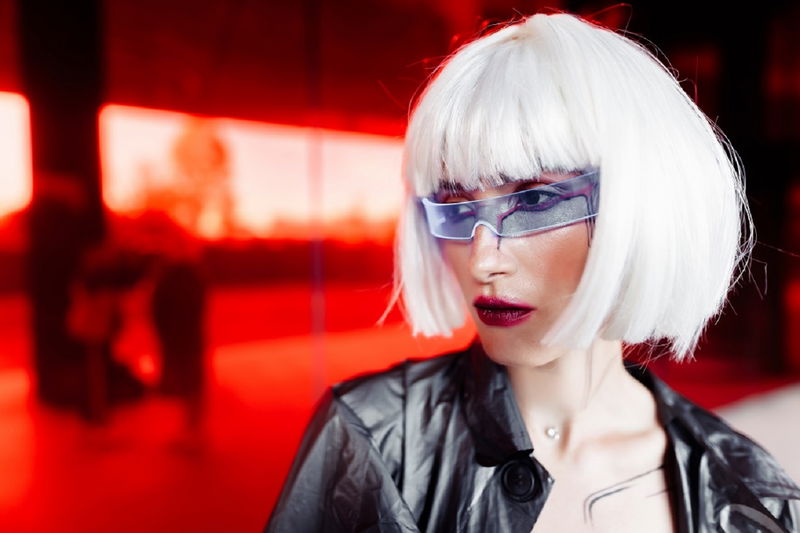
ERP Inventory Management allows midsize businesses to manage their day-to-day operations from a single platform, which includes finance, logistics, planning, and operations. It provides real-time information to help gauge complex workflows and facilitate advanced automation.
Inventory management is a critical skill that allows businesses to maximize profits while satisfying customers with the least amount of stock. As we can see, inventory management is all about data. Purchases, reorders, shipping, warehousing, storage, receiving customer satisfaction, loss prevention, stock turnover, and other factors are all considered.
This information can be found in many inventory management systems. Companies combining enterprise resource planning (ERP) with inventory management functionality have a competitive advantage. The main competitive advantage, however, is in real-time information sharing across different business units.
How can you improve efficiency?
You can get the visibility you need to manage and control your inventory levels with modern enterprise resource planning (ERP) software. It can help your company optimize inventory levels, increase warehousing efficiency and improve last-mile delivery.
Are You Having Trouble Controlling Your Inventory Management?
You will need many parts to make your custom-made products. As a small business requirement, you may not have the capital or space to purchase large quantities of raw materials in advance. Small and medium-sized custom manufacturers face many challenges. Managing inventory can make or break your business processes.
You can improve your inventory management by adopting best practices and investing in an inventory management system. This will help you keep your inventory under control and ensure that you have the right parts and quantity of parts on hand to avoid production bottlenecks. It will also allow you to finish jobs on time and deliver customer orders.
What is ERP Inventory Management?
Inventory management, as part of Enterprise Resource Planning (ERP), enables businesses to manage all aspects of their operations from a single platform. This includes inventory, finance, and logistics. ERP inventory management systems provide real-time inventory information for the entire company. This is a vital capability for companies wanting to grow, have complicated workflows or supply chains, require advanced automation, work in "just-in-time" mode, sell multiple products, or maximize inventory investments.
How ERP can Optimize Inventory Management?
Simply put, ERP systems provide inventory data that can be used to help business leaders make better and faster decisions. With the right platform, authorized users can access a central dashboard to analyze the following functions quickly.
- Logistics
- Finance
- Operation
- Stock
Accessing all this information in one place eliminates the need to go to different systems. This minimizes user error and increases overall efficiency.
Are You Looking for Inventory Management? Three Questions to Ask
Businesses can use these questions to assess their inventory management processes and systems.
1. Can my Existing System Help Me Plan?
Can your current system provide insight into inventory turnover rates, lead times, and sales (and to whom and when), as well as information on stock levels and replenishment?
2. Do We Have Strategic Insight From My Current System?
You need a system that can help plan for growth and keep you informed about changes in the market, especially with today's supply chain challenges. Stockouts can drive customers away from your company and lead to stockouts.
3. Are My Sales and Customer Service Teams Equipped With the Right Information to Provide a Quality Customer Experience?
With modern technology, all team members should have access to inventory information. Not only do you need to know what is in stock, but also where it is, when it will arrive, and how quickly it can be delivered to a customer.
Integration ERP With Inventory Functionality
Many manufacturing and end-to-end ERP systems offer advanced inventory management capabilities that global companies require. In contrast, other ERP solutions only provide basic inventory management functionality. These capabilities can be expanded by integrating an inventory management system into the ERP system.
They can have centralized access to many data-driven real-time insights with this integrated solution.
- Get updates
- Statuses for reorder
- Shipping times
- Storage capacities
- Warehousing Logistics
- Data collection
- Customer satisfaction
- Loss prevention strategies
- Stock turnover
This information can give companies a competitive edge by making it available in just a few clicks. This data allows companies to make better purchasing decisions and forecasts.
They can therefore meet unexpected spikes in demand and not keep excess stock.
Common Inventory Challenges
Stock Excess
You should avoid stocking excess inventory if your business sells seasonal products. This reduces liquidity and increases overheads. But, too conservative inventory forecasts could lead to severe shortages. Historical sales data can be used by ERP inventory management systems to determine realistic thresholds for satisfying consumer demand.
Stock Shortages
Stock shortages can be as costly as excess inventory. Losing a profitable product at peak times can cause financial problems and drive customers to the competition. ERP inventory management software allows you to define minimum inventory thresholds for each product. You can also modify the threshold limit according to business needs yearly.
The system will alert you to place a purchase order for a product whose inventory is below the threshold. An ERP inventory management software can be used with automation software to generate purchase orders and send them out automatically.
Dead Stock
Also known as obsolete inventory or dead stock, this is stock that hasn't been sold or is still in use. These non-profitable items can drain your bank account daily as they take up warehouse space. ERP inventory management systems keep track of expiry dates and product manufacturing dates. They also alert you when stock is no longer profitable.
Inventory Turnover
Inventory turnover can be defined as the ratio of inventory sales or replacements in a given period. To know when to reorder products or remanufacture them, it is important to keep track of inventory turnover. Inventory turnover can be calculated as the cost of goods sold divided by the average inventory value. This information can help you make informed decisions about pricing, manufacturing, and marketing and purchase new inventory regularly. This automates the process and helps businesses remain productive between reorders.
ERP Inventory Management: How ERP Inventory Management Benefits Your Company?
ERP systems use a variety of data sources to provide insight into the performance history and other information. Organizations use this data to make better ordering decisions and forecast future demand. ERP-driven inventory management increases efficiency throughout the supply chain. It can reduce double-handling and automate everyday tasks like reordering.
There are other benefits to incorporating ERP in inventory management:
Supply Chain Transparency: When a business can integrate back-end systems effectively and communicate directly with its partner, it minimizes disruptions like a critical part not being delivered on time or a product priced too high. Integration ERP systems allow for the synchronization of order and shipping information.
Improved Reporting: Exhaustive inventory data allows decision-makers to fully take advantage of data-driven insight, such as understanding the top-performing SKUs, landed cost per goods sold (COGS), and sales by channel and location. ERPs allow for custom reports, which are accurate and useful data.
More Accurate Counts: ERP systems track excess inventory, shortages, and planned replenishment and provide COGS and average turnover metrics. The warehouse system records and reports product transfers from shipping to receiving.
End-to-End Inventory Analysis: ERPs analyze every stage of inventory flow, such as the cost of goods sold and turnover rates. Companies can increase their inventory efficiency by analyzing key inventory metrics.
Quality Checks: Many ERP systems allow you to use logic to define inventory quality checks. You can indicate that products must meet safety or environmental standards. The system will then check the product safety information. The system will alert staff to make necessary changes if it detects that the item is not compliant.
Inventory Planning: Each product in the ERP has an inventory status. Customers, staff, and partners can view and check available numbers and order information. Your inventory history and metrics are easily accessible to ease planning and increase customer satisfaction. The ERP system guides staff through a well-planned and planned cycle counting process. Regular cycle counting is an important tool for inventory management and checks and balances.
Primary Benefits
Efficiency Increases
One source of truth is a centralized inventory management system that manages all business operations. This centralized approach reduces overhead costs and lowers costs. It also allows for automating day-to-day operations to improve productivity and increase competitive advantage.
Cost-Effective
Instead of focusing on specific resources or systems that can handle different sections of an organization, the ERP inventory management software handles multiple business segments simultaneously, reducing workload and expenses.
Transparency in the Supply Chain
Many businesses outsource their shipping needs to third-party logistics providers or shipping companies. ERP inventory management systems allow them to integrate with other providers to achieve full system collaboration. Order, inventory, and shipping information are synchronized across the supply chain to facilitate transparency in the supply chain.
Data Collection and Reporting
These systems allow for quality data collection and real-time updates on orders, stock, customers, and customers from a central location. These systems allow users to create powerful sales reports that provide valuable insights and track business performance, allowing them to plan for growth.
Inventory Analysis
ERP systems monitor and report inventory shortages and excess inventory. They also track metrics such as average turnover rate, cost of goods sold, etc. These systems also track shipment and transit times. Companies can increase inventory efficiency and customer satisfaction by tracking and analyzing key inventory metrics.
Quality Checks
Many ERP inventory management systems have built-in logic to aid in quality checks. The system can check whether products meet safety standards. It will notify you if an item is not in compliance.
Read More: Increase efficiency and productivity with ERP solutions
The Key Features
Stock Management and Tracking
Stock management is the process of managing inventory. This includes ordering, storing, and tracking inventory. This applies to all items a company uses to manufacture its products or services, including raw materials and finished goods.
Inventory is an asset that represents capital tied up. Managing stock effectively will allow you to free it up. Effective stock management involves assessing different stock types and acknowledging specific needs. It allows for reasonable stock levels while balancing surplus supplies and reducing the amount of capital tied up.
Stock tracking and warehouse management help to organize certain items. They can identify an item with a unique number and the location of that product. Small businesses can choose between periodic or perpetual stock management.
Warehouse Management
Warehouse management oversees and controls day-to-day operations such as shipping, receiving, goods choosing, workload planning, staff training, tracking, and monitoring goods movement.
An ERP solution's warehouse management module optimizes operational processes. It provides real-time visibility to inventory levels, storage, staff productivity, and demand forecasting. It streamlines and automates processes to reduce time and effort. You can also get a snapshot of the facility's activities without conducting warehouse audits.
A warehouse management module offers many benefits:
- Reducing picking errors
- Optimizing stock control
- Maximizing space usage
- Ensure employee productivity and compliance with safety and health regulations
B2B E-Commerce
B2B eCommerce solutions allow wholesalers and retailers to connect and sell large quantities. To promote business growth, you can reach new customers with digital marketing strategies through a robust B2B eCommerce platform. It allows for better customer and supplier management.
By leveraging data, you can create personalized shopping experiences for customers. Sales can be boosted by offering to cross-sell or up-sell recommendations.
Payment Gateway
A payment gateway lets merchants accept electronic checks and credit card payments from their websites. The website collects payment information and sends it to a financial institution to process and deposit funds to the merchant account.
Some payment gateways offer a virtual terminal that allows merchants to enter transaction data. Some payment gateways offer an automatic recurring billing option that allows merchants to submit recurring payment information, which can be repeated according to a set schedule. This option allows merchants to submit transactions every month, quarterly, semi-annually, or annually.
Analytics and Reporting
It is possible to forecast demand accurately using data analytics. Data analytics gives you valuable insights into customer behavior, product performance, and channel performance to increase sales. It improves operational efficiency, which can help to increase supply chain performance, reduce stockouts, and speed up order fulfillment. Real-time data can increase sales, profit maximization, and customer satisfaction.
Real-time data analysis helps businesses keep inventory levels at the right level. It also allows them to predict seasonal trends and spikes or depressions in customer demands. Advanced reports with key performance indicators and metrics greatly increase profitability and give you a competitive edge.
What are the Major Functions of an ERP Inventory Management System?
Consider the long-term potential of any new system: A system that touches so many areas of your business and takes time and effort must be able to meet your current and future needs. You should avoid systems that are limited in functionality and will be obsolete within three to five years.
Here are five steps to help you find the right system for your business.
Step 1: Identify Your Desired Outcomes
Make sure you consider the goals of your stakeholders and develop a business case. Strategic planning involves analyzing business trends, core competencies, and external opportunities.
Ask Yourself these Questions: How does the purchase of the proposed item align with long-term goals, both previously established and newly revised? What insights will it provide that are unavailable today to help us plan our inventory strategy?
Step 2: Examine the Project
Which data sources are required to integrate key metrics into ERP inventory management software? What suppliers and partners will have access to the ERP inventory management solution? Make a list of all the required capabilities and features to achieve the desired result.
Step 3: Create an ROI Analysis
Don't just focus on cost-cutting. Instead, consider how the investment will increase your company's profitability, efficiency, and customer satisfaction. Explain how technology will allow your business to grow by better managing its inventory.
Step 4: Draft a Vendor List
Review case studies from similar businesses to help you determine which systems are best suited for your business. To narrow down your options, ask the following questions:
- Are the systems flexible, scalable, and easy to integrate?
- Are there any testimonials from other companies in the industry?
- What type of training is required? Is the company able to support training?
- Is there a free or paid trial version that can be used for testing purposes?
- How much does the software cost upfront? Or monthly for cloud-based applications? How about maintenance?
- How long will it take before we are up and running again?
Step 5: Keep an Eye on the Future
Examine the product goals of potential system vendors and determine if they align with your business. When deciding whether an ERP inventory management system will work for you, use the checklist below.
ERP Inventory Management: How to Get Up and Run?
An implementation roadmap is necessary to properly implement an ERP inventory management software system and reap its full benefits. The roadmap consists of three steps:
Create the Record: Incorporate all data and functions into one ERP system or link data from legacy systems to your ERP for real-time integration and updates.
Elevate the Record: Layer for other functions such as payroll, procurement, and advanced analytics. All these tasks can be done in one record system for optimal performance.
Expand with Advanced ERP Functions: ERPs offer advanced functions such as planning, analysis, quality management, and analytics, allowing your company to innovate and adapt to changing market conditions. ERP systems can handle many functions and areas and, thus, many aspects of a business. The roadmap can help your business get from where it is now to where you want it.
An ERP System is Used to Control Inventory
An ERP system optimized for inventory management automates the necessary functions to ensure stock buying, organizing, and transferring all work in sync. It also integrates the inventory requirements of customers, suppliers, and staff to maintain optimal stock levels. Below is an illustration of how an ERP might interface with these groups, their respective systems, and your central database. The ERP is a central "brain" that manages inventory operations.
Each group of the diagram has different tasks and requires different systems. Suppliers use inventory, financial and prediction applications. All of these systems must be working together. Each specialized software system must be able to communicate with the ERP system.
Let's say a company uses PLM to manage its inventory from conception to production. This will give you a better understanding of how ERP integrates with other systems. PLM and ERP are complementary. ERP is responsible for production resource planning. They would work consecutively. Initial product data is retrieved from the PLM. Once a product has reached a point in its development where it requires resources, the ERP integrates production with the rest.
It would help if you had a network of people, systems, and manual processes to manage inventory properly. When growing your business, inventory control requires more than "one system and done." A centralized approach to inventory control is essential. Start early to implement an inventory control system. It would help if you also assembled a team of internal experts to assist you.
- Keep current inventory records
- Be realistic about your budget
- Establish milestone goals
- Facilitate user acceptance testing, training, and other implementation checks
Companies with disparate, disconnected systems are missing out on vital inventory insights that could allow them to run their business more efficiently. A robust ERP system with strong inventory management capabilities can make inventory management a competitive advantage. Look out for integrated business intelligence that combines visual analytics with data to aid managers in making better decisions. You can customize your design to grow with your company, adding resources and features as needed.
Inventory Management Techniques
Just in Time (JIT)
JIT inventory management keeps track of the inventory required to perform daily operations. Its primary function is to minimize storage costs and reduce waste. Only new stock can be purchased by an organization when older stock is nearing replenishment.
The JIT technique will fail if there is a sudden increase in demand for a product. It doesn't have the resources to meet demand fluctuations. The JIT technique can be cost-saving but will result in losing customers to your competition. Companies that use this strategy require robust forecasting tools to make accurate predictions.
Minimum Order Quantity (MOQ)
The minimum order quantity is the minimum number of units you can buy at any time. A manufacturer might have a MOQ of 500 units, meaning they can only buy 500 units at any given time. Suppliers also benefit from a steady cash flow.
ABC Analysis
ABC analysis divides inventory items into three categories: A, B, and C. Items in the A category have strict control and are very expensive. Category B is more affordable and less tightly controlled. Category C is the most popular category and requires a relatively low investment. It also has the highest availability. This category requires minimal control.
FIFO and LIFO
Businesses use the first items to enter the warehouse in FIFO (First In, First Out). The food industry follows FIFO inventory management procedures. This means that you consume perishables first.
For non-perishable goods, the LIFO (Last In, First Out) method is used. LIFO is a method that considers the fact that prices continue to rise, so inventory purchased recently is often sold first to maximize profits.
Economic Order Quantity (EOQ)
Businesses can reduce inventory waste with EOQ by ordering as little inventory as possible. It helps businesses save storage space and money while also helping them achieve their target goals during peak demand.
Dropshipping
Dropshipping is a method of selling goods that merchants don't have or stock. The merchant sends the order to the supplier once he has received it. The supplier will then ship goods to the customer for a merchant. Dropshipping is a low-cost option for businesses that don't need inventory management.
Conclusion
An ERP inventory management system with its extensive features can help you reduce costs, streamline inventory management, and give you an edge over your competition. ERP inventory management is ideal for rapidly expanding eCommerce businesses with multiple online stores and channels. ERP inventory management systems allow companies to manage logistics, operations, finances, and inventory from one system. This reduces errors and increases efficiency.
These six factors are important for large business owners to consider when considering an ERP system for inventory control. For a business to survive, inventory management is vital. The customer and the company benefit from the effective presentation of stock product information. The software can also help businesses run more efficiently, as proven.