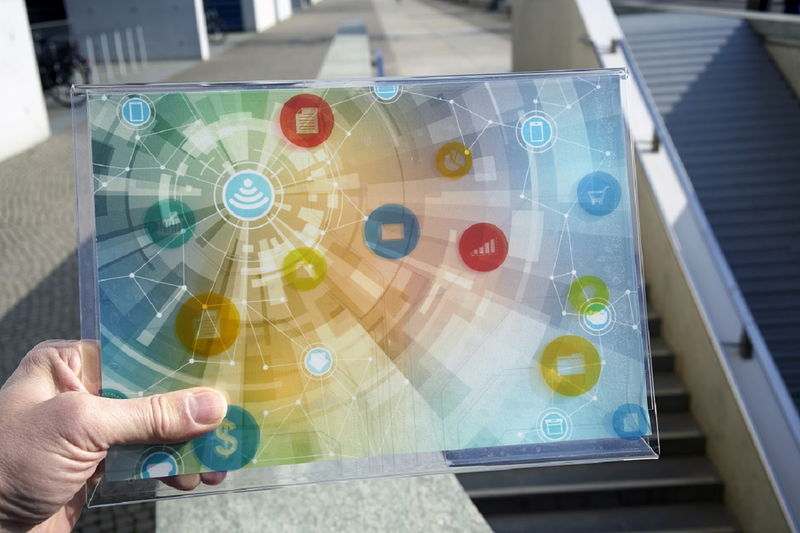
The high degree of efficiency and diversity in the manufacturing industry makes it possible to find a solution that improves performance, lowers prices, increases revenue and productivity. ERP manufacturing allows for the creation of a central database that integrates all operational activities.
ERP systems used to be only for large corporations. In the last year, however, they have become more popular.
Examine the Top 10 Benefits of ERP in the Manufacturing Industry
Adaptability and Automation to Automate Business Processes
ERP manufacturing Automates standard procedures within your company by consolidating real-time information in one central hub and giving users visibility of every operation without moderation team member interference. ERP manufacturing also helps speed manufacturing process speeds up, reduce error risk and boost profitability compared to manual operations under business operations to deliver better customer service in all business processes.
Manage Cash-Flow
A steady cash flow for most companies is crucial. You can manage cash flow better with an integrated manufacturing ERP solution. You can run purchasing and planning reports, track past due invoices, and receive real-time data that allows you to check your data quickly. Every transaction is recorded, so you will have a record of everything that goes out.
CRM (Customer Relationship Management)
Most of a business's revenues come from just a subset of its customer base, so manufacturers must maintain careful records of interactions with top customers to remain competitive in the market. An ERP system with integrated CRM functionality enables manufacturers to keep tabs on these interactions without spending additional funds for an external CRM solution; salespeople using an integrated CRM module are better able to track leads efficiently while continuing conversations, so handoff to new people will go smoother.
Keep all quotes, orders tracking information, emails, contracts, issues, and solutions organized into one central hub. Customizable reports notify upper management about customer satisfaction issues that require action; dashboards provide all personnel access to necessary data, while C-level managers benefit from the integration of an ERP sales module for comprehensive insights into sales performance; additionally, many providers of manufacturing ERP software aim at speeding up manufacturing processes while simultaneously cutting costs and improving accuracy through Industrial Internet of Things technologies.
Industrial Internet of Things: Enabling it
Only recently have internet-connected refrigerators been considered futuristic. Machine connectivity, the Industrial Internet of Things, and everyday object networking have become commonplace across industries and objects. Manufacturing has gradually adopted IIoT into production lines with real-time sensors embedded into parts and equipment connected to production systems - this helps ensure prompt notification whenever maintenance or repairs need to be performed on any equipment in need of attention. IIoT technology improves maintenance management through rapid notification when any component requires attention or repair.
Producers can connect their products directly to the internet in order to monitor problems, analyze usage patterns, and keep an eye on clients. Updates may even be automatically sent directly to products to enhance functionality, eliminating customers needing to visit stores or return items themselves.
Making a Policy Decision
Open-source ERPs allow companies to make more accurate manufacturing decisions faster. Their clients can assess situations more rapidly and accurately using open-source ERP. By accessing key performance statistics such as sales volume and margin of sale at any time, manufacturers can stay focused and take timely actions at any point when the growth of the industry projects at over 10% yearly growth projection. Therefore, understanding internal divisions and systems is crucial in managing daily operations successfully.
Reduced Costs And Improved Profitability
As business executives look ahead, their primary aim should be increasing revenue over the next two years. Lower costs result in greater work output and profits; ERP allows enterprises to quickly respond to changing market dynamics like raw material costs and delivery schedule shifts with quality decision-making thanks to quick processing times stored all data within one integrated database, including increased organizational efficiency that reduces wasteful practices while pinpointing areas less profitable while controlling and managing inventories has never been cheaper.
Want More Information About Our Services? Talk to Our Consultants!
Improved Business Insights
Businesses can quickly increase product output when quality management, project planning, simplification, and aligning sales chains are accomplished swiftly. Maintaining consumer satisfaction requires timely deliveries of goods via actionable insights with real-time visibility in manufacturing organization that helps to meet business challenges in development services with business intelligence.
Manufacturing ERP for SMEs offers precise data to allow management an accurate view of inventory levels. Modern ERP programs like cloud ERP or web ERP help manufacturers increase profitability through increased tracking, automation, and collaboration capabilities. Manufacturing ERP programs for small enterprises (SMEs) offer accurate stock levels displaying accurate details to provide precise management visibility into stock levels. Modern manufacturing ERP programs such as cloud ERP or web ERP programs may help manufacturers boost internal profitability by improving internal processes like tracking automation collaboration & tracking solutions for SME manufacturers.
Flexible Workplace
In a world of pandemics, manufacturing flexibility allows for rapid responses to changing customer needs. Flexible manufacturing allows a business to better collaborate with customers and the market, respond more quickly to changing demand, and produce to order. Flexible techniques can increase market share and efficiency and reduce costs.
Improved Product Quality
ERP systems can help businesses better manage production. This technology gives managers instant knowledge of product defects and problems occurring in production lines. Team leaders can identify problem areas and quickly fix them. As a result of improving the quality, sales will increase.
Providing One Source Of Company Data
The manufacturing industry often needs help with logistics issues when assembling data from multiple sources. ERP software provides a central location for all information about the business, including productivity statistics, pricing, and administrative statistics. It is possible to make actionable and real-time decisions for an organization by using the exact source of data.
Ten Trends that Will Dominate Manufacturing by 2023
This blog will discuss the manufacturing trends we predict for 2023 and how manufacturers can benefit from them.
The Uphill Battle Is A Result Of Labor Issues
News stories have detailed the Great Resignation. Thousands of employees left their jobs to seek better opportunities elsewhere - better pay, workplace conditions, and a balance between work and life. Manufacturing resignations increased by 60 compared with pre-pandemic levels, while recent surveys show one-fifth of workers believe their resignation may continue within one year;
Manufacturing employment issues remain an acute concern; Due to its technical nature, manufacturing production work has become acutely affected by labor shortages.
As manufacturers move toward 2023, their primary objectives should be hiring and retaining young talent.
Workers Demand More Favorable Working Conditions
Current job markets offer manufacturing workers more influence than ever to influence manufacturing firms to improve workplace conditions, with manufacturers creating new policies and programs designed to accommodate employees better, such as flexible work hours and higher wages for workers and advancement opportunities and wellness programs. With so much competition among manufacturing firms today, manufacturers need to attract new workers and retain existing ones by helping create greater work-life harmony for everyone involved in production processes.
Health remains of primary importance to manufacturers as employees and vendors return to work environments. They should continue emphasizing proper sanitization measures while closely tracking those entering or leaving their facility. Traceability will remain an increasingly prevalent trend within manufacturing; companies are taking back data owned by OEMs while demanding increased supplier transparency.
The Day of the Product-as-a Service
At one time, relationships between manufacturers and their customers were, at best, superficial: once customers purchased something, they only interacted with the manufacturer again if in need of repairs or needed to add other equipment. Nowadays, customers expect brands they use regularly to be accessible 24/7 so they can make purchases when necessary and without unnecessary transactions between purchase and consumption. These shifting customer expectations present some unique opportunities as well as challenges. In particular, Products as Services represent such opportunities.
Product as a Service (PaaS), referred to as Servitization or PaaS and sometimes abbreviated as "PaaS," refers to an arrangement where manufacturers provide subscription-based services or lease equipment rather than selling directly. Customers pay only for what services they need while benefiting from OEM support and new value-added options that help optimize operations.
Manufacturers also stand to gain from Product as a service offering. Moving away from selling equipment as capital expenses towards an ongoing expenditure model means manufacturers no longer need to process single transactions one at a time; with PaaS, they can generate recurring revenues, which allow them to capture more aftermarket revenues during the equipment's entire lifespan while at the same time gathering information on customer usage data that allows them to optimize current offerings or create brand new offerings for customer use.
PaaS has generated significant attention over recent years. Yet its technology was far from becoming an attractive business model until very recently - thanks to IoT devices, AI, predictive analytics, and related technologies, which have finally enabled PaaS to become a viable business model and is becoming more accessible and cost-effective as time progresses; meaning more manufacturers can take advantage of PaaS services.
PaaS, which leverages these factors with shifting consumer habits - such as providing customers with superior experiences at lower cost -- will emerge as a top manufacturing trend by 2023.
The Internet of Things (is) still The Big Thing
Industrial IoT (or, more correctly, the Industrial Internet of Things - IIoT), an emerging manufacturing trend in 2023 due to its variety of use cases, is fast becoming one of the major manufacturing trends in 2023. IIoT allows devices connected through internet infrastructures to exchange real-time information, enabling manufacturers to make informed strategic decisions and achieve goals such as cost cuts, increased efficiency, safety improvement, and product innovation - among many others.
This is partly because IIoT can be used for a variety of purposes, such as:
- Monitoring equipment in real-time and comparing metrics to established Key Performance Indicators (KPIs) allows for measuring overall equipment effectiveness.
- Setting a baseline of normal behavior for equipment and using that to detect abnormal behavior for preventive maintenance
- Remote analysis of equipment can identify issues and potential problems before they occur.
- Monitor production in real-time, including specific production lines, unit operations, and equipment. This will reveal hidden inefficiencies.
- Improved traceability by using radio frequency identification and barcodes to track finished products and supplies
- Integration of complex systems with data from enterprise resource planning systems (ERP), quality management software, and computerized management systems to perform in-depth diagnostic, prescriptive, and predictive analytics
Product as a Service, a combination of these two applications, has cemented IIoT as a trend in the industry for another year. To collect customer data and unlock its valuable data-driven insights, manufacturers need to embed IIoT sensor technology into equipment that they plan to lease.
Read More: What is Manufacturing ERP? Everything You Need To Know
This is the Next Generation in Predictive Maintenance
Predictive maintenance has long been an established trend within manufacturing industries. While its significance will not change by 2023, manufacturers are beginning to adopt predictive resolution instead of predictive maintenance as part of their strategies for maintaining profitability and growth.
The predictive resolution goes beyond predictive maintenance's use of data analytics to detect anomalies and their causes in equipment performance, providing technicians greater insight into solving them more accurately and faster. By increasing chances for resolution on the first attempt, the predictive resolution allows manufacturers to increase equipment efficiency while cutting costs while increasing first-time fix rates and speedy repairs.
Manufacturers have long desired predictive models yet need help accessing enough data in order to do so. Recent innovations such as Artificial Intelligence (AI), Machine Learning (ML), and Natural Language Processing (NLP) allow manufacturers to convert unstructured information into forms usable by predictive engines.
As predictive revolution technology improves and costs decrease, manufacturers can become more affordable when combined with IIoT solutions. By applying predictive resolution with IIoT capabilities, manufacturers can extend machinery lifespan, ensure production assets or customer equipment operate optimally and identify issues before unplanned downtime occurs.
Product as a Service provides another key benefit, giving manufacturers access to valuable customer data, which they can use for machine learning models or prediction resolution.
Use these five steps to simplify your move to predictive maintenance:
The Modern Approach to ERP
ERP systems have long been an indispensable wide range of features of manufacturing firms due to their ability to automate processes, provide real-time accurate information, and reduce costs. Unfortunately, many manufacturers rely on outdated legacy systems that no longer meet their needs; as the manufacturing sector recovers post-COVID-19 outbreak, mergers and acquisitions (M&As) have also seen dramatic spikes, leaving newly formed companies saddled with significant debt.
Manufacturers have responded by updating their systems, transitioning to cloud solutions, and reconsidering what they want from an manufacturing ERP software system. 2023 should see an emergence away from customizing ERPs - adding unnecessary complexity that restricts consolidation efforts - towards modernization, where manufacturers take the initiative to assess business requirements, design global templates with best practices as the foundations, and optimize for growth.
The Meaning of Big Data for Manufacturers
Big Data has taken on greater significance due to the rise of IoT technology and predictive resolution solutions. Manufacturers can utilize significant data sources from an ever-expanding network and modernize systems to gain a complete picture of their businesses through this source of relevant insight.
Manufacturing companies with access to this data can use it to make more informed decisions regarding sourcing, production, fulfillment, and cost reduction. Such decisions support growth strategies while improving outcomes; should any decisions fail, they can learn what went wrong while adapting future approaches accordingly. 2023 marks an exciting era where Big Data goes beyond mere visibility; find its meaning and benefits.
The Digital Twins Improve Production Efficiency
Digital twins are a relatively new advancement in IoT. They're an exact copy of actual equipment or any component rendered in a virtual world. The digital twin is a replica of the actual asset, not just in appearance but also functionality, connections to other machines or components, and environmental conditions. The simulation allows manufacturers to conduct tests, create scenarios, train employees, and evaluate equipment performance under various conditions without touching the tangible asset.
Manufacturers can use digital twins to their advantage in all aspects of the business.
- We are modeling various processes to identify bottlenecks, inefficiencies, and potentials.
- An easy and inexpensive way to test new production lines and prototype new products that will accelerate the speed of market
- Monitoring equipment health and performance on production floors and in the field.
- Test out improvements and repairs to measure their effectiveness, increase FTFRs, and support prediction.
- Training new employees and technicians using the latest models of equipment
- Modeling of new business opportunities to support growth strategies
Rolls-Royce provides an outstanding example of digital twin technology in action. A commercial aircraft engine manufacturer, it utilizes IoT sensors on 13,000 engines across its fleet to gather health, fuel consumption, service needs, and performance information, which is combined on Microsoft Azure to form digital twins used for improving maintenance practices, tracking inflight performance tracking capabilities as well as offering fuel and route recommendations to airline customers, etc.
Read More: Process and Features of Manufacturing ERP
Given their vast array of uses, digital twins will likely become an industry trend by 2023; their prominence will only increase with time.
Manufacturers Can Make The Most Of Supply Chain Challenges
Supply chain disruptions will likely remain, even though we would all love them to end by 2023. Unfortunately, current circumstances do not bode well; with rising freight costs and driver shortages making matters even worse; factory closures due to geopolitical conflict; climate change; new weather patterns all being factors. Manufacturers must adapt accordingly and make the best of bad situations through outsourcing strategies such as these.
Some manufacturers opt to handle fulfillment themselves rather than depend on third-party logistics firms for fulfillment services by purchasing an outside logistics firm or creating in-house logistics operations. This enables greater supply chain visibility, quality control, reduced shipping costs, and time savings due to more efficient logistic networks.
Direct-to-consumer sales have also evolved as an alternative to multi-tier channel distribution models, where products are moved directly from manufacturer to distributor or wholesaler to final consumer. Like insourcing, this model eliminates intermediaries so manufacturers have greater control of the brand image, pricing, and building stronger relationships with original equipment manufacturer clients. Furthermore, some companies use this tactic directly with suppliers rather than through intermediaries, creating more integrated supply chains.
As more manufacturers follow suit in 2023 and find innovative solutions to supply chain issues, investing in this technology could provide resilient supply chains capable of weathering disruptions and creating resilient supply chains. It would also add redundancies within supply chains to withstand disruptions while creating resilient supply chains.
The Interest in Near-Sourcing & Reshoring Remains High
Reshoring, the process of shifting imports back into domestic production, was in full force among U.S. manufacturers by 2023. Reshoring, also called nearshoring, has gained popularity for a variety of reasons:
- In recent years, the economies of many countries considered offshoring destinations have grown stronger, increasing their wages.
- The infrastructure of countries where labor is cheap only supports complex manufacturing processes.
- COVID-19 has raised the issue of manufacturing industries' dependence on offshore facilities when supply issues lead to production problems.
- The global port congestion and shipping rate increases are predicted to continue well into 2023.
- Robotics and advanced software allow manufacturers to automate several processes that previously required manual intervention.
Manufacturers continue evaluating sourcing strategies alongside renewed efforts at reshoring. With supply chain disruption causing difficulty for many global supply chain players sourcing material elsewhere.
By 2023, reshoring will remain one of the primary trends in manufacturing, with companies looking for ways to eliminate or minimize their dependence on foreign materials. Reshoring will enable American producers to remain resilient against disruptions to supply chains while simultaneously contributing to strengthening U.S. economic fortunes.
Want More Information About Our Services? Talk to Our Consultants!
Conclusion
Manufacturing, or "factory," refers to one sector of the economy producing goods and services, requiring efficient production methods. Manufacturing software offers one way of improving the operational efficiencies of any organization, and understanding pricing schemes can give excellent insight. To find out more, get intouch with the best and most reliable software solution for manufacturing operations.