdated. Email sharing sensitive data poses serious security risks and can make finding what you need difficult.
- Integration issues between systems are another sign that you're ready to implement ERP. The system can eliminate manual data transfers and inconsistent connections by bringing together information from all business functions.
While some costs are associated with ERP software deployment, they often provide a fast return on investment. There are many resources available to help you build your business case.
ERP Components That Are Essential For Distributors And Manufacture
While ERP has many features vital for manufacturers and distributors, here are some most important.
- Manufacturing or Production Module
It allows companies to manage product planning, material sourcing, production control, quality evaluation, manufacturing forecasting, and product planning. The latest ERP systems integrate make-to-order, make-to-stock, just-in-time manufacturing, and lean operations. Automated planning, scheduling, fulfillment, and other functions help manufacturers to streamline their operations. This improves manufacturing speed and accuracy.
- Supply Chain Management
It's never been easier to manage the supply chain. ERP allows you to streamline product flows from production (for returns) and vice versa (for customers). ERP can also speed up order fulfillment by reminding you of the due date. This streamlined supply chain allows for innovation, lowers operational costs, and gives you a competitive advantage.
- Material and Inventory Management
A robust ERP system allows you to know when it is time to place orders. You can also record product movements automatically and efficiently. These insights can help distributors and manufacturers optimize inventory, reduce overhead costs, minimize waste, and lower delivery costs.
The Key Benefits of an ERP System for Distributors and Manufacturers
ERP addresses the needs of highly competitive manufacturing and distribution businesses in many ways. These are the top benefits of an ERP system for your business:
Repetitive Processes
A complete ERP solution automates your manufacturing and distribution businesses. You can automate creating invoices, updating customer details, and responding to customer queries. Automate order placement when stock is low and update customers on their order status (packed or shipped, etc.). You can also update the finance department regarding raw material requirements. This will speed up production, reduce errors, and increase profits.
Prepares for Change Customer Demands
With manual data tracking, planning, adjusting, adapting, and responding to changing customer needs can be difficult. An ERP system allows you to access real-time information quickly and makes it easier to make better decisions. An ERP system can be integrated with CRM to help you understand customer satisfaction levels. It will also show you what customers think about your products and how frequently they contact your support team. Combining this information lets you understand customer needs and financial interactions with your business. This will allow you to optimize your products and market strategies for better results.
Increase Customer Satisfaction
Businesses can streamline their process scheduling and coordinate distribution channels with better inventory control and production planning. This allows them to improve on-time delivery and reduce costs. Suppose everyone within your company has access to important information such as shipping instructions and bills of material. In that case, it will reduce production time to reach consumers. Customers will be happier if they receive their products faster. ERP gives you real-time inventory data to plan deliveries and manufacturing processes to meet customer demands.
Increase Productivity
Companies that rely on their employees more often have higher labor costs than those that use automation. Companies can automate tedious tasks with an ERP system, which allows them to spend less time and labor on the same work. This gives employees more time to complete higher-value tasks. This will increase productivity and lower labor costs.
Enhances Reporting
With one click, ERPs make creating reports with pre-defined metrics or ready-to-use formats easy. This allows you to analyze various aspects of your business and help customers understand what they expect. You can customize reports depending on the aspect of your business and optimize your strategies accordingly. To analyze inventory levels and place orders, for example, create an inventory report. ERPs also have a business intelligence function that allows you to create actionable reports such as forecasting and current business conditions. This helps reduce decision-making time.
Adapt to Legal and Regulatory Changes
Distributors and manufacturers already have many responsibilities. Non-compliance with regulations is not something you want. ERP will take care of this for you. Modern ERP systems have built-in compliance features that help you meet different legal requirements depending on your country. ERPs can help you comply with the GDPR (General Data Protection Regulation), which focuses on privacy and data protection in the European Area and European Economic areas. You can also contact your ERP vendor for assistance in implementing the changes required to conform to changing regulatory frameworks.
Removes Wastage
Overproduction or procuring products in excess can lead to waste and losses. Complex workflows can lead to over-processing and unnecessary delays in production or distribution. Modern ERP systems help manufacturers reduce wastage and avoid overproduction. ERP software can ensure that your production/procurement aligns with consumer goals and your company's key performance indicators (KPIs). Advanced forecasting is a great way to anticipate customer needs and increase/decrease production. This allows you to ensure no customers are missed and saves on production costs.
How Manufacturers Can use ERP To Gain Competitive Advantage
Every company hopes to see a return on its ERP investment. It is important to make more money and outperform your competition. However, it cannot be easy to stand out in an age where almost everyone has an ERP system. QAD's ERP software is a great way to get a competitive edge in your industry.
Choose The Right ERP System for Your Company
Although many ERP solutions provide the same core functions, there are a few differences that you should be aware of. Your ERP software must be tailored to your industry to ensure you get the best value for your money. If you were in manufacturing, you wouldn't tell a professional services firm how to do business. ERP systems are no different. It doesn't necessarily mean that the cloud is best for everyone else or vice versa. The key to choosing the right ERP software is to partner with the right company to ensure your business has the support and training it needs.
Don't Waste Money on Customizations That Won't Help You Grow
Although it might be tempting to customize everything about your new system, you should first consider whether these customizations will significantly affect how your business operates. Customizing little things that don't give you an edge is unnecessary. Instead, use your customizations for areas that do. However, customizations should not be limited. Customizing ERP is a great way to increase your business's competitiveness. You should tailor your ERP to your unique business process if you have created a way for your company to be more successful. You will save time and money by separating the two.
Make The Most Of Your ERP's Predictive Capabilities
ERP software users can benefit greatly from real-time analytics. Automated software improves preventative maintenance and detects potential problems before they occur. This is something that ERP systems without advanced features will continue to struggle with. Your ERP's predictive capabilities allow you to spot potential errors and eliminate them immediately. Smart technology can eliminate errors thanks to the many ERP and IoT partnerships. Avoid being caught unawares by making mistakes and silly errors. Use ERP to stay ahead of your competition.
Enhance Planning, Scheduling, and Execution
ERP systems have advanced planning and manufacturing modules supporting all production methods. Execution modules allow decision-makers full access to data collection options, quality measures, and scheduling. They also provide visuals of master schedules that make it easy for planners to create accurate "what-if" scenarios. Rerouting conflicting schedules and meeting demand only increases conflict prevention and error prevention. This allows you to focus on the bigger picture. It's easy to see how bad reviews affect a company's online reputation. You must ensure that your ERP software works for you, not against you. ERP can make it easy to stand out from your competitors.
Conclusion
ERP systems can help distributors and Manufacturers Streamline Processes, increase productivity, reduce errors, and improve customer service. To get the best ERP system for your business, it is important to partner with an experienced provider such as ArionERP.