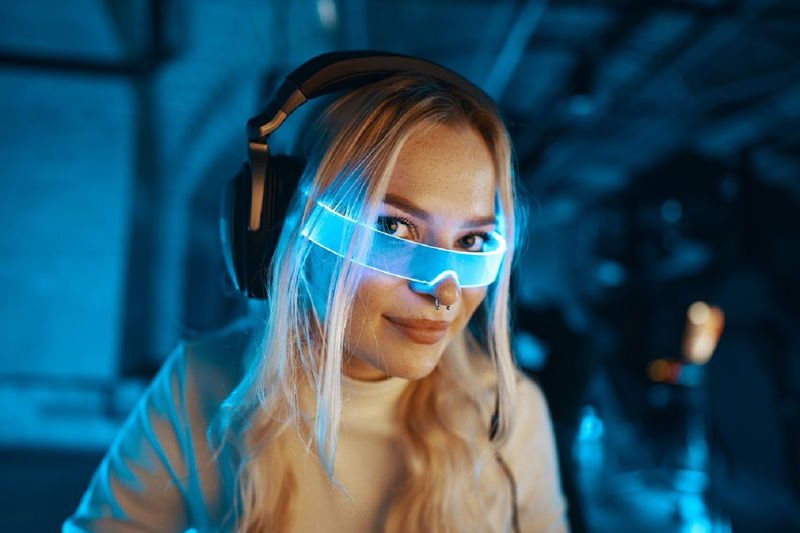
Manufacturers understandably emphasize productivity; however, achieving maximum output requires knowing each aspect of a business - from supply and demand networks, capabilities analysis, target markets, and delivery strategy development to operational visibility. An effective plan that keeps consumers satisfied while yielding profit can be executed successfully.
Manufacturers refer to this intricate act of coordination as types of capacity planning. Efficient capacity planning software is integral for timely customer order fulfillment, cost reduction, and profit maximization, yet as complexity arises due to staff shortages or supply chain problems, it becomes ever harder. Today's most successful manufacturers rely on cutting-edge capacity planning systems that offer drag-and-drop simplicity with speed for increased agility in meeting consumer expectations as they change.
Due to their ever-evolving natures, customer demand and manufacturing capacities require constant evaluation when selecting an effective workforce capacity planning tools and method. Simply depending on emails, spreadsheets, or Post-it Notes will only lead you further behind competitors who can respond more rapidly with agile production goals of capacity planning approaches that utilize networked approaches for real-time planning capacity management.
You can employ other solutions to address production capacity planning difficulties and boost operational effectiveness. Still, to carry out any plan effectively, you will also require a suitable accurate capacity planning solution in place.
What Is Capacity Planning In Manufacturing?
Capacity planning in manufacturing erp refers to the practice of allocating resources needed for product production in response to consumer demand, which also impacts production scheduling, excess inventory management control, and supply chain management.
Approach to capacity planning typically encompasses three primary components: personnel, products, and equipment. When developing this strategy, many considerations must be considered, such as the type of goods produced, use of equipment employed, employee availability, and total machine count to meet anticipated client demand. Once these parameters have been computed, it becomes essential that producers satisfy anticipated consumer demands through these calculations.
Manufacturers' financial performance can suffer immediately without an effective capacity planning strategy. You might opt to implement one by:
- Failing to produce enough goods can result in delays or short deliveries.
- Producing too many may force you to sit on goods that you are paying for.
- It may produce incorrect products which need reworking or must be wasted altogether.
Capacity Planning Strategies Explained
Manufacturers rely on various capacity planning techniques to meet demand efficiently. Before considering any approach, its benefits and drawbacks must first be assessed.
Driver-Based Capacity Planning Strategies
Driver-based capacity planning strategies in ERP depend on constant access to goods, labor, and machinery necessary customer satisfaction. Manufacturers must possess:
- Strong relationships with suppliers ensure that delivery times of customer orders don't suffer when new components and raw materials arrive for processing.
- Adaptable labor pools of workers with various skill sets are key in providing workers the flexibility to switch seamlessly among various production efficiency lines and alter production management levels as required.
- Access to machinery, inventory, and transportation resources is required for manufacturing and distributing consumer products they currently want or demand.
An approach centered on driver-based capacity planning offers many benefits for optimizing inventory levels and adapting quickly to changing market needs. On the downside, idle workers and equipment may incur costs related to making adjustments as required for production plans to keep moving along at its pace.
Time-Based Capacity Planning Strategies
It's possible to allocate design capacity expansion according to today's or tomorrow's expectations through time-based capacity planning techniques and then either meet actual demand forecasting directly or lag behind it.
1. Lag Strategy
Allocating sufficient human resources to satisfy actual demand instead of estimated estimates is known as "lag strategy," or allocating enough current resources in line with actual demands instead of estimated demand estimations. Taking such an approach ensures minimum costs while delaying providing clients with goods or services as quickly as they may need them - especially should an unexpected surge of orders emerge, or you take on large new clients that require expedited turnaround time turnaround - with this tactic, you risk failing to meet deadlines due to being caught off-guard.
2. Lead Strategy
While expanding capacity strategies ahead of future demand is riskier, expanding accurate capacity plans faster can meet those demands more rapidly than any lag strategy ever could. You could add resources or expand systems as part of the lead strategy, although resource addition is usually the preferred method to increase capacity planners. Your resource plan should reflect these decisions accordingly.
3. Match Strategy
Match strategy offers the optimal balance of lead and lag strategies. Under its care, strategic capacity planning occurs more frequently while closely tracking both actual and projected demand and market shifts and trends to gradually meet it with capacity management adjustments that adjust to meet actual demands. It scales more effectively than the lead strategy's high degree of flexibility while offering reduced risks.
Agile Capacity Planning Strategies
Using an adaptive capacity planning technique, agile capacity planning shifts future capacity in advance according to demand, market, and sales data. By adding capacity in anticipation right before it's needed based on real-time demand and sales estimates, it attempts to eliminate manual guesswork. Accuracy in forecast predictions determines if agile capacity planning succeeds or fails. For intricate situations, including past patterns, seasonal fluctuations, and sales team promotions, an advanced supply and demand planning solution such as KeteleQ can add further agility to an already adaptable approach.
An agile capacity planning strategy offers numerous benefits to manufacturers. These include matching investments to anticipated demand more closely, linking profitability directly to investments for better-informed decisions, and helping sales and marketing teams pursue profitable markets more easily. On the downside, additional data from more manufacturing industry areas must also be supplied with higher confidence ratings than they previously required for proper capacity planning decisions to be effective.
Read More:- Maximizing Profits: Top Strategies for Efficient Ecommerce Inventory Management
Benefits Of Capacity Planning
Forecasting future production cycle requirements allows businesses to ensure they have enough resources available to them to fulfill customer demands. Below are some key benefits of ERP capacity planning:
1. Reduce Stock-Outs
Stock-outs occur when your business cannot meet client demand on time, leading to customers being disgruntled or simply going elsewhere to satisfy their requirements. Thankfully, capacity planning provides another great tool for mitigating and eliminating stock-outs.
2. Increase Capacity Delivery
Assuring your staff access sufficient delivery capacity constraints is one way to gain an edge in the market and boost deliveries quickly and on demand. Various Agile certifications provide more insight into this matter.
3. Determines Process Inefficiencies
Consider how long it will take your team to finish a specific task. Knowing this information can be very useful when planning service industry projects that involve multiple tasks being managed at once by different resources; consider what kind of task they're handling, and an estimated time it might take them.
4. Facilitates Risk Management
Planning ahead can improve your ability to overcome challenges, regardless of magnitude. Even after doing all you can in preparation, unexpected problems still may crop up that require swift responses - like your supplier closing unexpectedly or three of your drivers contracting flu - you need high-level strategies you can refer back to quickly to make informed changes quickly and decisively.
5. Elimination Of Excess Capacity
Capacity planning helps organizations meet future resource demands efficiently. You can easily assess how long, energy, and effort each team member expended completing each task successfully - helping reduce overall resource expenses with intelligent resource decisions made at management time.
6. Confirm Availability
Capacity planning allows an organization to meet its future resource needs more successfully and successfully manage costs through resource optimization decisions that reduce overall expenses by making wise resource management choices. For example, you can accurately measure each team member's time, energy, and productivity when finishing tasks. By planning properly, you may also discover where savings opportunities lie for reducing overall resource expenses in an organization.
Want More Information About Our Services? Talk to Our Consultants!
Conclusion
Forecasting future business requirements and ensuring sufficient resources to meet them are both key components of ERP capacity planning. By creating plans with this objective in mind, your business can ensure that all of its current and future needs are fulfilled by having enough actual capacity plans.
Capacity management involves input from multiple business roles and using tools and procedures. It approaches from strategic planning through to considerations such as production planning and additional capacity, resource capacity requirements, and impending requirements. By employing proactive measures, you can develop an action plan for meeting demand now and into the future.