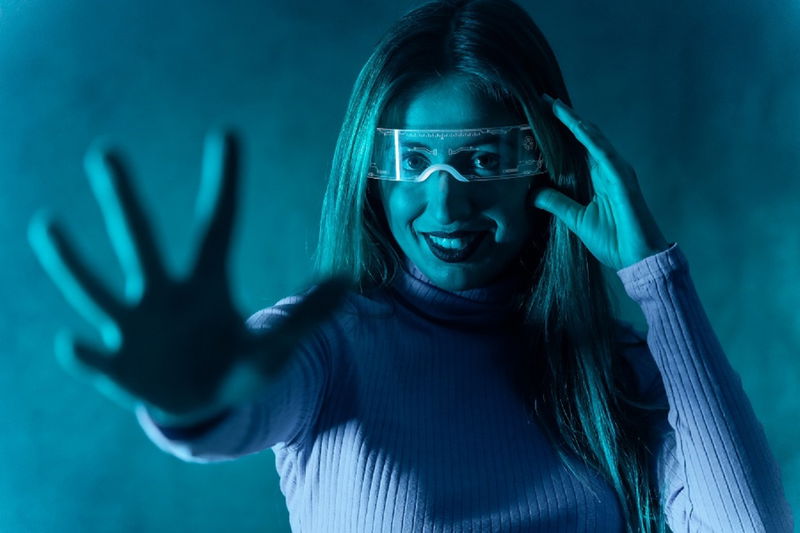
Organizations that use proactive types of maintenance planning can reduce unplanned downtime by 25%, enhance equipment longevity by 20%, and save 10% on maintenance team expenditures.
Proactive form of maintenance, a systematic approach to facility management, seeks to foresee and address problems before they arise. It seeks to stay one step ahead by continually monitoring equipment and taking preventive action.
This is in contrast to reactive maintenance history, which deals with issues as they emerge, and preventive maintenance schedules, which entails regular usage-based maintenance activities chores. By adopting a proactive maintenance strategies, facility managers can-
- Increase asset availability
- Identify potential equipment failures early on
- Prevent unplanned downtime
- Reduce breakdown maintenance costs
Maintenance Strategies For Proactive Facility Management
Implement Automated Analytics To Predict Downtime
With automated analytics, you can find possible predictive maintenance efforts problems and fix them before they become expensive fixes. You can accomplish this by gathering information from embedded sensors placed all over your property and utilizing it to build predictive models. Then, these models can be utilized to spot trends and patterns that might point to the need for upscaling.
For instance, you may monitor the humidity and temperature in your HVAC system with automated analytics. If the data reveals that these values deviate from the expected range, it may be a sign that something is wrong with the system. Being aware of any problems in advance enables you to take corrective action before the issue results in a severe breakdown.
Inspect And Repair Critical Assets First
Proactive maintenance With FSM software on equipment must be started with your most important assets first. These are the resources that most influence the general effectiveness and production of your establishment. For instance, plumbing problems ought to take precedence over elevator malfunctions as, while individuals can still use the stairs to go between floors, the absence of water has a substantial negative influence on day-to-day living.
Prioritizing these assets' condition-based maintenance requirements can help you avoid costly malfunctions and lower the associated repair expenses. When determining your vital assets, it's important to include stakeholders who have a thorough grasp of the facility and its operations. Furthermore, carrying out a critical analysis can assist in estimating the degree of influence an asset failure might have on your company.
Modernize Outdated Equipment and Boost Asset Performance
An additional tactical method for managing a plant is to concentrate on modernizing outdated machinery. No asset or piece of equipment will break down overnight. However, if you put in the extra work to give outdated assets more attention, you can extend their life and improve their performance.
For instance, unless there are leaks, roofing is frequently neglected during maintenance due to its approximate 25-year lifespan. The same holds true for electrical systems. But, if a problem occurs, it isn't easy to resolve. Thus, preventive maintenance of outdated equipment is important.
Use Augmented Reality To Bridge The Skill Gap
The goal of proactive facility management is to prevent equipment malfunctions before they happen. To do this correctly, you need skilled professionals. Employees who have inadequate training won't be able to fix equipment correctly. Offering training is not enough; you also need to ensure that the personnel receiving it will be better equipped to handle any problems that may arise.
This is the role of Augmented Reality (AR). It's a tool that can help you properly train your maintenance personnel. We can build augmented reality simulators so that staff members can practice mending various types of machinery. This real-time experience helps you identify areas where your workers may benefit from additional training. If they lack skills in certain areas, you can give them extra training and support.
Use AI To Reduce Labor Costs
The issue facing managers responsible for proactive facility management is that they must make financial commitments in advance, even in the event of an emergency. Getting superiors' approval for this can be challenging. Nevertheless, what if there was a method to cut upfront costs on preventative maintenance? Artificial Intelligence (AI) can help with this.
AI can perform numerous maintenance jobs automatically, allowing your maintenance crew to concentrate on more challenging and significant task assignments. AI, for instance, can monitor maintenance requests, assist in scheduling preventive maintenance, and generate progress reports. All of these things can improve and streamline your maintenance process.
Read more: Max Gain, Min Cost: Field Service Predictive Analytics? Save 50k
Implement Service Management And Organize Routine Tasks
Service management is the next proactive facility maintenance tactic. Establishing a service management system facilitates the organization of maintenance jobs, guaranteeing their effective planning, scheduling, and execution. If you implement service management, you'll be prepared for maintenance requirements at all times. Make a long-term plan and assign service-level agreements to each work related to the facility.
Consider, for example, a large office building. With service management, you may schedule maintenance for items like elevators, lights, and air conditioning. Depending on how critical these concerns are, you reach a consensus on how quickly they should be resolved. That way, you'll know exactly when and how to remedy anything that breaks. This type of structure inspires you, makes it easier for you to see the big picture, and motivates you to keep making things even better over time.
Streamline Work Orders With FSM Software
One essential tool for managing facility maintenance is the work order. Work orders guarantee the efficient operation of maintenance by assuring that tasks are completed and promoting communication between internal and external teams. Field service management software should be used to optimize such crucial procedures.
With the use of field service management software, you can automate work orders, get real-time visibility into them, increase accuracy, improve communication, and produce comprehensive reports and analytics.
Costs Of Proactive Maintenance
According to research, organizations with annual revenues exceeding $1 billion incur an average annual proactive maintenance cost of around $1.5 million for proactive facility management. As these costs vary depending on size and complexity, specific figures cannot be quoted; rather, we can outline factors which influence costs; these include-
- Labour costs associated with maintenance staff
- Material costs (parts, supplies and tools)
- Travel and Transportation
- Equipment downtime
Proactive Maintenance Benefits
Here we will see how proactive maintenance helps a business save money over time by decreasing downtime, improving equipment availability and dependability, as well as prolonging equipment lifespan through reduced wear-and-tear.
Preventive maintenance benefits in terms of reduced incidences related to safety events. Proactive care would increase operating equipment safety, particularly that with potential catastrophic failure. Oil and gas firms demonstrate their stringent preventive maintenance checklist procedures to guarantee hazardous substances stay contained.
How Can Proactive Maintenance Save Costs?
Proactive facilities management already significantly reduces costs by preventing issues from arising rather than responding after they have occurred. While facilities managers may find this challenging due to recording all costs accurately without errors, investing a bit upfront pays dividends later.
How to reduce costs without compromising preventive maintenance plans is currently the ultimate challenge, and facility management software offers a solution by expediting operations quickly while saving both money and time on hiring additional staff members.
Conclusion
Field service management solutions encompass an array of tactics designed to minimize unscheduled downtime and equipment malfunctions, and improve plant performance and safety with cost savings realized from allocating resources optimally. Over time, proactive unplanned maintenance approaches could reap considerable advantages for any organization, including improved efficiency, reduced expenses and decreased preventive maintenance procedure.