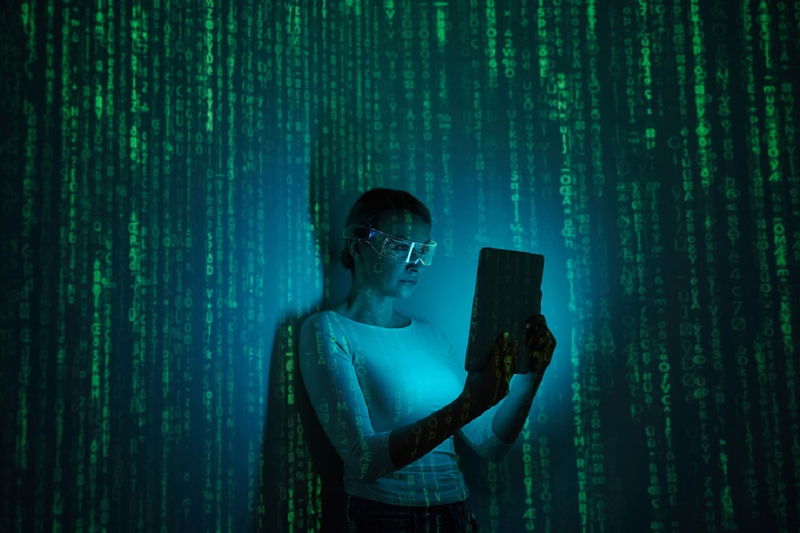
Improve online shopping platform and marketing strategies by learning essential inventory management techniques. Now comes your time! Your eCommerce business has launched after months of planning and hard work - it's even running already. Congratulations on creating and living out your dreams! Retail is full of untapped potential; knowing how to do real time inventory management properly will maximize that potential and ensure its maximum growth potential for success in any retail venture.
What Is Ecommerce Inventory Management?
Ecommerce company inventory management refers to procuring, storing and selling stock at its optimal prices and locations for maximum profitability. Effective inventory management ensures you know which reserve exists as well as its respective sale prices, intended destination(s), length of stay (how long they remain on shelves, etc).
Businesses must understand inventory management to reduce waste and costs while saving time and resources. By giving customers what they want when they want it, maintaining supply increases customer expectations while decreasing wasteful practices.Many businesses need to be made aware of the best real time inventory management practices. Even larger firms failed because they required proper techniques and systems.
Learn The Intricacies Of Inventory Management
Why It Is Important
Stock control does not have to be difficult, but it is still essential. Stock levels can help you to know;
Reorder: When stock is running low. Be aware when your supply levels dwindle to ensure you can supply your customers with products. If you run short of milk on your weekly shopping experience, you will buy more before the milk runs completely dry.
Reordering: How Much? Suppose that you own and run an online store of pets. After seeing how well squeaky toys for carrots sold, you need more. Order only a few, or you risk creating too much noise with overstock. Inventory management helps maintain appropriate levels.
Order: If the carrot sells well as a toy, would a tomato that squeaks also? Inventory tracking can also help measure product success and justify purchase decisions.
How Long Should Stock be Left Out/in Warehouse: Perishable items may become waste without adequate real time inventory management and could go unsold and remain unsold, becoming outdated or no longer fashionable.
Inventory Management Software: Finding The Best One
Selecting a real time inventory management solution can be daunting. Consider your business's size and individual requirements when choosing; GoCodes recommends answering these critical questions about each potential software option before settling on one.
- How many users are required?
- Is the software scalable as your business grows?
- Does the software work with other systems or devices?
- Do they offer data migration support?
- Can the reporting system be customized?
- Can you audit your stock history?
- Is it possible to detect and prevent inventory theft, loss or misplacement using this software?
- Need to use the Inventory Management Software on Multiple Devices?
- How good is their support in troubleshooting issues?
You want software that meets the following criteria:
- Has the ability to analyze data instantly;
- Optimize inventory by analyzing data
- Considers both overstocking (and understocking) and the stocking of products.
- Takes into account seasonality;
- Adjusts the settings based on where the product falls in its lifecycle.
Software that optimizes pricing can also immensely help profit maximization and clearing space for new items. By receiving recommendations about when, why, and at what prices your items should be sold at higher or lower prices, respectively, based on season sales data, as well as when your stock can be cleared out at the highest profit while making room for future additions.
Auditing: What You Should Know
Auditing involves checking your stock. Although automated software has advanced significantly, manual auditing still plays a vital role in accounting for stolen products or detecting potential problems with overstocking or understocking issues.Initial auditing may include counting all stock at least twice annually - this method takes time, can be tedious and can become boring quickly.
Second, conduct an annual count to complete a cycle counting audit that measures accuracy by comparing already recorded numbers with ones newly counted.Spot-checking is another critical strategy you can employ. Doing this requires randomly comparing an item's number against those recorded by software to ensure all numbers you use are correct. This technique ensures accuracy across your work process. Different approaches work better for other companies; here are a few methods you could try.
Audit Of Types
Setting Par Levels
Sometimes referred to as maintaining safety stocks, setting Par levels allows a company to structure, organize, and prioritize certain products by guaranteeing there's enough inventory of each. Developing this level in hospitality environments helps prevent food waste while creating healthy checklists.
Calculate the Par Level with this formula.
Par Level (Weekly Inventory Use + Safety Stock)/ Delivery per Week.
Keep between 20-30% as emergency savings reserves.
With this approach, employees can possess less knowledge of inventory forecasting management; staff will know exactly how much is necessary.
First In, First Out (FiFO)
To maintain an efficient flow of products and simplify record keeping, use First in First Out as the framework focuses on selling older stock first - in other words, FIFO (First In, First Out). It makes record-keeping much simpler because no inventory counting is needed anymore!Fashion requires that many products quickly change in line with trends, from tech devices and clothing to anything in between. Don't allow piles of "Mom Jeans" to accumulate in your closet; now they could come back into style for sale!FIFO stock rotation allows for regular replenishments without incurring clearance sales costs or drastic inventory reductions.
ABC Management System
This approach to categorization identifies items from least valuable to most valuable by simply reviewing inventory to see whether any particular line falls into A, B or C categories;
A is for highly valued but limited quantities, while B/C have regular products with moderate numbers, while C covers those of lower value but higher numbers.B contributes 15% of revenue and 30% of stock. C provides 5% in revenue contributions while also holding half the store.
Your online shoe shop could use ABC as follows.
A: High-end expensive trainers (80%). Simply selling three in a day will generate most of your earnings, as these items tend to sell slower due to limited appeal among buyers.
B: Work shoe sales fall between what has been in stock and what has been ordered, though sales don't tend to be extensive; nonetheless, they exist, and these essential products represent around 30-35% of stock and 15%-18% of total revenue sales.
C: socks are our most sought-after daily stock item, accounting for 50%. Despite selling in large volumes, their cost remains very affordable and only 5% profit is gained on each sale.
This Strategy Lets You Focus On Products With High Potential Profits For An Ecommerce Brand And Decide What Items Should Be Stocked In Advance.
Essential Inventory Management Strategies For Ecommerce Solutions
To use inventory management effectively and maximize profit and customer experience, keep these five methods in mind when managing inventory for an eCommerce supply chain business. They're sure to improve inventory lifespan while guaranteeing lasting potential customer relationships!
-
Prepare An Inventory Of Safety Stock
It's essential to be prepared in case any unexpected events arise; having an adequate stockpile of safety supplies is vital.Your inventory could come in handy for numerous purposes; just consider recent instances of last-minute shopping carts as proof that supply and demand can be unpredictable. Being prepared can give you peace of mind; keep one handy to prepare yourself in case anything unexpected comes your way!
-
Balance Inventory
Suffice it to say, and it is simple enough: the key lies in stocking enough inventory without overstocking or simply finding that right balance!Stock levels that exceed capacity require liquidation to prevent your inventory from depleting too quickly and leaving customers disappointed in finding what they want unavailable, while at the same time, risk losing potential clients through poor reviews and clearance sales. This situation will create losses both financially and through possible bad reviews from unhappy customers. Avoiding this issue requires using appropriate ecommerce software and managing inventory properly.
-
Kitting Can Be Useful
Kitting, the practice of grouping stock for sale as part of an offer (e.g. Buy Two Get One Free), helps eliminate excess inventory at an incredible value, increases average order values, and lets customers know they are receiving great savings deals.
-
Evaluate Past Purchases To Predict Future Stock.
Looking back over your purchases to predict future stock allows for establishing an effective feedback loop, which helps determine which stocks work. It allows for easy identification of whether inventory needs to increase or decrease; you can track stock to identify which products sell best while monitoring annual trends.
-
Creative Storage
It is crucial that when stockpiling items for sale, careful thought be put into their storage options. If storing in an additional room or warehouse, ensure that items can easily be located by keeping their labels clearly displayed and labeling each box or bag according to their type.
Place them somewhere easily accessible so your customers receive their product sooner. Consider trends and sales when selecting their location; adjust as necessary so your stock stays manageable while providing exceptional customers happy service.
Inventory optimization can make or break e-commerce profits and costs. Inventory Control plays an essential part in increasing profits while decreasing expenses.Inventory Management requires tools and techniques that enable you to predict customer demands and track trends accurately.Manual inventory tracking using spreadsheets may become cumbersome, leaving important features accounted for. Inventory management tools exist for companies of any size to track inventory levels efficiently. Many inventory control techniques can be implemented quickly and affordably to improve e-commerce sales and profits.
Also Read: Top 10 Eminent Benefits of Inventory Management Software
The Best Inventory Tools and Techniques for Ecommerce
ABC Analysis
ABC Analysis (Activity-based costing Analysis) is an inventory classification method which groups products by value.
What it Does
Our inventory is divided into A, B and C categories for easy organization.
- Items marked "A" are of high priority, are fewer and add significantly to the overall value.
- The middle is where the "B"-items are located
- The most common things, "C", contribute to the lowest value of the entire total.
It's useful
ABC Analysis is an Inventory Audit Technique which can prove immensely helpful when various products have differing prices and sales values to account for. This process helps identify items of higher priority requiring more focus on revenues generated.
Benefits
ABC Analysis allows businesses to focus on what matters most for them. It also enhances Inventory Control and customer satisfaction by making high-value products readily available while increasing cash flow by eliminating low-value stockpiling activities.
Other Considerations and Disadvantages
ABC Analysis can be too simplistic as it needs to consider seasonality or new product launches. Also, its framework cannot accurately represent consumer behavior or trends.
JIT (just in time) Inventory
Toyota utilizes the Just-in-Time Inventory Management Strategy HTML1 developed in Japan for inventory and manufacturing process management.
What it Does
JIT's strategy aims to reduce inventory costs. This can be accomplished by only ordering completed goods when necessary - thus decreasing stock levels and carrying costs.
It's Useful
Just-in-time can help businesses meet fluctuating demand levels without risking holding onto expensive inventory, which would otherwise accumulate quickly over time. Businesses manufacturing high-value products may find this service particularly advantageous since inventory costs often prove significant.
Benefits
JIT inventory can reduce costs associated with excess inventory by eliminating obsolete stock, waste and unnecessary expenditure. This reduces outdated products, waste disposal-related fees and expenses related to holding onto unneeded supplies.
Other Considerations and Drawbacks
JIT requires reliable suppliers with clear inventory visibility; thus, it may not be suitable for every small business. Production cannot afford any errors or delays, as any disruption to this schedule could halt operations and damage current customer feedback relations.
Economic Order Quantity (EOQ)
An Economic Order Quantity formula can help calculate an ideal order quantity of units for future purchase orders.
What it Does
Three variables are utilized within the EOQ Model. These variables include:
- Cost of Maintaining Inventory (H:) outlines the costs associated with keeping stock in the warehouse.
- Demand (D) for the Year (Y): Sales demand over the previous 12 months
- Order cost refers to the price per unit purchased.
It's Useful
Organizations with predictable and steady demand can benefit significantly from using an Economic Order Quantifier (EOQ). Assuming constant need means any fluctuations would lead to inaccurate calculations;
Benefits
EOQ provides companies with an effective means to reduce inventory levels and costs while meeting customer demand for inventory.
Other Considerations And Drawbacks
It should be remembered that EOQ assumes constant demand levels - this may only sometimes be accurate. Discounts or changes due to bulk purchasing are not considered in these figures.
Safety Stock
Safety Stock: A quantity kept on hand in case of stockouts.
What it Does
Once again, this calculation allows you to determine how many safety stocks to hold per SKU.
- Maximum Daily Use
- Maximum Lead Time
- Daily average usage
- Lead time
Now, plug this information into a stock safety calculator, or try this formula instead. Maximum Daily Usage multiplied by Maximum Length of Time = Average Daily Usage.
It's useful
Demand can be unpredictable. Carrying sufficient safety stock may help protect you when forecasts don't go as expected or demand spikes unexpectedly.
Benefits
Maintaining safety stocks can help businesses reduce stockout costs while meeting unexpected customer journey demand - keeping customers satisfied without needing as much capital for overstocking.
Other Considerations and Drawbacks
The appropriate quantity of safety stock must be ordered; otherwise, it could result in overbuying or understocking depending on how accurately your variables were entered. Inventory management software and cloud-based fulfillment expert services often come equipped with tools that simplify calculating safety stocks, such as historical data analysis tools, automated inventory reports, or order history archives.
Order Point Formula
Reorder Point Formula is activated whenever an item's stock level falls below a predefined point.
What it Does
A Reorder Point (ROP) system allows businesses to order stock at precisely the right moment to replenish inventory in an efficient and timely fashion before it runs out. The formula behind ROP:
Order Point (ROP = Demand during Lead Time + Safety Stock).
First, multiply the days in your lead time by your daily average sales rate or demand (demand).
Demand for Lead Time = Average Daily Sales multiplied by Lead Time
It's useful
Utilizing the safety stock calculation discussed earlier, and safety stocks can be calculated. The earlier analyses will also be used here to calculate your safety stocks. Reorder points can be an extremely effective tool to save business owners time when managing inventory replenishment processes, helping keep inventory replenishment processes on track and manageable.
Benefits
The reorder-point formula helps avoid stockouts and excess inventory while improving cash flow. This method considers lead times and daily average sales to gain an accurate representation of how many units must be manufactured today to prevent stockouts.
Other Considerations and Drawbacks
Other Considerations and Pitfalls Reorder points could be incorrectly determined if the lead time was unreliable.
Tracking by Batch
It is used as a method of monitoring goods within warehouse supply networks.
What it Does
Batch Tracking involves keeping tabs on products produced or received based on production/receipt dates, serial numbers or unique identifiers provided with each batch that allows companies to trace any issues back to their source and discover potential problems or defects simultaneously.
It's useful
Businesses involved with food, cosmetics and pharmaceutical products or needing quality control or traceability will find batch tracking extremely valuable.
Benefits
Batch tracking systems offer many advantages for improving product traceability, customer service safety, and upholding quality control standards.
Other Considerations and Drawbacks
Implementing a batch tracking system takes time, as you will require effective organizing and overseeing batch data.
FIFO (Freight In First Out) And Lifo (Load In First Out) Are Methods.
Of inventory valuation used by businesses today. Both practices entail tracking items from first in to first out.
What It Does
FIFO operates under the assumption that older inventory items will sell first, while LIFO operates with the opposite belief - selling newer inventory items first.
It's useful
FIFO can be particularly advantageous to industries containing products subject to expiration or obsolescence; however, LIFO provides tax benefits during inflationary increases.Each method offers advantages and disadvantages; what's important here is having Inventory Integration built into your accounting software -- be it Quickbooks, Xero or something else altogether.
Accounting software streamlines the accounting process, simplifying the accurate tracking of inventory costs, revenues and profits.
Benefits
FIFO allows for better representation of inventory on the balance sheet, while LIFO reduces income taxes during periods of higher prices.
Other Considerations and Drawbacks
FIFO can increase taxable income when inflation occurs, while LIFO requires more complex accounting procedures that may not be user-friendly.
Perpetual Inventory Management
A perpetual inventory system uses automated and software tools rather than manually tracking stock for inventory control in real-time.
What it Does
Recurring inventory systems continually update records as sales, purchases and returns occur, using software and barcode scanners to keep an inventory register updated and accurate.
It's Useful
E-commerce businesses can reap significant advantages by adopting an ongoing inventory management system, particularly those engaging in Multi-channel fulfillment solutions or having high sales volumes.
Benefits
The numerous benefits of perpetual inventory systems, such as real-time inventory data delivery, reduced human errors, and improved forecasting capability, can all add to their advantages.
Other Considerations and Drawbacks
Inventory tracking requires an initial investment. You must evaluate your existing technology stack to assess whether automating inventory tracking should become part of it.
Barcoding & Automation
Automating inventory control has transformed how businesses manage their stock. Barcoding & automation offers another powerful means for this purpose.
What it Does
Barcoding involves assigning unique barcodes for every product sold and scanning these barcodes with inventory scanners - often known as barcode scanners - to update stock records automatically.By automating inventory control processes, this technique streamlines inventory control processes by eliminating manual data input requirements.
It's useful
Barcoding and automation solutions can benefit businesses of any size. From shipping options to inventory barcodes, barcoding solutions can save time, effort and costs by streamlining operations.
Barcoding systems become ever more indispensable as sales volumes rise. By eliminating human mistakes that cause inventory management hiccups and errors from occurring, barcode systems prove invaluable as sales volumes rise and inventory management issues worsen. With higher volumes come higher risks from human mistakes, which threaten inventory control management issues if left without this safeguard in place. As sales volumes rise further, an effective barcoding solution becomes even more necessary as its presence helps prevent human mistakes that cause inventory management disruptions and problems from occurring more frequently than anticipated.
Benefits
Benefits involving Automation and Barcoding: it improves accuracy in inventory counts by eliminating human error, increasing speed and providing real-time inventory levels.
Other Considerations and Drawbacks
Barcoding systems require significant investments in training and technology upfront to implement successfully; accuracy and quality barcodes play a pivotal role.
Inventory Management Software
Inventory Management Software makes inventory control simpler.
What It Does
Inventory management software automates inventory tracking across various channels.
It's useful
An inventory management platform can prove extremely helpful for businesses of any size, particularly those managing inventory in multiple locations and sales channels.Used with the warehouse management system (WMS), RFID provides greater visibility into supply chain operations for online ecommerce store businesses and allows more excellent inventory tracking across their supply chains.
Benefits
Software for inventory management includes:
- Inventory tracking in real-time
- Integration of e-commerce platforms
- Stock forecasting
- Reorder notification alerts
- Automatic inventory reports
- Depending on the software, you can do even more
Other Considerations and Drawbacks
To use inventory management software effectively, an investment of time and resources upfront must be made, as well as going through an initial learning phase.
Omnichannel Fulfillment center location providers often come equipped with inventory-tracking features. You can outsource all aspects of the network of fulfillment centers while keeping an eye on inventory via the cloud-based platform provided.
Arionerp: Streamline Your Inventory Management
Inventory management can be challenging, whether done manually or with technology. Arionerp can simplify these time consuming tasks by streamlining its inventory system with one dashboard view of available products in each storefront location and tracking their status over time. Arion Erp is an innovative cloud-based Warehouse Management System that integrates all the tools and techniques needed to control inventory.
Conclusion
An ecommerce inventory management system can make life much more straightforward. Proper techniques and software will enable you to keep an eye on all the stock you own and produce greater profits, keeping customers happier while increasing customer retention rates.