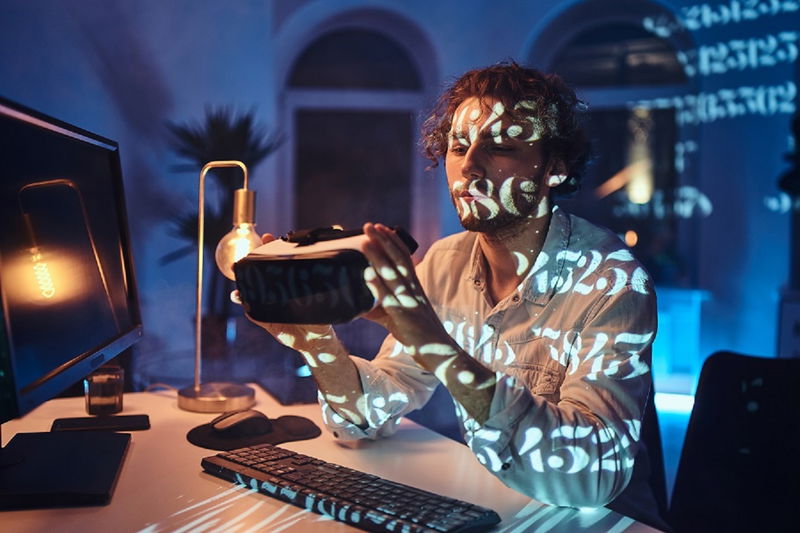
What Is ERP Inventory Management?
Enterprise Resource Planning (ERP) inventory management has a wide range that enables companies to control all elements of their business from one platform. This includes enabling companies to control all elements of finance and logistics.ERP inventory management solutions give the entire business access to real-time inventory data. This is vital for companies that want to grow, have complicated processes or supply chains, need high levels of automation, operate in "just-in-time" mode, sell various products, or want the most return on their inventory investments.
Why Is Inventory Management Critical?
The key to a company's health is inventory management. It helps ensure that there is never too much stock or too little stock, which reduces the risk of stockouts.
Public companies must keep track of inventory to comply with Securities and Exchange Commission rules and the Sarbanes-Oxley Act. To prove compliance, companies must document their management processes.
Inventory Management Has Many Benefits
Inventory management has two significant benefits. It ensures that you can fulfill any incoming or open orders, increasing profits. Also, inventory management:
- Saving Money: Understanding stock trends allows you to see the amount and whereabouts of stock so that you can better use what stock you have. This allows you to store less stock in each location (store, factory), and you can pull from any location to fulfill orders. All of this reduces inventory costs and decreases stock that isn't sold.
- Increases Cash Flow: Proper inventory management will allow you to spend less on inventory that doesn't sell and keep cash flowing through your business.
- Satisfies Customer base: It is important to ensure that customers are satisfied and receive what they need quickly.
What Are The Advantages Of Inventory Management?
Accurate inventory management is essential for a product business to succeed. Stock mistakes and other issues can be prevented with regular stock tracking. The following are some advantages of having an effective inventory management system:
- Improved Inventory Accuracy: You can know what is in stock so you can order the inventory that you need to meet your customers' needs.
- Lower risk of overselling: Inventory Management helps you track inventory and backorder so that you sell only a few products.
- Savings on Stock: Stock costs a lot until it is sold. Storage management costs, shipping costs, insurance, and salaries are all part of the carrying costs. Stock is also susceptible to theft, loss due to natural disasters, or obsolescence.
- A better planning and management approach will help you avoid stockouts and excess stock.t can help a business reduce the time it takes for an item to go out of stock and prevent carrying too many inventory items. Our "Essential Guide to Inventory Management" will help you solve stockouts.
- More Insights: With inventory tracking and stock control, you can easily spot sales trends, the track recalls, or track expiry dates.
- Negotiate Better Terms with Suppliers and Vendors: Inventory Management provides insight into which products are selling and how many. This knowledge can be leveraged to negotiate better terms and prices with suppliers.
- More Productivity. Time saved by reasonable inventory management solutions can be used for other activities.
- Higher Profits: Higher inventory turnover results from a better understanding of demand and supply, which also increases earnings.
- A More Organized Warehouse A more efficient warehouse with items that are organized according to demand. This reduces labor costs, speeds up fulfillment and lowers labor costs.
- A Better Customer Experience: Customers who receive their orders on time are more loyal.
What Are The Disadvantages Of Inventory Management Systems?
Inventory management software has the same disadvantages as other software. The downsides of inventory management systems are that they can be costly, difficult to use and vulnerable to hackers. But there are simple ways to mitigate these weaknesses.
- Too expensive for small businesses: Although inventory management software may seem prohibitive to small businesses, the cost often pays off in higher profits and better customer loyalty. Cloud-based solutions have made software previously reserved for large corporations accessible to small businesses.
- It's not easy to learn: Business software can sometimes be challenging to understand. Managers can invest in online training to bring users up to speed quickly.
- System crashes are possible: Software can crash. Cloud-based platforms can help you eliminate the risk of losing data or productivity.
- Malicious Hacks Malicious Hacks pose a threat to all businesses. The Internet of Things (IoT) adds complexity. Because of the potential for a vendor to be hacked, cloud-based software is typically more secure than any single company.
- Reducing Physical Audits: It's simple to forget about a physical inventory check when you automate warehouse operations. Regular audits can solve this problem.
Management Of Inventory Challenges
Inventory management is complex because you need more inventory, are unable to sell it, need more inventory to fulfill orders, and need to know where your inventory items are located. Other obstacles include:
- Getting Accurate Stock Details: With accurate stock information, it's possible to know when stock should be replenished or which stocks are performing well.
- Poor Processes: Work can be slow and error-prone if it needs to be not done correctly or manually.
- Changing Customer Demand: Customers' tastes and needs are constantly changing. How will your system track trends if it can't detect changes in customer preferences?
- Warehouse Space Well: If products are challenging to find, staff can save time. This can be eliminated by mastering inventory management.
Essential Things To Consider For ERP Inventory Management
Inventory management is a key skill that helps companies make the most profit and satisfy customers with the lowest stock investment. As we can see, inventory management is entirely about data. Aspects include purchases, repeat orders, shipping, warehousing, storage, and receiving; customer satisfaction; loss prevention; and other factors.
This information can be found in many inventory management systems. Companies that combine their enterprise resource planning (ERP) with inventory management functionality have a competitive advantage. However, the main competitive advantage lies in sharing information across different business units in real time visibility.
The Benefits Of Inventory Management Software Integrated with ERP
You can save money by using inventory management techniques to keep accurate stock counts and help you save. You can reap even more benefits if you have an ERP system with inventory management capabilities. This type of system will allow you to:
- Knowing Inventory Levels Across the Organization: ERP Systems can provide a complete picture of orders across all divisions, from sales to accounting to fulfillment. Centralized purchasing helps reduce duplication in replenishing stock and saves money by allowing you to buy in bulk. Integrating your inventory software with back-office and accounting processes can bring additional benefits.
- Automate Manual Tasks RFID scanning and barcode scanning can speed up stock-taking, receiving, and fulfillment. The software reduces mistakes in manual entries and frees staff members from repetitive tasks.
- More visibility with real-time data: The best inventory management software will allow you to access all SKUs in any facility. This software will provide this information to any device, regardless of where they are.
- Forecasting can be improved: Software that handles data collection and analysis can give insights into trends. You can also improve stock demand forecasting by understanding trends.
- Data-Driven Stock Decision Making: Use the inventory management software's analytics capabilities to make data-driven stock decision-making. Reduce inventory and carry costs to save money.
- Uninterrupted Production: You can forecast demand and lead times to ensure that production does not suffer from a shortage.
- Harmonize Multiple Inventory locations: See stock levels at all your warehouses and distribution centers, as well as in retail stores and suppliers.
- Optimize all Inventory: An inventory management system that is robust and efficient helps you maintain the correct stock levels and quantities at the lowest carrying costs. This software will help you make sure you have only a few items.
- Increase your inventory as your business grows: Accurately tracking 1,000 SKUs across 15 facilities by hand is impossible. This task can be handled by inventory management software.
- To make sure that generally accepted accounting principles are being followed. Financial transparency requires accurate stock valuation. Inventory management software must deliver the precise precision required by GAAP.
- Increase Product Visibility in Recalls. Digital systems enable managers to use lot/serial number records to track products by date/location.
So these were the benefits of Inventory Management Software
ERP Inventory Management: How ERP Inventory Management Benefits Your Company
ERP systems use a variety of data sources to provide insight into the performance history and other information. Organizations use this data to make better strategic decisions and forecast future demand.
ERP-driven inventory management increases efficiency throughout the supply chain management. It can reduce double-handling and automate everyday tasks like reordering.
There are other benefits to incorporating ERP in inventory management:
- Supply Chain Transparency: When a business can integrate back-end systems effectively and communicate directly with its suppliers, it minimizes disruptions like critical components not being delivered on time or prices too high for the product. Integration ERP systems allow for the synchronization of order and shipping information.
- Better reporting: Accurate inventory data allows decision-makers to fully take advantage of data-driven insight, such as understanding the top-performing SKUs, landed cost per goods sold (COGS), and sales by channel and location. ERPs allow for custom reports, which are accurate and valuable data.
- More precise counts: ERP system tracks and reports excess inventory, shortages and planned replenishment. It also provides metrics such as the average turnover rate (COGS). The warehouse system records and reports product transfers from shipping to receiving.
- End-to-end inventory analysis: ERPs provide data for every stage of inventory flow, such as the cost of goods sold and turnover rates. Companies can increase their inventory efficiency by analyzing key inventory metrics.
- Quality checks Most ERP systems allow you to use logic to define inventory quality checks. You can indicate whether products must meet safety or environmental standards. The system will then check the product safety information. The system will alert staff to make necessary changes if it detects that the item is not in compliance.
- Inventory planning Each product has an inventory status in the ERP. Staff, customers, and partners can check availability, numbers, and order. Your inventory history and metrics are easily accessible, which makes planning easier and improves customer satisfaction.
- A cycle counting system: An ERP system guides staff through a well-planned and planned cycle count process. Regular cycle counting is essential for inventory management and checks and balances.
What Are The Major Functions Of An ERP Inventory Management System?
Consider the long-term potential of any new system: A system that touches so many areas of your business and takes time and effort to put in must be able to meet your current and future needs. You should only use systems that are limited in functionality and will be obsolete within three to five years.
Here are five steps to help you find the right system for your business processes.
Step 1: Identify the Outcomes You Want
Make sure you consider the goals of your stakeholders and develop a business case. Strategic planning involves analyzing business trends, core competencies, and external opportunities.
Ask yourself these questions: How does the purchase of the proposed item align with long-term goals, both previously established and newly revised? What insights will it provide that are unavailable today to help us plan our inventory strategy?
Step 2: Identify the Project
What data sources are necessary for ERP inventory management software to combine critical metrics?? What suppliers and partners will have access to the ERP inventory management solution? Make a list of all the capabilities and features required to achieve the desired result.
Step 3: Create an ROI Analysis
Don't just focus on cost-cutting. Instead, consider how the investment will increase your company's profitability, efficiency, and customer satExplainly; explain how technology will allow your business to grow by better managing its inventory.
Step 4: Draft a Vendor List
To assist you in choosing the solutions that are most appropriate for your company, review case studies from organizations comparable to yours. Ask the following inquiries to limit your options:
- Are the systems flexible, scalable and easy to integrate?
- Are there any testimonials from other companies in the industry?
- What type of training is required? Is the company able to support training?
- Is there a free or paid trial version that can be used for testing purposes?
- How much does software cost upfront? Or monthly for cloud-based system applications? How about maintenance?
- How long will it take before we are up and running again?
Step 5: Look Ahead
Examine the product goals of potential system vendors and determine if they align with your business.
When deciding whether an ERP inventory management system will work for you, use the checklist below.
ERP Inventory Management: How To Get Up And Run
An implementation roadmap is necessary to properly implement an ERP inventory management software system and reap its full benefits. The roadmap consists of three steps:
- Create the record: Integrate all operations and data into a single ERP system, or connect legacy system data to your ERP for real-time upgrades.
- Lift the record: Layer for other functions such as advanced analytics, purchasing, and payroll. For optimum performance, all of these duties can be completed in a single record system.
- Expand with advanced ERP features: ERPs offer sophisticated functions such as planning, analysis, quality management, and analytics that will allow your company to innovate and adapt to changing market conditions.
ERP systems can handle many functions and areas and, thus, many aspects of a business. The roadmap can be used to help your business get from where it is now to where it should be.
An ERP System Is Used To Control Inventory.
An ERP system automated and optimized for inventory management necessary functions to ensure stock buying, organizing, and transferring all work in sync. It also integrates the inventory requirements of customers, suppliers and staff to maintain optimal stock levels.
Below is an illustration of how these organizations, their systems, and your central database might interact with an ERP. The "brain" that controls inventory operations is the ERP.
Each group of the diagram has different tasks and requires different systems. Suppliers use inventory, financial and prediction applications.
All of these systems must be working together. Each specialized software system must be able to communicate with the ERP system.
Let's say a company uses PLM to manage its inventory from conception to production. This will give you a better understanding of how ERP integrates with other systems. PLM and ERP are complementary. ERP is responsible for production resource planning. They would work in a sequential fashion. Initial product data is retrieved from the PLM. Once a product has reached a point in its development where it requires resources, the ERP integrates production with the rest.
You need to have a network of people, systems and processes to manage inventory properly. When you are growing your business, inventory control requires more than just "one system, done." It is crucial to use a centralized system for inventory management.
Implementing an inventory control system should begin early. Additionally, you want to put together a team of inside experts who can help you.
- Maintain up-to-date inventory data.
- Be realistic about your budget.
- Establish milestone goals.
- Facilitate user training, acceptability testing, and other implementation controls.
ERP Inventory-Management Must-Haves Attribute-Code System - Arion ERP
Country of origin GMO. Non-GMO Organic, transitional, and nonorganic. Heavy metals. Allergens. The complexity of inventory management for customer-specific quality parameters is increasing every day. Food and beverage plants need to be able to manage all these attributes with the help of a single digital platform.
It is essential to control expiration dates and other quality attributes. This allows you to satisfy customer requirements, comply with regulations, protect consumers (and your reputation), and operate profitably. Here's the catch: you need the ability to collect and use actionable data to be able to manage your inventory and make better decisions. It could be a cost saving for your business revenue if you manage your inventory in a different way. Many food and beverage plants, including distributors and processors, need help to connect their supply chains to manage inventory at the date-code and attribute-code levels.
Why Can't Food and Drink Manufacturers Manage their Inventory?
Multiple systems, legacy systems, and spreadsheets with outdated capabilities are all examples of obsolete systems. Many food businesses fail, and many try to do it manually. Don't. (Don't.) We have seen many companies make costly inventory mistakes when their inventory management systems need to allow them to manage both expiration and attribute. One distributor accidentally sent organic strawberries to customers who were paying for nonorganic ones. One distributor should have fulfilled a customer's urgent need for additional products. This was because the customer service team of the distributor needed more information about when the next batch would arrive from the supplier. Supervisors can be alerted to possible mix-ups by using real-time inventory management software. Imagine an operator pulling the wrong item. Your people might prefer to find out this after the fact or while they still have time to rectify it. We'll take our word for it: the drinks packager who accidentally used the wrong flavor concentrate drum had to stop the line for 4.5 hours to get it out and put the right flavor in the tanks. An alert would have been appreciated. Substitutions can also be affected. Supervisors will only give operators a correct substitute if they have an automated list of substitutes. Your operators will be able to see the next-best substitute if they run out. A flavorings company saw its on-time delivery rates increase by 20% after it was able to manage substitutions according to date and attribute codes.
The use of non-integrated systems that don't support real-time information can lead to confusion, risk, and revenue loss.
How much control do you have over date-sensitive inventory? How much control do you want? Are you able to perform the following tasks with your inventory management system?
- Use date codes and attributes to manage.
- Not selecting the "best" item? Alert operators
- To ensure ingredients are updated and kept from being thrown away, recommend and prioritize the best substitutes.
- As you make substitutions, track what went into each batch.
- Connect attributes to customers and orders
- To prevent stock overstocking, provide clear predictive models available on-demand
- To avoid contamination, trace the usage of products and map where they are kept.
- Encourage your managers and operators to make intelligent business decisions.
- You need support options that allow you to get the right date-sensitive products at the correct times to your customers. A date control is not a feature that's optional or a luxury. It's essential. Innovative manufacturing platforms help you streamline your manufacturing process.
It's time for your inventory management system to become smarter and keep up with industry requirements and demand planning.
Food and beverage are highly competitive. Do you want to open the door for a competitor or lose valuable retail placements? Don't let inefficiency leave you with no profit. You want to comply with regulations. Consider how customer service and profit margins could be improved if overhead was reduced and efficiency increased by automating and removing silos. Talk to an outside expert about your inventory management system. They can help you evaluate it and show you what is possible.
Conclusion
The system will be more efficient and can also optimize the inventory to reduce resource consumption. The creation of an enterprise information management platform aims to enhance long-term management ideas and create a resource management strategy that is optimized. Additionally, it optimizes the distribution of corporate resources. Enhancing core management competencies. To optimize budget management in financial management, enhance corporate budget management systems, and accomplish long-term strategic goals, the ERP system's multifunctional data analysis capabilities are leveraged. An extensive overview and analysis of the budget management system are provided in this study. For a manufacturing company. It also proposes improvement suggestions to address the problems and defects that may occur during its application. The system is designed to optimize the allocation of resources and how it can manage inventory and improve human resource management. This will allow the enterprise to maximize the benefits of the ERP system, covering business workforce management and inventory control. ERP aims to increase the whole industry's use efficiency. This will enable retailers to handle inventories more effectively, and the procedure can be utilized to cut losses and promote greater industry growth.