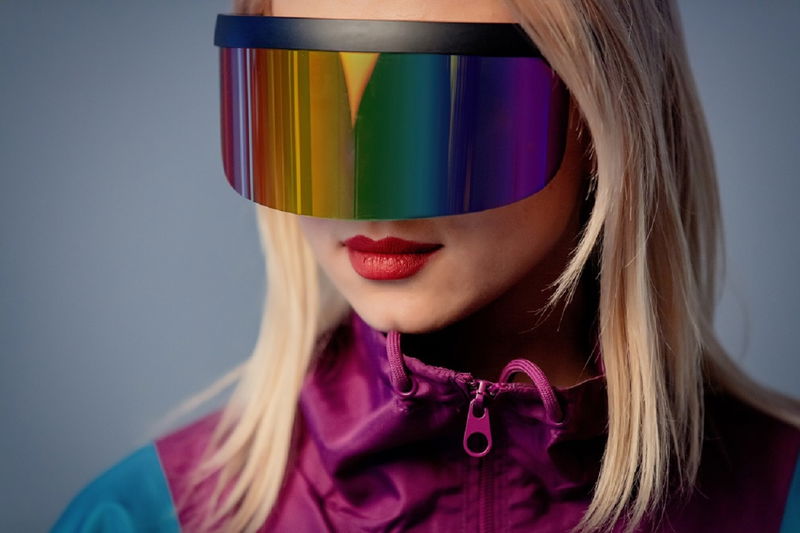
At the core of repair and maintenance lies efficient management: when unexpected breakdowns or equipment failures threaten productivity levels unexpectedly. Businesses from diverse industries have taken an innovative approach toward operational excellence by harnessing custom repair management tools like Arion repair management, which have played an invaluable role in streamlining operations, cutting downtime, and catapulting productivity to new heights.
As we embark on this educational voyage through repair management tools, this blog seeks to shed light on their transformative potential and real-life tales of triumph involving organizations confronted with breakdowns but that have emerged more muscular, more efficient, and resilient thanks to repair management solutions. Join us as we delve deeper into this fascinating world and unravel success stories about how breakdowns turned into breakthroughs.
What is a Custom Repair Management Tool?
Custom repair management tools are software applications or systems specifically tailored to assist and streamline repair and maintenance operations within an organization. Unlike generic systems available off the shelf, custom tools are explicitly tailored to meet specific businesses or industries' unique requirements and demands.
Key Features And Functionalities Of A Custom Repair Management Tool Could Include:
Work Order Management
This tool empowers users to efficiently create, assign, and track work orders for repair and maintenance tasks by giving readings directly to relevant personnel or teams.
Asset Tracking
Organizations can monitor the status and condition of their assets, equipment, or machinery in real time to monitor asset performance maintenance history and identify when repairs or preventive maintenance is due. This feature facilitates continuous business operations.
Scheduling And Dispatching
This tool empowers users to schedule maintenance tasks, allocate resources efficiently, and dispatch technicians or maintenance crews efficiently. Furthermore, this application optimizes personnel allocation based on skillset, location, and availability.
Inventory Management
Organizations can manage their inventory of spare parts and supplies needed for repairs with this tool, helping ensure optimal stock levels while decreasing overstock or stockout situations.
Reporting and Analytics
Custom repair management tools typically feature robust reporting features for users to generate reports on repair history, asset performance, costs, and more - providing users with data to help inform decision-making and drive continuous improvement efforts. This data-driven approach aids decision-making while driving ongoing improvement initiatives.
Integration
Integration can take the form of interfacing the tool with existing systems or platforms such as asset management systems, IoT devices, or accounting software to facilitate seamless data flow and ensure effective collaboration among various departments.
Mobile Access
Many custom repair management tools feature mobile applications or web browser access for technicians and field personnel to manage work orders, update statuses, and gain information while on the move. This enables access to work orders quickly while on the road or when accessing information remotely.
Customization
The tool can be tailored to an organization's unique requirements, industry, or workflow process. Customization allows adding features that align directly with an organization's operations.
Custom repair management tools can be particularly advantageous to businesses and industries with complex repair and maintenance needs, where off-the-shelf solutions may need to catch up in meeting those demands. Such tools improve operational efficiencies while decreasing downtime - leading to cost savings and enhanced asset reliability.
Repair Management Tools Have Evolved From Manual to Digital Format
Before we venture forth into exploring remarkable success stories, we must trace the fascinating story of repair management tools' historical development and profound significance. From humble pen-and-paper systems to modern digital marvels that harness data analytics for automation, these remarkable systems have seen an incredible transformation.
A Brief Look Into Traditional Approach: Past Perspective
At one time, repair and maintenance tasks were conducted using manual processes. Picture this: technicians using pen and paper to navigate an intricate maze of paperwork, spreadsheets, and phone calls to coordinate repairs. While this approach might have worked at first glance, errors soon found their way in as delays crept in and inefficiencies overtook everything that went into it.
Manual paper-based systems could often cause critical maintenance tasks to slip through the cracks like grains of sand falling between stretched fingers. There was always a risk of miscommunication, oversight, and data inconsistency, jeopardizing the efficiency and effectiveness of repairs and maintenance processes.
Digitization: Harnessing the Potential of Technology
As the digital revolution spread, an extraordinary transformation occurred within repair management. A wave of possibilities and efficiency opened up with digital repair management tools - software applications designed specifically for repair operations - arriving on the scene.
These digital marvels brought many features and capabilities that revolutionized how repair and maintenance were managed. Work order management became an automated, seamless process; tasks could now be assigned, tracked, completed with one click, or reported instantly to management via fundamental time reporting tools. Asset tracking became much simpler thanks to real-time monitoring capabilities in these tools that provided real-time monitoring reporting of equipment status in real-time.
Scheduling was no longer complex; it became efficient, providing precision and timeliness in scheduling operations. Inventory management made significant strides by giving insight into spare part availability while optimizing procurement practices; finally, reporting enabled organizations with data-driven insights into their repair and maintenance operations for strategic decision-making and continuous improvement efforts.
As it turned out, the digital transformation of repair management tools opened many opportunities. Gone were the errors, delays, and inefficiencies of old, replaced with an efficient data-driven strategy designed for today - and the future.
As we explore success stories, we shall see how the digital tools, including the repair management module, have revolutionized operations while pushing past what once seemed possible. Be inspired by stories of organizations that have harnessed technology's transformative potential, utilizing tools like the repair management module, to turn failures into unique innovations.
Success Stories of Turning Breakdowns Into Breakthroughs
Let's now examine some success stories where custom repair management tools have played an instrumental role in increasing efficiency, cutting costs, and strengthening operations overall.
Case Study 1: Manufacturing Marvel Comics
Problem: A large manufacturing company needed help managing and tracking maintenance tasks for its extensive machinery fleet. Breakdowns caused production delays while increasing operational costs significantly.
Solution: The company integrated a customized repair management tool into their equipment. This allowed maintenance teams to schedule preventive maintenance tasks, track real-time machine performance, and receive automated alerts of potential issues.
Results: Within several months, the manufacturing company saw an astounding reduction in machine breakdowns and downtime, leading to greater production output and cost savings due to more effective decision-making and resource allocation using this real-time data tool.
Case 2: Fleet Management Success
Problem: A logistics company operating a large fleet faced difficulty managing vehicle maintenance and repair schedules effectively, leading to unscheduled breakdowns, which increased costs and negatively impacted delivery schedules.
Solution: For fleet maintenance, the logistics company deployed a tailored repair management tool explicitly designed to track vehicle history, schedule preventive maintenance visits, and manage spare parts inventory. This solution successfully addressed their challenges in fleet management.
Results: The company experienced a dramatic decrease in unplanned fleet breakdowns. This enhanced reliability and customer satisfaction and enabled on-time deliveries of products to customers. With reporting capabilities available through this tool, analysis could take place for further optimization efforts by making data-driven decisions to reduce maintenance costs further.
Case Study 3: Hospital Efficiency
Problem: A large hospital faced difficulties managing maintenance for its critical medical equipment, with downtime potentially having life-threatening results and impacting the budget.
Solution: The hospital implemented a custom repair management tool tailored specifically for healthcare environments, which integrated with their equipment database and allowed scheduling routine maintenance, calibration, and immediate responses in case of equipment malfunctioning.
Results: The hospital saw significant equipment uptime and reliability gains, leading to better patient care and lower emergency equipment replacement costs. Furthermore, this tool ensured compliance with regulatory requirements regarding medical equipment maintenance.
Case 4: Property Management Success
Problem: An experienced property management company needed help maintaining multiple properties efficiently. Requests from tenants for repairs or maintenance work were often ignored or delayed until repairs could be scheduled, leading to their disappointment and dissatisfaction with management services.
Solution: The property management company implemented a custom repair management tool that allowed tenants to submit online maintenance requests directly, automated work order generation, and allowed property managers to track repairs in real time.
Results: Tenant satisfaction was significantly enhanced as repair requests were addressed quickly, leading to higher retention rates and reduced vacancies at the property management company. Its reporting capabilities provide insight into maintenance trends for proactive upkeep.
Related:- Quick Overview Of An Efficient Repair Management Software
Case Study 5: Advance Aviation Maintenance Services
Problem: An aviation company operating a fleet of aircraft needed help overseeing maintenance and repair on their planes due to their complex nature. Aviation maintenance regulations can be strict, leading to any oversight having serious repercussions that threaten flight safety, so this company needed a solution that ensured flight safety while cutting costs by minimizing downtime and downtime costs while optimizing flight performance and downtime costs.
Solution: The aviation company employed a customized repair management tool tailored explicitly for use within aviation. This system integrated seamlessly into the onboard systems of each aircraft to provide real-time data regarding equipment health and performance; additionally, it enabled scheduling routine maintenance checks and giving immediate responses for identified issues.
Results: The aviation company experienced significant improvements in aircraft reliability and safety using the predictive maintenance capabilities of this tool to replace components before failure occurred proactively, thus decreasing unscheduled maintenance requirements and cancellation/delay charges as a result of reduced flights - ultimately providing enhanced customer satisfaction as well as cost savings to their bottom line.
Case Study 6 - Oil And Gas Operations Optimization
Problem: An oil and gas exploration and production company faced operational challenges in overseeing its remote facilities such as oil rigs, pipelines, and processing plants. Ensuring their reliability and safety was vital, given the environmental risks inherent to this industry.
Solution: The company created and deployed a unique repair management tool tailored to the oil and gas sector, using IoT sensors and data analytics to monitor equipment conditions in real time and provide predictive maintenance recommendations, facilitating proactive repairs or component replacements.
Results: Implementation of this tool led to significant reductions in unplanned downtime and equipment failures by identifying maintenance issues before they escalated; operational safety was improved as environmental compliance improved, and resource allocation and cost control improved significantly.
Case Study 7: Raising Educational Institutions
Problem: An educational institution with multiple campuses was challenged with overseeing its facilities and infrastructure maintenance effectively, particularly repairs, which caused disruptions in classes or administrative activities that hindered overall student education and negatively impacted its learning environment.
Solution: The educational institution deployed a custom repair management tool for campus facilities management. Staff, faculty, and students could submit maintenance requests through an intuitive portal interface; work orders were automatically generated based on priority and location criteria and assigned accordingly to maintenance teams.
Results: The institution saw significant improvements in its maintenance operations efficiency. Repair requests were addressed quickly, minimizing disruptions to classes and campus activities, while its reporting capabilities enabled better resource allocation and budget planning, resulting in cost savings.
Case Study 8: Retail Revolution
Problem: A national retail chain operating multiple stores was experiencing difficulties managing maintenance and repair for all their stores, with breakdowns and maintenance delays hindering customers' shopping experiences and negatively affecting sales.
Solution: The retail chain implemented a custom repair management tool explicitly tailored for retail industry use. This allowed store managers to submit maintenance requests such as HVAC malfunctions, lighting problems, or store fixture repairs quickly through this system - also connecting quickly with suppliers and service providers to facilitate prompt responses from suppliers and service providers.
Results: The retail chain experienced significant improvements in store maintenance and customer satisfaction as store managers could request and track repairs more easily, creating an enjoyable shopping environment. In addition, reporting features allowed them to identify trends and address long-term maintenance costs more effectively, thereby cutting long-term expenses down significantly.
Key Takeaways From Repair Management Tools Custom Built for Businesses
These success stories illustrate the transformative potential of custom repair management tools across various industries. Such solutions have enabled organizations to address operational challenges, reduce downtime, enhance safety measures, boost customer service satisfaction, and achieve cost savings.
As We Conclude Our Investigation Of These Success Stories, Here Are A Few Key Takeaways:
Customization is Key
Tailoring repair management tools to specific industry needs and environments is integral for their success, with customization guaranteeing they meet any organization's specifications perfectly.
Data-Driven Decision-Making
Organizations can leverage real-time monitoring capabilities combined with analytics data for informed decisions about resource allocation, allocation of personnel effectively, and implementation of predictive maintenance strategies.
Proactive Maintenance
Custom repair management tools enable organizations to move away from reactive to preventative maintenance practices, leading to fewer breakdowns, reduced downtime, and greater operational efficiencies.
Enhance Customer Satisfaction
In industries where customer experience is at the core, these tools contribute to higher customer satisfaction by assuring reliable services with limited disruptions and providing high-level support services to keep them satisfied.
Cost Control
Cutting maintenance and repair expenses, allocating resources more effectively, and managing inventory efficiently are three strategies for saving costs that could make an accurate, impactful statement to investors about an organization's profitability.
Compliance and Safety
For industries subject to stringent regulatory standards, custom repair management tools offer the solution needed to ensure compliance and enhance safety.
Modern businesses recognize the significance of operational efficiency and reliability for success; therefore, custom repair management tools have become indispensable resources across various sectors. By investing in these tools and adopting digital transformation initiatives, businesses can effectively tackle breakdowns and maintenance requirements with improved productivity, safety, and customer service levels, resulting in lasting successes in productivity and customer service levels.
Unlocking the Benefits: How Custom Repair Can Benefit Your Car
Transforming Organizations With Repair Management Tools
Our earlier narratives in this blog showcase custom repair management tools' incredible impact on organizations. Not just tools; these digital wonders serve as catalysts of transformation to bring about operational excellence across many fields. Let's dive further into the remarkable advantages these tools bestow upon organizations.
Reduced Downtime: The Silent Efficiency Booster Can Dramatically Cut Your Downtime.
Custom repair management tool with preventive maintenance scheduling and real-time asset monitoring capabilities are adequate safeguards against unscheduled downtime, leading to significant increases in operational efficiency for organizations. No longer caught off guard by unexpected breakdowns, businesses take proactive measures to keep operations running smoothly.
Cost-Saving Strategies for Tacticians
One of the key advantages of these tools is their impact on an organization's bottom line. By reducing breakdowns and optimizing maintenance schedules, organizations can substantially cut repair and replacement costs while simultaneously cutting inventory management costs significantly - mitigating overstuffed storerooms and shortages in essential spare parts.
Improved Productivity With Symphony
Custom repair management tools offer unparalleled precision when orchestrating processes and workflows with their remarkable precision. By simplifying tasks and automating previously complex workflows, they usher in an unprecedented period of productivity that ensures maintenance teams no longer are bogged down with administrative hurdles; instead, they focus their energies on planned tasks to keep the industry running efficiently.
Data-driven Decision-making With the Sage Advisor
Custom repair management tools serve as essential advisors in today's data-centric age, offering valuable data and insight for organizations looking for ways to optimize equipment performance and maintenance trends - equipping organizations with informed decision-making power and providing for precision resource allocation decisions. They demystify equipment performance trends while uncovering maintenance patterns to enable informed decision-making by organizations. These tools also lay bare the path forward, so resources are allocated with care and precision for maximum ROI.
Increased Customer Satisfaction: The Customer Whisperer
Industries where customer satisfaction is the cornerstone of success often utilize customer support tools as essential ingredients. Downtime and delays are no longer tolerated as organizations deliver timely service repairs - leading to more than simply customer satisfaction and creating loyal clients. Organizations find their clientele not only satisfied but steadfast supporters of their brand!
Compliance is an Upholder of Integrity
Industry titans complying with stringent regulatory requirements can turn to custom repair management tools as the way forward. By tracking and documenting maintenance activities and assuring their compliance, custom tools provide businesses the stability to move ahead knowing their position on solid ground is secure.
Find Your Custom Repair Management Tool
Choosing the ideal custom repair management tool is like selecting an extraordinary work of art for your organization's operational canvas, carefully considering its individual needs, aspirations, and grandiose goals. Let's set off on an adventure as we uncover all of the factors that should guide the selection of a tool that can orchestrate efficiency and success within your enterprise.
Industry Specificity
Custom repair management tools need to create harmony across their canvas of custom repair management software applications, so choosing an industry-specific tool that fulfills its promise can create a theme for any organization in any sector - manufacturing, healthcare, logistics, or property management - is vitally important. It must resonate with industry best practices so it speaks the same language of your field seamlessly.
Scalability
An effective tool as organizations advance toward expansion and growth, their custom repair management tool should remain a steadfast companion. Adaptable enough to accommodate an increasing number of assets, equipment, and users without suffering performance degradation as the organization expands - your tool must adapt as you grow not to disturb operational harmony!
Integration Capabilities
In an age where information is the lifeblood of business operations, integration capabilities provide the conductor for its orchestra. Your chosen tool must seamlessly sync up with all existing systems, such as asset databases, ERP software, or IoT devices, and ensure data flows smoothly like music from one system into another, forging an integrated, coherent ensemble of information and knowledge.
User-Friendly Interface
A tool's user-friendly interface serves as the canvas upon which technicians, maintenance teams, and other users create masterpieces of efficiency. Ideally, it should be intuitive and user-friendly, like the notes of an appealing sonata, making navigating and using it intuitive so your workforce can channel its talents effectively without hindrance or obstruction.
Reporting and Analytics
Custom repair management tools offer rich reporting and analytics features to give insight into all facets of maintenance performance. Please select one that offers robust features so you can assess intricate maintenance performance issues such as cost trends or measuring equipment reliability; they should serve as trusted guides on the journey toward informed decision-making with customizable reporting features that meet the unique requirements of their user base.
Mobile Accessibility
In today's mobile-driven world, any tool lacking mobile accessibility is likened to being without instruments - leaving technicians unequipped for receiving orders, updating statuses, or accessing data in the field. Your chosen tool must, therefore, allow technicians access to information. At the same time, they're out on work orders - acting like the rhythmic pulse that keeps all stages in harmony while dispersed across geographical spaces.
As your selection process for custom repair management tools begins, each decision you make is essential in orchestrating an operational opus for your organization. Every factor considered and every note weighted contribute to creating the masterpiece your organization aspires to become. As you embark upon this selection journey, may you discover an instrument that fits seamlessly with your goals and aspirations, and may we wish that all those embarking find what they seek!
Conclusion
Custom repair management tools, especially those like the Arion repair management module, have emerged as standout performers in industry and enterprise, wielding batons of transformation to conduct organizations through turbulent waters of breakdowns and maintenance inefficiencies toward more reliable shores of productivity and reliability.
Here, we have discussed tales of success and triumph that illustrate the tangible advantages these tools bring organizations. These tools serve as sentinels of reduced downtime while protecting operational efficiency. Companies need thrifty tacticians who steer organizations away from repair and replacement costs. Orchestrators of productivity help organizations avoid sinkholes of repair costs by orchestrating an orchestra of productivity that transforms erstwhile chaos into an orderly array of well-executed tasks. Data consultants act as wise counsel, leading organizations toward data-driven decision-making while imparting insights and wisdom. Customer satisfaction experts ensure promises fulfill and exceed customer expectations while guardians of integrity maintain compliance against regulatory storms.
Under today's economic pressures, downtime is something other than what any organization can indulge in. Organizations that embrace customized repair management tools rise to operational excellence by equipping themselves with tools explicitly designed to increase competition and resilience while being ready to transform breakdowns into spectacular breakthroughs.
Want More Information About Our Services? Talk to Our Consultants!
Organizations engaged in manufacturing, logistics, healthcare, or property management can all utilize custom repair management tools as navigation tools toward greater efficiency and success. An adequately chosen tool acts as your guide as you steer toward shores of efficiency and reliability where success awaits!
As this symphonic journey concludes, may you, dear reader, take inspiration from its inspiring tales of triumph and transformation. May these words motivate you to find an appropriate custom repair management tool that echoes your organization's unique blend of efficiency and reliability, for in its embrace lie the keys to operational excellence - where breakdowns become opportunities to achieve amazing breakthroughs!