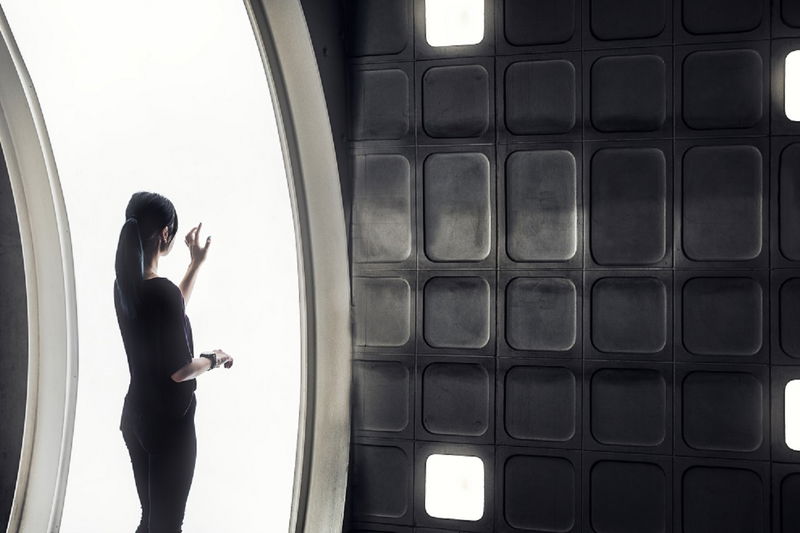
Inventory management refers to placing orders, keeping inventory on hand, using it, and selling it for a business. It involves handling components, raw materials, and finished goods as well as their processing and storage. Depending on a company's demands, there may be various kinds of inventory management systems.
The Development And History Of The Global Supply Chain
Over the last century, global supply chains have undergone dramatic transformations. Our approach to procuring, producing, and delivering commodities has drastically shifted. Today's supply chains are more efficient and complex than ever due to factors like computerization, containerization, innovative handling techniques, and the introduction of ocean-going boats.
At first, we thought it would be fascinating to examine how supply chains have operated historically and highlight essential inventions that shaped this industry.
The Supply Chain Before 1900:
Local and Regional Manufacturing and Supply
Before the industrial revolutions in Europe and America, most supply chains were limited and local. A farmer would harvest wheat from his field, send it off to be ground into flour at a mill, and deliver it directly to a baker who made bread before finally selling it at market stands as part of an agricultural supply chain.
Following the Industrial Revolution, things started to change rapidly. Although supply chains remained restricted to certain countries, railroad construction allowed quicker, more accessible, and less expensive goods transfers across greater distances. Hand trucks and other simple instruments made handling things simpler during this period. Unfortunately, international maritime trade was relatively inefficient because loose items were laboriously loaded onto ships' hulls and then unloaded again from them creating further inefficiency within international commerce.
The Early 20th Century Supply Chain:
Advances in Transportation and Storage
As soon as the internal combustion engine and the automobile were invented in the late 1800s, innovators began creating trucks to expedite the transportation of commodities via road. Mack Trucks was founded in 1900, and the first semi-truck was built near the end of the 19th century. Diesel engines powered by petrol first appeared in the mid-1920s; forklift trucks had preliminary designs before 1930 and underwent additional development before their official introduction.
Pallets first debuted in warehouses in 1925, marking a groundbreaking innovation for supply chain management. Pallets made it easier to stack items vertically while saving space by grouping them on pallets increasing efficiency when handling commodities.
The 1930s And 1940s Supply Chain:
Increasing Mechanization
World War II logistics played an essential role in military groups' survival as they required efficient supply lines domestically and overseas. Supply networks were necessary domestically to manufacture equipment and supplies and to support and ensure timely distribution to troops overseas. Supply chain engineering developed from an amalgam of efficient operations research and industrial engineering in the 1940s.
Over the following decades, pallets, handling, and storage methods were continually improved. The goal was to optimize rack architecture while better-using storage space available within warehouses speeding up delivery and distribution times as these modifications began streamlining loading, unloading, consolidation, and handling commodities operations.
The 1950s Supply Chain:
Standardization and the Arrival of Containerisation
Creating and implementing shipping containers was one of the most significant transformations to global supply chains. "One key advantage of shipping containers is their intermodal nature; they can easily be transported using various modes of transportation," as we noted in our guide to containerization. Standardization makes handling and transporting these containers swift and straightforward, whether by truck, rail, or ship.
Every minute saved can translate to cost and efficiency savings for an entire supply chain, as each minute saved adds up to improved margins, reduced waste, lowered environmental impacts, faster goods transfers, and quicker turnaround.
Shipping containers were first developed in the mid-1950s; however, their widespread adoption wouldn't occur until late 1966. Transportation equipment manufacturers then started producing cars capable of moving these containers. Containerization became one of the key factors contributing to lower international trade costs while increasing efficiency.
The 1960s And 1980s Supply Chain:
The Chain of Supply More Computerization and Increased Efficiencies
In the 1960s, products began moving away from railroads and onto trucks for distribution. Freight transportation became more reliable thanks to pallets, handling equipment, containerization, and other related fields; even over greater distances, time-sensitive raw materials and products could now be transported efficiently.
In 1967, computerization gained momentum, with IBM creating the first computerized inventory management process and forecasting system. Before this era, logistic data and records were collected, sent, and reported using paper records; data computers increased efficiency with better forecasting, warehouse storage capacity management, truck routing options, inventory control methods, and improved forecasting processes.
Once real-time warehouse management systems were introduced in 1975, managing orders, inventory, and distribution became simpler thus increasing productivity, Barcodes quickly replaced manual SKU and product code entry, making product scanning much simpler.
The 1980s and 1990s Supply Chain:
Enhanced Efficiencies and the Transition to a Worldwide Framework
Supply chain participants, transportation equipment manufacturers, and others expanded on their achievements during the 1980s. "Supply chain management" first debuted in 1983 and underwent further transformation through PCs; adaptable spreadsheets, mapping software, route planning services, and route optimization tools have helped track expenses more efficiently while improving earnings potential compared to earlier tools like paper records or envelopes. Alongside these developments emerged Enterprise Resource Planning (ERP) systems, supply chain distribution networks, and air freight optimization technologies.
MIT also developed RFID tags precursors to today's Internet of Things devices - to facilitate electronic tracking of shipments and goods.
The Current Supply Chain: Genuine Globalization
Current global supply chains continue to experience considerable change due primarily to manufacturing activity in Asia, China, Japan, and Korea are significant players as providers and exporters. Meanwhile, predictive and prescriptive analytics, combined with AI/ML techniques, have improved order management and forecasting capabilities and other benefits along with becoming a more networked, data-driven cooperative ecosystem that creates value through mutual use for all involved and tangible economic growth.
Of course, supply chain managers still need to overcome many barriers to meeting this objective. Ethics in product sourcing and production remain of increasing concern to consumers and corporations alike, particularly regarding workers' rights and environmental sustainability. Furthermore, supply chain managers require effective risk management systems if unexpected circumstances such as taxes, customs duties, natural disasters, or transportation challenges occur internationally.
No matter what the future holds for global supply chains, innovations that have led to higher profit margins, efficiency improvements, and optimization are surefire ways of driving value creation for suppliers and achieving optimal supply chain results.
Also Read: Mastering Inventory Management: A Quick Guide to Boost Your Business Efficiency
The Advantages Of Good Inventory Control
Cost Savings
The reduction of carrying costs related to excess inventory is one way that efficient inventory management strategies aid in cost optimization. Strictly speaking, cost optimization is challenging when there is too little inventory since it can result in lost sales opportunities or production delays. Resources that would be better used elsewhere are depleted by overstocking.
Enhanced Client Contentment
Effective inventory management lowers lead times and stockouts by guaranteeing that goods are available when customers need them. Happy customers are more inclined to recommend you to others and do business with you again.
Enhanced Operational Efficiency
Businesses may improve their manufacturing and procurement operations by keeping a careful eye on inventory levels and demand trends. As a result, they are able to decrease waste, streamline procedures, and raise overall efficiency. As a result, process optimization is more successful and total efficiency rises significantly.
Data-Driven Decision Making
An understanding of inventory management can help with demand planning, supply chain strategy, and forecasting. Businesses are able to make educated decisions that align with consumer preferences and market trends when they have access to precise data from inventory management systems.
Reduced Obsolescence Danger
Keeping outdated goods on hand runs the danger of making them outdated eventually. Through the replacement of products before they become obsolete, an efficient inventory management method lowers this risk.
Inventory Management's Difficulties
Demand Forecasting
The market in India is extremely dynamic and diverse, making it challenging to estimate demand accurately. Businesses require assistance in precisely estimating their demands for excess inventory in order to plan their inventory, as a result of demand swings, seasonal variations, and evolving consumer preferences.
Supply Chain Complexity
Multiple manufacturers, suppliers, and distribution channels are involved in modern supply chain activities, and they must cooperate to ensure constant inventory levels throughout their supply chain processes. Although coordinating all of these organizations can be difficult, it is essential to maintain consistent inventory levels.
Infrastructure And Logistics
Inventory movement is severely hampered by supply chain procedures, intricate tax regulations, and poor transportation infrastructure, especially for company categories that depend on just-in-time inventory control techniques.
Data Accuracy
Software for inventory management that is effective is built on accurate data. Inaccurate data can lead to any kind of judgmental departure; therefore, it is essential to maintain its integrity through strong tracking measures and frequent audits.
Technological Integration
Inventory management technologies must integrate seamlessly with current systems and investments for successful deployment. So, companies must ensure their IoT (Internet of Things) and RFID (Radio Frequency Identification) technology supports efficient inventory management procedures.
Techniques For Inventory Management
Corporations employ various inventory management strategies depending on the nature of their business category or product being evaluated. Just-in-time (JIT) production, materials requirement planning (MRP), economic order quantity (EOQ), and days sales of inventory (DSI) are some examples. While these four techniques are often used for inventory analysis, others may be.
Just-In-Time (JIT) Management
JIT inventory control carries some risks. A company might need more inventory if demand suddenly spikes unexpectedly, potentially harming customer relations and driving the business landscape away from its services to competitors. Furthermore, any delay of even one critical input could create bottlenecks, which cause further business loss for that firm.
The Planning Of Materials Requirements (MRP)
Due to this inventory management strategy relying on sales forecasts, manufacturers must keep accurate sales records to assess inventory requirements and promptly notify material suppliers of these needs.
Inventory Days Sales (DSI)
This financial ratio measures how long it typically takes a high-value business, including goods still in production, to convert its inventory into sales. There are various manual methods for interpreting Days Sales In Inventory (DSI), also referred to as average age of list or Days Inventory Outstanding (DIO), Days In Inventory Outstanding (DII), or simply Days Inventory Outstanding.
Quantity Of Economic Orders (EOQ)
These inventory control methods help businesses determine how many units to add with each batch order to reduce overall expenses based on constant customer demand. Holding and setup expenses are included within inventory costs in this model.
To avoid placing orders too frequently or stockpiling too much inventory, the Economic order Quantity (EOQ) model strives to ensure that just enough is ordered per batch. It assumes an equilibrium between setup and holding costs for merchandise that should minimize overall costs; indeed, minimizing both would reduce overall inventory costs significantly.
Conclusion
Inventory management is pivotal in every supply chain, impacting financial performance, customer satisfaction, and operational efficiency across industries. Increased effectiveness has been achieved thanks to companies adapting to changes in consumer needs, data analytics, technology, and supply chain techniques and adopting them themselves not to mention reaping direct benefits.