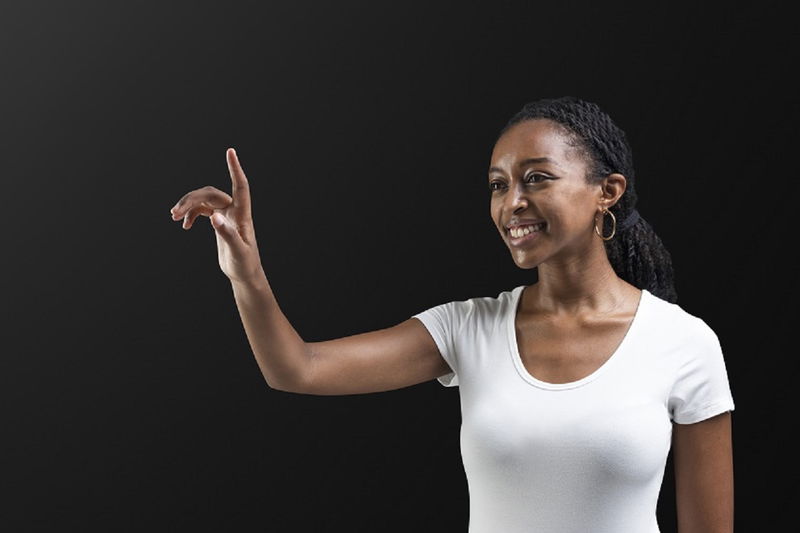
As part of their production process, batch manufacturers require lot tracking. Although most ERP software programs include some form of lot (and serial) monitoring as a feature, most do not provide enough detail required by chemical and pharmaceutical business operations.
What Are The Characteristics Of Lot Tracking Software?
Manufacturers benefit from using lot tracking ERP software offers solutions for many issues that arise:
- Ensuring compliance with standards and product safety
- Tracking raw materials, finished products, and related information during manufacturing process
- Detecting product flaws or contamination for recall concerns
- Supporting producers in precisely tracking stock levels.
- Simplifies product search to increase client support
Manufacturing Industries That Require Lot Tracking
Lot tracing is an essential component for businesses that operate under highly regulated environments, including textile manufacture, pharmaceuticals, medical devices, automobile parts & assemblies production, food & beverage production and cosmetic production to remain compliant with federal laws.
Food Safety Modernization Act (FSMA) mandates lot tracking by the US Food and Drug Administration (FDA), while in case of product contamination it requires food manufacturers to establish traceability systems to identify and recall items. Furthermore, as part of its Product Tracking Regulations for infant and children products the U.S. Consumer Product Safety Commission (CPSC) requires tracking all components used during the manufacturing process.
ERP Programmes With Traceability And Lot Monitoring
Locating products will become much simpler when employing a powerful lot tracking feature-rich ERP system, significantly improving customer service. In addition, inventory management becomes simpler so producers can maintain product availability without manually inputting data.
How Can Lot Tracking Work?
At the point of delivery by suppliers to manufacturers, lot and serial number tracking begin immediately. Although most components arrive with lot/serial numbers assigned already, sometimes receiving businesses must generate them themselves. Once received into the system a batch record will be created that contains detailed information for every lot or serial number such as:
- Source, which typically means PO number or Order No.
- Supplier Reference Number or Delivery Note Number from Supplier.
- Any applicable Use-By/Sell-By or Expiry dates (U/S/E dates).
- Inspection Findings.
- The Amount of Batch.
Enterprise resource planning can ensure that older batches are used first by creating a "pick list" when supplies are required for production in the production area. When supplies arrive, these items are then allocated directly to their intended job such as sub-assemblies (pizza bases) or finished products - producing batch records which closely reflect those created when these items enter stock.
Once a batch of pizza bases is complete, its lot number is assigned by the system to help keep track of which batches of base materials, wheat flour and other components were utilized as well as their source.
How To Track A LOT Inventory?
For effective inventory tracking, a checklist should be in place. A reliable inventory management system to track and store data should be the starting point, while accurate lot tracking may require technologies like ERP software implementation. Checkout below for advice:
- Establish an Identification and Tagging Infrastructure: This will make inventory tracking more efficient while guaranteeing accurate data.
- Employ Frequent Documentation Processes: These processes help accurately monitor inventory levels and stock balance.
- Automate Data Collection Utilizing Barcode Scanners or RFID Tags: Any firm can utilize such tools for accurate data collection while saving significant time.
- Undergoing Regular Checks and Audits: Conducting periodic audits helps detect inaccuracies and anomalies so errors can be addressed and make inventory tracking more precise.
- Accurate and Concise Data Recording: By creating an organized and succinct data recording system, inventory tracking becomes simpler while current trends can be identified and applied directly to inventory for maximum effectiveness.
Also Read: Revolutionize Your Manufacturing Process: 5 Ways ERP Software Boosts Efficiency and Profitability
Important Batch Production Features In ERP Software
There are several essential features any batch manufacturing ERP software system should possess:
Extra Lot Features
ERP packages typically provide only a limited set of lot attributes, such as number, date and description for their users' use. But batch makers typically need even more information, including container type, expiration date extensions, quality status statuses and expiration dates - your software should ideally support an infinite number of extra lot properties defined by users themselves.
Traffic Lights
Traffic Lights ERP software relies heavily on lists. Data are displayed as lists, with individual rows selectable to reveal forms with record-specific data. While long lists can be daunting, batch manufacturing traffic lights provide an invaluable solution: simple red, yellow and green markers make finding information much simpler by signaling which lots have passed quarantine and inspection and are ready for shipment. Simply put - some colors make finding what you need much simpler.
Labeling Of Products
Accuracy in printing labels is of utmost importance. Be sure to have an efficient system in place for labeling individual goods and lot numbers quickly and reliably.
Tracing Lots
Traceability should be at the core of manufacturing operations and should function from both sources to finished goods, as well as from source materials to final goods.
Selecting Techniques
While batch manufacturers frequently employ the FEFO (first expired, first out) principle for inventory picking purposes, traditional manufacturers often utilize techniques like LIFO or FIFO inventory picking techniques instead. Before selecting one of these selection techniques for yourself, be sure that they meet all of your needs.
Splitting And Consolidating Lots
Because manufacturing chemicals and pharmaceuticals often requires lot splitting or merging, lot splitting or merging may become necessary. It is crucial that multiple lot numbers can be combined into one; alternatively, operations could become more efficient by employing automatic lot splits based on quality; for instance.
ERP And Product Traceability
Product traceability is all around us, yet not always obvious. This involves an object's serial number being listed, something we see every time we complete a warranty card for our new computer, camera, or kitchen appliance. Manufacturers use serial numbers as a quick way of quickly determining its delivery or sale date as well as applying any applicable warranties accurately while they remain active.
Traceability extends far beyond warranty management; product safety is also a top concern that typically necessitates lot or batch number tracking. Nearly everything on an airplane you are about to board has either a lot or serial number assigned; similarly processed food items often come with their own batch number attached as well.
Most of us know that everyone from supermarkets to automakers are conducting product recalls, yet not all have considered how lot or serial number traceability plays into this process; even fewer realize that companies with effective ERP systems no longer need paper chases for tracking products.
An ERP system installed correctly today can deliver bidirectional traceability within minutes of reporting a product issue, such as when buying pizza at a store. Initial steps taken by this type of system would involve pulling all remaining inventory off shelves at the specific location where an issue was reported and notifying their warehouse or central distribution location if any is still present there.
Once a manufacturer learns of an issue lot number, their initial step should be to find out who among their customers received any from this batch. By spreading word back upstream and all along their supply chains to the manufacturer, everyone involved can check whether or not any problematic product exists in their inventory. But the system can do much more.
Utilizing pizza as an example again, manufacturers can identify all of the lot numbers used by examining the lot numbers on its box and asking "Where did those batches go? This corresponds with bidirectionality; similarly, suppliers of such goods could raise similar questions if any ingredients appear suspect.
All these questions can be asked and answered quickly using electronic databases, saving both time and resources in comparison to reading paper archive archives manually. Although pizza was used as an example here, similar needs exist across industries including aerospace and pharmaceuticals.
Conclusion
Lot numbering systems provide an effective method for monitoring batches of similar-type items, helping inventory management more effectively by maintaining appropriate stock levels in your inventory. Lot tracking helps simplify keeping an eye on moving stocks; and you can manage lot numbers effectively to maintain optimal levels in your stockpile with the use of an ERP system.