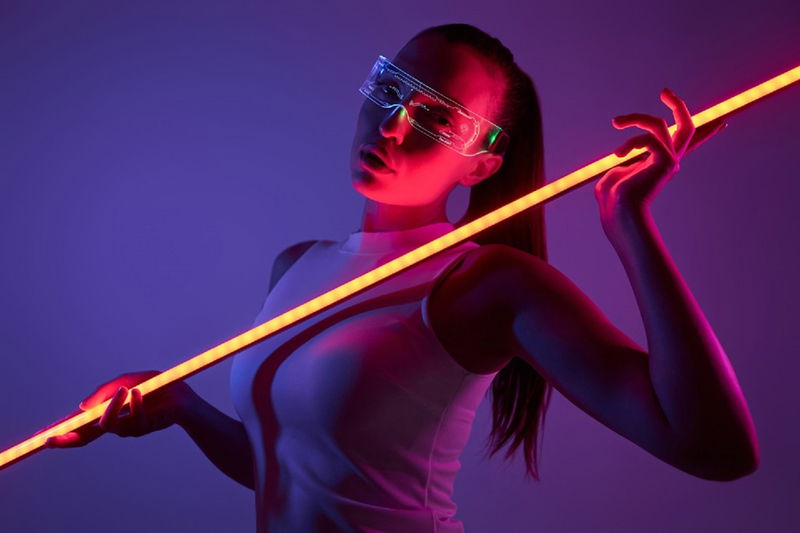
In order to effectively manage the supply chain, inventory management is necessary. In order to maximize efficiency across the supply chain, it entails monitoring stock levels and the movement of items, from raw materials being shipped out for manufacture to orders being filled.
Effective inventory management is essential to a company's lifespan as it lowers costs while enhancing cash flow and boosting profitability. Correct inventory organization will improve the efficiency of your supply chain. Without it, costly mistakes for all parties involved in your supply chain could result from misspeaks, overstocks, shortages, spoiling (when working with perishable commodities), and mis-shipments.
An inventory management system differs from enterprise resource planning (ERP) by focusing on one aspect of supply chain processes. They often include integration capabilities with various software programs like shipping, sales channel management and point of sale (POS), so you can tailor an integration stack specifically tailored to meet your company's requirements.
Inventory Management
Inventory management is crucial to successful business processes, yet many small companies must manage their products more efficiently. Some keep too few goods available and drive away clients; others overstock products to protect cash flow.
Critical Concepts In Inventory Management
Types Of Inventory
Raw materials are those that are used in manufacture. While finished goods are made but ready for retail sale, work-in-progress refers to products that are still being built.
Although they are employed in production, MRO (Maintenance, Repair and Operations) goods do not directly contribute to the finished product.
Metrics For Inventory
Lead Time is the time required to fulfill an order after receipt. Reorder Point (ROP) refers to an inventory level at which orders should be placed to avoid stockouts during lead times.
Economic Order Quantity, or EOQ, refers to an ideal order quantity which minimizes overall inventory costs (ordering and carrying expenses combined). Safe Stock refers to extra Stock being kept on hand to cover lead times or sudden changes in demand.
Valuation Methodologies For Inventory Valuation
First-In, First-Out (FIFO) assumes that older inventory items will be sold first, while Last-In, First-Out or LIFO provides for selling newly arrived inventory first. Weighted Average Costing determines an average price for every inventory item sold.
ABC Analysis
This method divides products into three groups according to their value and impact on a company:
- Items are costly goods that make a significant financial contribution.
- Items have moderate consequences and worth.
- Items represent less important items with lesser financial contributions.
Advantages Of Effective Inventory Control System
Advantages of Effective Inventory control system are as follows-
Inventory Management Strategies Can Help You Save Money
Staying abreast of which products are nearing expiration can help your company save on losses, as only using them after their due dates could incur more expenses than anticipated. Displaying prominently makes it easier for online buyers to purchase items, while optimizing inventory may become challenging if not monitored automatically.
Inventory Management Strategies Can Improve Cash Flow
An easy way to identify which products are selling quickly or slowly is to look at sales records and figures from previous months. From there, you can determine what items must be ordered and how much money should remain in reserves.
Techniques For Inventory Control Involve Devising Strategies For Overseeing Warehouse Operations
Maintaining an orderly warehouse order volume is another important objective as part of effective inventory management. Through effective inventory control systems, fast-selling products can now replace slower ones in terms of shelf space occupied.
Inventory Management Methods Help Increase Client Retention
Customers are delighted when ample goods are on hand and frequently return to make purchases, leading to lower churn rates and improved retention.
The Inventory Management Process
Before creating an inventory management plan, you must gain an in-depth knowledge of each stage of proper inventory management. This is key for reducing errors and selecting suitable software solutions for your company.
Products Will Be Brought Directly To You
At this stage, finished goods for customers, raw materials, and manufacturer subcomponents arrive in your warehouse.
Examine, Organize And Stock Items
Inventory control refers to inspecting, sorting, and placing inventory into their appropriate stock locations regardless of whether dropshipping, cross-docking, or another warehouse management system is employed.
Keep An Eye On Stock Levels
Reduce inaccuracy through cycle counts, perpetual inventory software or physical inventory counts.
Orders Are Placed For Stock
Customers place orders either in-store or via your website.
Orders For Stock Are Accepted
At this stage, your order will be handed off to your supplier; your POS system may automate it instead.
Take Products Out Of The Supply
By SKU number, items needed by suppliers or clients are located, removed from Stock and delivered directly.
Revamp The Levels Of Inventory
Utilizing a perpetual inventory system allows you to easily update inventory levels automatically and share them with stakeholders in a seamless fashion
Also read: Unlocking Success: The Top 10 Benefits of Inventory Management Software
Essential Methods For Inventory Control In Business
The essential methods for Inventory control in business are as follows-
-
Establishing Base Approximations Levels
Maintain a baseline for every product to track inventory demands. With its help, you can determine how many are in Stock with this level as a "warning indicator". When your list falls below this threshold, place orders with the wholesaler for additional inventory items immediately; be mindful that different base levels vary for other products.
Establishing a baseline requires knowing how quickly your products sell; this can only be accomplished if each item is tracked automatically. Remember that circumstances can change over time and adjust base levels as necessary throughout the year.
-
LIFO (last-in, first-out) and FIFO (first-in, first-out)
LIFO (last-in, first-out) and FIFO (first-in, first-out) are methods of organization that compare entries from last to first-out and vice versa.
One key concept in management and administration is "first-in, first-out." This principle spans all sectors of the economy including supply chains, technology and human resources. Inventory management techniques in supply chains dictates selling off older products first to protect your investment from expiring or perishable goods spoiling before being sold again; furthermore, old boxes cost money as liabilities rather than assets, with their quality diminishing over time.
LIFO (Lay-I-For-Others First) refers to selling your most up-to-date products first while keeping your older inventory until later. While this approach might seem less efficient than FIFO, using LIFO may reduce sales tax liability depending on how many goods are sold through this method.
-
Dropshipping
With drop shipping as your business model, you can operate without stockpiling goods in warehouses; instead, you sell directly from suppliers' warehouses using this strategy. One of the fastest-expanding strategies worldwide is dropshipping; anyone can create a website and marketing products through paid channels, as it requires minimal entry barriers to become one.
-
On-Time Delivery
One effective strategy is Just-in-time (JIT) inventory management. Under this model, orders only arrive when your stored goods are about to run out providing businesses with merchandise "as needed" while lowering inventory expenditures and costs. By switching over to JIT inventory management, they can avoid placing enormous orders for warehouse inventory, as well as manage any dead stock (items that consumers have never purchased or sold).
-
Make ABC Your Top Priority
ABC Prioritisation inventory management strategy may help streamline inventory prioritization efforts if your products fall under multiple categories. Specifically, this technique enables you to effectively focus on products requiring special care to use ABC analysis for inventory prioritization.
-
Regular Audit
Nothing beats an extensive physical inventory audit to know what items have sold well and whether any software auditing techniques could give additional insight. You have various methods available to you for conducting an extensive inventory review.
a) Physical Audit
Conducting an inventory physical inspection should be the initial practice. Physical auditing is a time-consuming endeavor that should only be undertaken once yearly; this practice allows companies to detect irregular inventory management practices and prevent sudden losses.
B) Counting In Cycles
Cycle counting enables you to manage the load efficiently without overtaxing yourself by periodically inspecting products with higher priority typically, selling items are counted more often when cycle counting.
-
Formula For Safety Stock Inventory
To manage safety stock inventories effectively, percentages should be your guideline. Keeping this in mind, assume for a moment that your list will run out by the end of the season. In this instance, you should order surplus inventory, as this will help avoid out-of-stock situations caused by inaccurate forecasting or shifting consumer demand.
-
Formula For Reorder Points
A reorder point formula measures stock percentage by multiplying total product sales during a particular season by its available inventory rate; this differs slightly from the safety stock inventory formula, as reorder point calculations take historical information into account while the safety stock formula considers changes in consumer demand.
-
Tracking Inventory In Batch
Inventory tracking allows corporations to monitor similar products in their inventory together in one package, providing an effective means of keeping tabs on things such as order volume, damaged components and expiration dates, an approach frequently employed across industries for monitoring inventory.
-
Lean Manufacturing Strategies And Implementations Strategies
Businesses using the lean manufacturing methodology must implement an inventory control system. Excess inventory can hide many issues that only become noticeable at its lowest inventory levels. Therefore, lean manufacturing methodology offers a solution that reduces financial losses and storage issues related to goods.
-
Estimating Demand
Demand forecasting inventory control techniques utilize past data to accurately predict future supply and demand requirements, primarily anticipating sales of goods and services to clients based on past and present client purchase values. E-commerce businesses may require assistance from business intelligence specialists to implement demand forecasting models.
-
Cross-Referencing
An inventory tracking strategy known as Just-In-Time (JIT) can be extended by cross-docking technology, which entails directly unloading goods from an incoming truck and uploading it now onto a departing one thus expanding the JIT concept further. Cross-docking technology works particularly well with online retailers since delivery requires few storage mechanisms between orders delivered to consumers.
Conclusion
Effective inventory management is an integral component of running a profitable company. Businesses can balance meeting consumer demand and cost optimization by understanding inventory management's basic principles, creating relevant plans, and taking advantage of technology. Building upon such foundations provides businesses with a solid basis for growth, financial success, customer happiness, and viability in dynamic industries like technology.