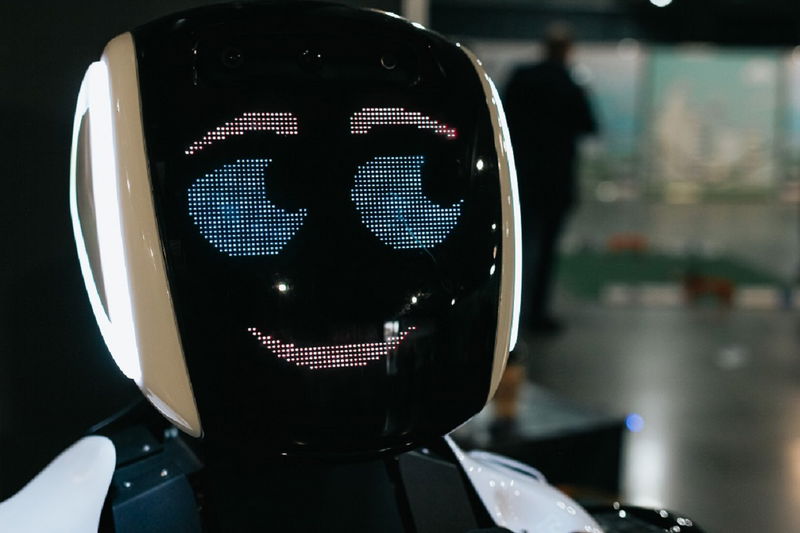
Predictive analytics is an indispensable tool in the modern digital era for forecasting future results, helping companies leverage massive amounts of data. Field service management stores data about technicians, assets, devices, clients and logistics; otherwise, it would simply become waste. If it is not used to streamline company operations, then its purpose becomes futile.
Pen and paper methods might work temporarily for startups, but in the long run, they won't suffice. Successful small businesses eventually outgrow analogue data systems; to gain access to analyses that automate and expedite interpretation faster on behalf of field service managers, teams should invest in an advanced field service management system with predictive analytics abilities.
Here, we'll explore how predictive analytics helps FSM prove its efficacy.
What Answers Can Predictive Analytics Provide To Field Service Managers?
Predictive analytics uses statistical algorithms and machine learning techniques to detect patterns and trends in data. By applying this analysis to future forecasting, predictive analytics in FSM can address queries such as these:
- Which assets and when are most likely to fail?
- What is the optimal time and place to conduct preventive maintenance?
- Are there specific technicians for a given task?
- Can resource allocation and scheduling be optimized so as to meet service-level agreements?
- How can we organize our servicing schedule so as to provide clients with minimal downtime?
- What components and equipment are necessary for a specific repair job?
- Is the likelihood that clients may encounter issues with their gear likely?
- Can we prevent frequent issues before they arise to reduce service calls?
- What steps can be taken to increase our operations' security and compliance?
Forecasting any change requiring action, from spare component stockpiles, field service assignments, field technician timetables, and customer satisfaction levels to shifts in customer loyalty levels, can be done. But in order to do this effectively, you will require access to relevant data and appropriate analytical tools.
Predictive Analytics Advantages
Here are the primary advantages of predictive analytics in field service operations:
Increase Safety
Predictive analytics helps reduce risks, lower infractions and accidents, and create a safe workplace. Predictive field service management solution utilizes historical data on safety incidents or compliance violations to identify regions that might pose potential compliance challenges. This enables organizations to take proactive steps, such as increasing employee training, by targeting these problem spots before they occur.
Optimize Resources
Enterprise organizations can optimize workday capacity planning and resource allocation with predictive analytics. Predictive service estimates can reduce workday capacity planning costs and boost service estimation accuracy. Field service companies can reduce operating expenses while increasing customer satisfaction by using past data analysis for customer retention purposes.
Predictive analytics helps predict inventory and service needs in specific regions based on previous service requests. It also improves scheduling, routing, and rerouting practices for field service workers, helping ensure technicians arrive where their presence is most needed.
Reduce downtime
Predictive analytics data can be leveraged to proactively schedule maintenance or repairs, eliminating downtime by enabling staff to address potential problems as soon as they arise. By anticipating and solving issues early on, organizations can avoid the negative effects of unscheduled downtime and larger, more costly problems that might otherwise develop over time.
Predictive analytics have the power to reduce downtime, enhance equipment efficiency overall, and reduce the frequency/length of equipment downtime, all of which have significant positive ramifications on FSM businesses' productivity and profitability.
Enhance Customer Satisfaction
FSM success hinges heavily on customer satisfaction; an unhappy experience can quickly translate to negative online reviews and result in the loss of both new and repeat business. However, data and predictive analytics offer ways to significantly increase satisfaction.
Using data such as customer service histories, equipment monitoring records, or any pertinent challenges that might be present, staff can become aware of the situation.
With this knowledge at their fingertips, technicians can come to their job sites knowing exactly what needs to be done, how best to fix an issue, and what parts might be necessary. This approach, as opposed to when field resources arrive with insufficient expertise, leads to faster resolution times and improves customer experiences.
Break Patterns
Effective Field Service Management organizations can use predictive analytics to identify common issues within field service activities quickly, then look back over previous data on service requests, technician performance and equipment failures to resolve them more quickly and efficiently than ever. Businesses could benefit greatly by applying this intelligence when planning field service activities and making data-driven decisions about field service strategies and activities.
Predictive analytics can assist field service teams in anticipating which kinds of service requests will most likely arise during certain times of the year or in particular areas.
Also Read: Maximize ERP Analytics For Performance Insights: Improve ROI By 50%
Understanding Predictive Field Service Process
Utilizing data analytics, machine learning and other technologies, this innovative approach to maintenance and customer care utilizes predictive models to predict when machinery or equipment will likely break and take proactive measures to fix potential issues before they arise. Field service organizations utilize this strategy in order to streamline operations; among the many advantages offered by predictive maintenance are:
- Reduced Downtime: Anticipating equipment failure allows organizations to plan maintenance or repairs during planned downtimes, thereby minimizing unexpected interruptions and productivity losses.
- Reduce Maintenance Costs: Predictive maintenance helps lower maintenance costs by allocating resources more effectively, thus eliminating needless component replacement and less frequent scheduled maintenance visits.
- Increased Equipment Lifespan: Prompt maintenance and repair can extend the lifespan of key pieces of equipment, providing greater value from investments made into it.
- Improved Safety: Predictive field service helps enhance workplace safety and reduce the likelihood of accidents by solving problems before they become urgent.
- Increased Customer Satisfaction: Reducing service interruptions through predictive strategies increases client loyalty and engagement for field service businesses.
Applying Predictive Analytics To Field Service Management
Start with these steps to integrate predictive analytics reasoning into your field service management procedure.
Convert To Big Data
Today's digital environment makes data collection virtually effortless. For example, technicians using their smartphones can collect and provide daily maintenance data via smartphone apps; equipment may issue alarms if it detects a breakdown and exchange performance data with one another; and all consumer contact points-call centers, web portals, and emails-can access this gathered information due to being part of the Internet of Things network.
Field service firms must embrace big data and implement tools to collect and consolidate it within their information system to gain a holistic, global picture of customer performance levels and activities with centralized data.
Track Key Data For Your Company
Big data presents its own set of challenges; its sheer volume can easily overwhelm its consumers. Establishing clear benchmarks and metrics at the outset is critical for developing a deeper understanding of your operations and performance assessment; more metrics may not always be better; instead, it's best to choose those most appropriate.
Predict Future Performance
Predictive analytics technologies, such as artificial intelligence and machine learning, make it possible to create statistical models from previous data for any installation or maintenance work carried out by field workers using predictive analytics technologies.
Studies conducted using statistical models can help you predict future trends and detect upcoming equipment breakdowns more quickly, for instance, by maintaining spare part inventories or keeping an inventory. You may even extract valuable insights quickly using predefined machine learning models.
Conclusion
Predictive analytics is an indispensable asset to organizations looking to streamline field service operations and other activities and expand their services. It also helps service providers outshone competitors by meeting and exceeding customer expectations for time, quantity, and quality results. Applying predictive analytics effectively is crucial to staying competitive and appealing to new clients while meeting or exceeding them in every way.