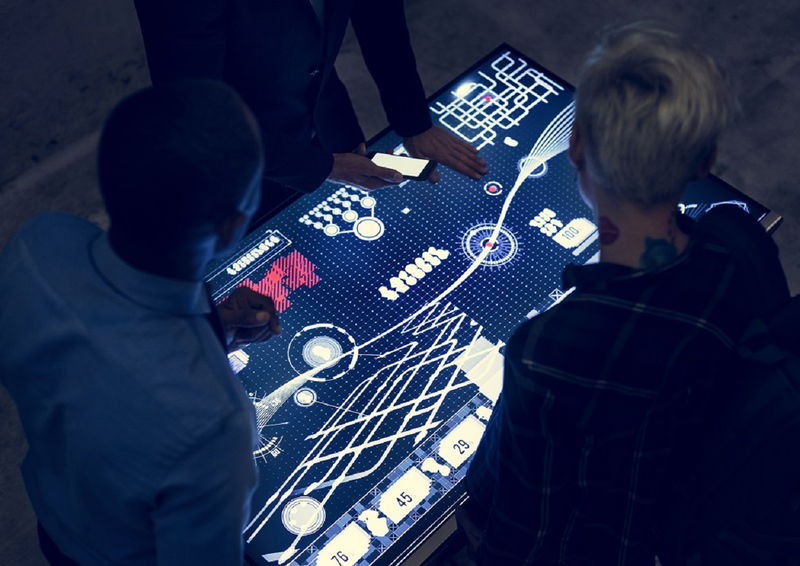
This post will cover the benefits of service repair management software and what you should look for when choosing a solution. It also explains how the technology has evolved within the field services industry.
Find out the Key Advantages of ERP in Repair Management
Support In Managing Repair Teams
ERP software provides the ideal way of effectively overseeing teams of repair module technicians. ERP can assist in overseeing teams responsible for various repairs types and equipment; its intuitive user interface enables teams to be easily created while tasks are managed efficiently to ensure task completion is accelerated quickly and efficiently by external or internal repair teams as well as emergency support teams; there may even be specific teams set up specifically to manage computers, machines etc.
Repair Requests are Easy to Make
Preventive Repair and Corrective Repair are among the many different forms we have discussed. For every operation, they require submitting requests to their repair teams. An ERP allows users to submit repair module requests electronically while quickly communicating with repair teams regarding urgent work, an efficient way of communication that speeds up this process.
Management Of Equipment And Categories
Industry success depends upon effectively overseeing multiple equipment pieces: computers, manufacturing machines and other devices may need to support work centers, offices or support systems - for instance, printers, scanners, and support systems must all be managed effectively in an ERP. Devices should also be classified based on type or manufacturer and listed with warranties periods or repair schedules within its system.
Performance Analysis
Most ERP systems allow you to analyze the employee's performance. ERP tools can help you evaluate the number and type of repairs requested. ERP reports can be used to improve our repair system. Using the support system, you can also get an overview of the number and type of machines that have been repaired or scrapped. We can assess the progress of repair requests assigned to specific employees.
Quick Configuration
Once you use ERP, there is no need to maintain different log books or files for managing the equipment list and repair schedules. ERP allows you to configure equipment and repair teams quickly. The configuration of different repair teams will help people identify which team is in charge of repairing the equipment. Managers can also create equipment categories and assign them to specific repair teams.
Documentation Made Easy
It isn't easy to keep track of all the activities when you manage a large industry. You will also have to record all your work, from the easiest to the hardest. You can easily document your repair activities with an ERP system. You can easily record all repair-related activities, including preventive and corrective repairs and repair calendars. It is possible to list the completed repairs and current and future works efficiently.
Quick Scheduling Support
Planning repair works is crucial to successful completion on schedule, whether preventive repairs are being scheduled in advance, corrective ones requested upon, or emergency ones requested, then planned accordingly by priority and emergency levels. By working more efficiently together as a team and prioritizing repair orders according to priority or emergency, repair teams will ensure work gets completed without equipment becoming dysfunctional, negatively impacting labor hours; repairs also help avoid severe damages inflicted on machines that prevent future breakdown. ERP software is useful in streamlining these processes, ensuring offices and work centers run all year round effectively, and ensuring efficient operations are always efficient for offices or work centers.
Repair Management Software: How it Overcomes the Challenges
Adopting an integrated solution for repair management can provide OEMs and businesses with service management several advantages. The top benefits include:
- Remove outdated paper-based methods OEMs and FSOs know the paper volume and speed. Software for equipment repair planning eliminates time-consuming, error-prone methods.
- Improved efficiency Repair planning software enhances all aspects of the planning process, from customer contacts to scheduling and technician availability. Depending on your software, billing and payment options may be included.
- Real-time scheduling The best equipment repair software offers real-time insights to all parties involved, including technicians and clients. FSOs can send a notification or messages using mobile apps. This allows them to communicate all important repair information about a particular job. Device type, customer history, location, arrival time for repair technicians, status of work indicators, etc.
- Greater control and visibility repair software allows businesses to see where, when, and what their technicians do. They can use the information to improve service quality by service provider. The results of customer surveys can also be used to track performance metrics and provide actionable insight into service quality.
Criteria of Evaluation for Innovative Repair Management Software
Not all software for service and repair is the same. Consider the following benefits, features and functionalities when evaluating solutions.
- Mobile Services- Select mobile repair software compatible with the device to provide workers with all necessary information on the go. Mobile access is available to all work orders, warranty information, parts inventory and equipment history.
- Contract Management- The graying workforce is a growing trend for many FSOs, OEMs and FSOs. It's important to select software that allows you to manage full-time and blended workforces. Ask the vendor if the software for equipment repair technicians is easy to integrate. Does the software make it easy for employees and contracted technicians to use?
- Self-Service Customer Portal - In today's business world, customer portals are no longer an optional feature. They have become a standard part of any solution that is customer-centric. For example, 88% of customers in the United States expect that brands have an online customer self-service portal. Your repair management software must also be able to serve your customers' needs. Software that has a self-service portal is a good choice. Features to look for include:
- A simple-to-use customer portal.
- Live job updates.
- Locations of technical repairs.
- Communications.
- This minimal level of control and transparency can increase customer satisfaction.
- IoT Servicetization and Predictive Maintenance- IoT devices used by the service sector are more than just consumer products. These include company computers, workers' mobile devices and intelligent home appliances. IoT can help companies improve their profitability. IoT devices, for example, can transmit critical data in real-time to workers so they can diagnose the problem better. It improves the efficiency of preparation, service and workflows. Predictive maintenance is a form of servitization that allows companies to improve customer retention and profitability. OEMs, FSOs, and AI can use data analytics and IoT to prevent equipment failures. They will send technicians out before the equipment fails.
- Augmented Reality AR (Augmented Reality) is a new interactive experience that enhances the real world by adding computer-generated 3D elements to an already existing environment. This all happens in real time. AR is also a great visual tool for field workers, as it can overlay device diagrams and instructions onto equipment. Technicians can access This critical information in the field to help them complete the repair on their first attempt.
- Major Brands - Ideal appliance scheduling software should work with major brands. It is important that software can handle high-profile clients and serve brands technicians know. Ask the following questions: Is the software compatible with major brands of appliances, and does it provide real-time data on appliance manuals and parts inventories?
Why Do We Need an ERP for Repair Management?
Manufacturers and vendors still bear responsibility once a product has been sold to its customer. After-sale services should be offered as necessary. It's especially crucial that long-lasting items, like refrigerators, are repaired properly to extend their useful lifespans; otherwise, problems could occur sooner.
A repair can be defined simply as correcting mistakes; repair can turn an inoperable product back into usability or functionality, thus supporting business expansion and maintaining profitability. Repair effectiveness is of utmost importance in any firm wishing to maintain 100% support from their customer base; unfortunately, managing every request manually would likely prove unmanageable; an ERP tool can assist by linking repairs with tasks and alerting team members of deadlines for completion of repairs.
This marker features various tools designed to aid Repair management. They offer comprehensive support in recording all repairs-related requests or queries and prioritizing and prioritizing them accordingly. In this blog, we discuss why an ERP should be utilized as a part of their repair activities management strategy and explore its many customer service benefits.
Why ERP is the Best Choice for Repair Management?
Repair Order Management Made Easy
All actions within an enterprise should be undertaken carefully and methodically, from tasking management, priority assignment and system administration, through to creating service orders with ERP tools when clients request repair of products - it provides regular updates regarding progress as well as allows preparation of repair orders and documentation of repair orders.
Tracking Product Repairs Efficiently
Tracking repairs efficiently is often one of the biggest headaches for companies when managing repair operations; however, an ERP system makes this much simpler and more efficient. Tracking progress becomes easy by entering necessary details on a single platform and creating repair requests. Once done, the team marks completed repairs in their tool. With just a click, the manager of our repair team can view and view orders with their statuses; cancellation processes become irrelevant.
Managing Guarantee And Warranty
The company may offer different repair services, so the invoice for the repair will vary. The company might be required to perform all repairs for free if a warranty covers the product. A product that does not have a warranty can still be repaired for a charge. The ERP-assisted repair management makes it easy for users to calculate payment and track warranty.
Read More: Spotlight On An Efficient Maintenance Management Software
Complete The Work On Time
An organized system makes repair work simpler to accomplish. A team dedicated to repair management will find tracking all requests and progress much simpler; customers will get their products fixed as quickly as possible; ERP tools may also help manage prices or track product location more accurately than they could before using these tools; team efficiency will increase as these ERP tools allow the creation of repair reports; the entire process can also be monitored from its creation right through until completion.
Customer Satisfaction
Customer satisfaction should always be the top priority, whether assessing quality, repairing or delivering products. A company that effectively manages tasks can guarantee customer happiness; after-sale repairs play an integral part in customer retention - when companies respond promptly to customers requiring repair work, they tend to remain loyal customers; otherwise, they could end up breaking relationships completely due to poor service provided or delayed responses when their repair request comes through.
Integration with other Tools
ERPs are available in different versions or modules. The repair operation should be a part of the manufacturing and sales industries. The repair tool should support many different operations. Most repair tools have been designed to be compatible with other advanced tools, especially manufacturing ones. The repair tool is not only used for the tasks that customers assign but also to fix products with manufacturing defects. The business will avoid scraping manufactured goods.
Simple Invoicing
All businesses need invoicing assistance. Invoice generation is supported by software systems that enable repair management. The invoices can come in different forms when it comes to repair. It is possible to generate the invoice before or after the repairs. Charging a repair fee or creating an invoice in certain situations may be unnecessary. Sometimes, a product may be offered with a free warranty or service. Software assisted in repair can also be the most beneficial for businesses because of its integration with payment gateways and invoice address management.
Repair Management Trends - Future Of Automation
Repair management software is a great investment for your company if you have benefited from computerized repair systems or software. Repair management software must be constantly updated because technology is rapidly changing. The latest repair management trends and their methods of repair management are discussed.
Utilizing Cloud Computing
Cloud-based software has quickly gained popularity among companies due to its convenient nature and accessibility across devices. It provides quick decisions with live data available immediately. Installation can also be easily managed. Cloud repair management solutions also make decision-making faster as data can be readily accessed at all times allowing companies to make smart decisions more rapidly.
The software provides maintenance teams with push notifications via SMS and email, helping teams communicate more efficiently between technicians, managers, and customers and repair management software in the cloud. Communication also improves as technicians use work orders data to set priorities more easily; with API (Application Programming Interface), devices that are internet enabled can share data easily between themselves and repair management software in the cloud, whether your assets are located onsite, on mobile devices or globally distributed they will generate automated maintenance requests allowing preventive maintenance to work more effectively than ever.
Predictive Maintenance Is Better Than Preventive Maintenance
Repair management software has evolved significantly in the last several years to shift away from reactive maintenance towards preventive solutions, with businesses being able to save up to 18% in budget expenses by quickly responding to any problems that arise. Predictive maintenance could replace this approach more efficiently.
59% of respondents in one survey identified predictive maintenance as one of their favorite features of repair management systems. Predictive maintenance tools provide real-time information to facility managers, owners of businesses and repair professionals about what assets require more attention in terms of repairs or maintenance; unlike traditional management advanced tools, it measures reliability instead. Furthermore, predictive maintenance saves your staff time and energy by eliminating guesswork regarding the priority of asset maintenance - particularly useful for companies managing an array of equipment assets at once.
Artificial Intelligence, The Internet of Things, and Internet 4.0
Modern technologies such as Internet 4.0 and artificial intelligence will have an immense influence on industrial plant maintenance automation in the future. A repair management system must incorporate machines that utilize artificial intelligence or their ability to self-regulate with computerized machines to preserve human elements within an automated repair management system. Internet 4.0 allows computers to communicate without human interference while smart devices monitor themselves without technicians as an aid; maintenance managers have access to real-time data for managing maintenance operations more effectively and taking preventive actions in response to potential unforeseen issues.
Businesses are using IoT to manage assets more effectively. Predictive maintenance allows real-time decisions about asset management to be made quickly; maintenance will become a profitable function instead of an expense center; data gathered via IoT allows faster maintenance audits than ever.
Intelligent Data-Driven Maintenance
As we have already mentioned, many software firms that offer repair management are embracing artificial intelligence algorithms and machines. It will be possible to use more data-driven alternatives for maintenance. With these advanced customizable options, you can streamline future certifications, audits and root-cause analyses via advanced capabilities in business organization operations.
Adding Value
Repair management software needs continuous improvements; regular updates to its features will keep it relevant and in sync with industry changes and client trends. Repair management software providers must keep in touch with clients and understand trends to build future-ready companies; what changes have occurred within an industry? Does the current repair management software meet those demands? Additionally, features applicable across industries must exist that make this solution applicable - are providers willing to collaborate on individual client requirements to implement unique features?
Repair management software should also be flexible enough to adapt as smaller organizations or enterprises expand. They have different requirements than major grain elevators or utility corporations.
Read More: Maintenance Management Software 2023: The Ultimate Guide
Mobile Use
A desktop-based software for repair management makes it easy to create, track, and assign work orders. However, to view them, you still need a computer. Why not make use of the mobile phones that everyone carries? You need a repair management app that is mobile-friendly. Mobile repair management software offers many benefits to technicians. Repair management software aims to simplify the use of features and mobile operational functionality.
Build A Culture That Values Reliability
Industry 4.0 encompasses many topics; however, implementation begins with people. You should prepare maintenance staff members for any changes in new procedures or systems; you should establish an ongoing improvement culture immediately.
First on your agenda should establish guiding principles to support optimal maintenance practices. The next step to ensure data integrity and develop healthy habits is to formalize processes in each area, from purchasing to work orders. Communication plays an integral part in creating trust and accountability among employees. Recognizing and rewarding those who adopt new practices encourages others to do the same.
Other Languages
As companies expand internationally, having a repair management program that speaks the local language can prove advantageous for all parties involved. New doesn't always equate to complex; when building on what's already working well, you don't necessarily need a complete redesign of all products (such as software). A well-organized software product designed specifically for repair management must also be easy for users and clients to appreciate regular refresher sessions on its latest features and software versions.
QR Codes Can Be Used To Organize Maintenance Information
Maintenance crews can easily find information when each asset has a unique QR code. The QR code is all they need to know the type of work or the priority level. It is easier to access and organize maintenance information.
Safety at Work
In 2023, industrial maintenance automation will focus largely on safety. The primary objective will be enhancing communication and collaboration among departments such as operations, maintenance, and safety; using company-wide technologies rather than isolated ones may enhance data exchange; by consolidating information from various sources, you may help your team perform duties at appropriate times, thereby improving both their effectiveness as well as creating an overall safer working environment.
Conclusion
Businesses relying on software specifically tailored for running maintenance operations depend heavily on repair management software, and it seemed worthwhile making predictions regarding its future development.
You should always think ahead about maintenance automation in the industrial sector to make the best use of both your short- and long-term investments, including human error reduction and collecting and assessing machine performance data to be an efficient manager of tomorrow. The maintenance manager of today will likely not recognize what lies in store. Get in touch with the best and most reliable software solution to manage repair operations effectively.