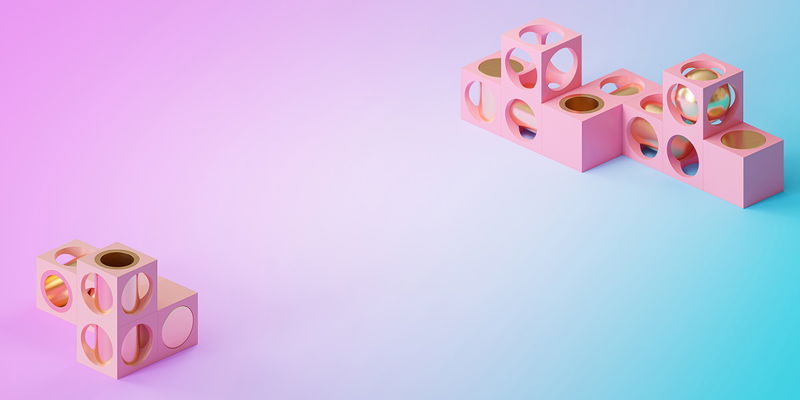
So, here you will get to know what is maintenance software helps your team manage maintenance activities more effectively by scheduling, overseeing, monitoring, and assessing every task completed on an ongoing basis. Maintenance software enhances efficiency by centrally organizing, planning, tracking, and evaluating each activity continuously, increasing organizational visibility and improving connectivity between tasks completed regularly.
Maintenance software comes in various forms, from basic to sophisticated solutions like Enterprise Asset Management or Computerized Maintenance Management System software (EAM/CMMS software) that records and oversees every facet of maintenance operations, from inventory control to reporting. In contrast, more basic systems exist to handle work orders or requests.
What Is Maintenance Software Used For?
Cutting Down On Idle Time
- Make sure the equipment is available.
- Increase output.
- Reduce waste and redo work as necessary
- to prolong the asset's lifespan.
Preserving A Law-Abiding And Secure Work Environment
- Create SOPs to address safety and health.
- Gender Monitor incidents
- while tracking compliance with license requirements and audit records.
Keeping Expenses Under Control
- Reduce Labor Costs
- Order fewer replacement parts.
- Monitor and Control Warranty Costs.
Handling Both Personnel And Procedures
- Arrange resources, paperwork, and work orders.
- Plan labor and maintenance.
- Reduce administrative duties significantly while building stronger relationships with vendors.
Arranging Data
- Personalize and schedule reports
- Track KPIs and measurements
- Draft extensive asset histories.
Arranging For Routine Maintenance
- Establish triggers.
- Employ sensors for condition monitoring.
- Develop standard preventive actions.
Types Of Maintenance Software
Computerized Maintenance Management System (Cmms)
Here is what a CMMS maintenance software. A CMMS oversees all maintenance for assets during their use. Responsibilities may include inventory control, scheduling automation, and record keeping.
Enterprise Asset Management (Eam)
By employing Enterprise Asset Management software, an asset can be tracked throughout its full lifecycle - from design through construction, operation, and replacement - from conception to completion.
Asset Performance Management (Apm)
An Asset Performance Monitoring solution (APM) helps increase asset reliability by gathering and analyzing real-time data to measure risks and value. It collects and processes this data in real-time to provide immediate analysis of asset condition, reliability, and availability. Advantages of maintenance management software
Work Order Management
Switch from spreadsheets, whiteboards, and paper to maintenance management software to efficiently create, view, track, prioritize, and complete work orders more easily from anywhere at any time. Create task lists, attach files or documents, and access previous work orders related to any asset or request with this powerful solution, ensuring increased operational efficiency while eliminating unscheduled downtime for good!
Enterprise Resource Planning (Erp)
So, what are ERP systems, accounting and manufacturing operations can both benefit from ERP systems as daily business functions that need to be overseen, with data exchange between processes - from maintenance to accounting - made easier using ERP solutions.
Detailed Asset Histories
Asset performance over its entire history can be easily understood using maintenance software tools that record past issues, inspections, and fixes for specific assets. Notes, photos, and root cause analysis help facilities track past problems as they develop as reviews take place or repairs take place to particular assets; using such solutions allows maintenance teams to reduce downtime quickly while quickly and effectively repairing recurring problems by seeing how previous breakdowns were solved in the past.
Inventory Management
Lacking key parts, even just minutes of downtime can become days or weeks of production delays, yet with proper inventory control, it can happen differently. Maintenance management software controls inventory levels by tracking parts, linking you with suppliers and vendors, and optimizing levels. Plus, alert necessary staff when a stock drops below the minimum quantities threshold.
Maintenance Reporting
Data-driven decisions are always the best ones. By employing maintenance software, you can collect labor costs and asset performance metrics and then organize this information into easily understandable findings. Furthermore, maintenance reporting has never been simpler, with customized templates and automated reports making reporting hassle-free, allowing you to recognize patterns, pinpoint inefficiencies, and address problems before they escalate while identifying areas where expenses and downtime reduction could occur.
Maintenance Scheduling
No one ever seems to have enough time in a day to complete everything on their list, which makes maintenance scheduling software even more useful in helping organizations optimize their usage of available time and reduce expenses while increasing asset health and saving precious minutes of each workday. Calendars, workflows, usage-based triggers, automated reports, mobile apps, and notifications can provide your facility with all of these necessary tools in a streamlined package to save both expenses and time!
Preventive Maintenance
These days of running around to put out fires have passed us by; thanks to maintenance software, maintenance chaos has now been controlled, and preventive maintenance has been made more streamlined than ever. Through preventive maintenance software, you can plan care ahead, notify technicians when a task is due, and give them greater access to resources so their scheduled tasks can be completed more rapidly and efficiently - creating a streamlined procedure that aids the success of preventive maintenance programs.
Related article - Mastering Maintenance Management: An Advanced Guide to ERP Software
Top CMMS Software Trends: Future Of Industrial Maintenance Automation
Utilizing Cloud Computing
Evidence shows that due to the ease of accessibility of cloud-based solutions, more businesses are turning towards them. You can access them 24/7 on various platforms with data security guaranteed and installation being an effortless experience. With cloud-based maintenance management software systems, you have real-time access to maintenance data, so making decisions faster becomes possible.
Technicians receive emails, SMSs, and push alerts from CMMS software; maintenance teams may produce better work as managers, technicians, and customers share more information effectively. Based on what's contained within work orders, technicians can prioritize work more effectively for efficiency in communication.
Application Programming Interfaces or APIs enable seamless data exchange between internet-enabled devices and cloud-based CMMSs, allowing your assets to generate automated maintenance requests automatically regardless of location; completion of objective asset condition assessments helps make preventive maintenance even more cost-effective.
Predictive Over Preventive Maintenance
Since its debut, CMMS has evolved significantly, shifting from reactive maintenance solutions to proactive alternatives. Businesses using preventative maintenance management strategies such as this one can save up to 18% in budget by quickly responding to problems as soon as they occur; predictive maintenance may eventually replace this strategy with even more robust solutions.
59% of respondents in one recent study identified predictive maintenance as one of the critical features of CMMS systems, providing facility managers, company owners, and maintenance management experts real-time updates when using it. As its predictive nature allows it to measure reliability as opposed to more traditional tools, CMMS use allows your staff to identify which assets require more focus in repairs and maintenance, saving both time and effort when prioritizing asset maintenance for large organizations with many aids to manage simultaneously. This feature of predictive maintenance systems makes monitoring these vital assets far simpler!
Internet 4.0, IoT, And Artificial Intelligence
Industrial maintenance automation stands to benefit significantly from emerging technologies like Internet 4.0, artificial intelligence, and the Internet of Things, or IoT. A CMMS should be capable of communicating with equipment that possesses unnatural intelligence characteristics, thereby maintaining control.
Computers connected via the Internet 4.0 can communicate with each other without human assistance; smart devices don't rely on technicians; they monitor themselves. Maintenance managers gain access to real-time data that gives them insight into potential issues that need immediate resolution, thus helping prevent unexpected pitfalls from emerging.
Businesses are turning to IoT data in their asset maintenance strategies. Real-time asset decisions are being made via predictive maintenance, making maintenance no longer a cost center but instead an asset profit center. By harnessing the Internet of Things collected data for long-term planning purposes and intuitive maintenance techniques using collected information, faster audits may also become a reality. Which enables machines to act autonomously but still retain human char
Intelligent Data-Driven Maintenance
As previously discussed, more CMMS software providers are adopting machine learning and artificial intelligence into their maintenance management systems to offer more intelligent data-driven maintenance options that streamline audits, certifications, and root cause analyses for companies' future operations. With such advanced options, you can simplify audits, certifications, and root cause analyses for better company operations.
Adding Value
Substantial updates to CMMS versions can undoubtedly add value, yet current systems must maintain their worth through feature additions that keep pace with client trends and requirements. A provider must stay abreast of industry developments to provide solutions capable of meeting them; features must apply across industries while being ready to accommodate custom features for specific customers should also be considered.
As we advance, the CMMS must also be adaptable enough to support growth within small businesses or organizations - these requirements might differ significantly from large utility providers or grain elevators.
Mobile Use
Work orders can be easily created, assigned, and tracked using desktop-based CMMS systems; however, computer access remains necessary to view them. But why limit yourself? Why not utilize mobile phones that almost everyone carries around with them, as accessing these mobile CMMS apps is now so prevalent? Technicians using such mobile-friendly apps enjoy many advantages; simplifying usage on portable devices should also be an immensely beneficial benefit.
Create A Culture Of Reliability
Industry 4.0 represents a massive transformation that touches every aspect of manufacturing operations, starting with people. Training and organizing your maintenance team effectively and making changes necessary due to new procedures or systems can make all the difference when embarking upon this transition. Your best strategy for success would be to start this continuous improvement culture immediately.
Your first priority should be setting forth guidelines to support optimal practices for maintenance. Next, create formal procedures for each operation - from purchasing to work orders - to protect data integrity and encourage positive habits. Communicating effectively as part of this effort is vitally important, while rewarding employees who welcome change to promote the remaining staff in implementing new protocols.
Other Languages
As more companies expand internationally, implementing a CMMS that speaks the local language can prove immensely helpful for all parties involved. While new and improved can often mean more complicated or involved systems, keep an eye out on what has worked successfully before you change everything completely; software must remain intuitive, well structured, and user friendly for newcomers; remain abreast of training requirements for existing customers while always offering training seminars regarding features additions, refresher seminars or innovative applications which clients appreciate greatly.
Organize Maintenance Information With QR Codes
Maintenance teams will easily access information when each asset has a QR code assigned for easier work order identification or prioritization. Scan the QR codes quickly to determine work orders' type or priority status- saving time and effort while making maintenance information more accessible to access and organize.
Workplace Safety
Safety will remain at the core of industrial maintenance automation in 2023. Improving cooperation and communication among operations, maintenance, and safety divisions will be necessary, while data exchange may benefit from using whole-company solutions instead of discrete technologies. Using shared data sets, your teams may complete appropriate tasks at appropriate times to improve their effectiveness and compliance while creating a safer atmosphere overall.
Want More Information About Our Services? Talk to Our Consultants!
Conclusion
Companies stand to benefit immensely from employing sophisticated AI algorithms for software maintenance anomaly detection. These systems offer invaluable insights that assist in optimizing operations, from increasing security and user experience, to controlling cloud expenses, and measuring key performance indicators.
Recognizing the challenges inherent to applying machine learning to anomaly detection requires being conscious of all associated difficulties, including managing large dimensions and distributions and selecting suitable subspaces.
Companies can greatly boost the operational effectiveness of industrial equipment by employing anomaly detection techniques in practice. Read our in-depth blog on advanced AI algorithms for software maintenance anomaly detection to learn how these AI-driven solutions could enhance company operations while revolutionizing anomaly detection.