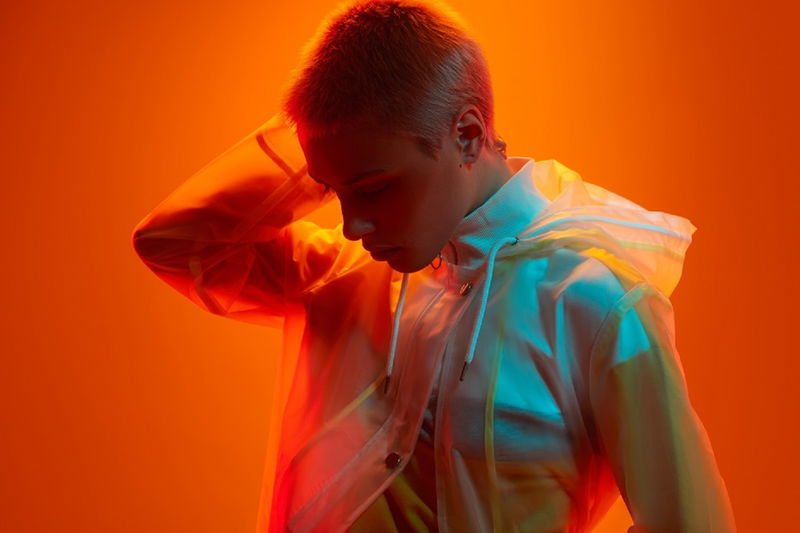
Advanced analytics encompasses predictive analytics, which projects activity, behavior, and trends using both historical and current data sets. Predictive models created from datasets utilize machine learning algorithms, data queries, and statistical analysis techniques to assign scores representing their probabilities for specific actions or events occurring.
Data analytics encompasses using quantitative methods and expertise to interpret data to provide answers on topics as diverse as companies, weather patterns, healthcare costs, and scientific research. Predictive analytics is integral to data analytics' scope - commonly known as "business analytics." Herein, in this discussion, the role of predictive analytics within businesses will be examined extensively.
What Is Predictive Maintenance?
Predictive maintenance (PdM) can improve process plant maintenance efficiency. Using artificial intelligence (AI), machine learning (ML), and Internet of Things sensors, PdM contributes significantly to Industry 4.0, big data, and the emergence of the Internet of Things.
Predictive maintenance software is one of the many subcategories of predictive analytics. Big data, the Internet of Things (IoT), Artificial Intelligence/ Machine Learning, and predictive maintenance tools techniques can all be combined together in this area to monitor machinery and detect component failure.
Due to predictive maintenance tracking the condition of parts using Internet of Things data, this technique may also be known as condition monitoring or "CM."
How Is Predictive Maintenance Related To Predictive Analytics?
Predictive analytics and predictive maintenance both involve applying machine learning techniques to real-time big data gathered via IoT sensors or other monitoring systems.
Predictive maintenance manager aims to protect equipment downtime against failure by monitoring every component and notifying you via condition monitoring if signs of potential malfunction emerge. Predictive maintenance technology helps avoid unexpected component failure from taking you by surprise and also helps ensure timely responses should one arise unexpectedly.
Predictive analytics encompass several statistical methodologies such as data mining, predictive modeling, and machine learning that utilize historical information and present-day conditions to predict unidentified occurrences that were once unknown or expected occurrences. Predictive analytics is widely applied in several fields and industries, including finance and e-commerce; its benefits extend further as analytical tools can identify minute irregularities with output quality, part availability, or any continuous metrics that require analysis; it can even predict fraudulent events or anticipate client demand forecasting within companies themselves.
Predictive maintenance should not be confused with accurate forecasts; instead, early abnormalities or early indications of failure can be detected with its help using predictive schedule maintenance.
Role Of Predictive Analytics And How Does It Work?
Every piece of equipment requires IoT sensors to begin its predictive maintenance journey, collecting real-time data that is then transmitted directly from these IoT devices onto a central condition monitoring system. Software automatically analyzes condition monitoring data that shows normal plant functioning to establish an "ideal" baseline of behavior for "normal" plant operation.
Predictive maintenance process systems utilize machine learning (ML) technology to quickly evaluate data streams coming in from IoT sensors, keeping a watchful eye for irregularities that indicate potential equipment failures, damage or need for repair while sending alerts as required.
Predictive maintenance requests solution monitors an entire plant by incorporating human domain knowledge, called human intelligence (HI), into machine learning systems. As a result, this PdM system is better at distinguishing anomalies that require immediate action from those within range of expected fluctuations, producing less focused alerts daily; eventually, engineers become used to simply dismissing alerts generated by such systems.
Which Industries Benefit From Predictive Maintenance?
Numerous industries can take benefits of predictive maintenance software like - banking, cybersecurity, energy & utilities, and health care - benefit significantly from predictive maintenance programs, with process manufacturing particularly benefiting greatly from them due to all their moving parts, critical equipment life, and constant production lines demands. Predictive maintenance technicians can provide considerable advantages in several process industries:
- Plants that produce chemicals for chemical industries,
- include gas and oil analysis facilities,
- refineries,
- cement manufacturing facilities,
- paper pulp factories,
- pharmaceutical sectors.
Related article - Streamline Your Maintenance Processes with Top-Rated Management Software: A Quick Overview
Why Does My Company Need Predictive Maintenance?
Predictive maintenance processes offer your manufacturing company many advantages over-reactive or preventive maintenance software. Your plant contains numerous pieces of equipment sensors, which all depend on working smoothly to keep production moving forward without interruption and avoid production downtime. By employing predictive maintenance strategies instead, these benefits will become clear.
Replacing parts can be costly and time-consuming for maintenance staff; any production halt may result from this replacement effort. By employing predictive maintenance for early warning of component failures, early condition-based intervention allows companies to address minor problems before they escalate further than necessary.
Your computerized maintenance management software solution schedule can be quickly altered in response to an early condition monitoring warning, allowing your team to investigate immediately and repair parts that might otherwise break soon before replacing costly ones more often. In doing so, predictive maintenance often allows them to help save costs over the longer term by fixing parts before they go bad again - helping save both you and your budget from expensive replacement expenses.
Assuming you get an early warning of malfunction, and investigate further to discover that something needs replacing soon enough, chances are there is still time before a part totally fails. Schedule its replacement when convenient both for the production schedule and maintenance operations team schedule; an early condition monitoring warning means the issue doesn't necessitate immediate attention, especially true if replacing something would require you to shut down part of your manufacturing facility - thus choosing an inconvenient time in advance to minimize downtime altogether.
One potential pitfall lies in your lack of replacement parts to respond quickly to sudden partial or complete part failure, or signs of impending failure, that arise unexpectedly and take you by surprise. Production might need to stop for hours until those components arrive from suppliers. Furthermore, your maintenance tasks crew could already be preoccupied with other pressing projects that require them to attend to unexpected malfunctions that threaten another part of the plant if left alone for too long.
What Are The Benefits Of Predictive Maintenance For Process Plants?
Predictive maintenance software primarily benefits process plants by decreasing maintenance expenses. Repair parts more cost-effectively to extend their lifetime and decrease downtime while replacing less frequently when optimal condition monitoring and predictive maintenance activities are used to predict failure of parts.
Predictive maintenance has been shown to decrease downtime by 5-15%, lower the cost of new piece of equipment condition by 3-5%, increase labor productivity by up to 20%, and bring inventory levels down by up to 30%, which leads to 5-20% decreases in carrying costs, according to Deloitte research.
Predictive maintenance can play an instrumental role in maintaining process plants' positive public image by helping avoid unscheduled component failures that damage public perception of process plants. Pollution incidents, explosions, leaks, and pollution incidents all tarnish reputations. At the same time, plant owners generally strive to protect the environment - early notice of impending part failure allows you to replace components before their failure endangers human safety or the ecosystem.
Predictive maintenance programs offer more significant savings and efficiency than preventive maintenance schedules ones, as they ensure components are tested at their most likely times of need rather than forcing your staff into following an arbitrary schedule that allows the same amount of time for every task each component may need to undergo inspection or testing, predictive maintenance also saves you time. It ensures all inspections occur as necessary rather than forcing everyone onto an identical timetable - something preventive maintenance programs don't.
Predictive maintenance allows you to increase employee satisfaction among operations and process engineers while decreasing annoyance levels among your workforce. Gaining control over your plant becomes much simpler thanks to predictive maintenance; with it, costly downtime decreases, organizational stability improves, and emergency responses become faster than before.
Predictive maintenance can help increase your bottom line by decreasing maintenance expenses, unexpected downtime costs, and unscheduled shutdowns that must take place because an unexpected part has broken.
Disadvantages Of Predictive Maintenance
Predictive techniques facilitate just-in-time maintenance costs to reduce unplanned downtime and extend equipment lifespan, with some potential downsides that should be kept in mind:
Initial Costs Can Be Considered Substantial: Predictive maintenance costs require purchasing sensors, data analytics software, and sometimes Internet of Things infrastructure - this upfront investment may be significant for most businesses.
Complexity: Implementation of predictive maintenance requires training staff on new methods of predictive maintenance, integrating various technologies and systems, and processing large volumes of data - creating additional obstacles some organizations are unequipped to overcome.
Predictive Maintenance Has Many Applications; Here Are Just Three Instances
Predictive Maintenance For Pumps
Pump motors must operate efficiently for your plant to remain effective, so using predictive maintenance to detect minute variations in vibrations from pump motors that might indicate imbalance from deposits on the impeller or other components may prevent deposits from accumulating to such an extent that they threaten machine downtimes and the pump's concrete structure. By monitoring vibrations closely and responding immediately, predictive maintenance identifies any minute variations that might indicate imbalance due to deposits on the impeller or components. It allows timely cleaning without endangering machine failures and structures with dangerous deposits accumulating over time.
Predictive Maintenance For Heat Exchangers
Partial blockages in heat exchangers can be identified via various measurements, including measuring temperatures in and around it and other parts. With predictive maintenance services available today, however, partial blockages in heat exchangers can be cleaned and their partial blockage removed as soon as they appear, cutting energy expenses and associated problems like erosion from occurring while it's blocked; sooner resolution would reduce energy consumption expenses while mitigating risk that could otherwise lead to plant shutdown and lost output if left unaddressed in time.
Predictive Maintenance For Furnace
Blockages in furnaces pose an operational and product damage risk that should not go undetected. Blockages can be identified and addressed quickly by replacing malfunctioning sensors and pinpointing temperature reading issues as the source. By doing this, products are protected from being wasted due to being cooked at incorrect temperatures and wasted time cleaning an oven that should have been spent producing; preventive maintenance tasks saved a more severe breakdown by quickly responding to minor problems early.
Predictive Maintenance Changes The Paradigm
Adopting predictive maintenance solutions in process plants is often hindered by process engineers' expectations that they perform reactive work; managers expect them to put out any potential fires they perceive in their machines or facilities.
Engineers who wish to utilize predictive maintenance must adopt the detective mindset, searching for signs that suggest potential issues and taking preventative actions against significant equipment failure or shutdowns. When early indicators show valve position at 90% and reformer tube temperature dropping significantly, predictive maintenance becomes possible, providing engineers with opportunities for early action against major equipment costly breakdowns or shutdowns.
Process manufacturing companies can save costs, increase productivity, and optimize plant efficiency by adopting a predictive upcoming maintenance (PdM) plan and solution explicitly tailored for equipment management and operations management.
Want More Information About Our Services? Talk to Our Consultants!
Conclusion
Predictive maintenance software companies allows critical asset performance or Asset availability, asset lifecycle, asset failure, asset health, asset longevity, asset reliability, and enterprise asset management and reactive maintenance team to be scheduled optimally to reduce frequency and maximize reliability without incurring additional costs. It uses machine learning, AI, sensor data, and equipment monitoring/vibration analysis as critical elements of its implementation. Even though predictive maintenance companies involve higher start-up costs and require specialist knowledge before being implemented effectively, it saves both money and resources if implemented by monitoring specialists/equipment manufacturers first.